ATC CNC Router
The ATC CNC router (Automatic Tool Change CNC router) is engineered for precision, efficiency, and versatility, making it an essential tool for businesses looking to streamline their production processes. Whether you’re working with wood, plastics, or metals, the ATC CNC router offers seamless automation that enhances workflow and reduces manual intervention. Designed to handle a wide range of applications—from intricate carvings to large-scale panel cutting—the ATC system automatically swaps tools during the machining process, cutting down on downtime and boosting productivity. With their advanced software and high-performance capabilities, these CNC router ensures consistent, repeatable results with minimal effort, making them perfect for industries like woodworking, signage, furniture making, and prototyping.
Built to deliver exceptional precision, the ATC CNC router combines cutting-edge technology with robust construction. This enables it to tackle complex tasks with ease while maintaining high accuracy and smooth finishes. Its user-friendly interface and customizable settings allow businesses to adapt to varying project demands, ensuring that every job is completed on time and to the highest standards. Whether you’re looking to expand your production capacity or improve your manufacturing efficiency, the ATC CNC router offers the performance, flexibility, and reliability that modern industries demand.
-
AKM-C1 CNC Router
Rated 5.00 out of 5$10,500.00 Add to cart -
AKM-C2 CNC Router
Rated 5.00 out of 5$13,400.00 Add to cart -
AKM-C3 CNC Router
Rated 5.00 out of 5$18,100.00 Add to cart -
AKM1325C CNC Router
Rated 5.00 out of 5$13,400.00 Add to cart -
AKM1530C CNC Router
Rated 5.00 out of 5$14,000.00 Add to cart -
AKM2030C CNC Router
Rated 5.00 out of 5$14,600.00 Add to cart -
AKM2040C CNC Router
Rated 5.00 out of 5$15,000.00 Add to cart -
AKM1325C-4A CNC Router
Rated 5.00 out of 5$20,000.00 Add to cart -
AKM1530C-4A CNC Router
Rated 5.00 out of 5$20,600.00 Add to cart -
AKM2030C-4A CNC Router
Rated 5.00 out of 5$21,200.00 Add to cart -
AKM2040C-4A CNC Router
Rated 5.00 out of 5$21,600.00 Add to cart -
AKM1212-5A CNC Router
Rated 5.00 out of 5$57,500.00 Add to cart
Tips For Choosing The Right ATC CNC Router
Selecting the right ATC CNC router is a crucial decision for any business looking to improve manufacturing efficiency, precision, and productivity. The ideal CNC router will depend on factors such as your material needs, workspace size, production requirements, and the long-term goals of your operation.
Assess Your Material Requirements
Understanding the materials you’ll work with—wood, metal, plastic, or composites—is crucial when selecting an ATC CNC router. Different materials require varying levels of power, cutting speed, and tool types. Ensure the CNC router you choose can handle the density and hardness of your most frequently used materials for optimal performance.
Determine the Right Machine Size
Machine size determines the maximum workpiece dimensions that can be processed. Choose a CNC router with a working area that suits your largest projects, but avoid oversizing if your workpieces are typically smaller. Consider available workspace and ensure the machine fits comfortably without sacrificing productivity.
Consider the Number of Tool Stations
The number of tool stations directly impacts the CNC router’s ability to handle different tasks without manual tool changes. More tool stations reduce downtime and improve efficiency for complex projects. Consider the variety of tools required for your production and choose a machine with a sufficient number of stations.
Evaluate Spindle Power and Speed
Spindle power determines the CNC router’s cutting capabilities, especially for tougher materials. A higher spindle speed can reduce machining time and improve surface finish. Choose a CNC router with adequate power and speed for the materials you work with to ensure smooth, efficient operations and high-quality outputs.
Look for Software Compatibility
Ensure the ATC CNC router integrates seamlessly with your existing CAD/CAM software. Compatibility with industry-standard formats like DXF or G-code ensures smooth design transfers and minimal setup time. Choose a CNC router that offers flexibility in software integration to ensure long-term efficiency and adaptability.
Assess the Machine’s Precision and Accuracy
The precision of your ATC CNC router is vital for delivering high-quality, repeatable results. Look for a CNC router with low tolerance and high repeatability to minimize errors and material waste. A machine with high accuracy will ensure consistently precise cuts for both complex and simple designs.
Consider the ATC Type
The ATC type affects tool change speed and overall efficiency. Fixed linear tool changers are simple and reliable, while Follow-up linear tool changes offer faster transitions. Disc tool changers provide higher tool capacity but may come with more complex maintenance needs. Select the best ATC type based on your production speed requirements.
