Plywood CNC Router
Plywood CNC routers are versatile, high-precision machines designed to cut, shape, and carve plywood with exceptional accuracy and efficiency. Whether you’re a woodworking professional, hobbyist, or part of a manufacturing team, these CNC routers are indispensable tools for creating intricate designs, prototypes, or large-scale production pieces. Combining advanced technology with ease of use, plywood CNC routers empower users to achieve consistent, high-quality results while minimizing material waste and production time.
Equipped with features like computer-aided design (CAD) and computer-aided manufacturing (CAM) compatibility, these machines allow for seamless integration with design software. This makes it easy to translate your creative vision into reality, from custom furniture and cabinetry to artistic decor and signage. With their ability to handle complex designs and repetitive tasks, plywood CNC routers excel in projects that require both precision and scalability.
Modern plywood CNC routers are available in a variety of configurations, catering to different needs and budgets. From compact desktop models for small-scale projects to industrial-grade machines for heavy-duty operations, there’s a CNC router for every application. Many models also feature user-friendly interfaces, robust spindles, and advanced safety mechanisms, ensuring reliable and efficient operation for users of all skill levels.
-
AKM-4A2 CNC Router
Rated 5.00 out of 5$15,000.00 Add to cart -
AKM-4A3 CNC Router
$22,000.00 Add to cart -
AKM1325-4A CNC Router
Rated 5.00 out of 5$15,000.00 Add to cart -
AKM1530-4A CNC Router
Rated 5.00 out of 5$15,600.00 Add to cart -
AKM2030-4A CNC Router
Rated 5.00 out of 5$16,200.00 Add to cart -
AKM2040-4A CNC Router
Rated 5.00 out of 5$16,600.00 Add to cart -
AKM1325C-4A CNC Router
Rated 5.00 out of 5$20,000.00 Add to cart -
AKM1530C-4A CNC Router
Rated 5.00 out of 5$20,600.00 Add to cart -
AKM2030C-4A CNC Router
Rated 5.00 out of 5$21,200.00 Add to cart -
AKM2040C-4A CNC Router
Rated 5.00 out of 5$21,600.00 Add to cart -
AKM1212-5A CNC Router
Rated 5.00 out of 5$57,500.00 Add to cart -
AKM1224-5A CNC Router
Rated 5.00 out of 5$61,000.00 Add to cart
Tips for Choosing the Right Plywood CNC Router
Selecting the right plywood CNC router is crucial for achieving optimal performance and quality in your woodworking projects. With a wide range of machines available, it’s essential to consider features that align with your project goals, material requirements, and budget.
Identify Your Project Requirements
Determine the scope of your projects, including size, complexity, and frequency. For intricate patterns or repetitive production, prioritize CNC routers with high precision and automation features. Understanding your goals helps narrow your options to machines that deliver the performance you need.
Choose the Right Cutting Area
Match the cutting area of the CNC router to the size of the plywood sheets you’ll be working with. Industrial projects often require larger workspaces, while compact models are sufficient for smaller or hobbyist applications. A suitable cutting area minimizes repositioning and ensures efficiency.
Check Material Compatibility
Not all CNC routers handle plywood equally well, especially thicker or denser materials. Look for machines with adjustable spindle heights, powerful motors, and cutting tools designed to work with various plywood grades and thicknesses.
Evaluate Precision and Repeatability
Precision is key for detailed designs and consistent results. Choose CNC routers with advanced linear guides, ball screws, and high-resolution controllers. Repeatability ensures that every cut matches the design, making it critical for professional applications.
Consider Spindle Power and Speed
Spindle power directly affects cutting performance. High-power spindles are better for thick or dense plywood, while variable speed settings offer versatility for different tasks. Ensure the CNC router’s spindle can handle the materials and cutting speeds your projects require.