Check for Robust Build Quality
A strong, durable build ensures consistent performance and longevity. Opt for an ATC CNC router made from high-quality materials like steel or aluminum. A sturdy machine will reduce vibrations, leading to smoother cuts, improved precision, and longer machine life, even under heavy use.
Evaluate Ease of Use and Setup
Choose a machine with an intuitive interface and simple setup to reduce operator training time. User-friendly controls can help minimize errors and boost overall efficiency. Machines with easy calibration and quick configuration allow operators to focus more on production and less on machine setup.
Consider Maintenance and Support
Check the availability of spare parts and the quality of customer support. A reliable service network ensures timely repairs and minimal downtime. Choose a manufacturer that offers comprehensive maintenance services, easy access to parts, and responsive technical support to keep your CNC router in peak condition.
Energy Efficiency and Operating Costs
Energy consumption and operational costs can accumulate over time. Look for energy-efficient ATC CNC routers with features like variable speed drives or energy-saving motors. These features help reduce electricity costs while maintaining high performance, making the CNC router a more cost-effective long-term investment.
Evaluate Future Scalability
Consider whether the ATC CNC router can grow with your business. Look for machines with upgradeable components, such as additional tool stations or enhanced spindle power, which will allow you to adapt to evolving production needs. Choosing a scalable machine ensures that your investment remains valuable as your business expands.
What Materials Can The ATC CNC Router Cut
The ATC CNC router is a versatile machine designed to handle a wide range of materials across various industries. It is capable of cutting and shaping wood, plastics, composites, metals, and even some stone materials. Its high precision and automatic tool-changing capability make it ideal for tasks that require multiple tool types, such as intricate woodworking, plastic engraving, or metal machining. The CNC router’s spindle power and speed can be adjusted to suit the material’s hardness, thickness, and desired finish. Whether you’re creating complex designs in soft materials like MDF and acrylic or working with tougher materials like aluminum and brass, the ATC CNC router offers consistent, reliable performance. This flexibility allows businesses to streamline production and expand their capabilities across different material types.
Application Industry
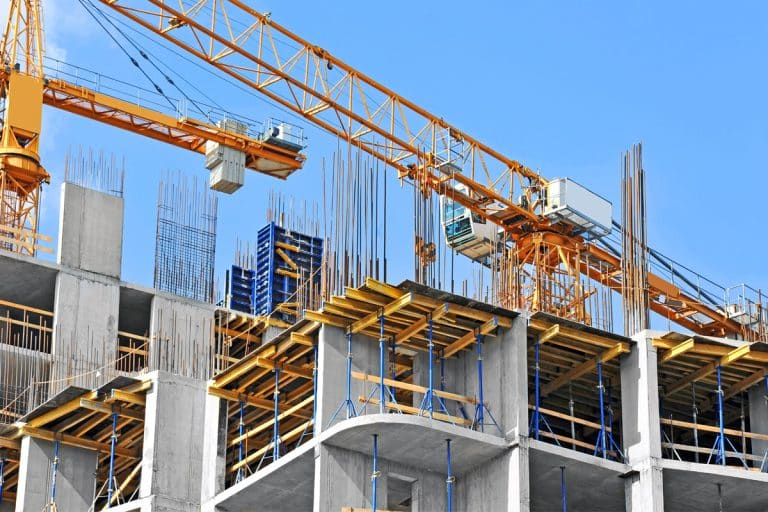
Construction Industry
The integration of CNC routers into construction workflows has ushered in a new era characterized by meticulous detailing, rapid prototyping, and improved material utilization.
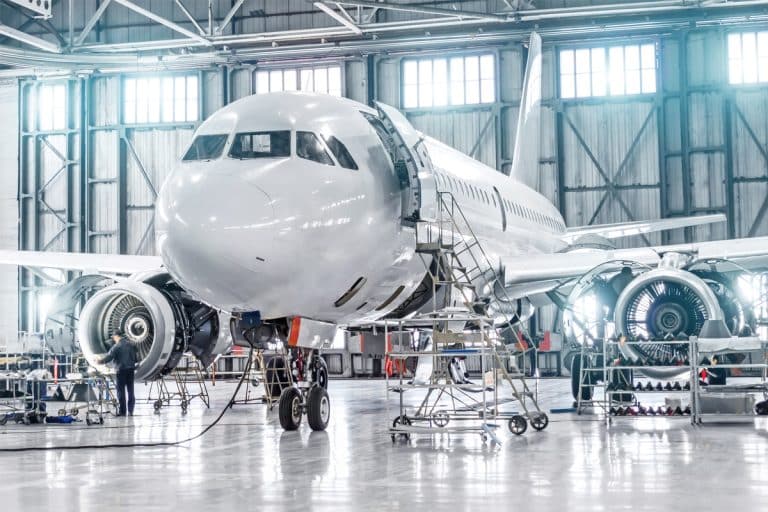
Aerospace Industry
The CNC router is widely used in aerospace engineering due to its unparalleled ability to carve complex designs, manufacture complex parts, and ensure tight tolerances.