Ensure Software Compatibility
Verify that the CNC router supports common CAD/CAM software to streamline your workflow. Seamless integration with design tools allows you to create complex patterns, adjust parameters, and transfer files easily, reducing setup time and errors.
Prioritize Build Quality
A CNC router with a sturdy frame and high-quality components will provide durability and stable performance over time. Robust construction minimizes vibrations, ensuring clean and accurate cuts while extending the machine’s lifespan.
Look for User-Friendly Features
Ease of use is especially important for beginners or those upgrading from manual tools. Opt for CNC routers with intuitive interfaces, clear setup instructions, and training resources to help you get started and operate the machine effectively.
Consider Dust Management
Woodworking generates dust, which can interfere with precision and machine maintenance. Choose CNC routers with a built-in dust collection system or ensure compatibility with external units to maintain a clean, safe working environment.
Check Safety Features
Safety is non-negotiable. Look for CNC routers with emergency stop buttons, protective covers, and motion detection systems. These features minimize risks and ensure a secure working process, especially in busy or shared workspaces.
Assess Customer Support and Warranty
Strong customer support and a reliable warranty are essential for peace of mind. Choose manufacturers or suppliers with responsive service teams, training programs, and accessible spare parts to ensure smooth operation and problem resolution.
Compare Value for Money
Set a realistic budget and compare options within your price range. Focus on long-term value by considering the machine’s capabilities, durability, and operational costs rather than opting for the cheapest option, which might compromise quality.
What Materials Can the Plywood CNC Router Cut
Plywood CNC routers are highly versatile and capable of cutting and engraving a wide range of materials beyond just plywood. These machines are designed to handle various wood-based materials such as MDF, particle board, and hardwoods, making them ideal for diverse woodworking applications. Additionally, they can process non-wood materials like plastics, acrylics, and soft metals, offering flexibility for creative and industrial projects. The precision and power of plywood CNC routers allow them to cut through materials of varying thicknesses with ease, delivering clean edges and intricate designs. Whether you’re crafting furniture, creating signage, or producing detailed prototypes, these machines can adapt to different material properties, ensuring consistent and professional results.
- Softwood Plywood
- Hardwood Plywood
- Marine Plywood
- Exterior Plywood
- Interior Plywood
- Baltic Birch Plywood
- MDF Core Plywood
- Melamine-Coated Plywood
- Particleboard-Core Plywood
Application Industry
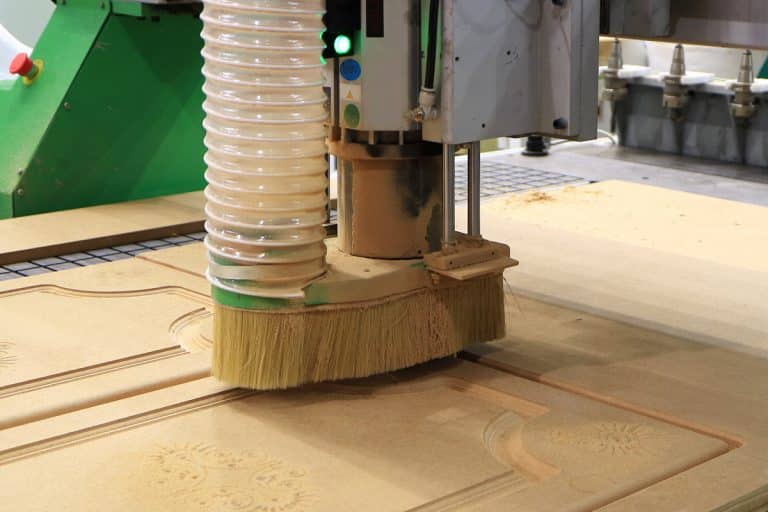
Woodworking Industry
The CNC router is a sophisticated tool that offers unparalleled precision, efficiency, and versatility, redefining what is possible in the world of woodworking.