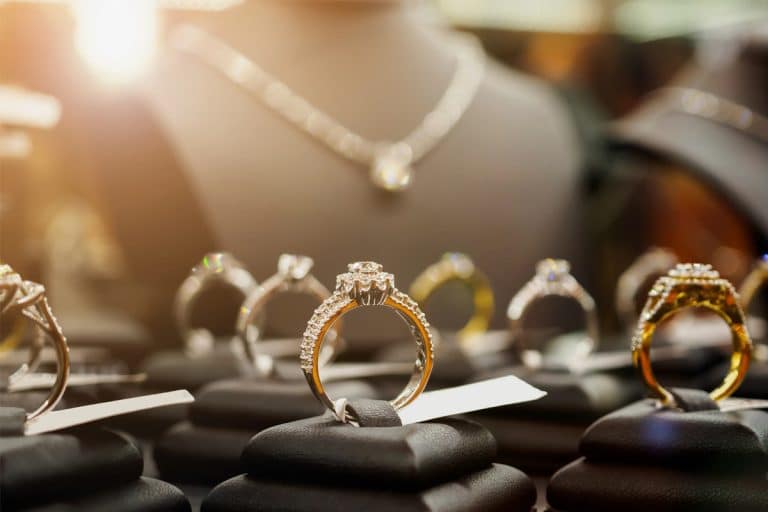
Jewelry Industry
The CNC router revolutionize the way fine jewelry is designed and made by delivering unparalleled precision and efficiency and producing intricate designs with meticulous attention to detail.
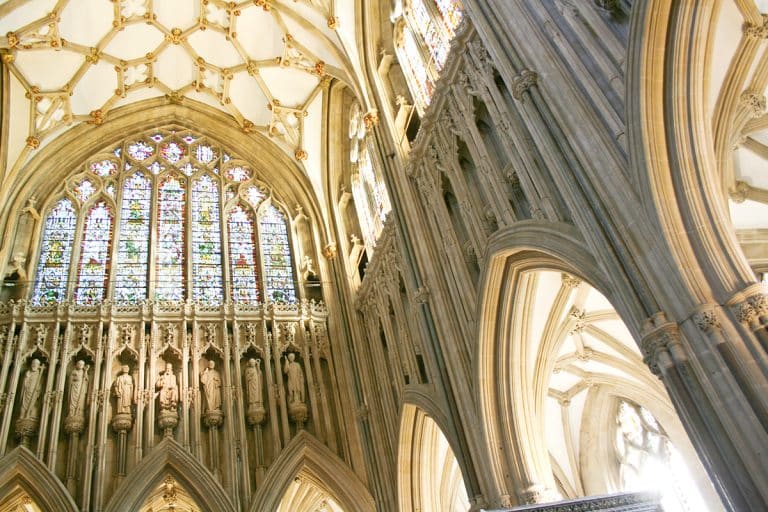
Stone Carving Industry
The integration of CNC routers into the stone carving industry is not only revolutionizing the way craftsmen carve, it is also redefining the boundaries of artistic possibilities in this ancient practice.
Blog
What is CNC Router Homing and Why is It Important?
CNC router homing is a fundamental process. In this article, we'll break down what CNC router homing is, how it works, and why it's an indispensable part of every machining ...
Read More
What Should I Consider When Buying a CNC Router from an Overseas Supplier?
In this guide, we’ll walk you through the key considerations when buying a CNC router from an overseas supplier to help you make a confident and informed decision.
Read More
How to Choose the Right Vacuum Pump for a CNC Router Vacuum Table?
This guide will walk you through the factors to consider when choosing a vacuum pump for your CNC router vacuum table, helping you make an informed decision based on your ...
Read More
How Do I Ensure Electrical Safety with a CNC Router?
In this article, we'll explore the key steps to ensure the electrical safety of CNC routers, from proper installation to operator training, to provide you with guidance to ensure electrical ...