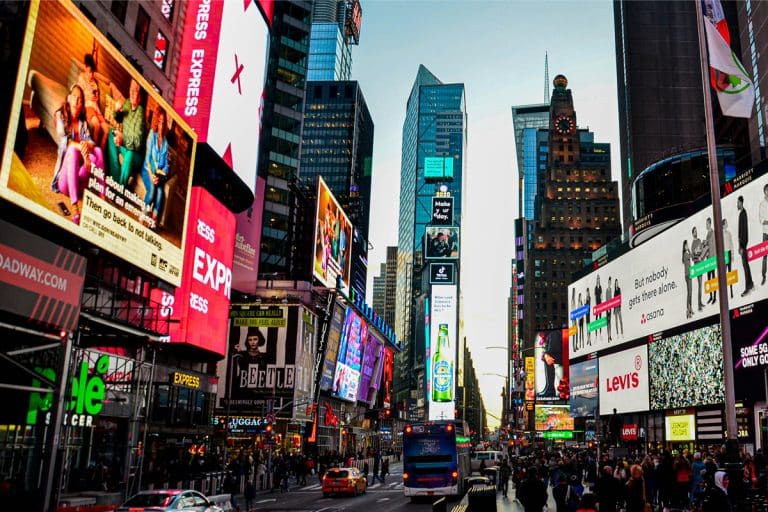
Advertising Industry
The CNC router excels at carving, engraving, and shaping a variety of materials, from wood and plastic to metal and composites, giving advertisers a canvas as diverse as their imagination.
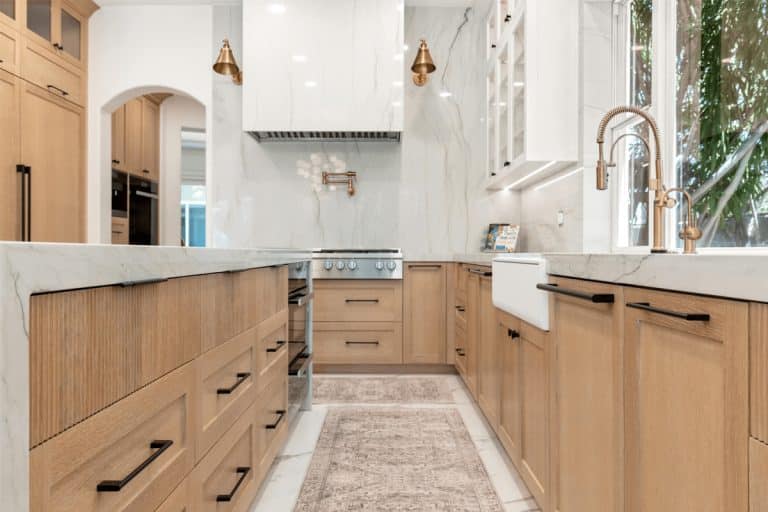
Bathroom Industry
The CNC router is equipped with advanced computer programming and cutting-edge machinery, ushering in a new era of efficiency, precision, and creativity in the bathroom industry.

Mold Industry
The CNC router enables manufacturers to create complex, detailed molds with unparalleled precision and speed, making them an indispensable tool in the mold industry.
Blog
How Deep Can a CNC Router Cut?
In this article, we'll break down the elements that influence CNC router cutting depth, typical values across different materials, and how to approach deep cutting safely and effectively.
Read More
What PPE is Recommended When Operating a CNC Router?
In this article, we'll go over the essential PPE recommended for CNC router use and explain how each item contributes to a safer and more comfortable working environment.
Read More
What Cooling Methods Are Needed for Metal CNC Routers?
This article explores the key cooling methods used in metal CNC routers and provides practical insights into selecting the right cooling system for your specific machining environment.
Read More
What Causes CNC Router Spindle Overheating?
In this article, we'll explore the common reasons why CNC router spindle temperatures rise beyond safe limits and provide practical solutions to help you prevent or fix the issue before ...
Read More
Frequently Asked Questions
Can CNC Routers Cut Plywood?
Yes, CNC routers are highly effective at cutting plywood, one of their primary applications in the woodworking and manufacturing industries. These machines utilize computer-controlled precision to cut, shape, and engrave plywood with exceptional accuracy and consistency. Here’s how the process works:
- Design Creation: A digital design is created using CAD (computer-aided design) software, defining the exact cuts and shapes required for the plywood.
- Programming: The design is translated into G-code, which serves as instructions for the CNC router, directing the tool’s movements, speed, and depth.
- Securing the Material: The plywood is securely fastened onto the router’s workbench using clamps, a vacuum table, or other methods to prevent movement during cutting.
- Tool Selection: The appropriate cutting bit is selected based on the type of cut and plywood thickness. Options include straight bits for simple cuts and V-shaped or ball-head bits for detailed designs.
- Cutting: The CNC router follows the programmed instructions to cut the plywood, delivering precise, clean results. The process ensures uniformity across repeated cuts.
What Is the Best Plywood for CNC Routing?
The best plywood for CNC routing depends on your project’s requirements, such as precision, durability, and finish. Certain types of plywood are particularly well-suited for CNC routing due to their consistent quality, structural stability, and ability to handle intricate designs. Below are some popular options:
- Birch Plywood: Known for its fine grain, stability, and strength, birch plywood is a top choice for CNC routing. Its smooth surface and uniform composition make it ideal for retaining intricate details.
- Baltic Birch Plywood: Featuring a higher number of veneers and fewer voids, Baltic birch plywood offers exceptional strength and a clean finish. It’s perfect for precision CNC work, such as furniture or decorative panels.
- MDF Core Plywood: With a medium-density fiberboard core, this plywood provides a smooth, void-free surface, reducing routing errors. It’s excellent for projects requiring a fine finish and uniformity.
- Marine Plywood: Engineered to resist moisture, marine plywood is suitable for projects exposed to water. Its high-quality veneers and durable bonding make it a reliable choice for CNC processing.
- Melamine-Coated Plywood: For projects requiring a sleek, finished look, melamine-coated plywood offers a durable and smooth surface. It’s frequently used for cabinetry and furniture.
- Hardwood Plywood: Plywood made from hardwood species like oak, maple, or walnut is ideal for projects requiring durability and a premium aesthetic. It’s excellent for decorative applications.
- Veneered Plywood: Plywood with decorative veneers, such as mahogany, cherry, or teak, adds elegance to CNC-rout pieces. This option is ideal for projects where appearance matters.
What Kind of Router Bit for Plywood?
Choosing the right router bit for plywood is essential for achieving clean cuts, minimizing chip-out, and ensuring precision. The type of router bit you select depends on the type of cut you need and the project requirements. Below are common router bits ideal for cutting plywood:
- Straight Router Bit: A versatile option for making straight cuts, grooves, and basic edge profiles. Straight bits are widely used for sizing plywood sheets or creating standard cuts.
- Spiral Upcut Router Bit: Spiral upcut bits excel at chip evacuation, pulling chips away from the cut for deep grooves or slots. They are ideal for cuts that prioritize material removal efficiency but may cause slight chip-out on the surface.
- Spiral Downcut Router Bit: Perfect for achieving a clean top surface, spiral downcut bits push chips downward, minimizing chip-out on the top side. They’re ideal for decorative cuts or when a polished top finish is required.
- Compression Router Bit: Compression bits combine upcut and downcut flutes, reducing chip-out on both the top and bottom surfaces of plywood. These are ideal for projects requiring a clean finish on both sides, such as furniture or cabinetry.
- Flush Trim Router Bit: Flush trim bits are used to precisely trim plywood edges to match a template. They are available in top-bearing and bottom-bearing styles, depending on the orientation of your template.
- V-Groove Router Bit: Used for decorative purposes, V-groove bits are perfect for engraving grooves, chamfers, or artistic designs in plywood projects.
- Spoil Board Surfacing Bit: For leveling a spoil board or ensuring a flat surface beneath your plywood, spoil board surfacing bits are an essential tool for consistent cutting.
- Rabbeting Router Bit: Rabbeting bits are designed to create recesses or rabbets along plywood edges, making them useful for joining panels or constructing box-like structures.
- Ball Nose Router Bit: Ball nose bits are ideal for 3D carving and contouring in plywood, creating rounded edges and curved designs with precision.
How to Routing Plywood Without Splintering?
Routing plywood without splintering requires the right tools, techniques, and preparation. Follow these tips to ensure clean, professional cuts and avoid damaging the material:
- Use a High-Quality Router Bit: Invest in sharp, carbide-tipped router bits designed for woodworking. Dull or low-quality bits can tear wood fibers, increasing the risk of splintering. Regularly inspect and replace bits as needed to maintain sharpness.
- Choose the Right Router Bit Type: Select a router bit suited for plywood, such as spiral upcut, downcut, or compression bits. Spiral upcut bits are great for removing chips efficiently, while downcut bits minimize splintering on the top surface. Compression bits handle both surfaces effectively, reducing splintering on both sides.
- Adjust Feed Speed: Optimize the CNC router’s feed speed to match the plywood’s thickness and the bit used. Feeding too quickly can cause tearing, while slow feeding may result in burning. Test different speeds to achieve the smoothest results.
- Use a Backing Board: Place a sacrificial backing board beneath the plywood to support the wood fibers. This prevents splintering on the bottom side of the cut. Replace the backing board as needed to maintain its effectiveness.
- Apply Masking Tape: Apply masking tape over the cutting area to support wood fibers and minimize splintering. Score the tape along the cut line to prevent it from lifting during routing.
- Opt for Downcut Helical Bits: For clean top surfaces, consider using downcut helical router bits. These bits push fibers downward, minimizing tear-out on the plywood’s top side.
- Take Shallow Passes: For deeper cuts, make multiple shallow passes instead of a single deep cut. This reduces stress on the plywood and ensures cleaner edges.
- Route Along the Grain: Whenever possible, align your cuts with the grain direction of the plywood’s surface veneer. Cutting against the grain increases the likelihood of splintering.
- Secure the Material Firmly: Clamp the plywood securely to the workbench to minimize vibrations, which can cause uneven cuts and splintering. Ensure the plywood remains stable during the routing process.
How Precise Are Plywood CNC Routers?
Plywood CNC routers are highly precise tools capable of achieving exceptional accuracy in woodworking projects. The precision of these machines depends on factors such as the machine’s build quality, components, and operating conditions. Here’s an overview of their precision capabilities:
- Precision Range
- Typical Accuracy: Most plywood CNC routers offer precision within ±0.001 to ±0.005 inches (±0.025 to ±0.127 mm).
- Higher-End Machines: Industrial-grade routers can achieve even tighter tolerances, often ±0.0005 inches (±0.0127 mm) or better.
- Factors Influencing Precision
- Machine Build Quality: A rigid frame and stable gantry reduce vibrations, ensuring consistent accuracy.
- Linear Guides and Ball Screws: High-quality components maintain precise motion and positioning.
- Spindle Quality: A robust spindle with minimal runout ensures clean, accurate cuts.
- Tool Calibration: Properly calibrated tools and bit alignment are crucial for maintaining precision.
- Repeatability: Plywood CNC routers excel at repeatability, meaning they can produce identical parts with high accuracy across multiple runs. This consistency is vital for projects requiring uniformity, such as furniture components or decorative panels.
- Material Considerations: The precision of cuts on plywood may vary slightly depending on factors like.
- Plywood Quality: Variations in density, voids, or imperfections can affect the quality of the cut.
- Tool Engagement: Incorrect feed rates or bit selection can lead to slight deviations or splintering.
- Software and Toolpath Control: Advanced CAD/CAM software allows users to program highly detailed toolpaths, enabling CNC routers to produce intricate designs and complex cuts with exceptional precision. Software accuracy complements the hardware’s capabilities.
- Maintenance and Setup: Regular maintenance, such as cleaning, lubricating moving parts, and ensuring alignment, is critical for preserving precision. Improper setup or wear on components can reduce accuracy over time.
How to Safely Operate Plywood CNC Routers?
Operating a plywood CNC router safely requires adhering to proper procedures, using appropriate safety equipment, and maintaining a well-prepared workspace. Below are essential guidelines to ensure safe and efficient operation:
- Wear Appropriate Safety Gear
- Eye Protection: Always wear safety goggles to protect against flying debris.
- Hearing Protection: CNC routers can be noisy, so use earplugs or earmuffs.
- Dust Mask/Respirator: Protect yourself from inhaling fine dust particles, especially when cutting plywood.
- Gloves (Optional): Use snug-fitting gloves if necessary, but avoid loose clothing or gloves that could get caught in moving parts.
- Inspect the Machine Before Use
- Check for loose components or damaged parts.
- Ensure that the router bit is securely installed and in good condition.
- Verify that all cables and connections are intact and properly grounded.
- Secure the Plywood Properly
- Use clamps, a vacuum table, or other holding methods to ensure the plywood is stable and won’t shift during cutting.
- Avoid placing hands or tools near the cutting area while the machine is in operation.
- Set Up Correctly
- Tool Path: Double-check the programmed tool path to avoid errors.
- Material Settings: Match the feed rate, spindle speed, and cutting depth to the plywood type and thickness.
- Zero Position: Set the CNC router’s home or zero position accurately.
- Maintain a Clean Work Area
- Keep the area around the CNC router free from clutter.
- Regularly clear sawdust and debris using a dust collection system or vacuum.
- Monitor the Machine During Operation
- Stay alert and watch the CNC router while it is running. Never leave the machine unattended.
- Be ready to hit the emergency stop button if necessary.
- Avoid Overloading the Machine
- Do not push the CNC router beyond its capabilities. Excessive feed rates or cutting depths can cause tool failure or material damage.
- Use the correct router bit for the task and ensure it’s sharp and appropriate for plywood.
- Follow Proper Shutdown Procedures
- Turn off the spindle and wait for it to come to a complete stop before making adjustments or removing material.
- Shut down the CNC router and disconnect the power supply when maintenance is needed.
- Perform Regular Maintenance
- Clean and lubricate moving parts to ensure smooth operation.
- Inspect belts, rails, and bits for wear and tear and replace them as needed.
- Be Aware of Potential Hazards
- Avoid distractions and maintain focus while operating the machine.
- Stay clear of moving parts, and never attempt to touch the bit or material while the machine is running.
What Customer Support Do Plywood CNC Routers Provide?
Plywood CNC routers come with reliable customer support options to ensure smooth operation and user satisfaction:
- Free Online Technical Support: Customers can access complimentary technical assistance through online platforms, including email, chat, or video support. This service is ideal for troubleshooting, software setup, or resolving operational issues remotely.
- Paid On-Site Training: For users requiring hands-on guidance, on-site training sessions are available at an additional cost. These sessions cover installation, operation, and maintenance to ensure optimal use of the machine.
What Is The Warranty Period of Plywood CNC Routers?
Our CNC router is backed by a comprehensive warranty designed to give you peace of mind and protect your investment:
- 3-Year Warranty for the Entire Machine: This full warranty covers any defects or malfunctions in the machine as a whole, ensuring reliable performance and longevity over time.
- 5-Year Warranty for Core Components: Key components essential for optimal machine operation are covered for 1.5 years. This includes parts that may experience wear and tear with regular use, ensuring you have support for the most vital parts of the machine.