Read More
Frequently Asked Questions
What Does ATC in CNC Routers Mean?
ATC stands for Automatic Tool Changer in CNC routers. It refers to a system that allows the CNC router to automatically change tools during the machining process without manual intervention. This automation is achieved through a tool storage mechanism, such as a carousel or magazine, which holds multiple tools for different tasks.
The ATC system enhances efficiency by reducing downtime, allowing the CNC router to seamlessly switch between tools as required by the machining program. Whether for drilling, milling, or engraving, the ATC ensures that the correct tool is used at the right time, streamlining operations, improving productivity, and enabling complex, multi-step processes to be completed without interruption.
Overall, the ATC system makes CNC routers more versatile and capable of handling intricate and varied tasks, increasing accuracy and reducing manual labor during production.
What Are ATC and APC in CNC Machining?
In CNC machining, ATC (Automatic Tool Changer) and APC (Automatic Pallet Changer) are automated systems that improve the efficiency and versatility of the machining process by minimizing manual intervention and reducing downtime.
- ATC (Automatic Tool Changer): An Automatic Tool Changer is a mechanism that allows a CNC machine to automatically change between different cutting tools during a machining operation. The system holds multiple tools in a tool magazine or carousel, and based on the program, the CNC machine can select and replace tools without the need for human intervention. This feature enables the machine to perform complex tasks, such as drilling, milling, and engraving, using a variety of tools in a single setup, improving efficiency and reducing downtime for tool changes.
- APC (Automatic Pallet Changer): An Automatic Pallet Changer is a system used in CNC machines, especially machining centers, to automatically swap workpieces or pallets. While one pallet is being machined, another can be loaded or unloaded outside the machine. This system minimizes idle time between workpieces and ensures continuous, uninterrupted production. APC systems are particularly valuable in high-volume manufacturing, where quick workpiece changes are essential for maintaining production flow.
What Are the Different Types of ATC in CNC Routers?
In CNC routers, Automatic Tool Changer (ATC) systems come in various designs, each offering unique advantages to meet different production requirements. Here are the most common types:
- Disc Tool Changer: The disc tool changer features a rotating disc with multiple tool slots around its circumference. The machine’s spindle retrieves the tool from the disc when needed. The disc rotates to bring the next tool in line for use. This system is popular for machines that need to handle a moderate number of tools and is space-efficient.
- Fixed Linear Tool Changer: The fixed linear tool changer arranges tools along a fixed linear track. The machine’s spindle moves horizontally or vertically along the track to retrieve the required tool. This type of system is ideal for machines with limited space and when a linear, predictable tool change sequence is needed.
- Follow-Up Linear Tool Changer: The follow-up linear tool changer also arranges tools linearly but with the added benefit of the tool magazine moving along with the spindle. This system speeds up tool changes by reducing the distance the spindle has to travel to retrieve the tool, reducing downtime, and improving machining efficiency.
How Much Do ATC CNC Routers Cost?
The cost of ATC CNC routers can vary significantly depending on the type, features, and intended use. Here are the typical price ranges for different categories:
- Hobby ATC CNC Routers: Price Range: $6,500 – $7,500. These CNC routers are designed for small-scale, non-industrial use, such as DIY projects or small workshops. They offer basic automatic tool-changing features and are ideal for less demanding tasks.
- Industrial 3-Axis ATC CNC Routers: Price Range: $11,000 – $19,000. These CNC routers are more advanced and are used in various industries for tasks like woodworking, signage, and prototyping. They offer improved precision and productivity compared to hobby models, with automated tool changing for higher efficiency.
- Industrial 4-Axis ATC CNC Routers: Price Range: $20,000 – $25,000. These CNC routers come with an additional rotational axis, enabling more complex machining tasks such as angled cuts or precise drilling. They are typically used for medium to heavy-duty applications, offering more versatility and precision.
- Industrial 5-Axis ATC CNC Routers: Price Range: $56,000 – $75,000. These high-end CNC routers provide full 5-axis control, allowing for extremely precise and complex cuts. They are used in industries like aerospace, automotive, and high-end prototyping, where detailed and multi-dimensional machining is required.
How Do ATC CNC Routers Work?
ATC (Automatic Tool Changer) CNC routers are designed to automate the process of switching tools during machining tasks, which greatly improves efficiency and reduces downtime. Here’s how they work:
- Tool Storage System: ATC CNC routers come equipped with a tool storage system, typically a tool magazine or turntable. These hold multiple tools in designated slots. The storage system can rotate or move to present the correct tool to the spindle during the machining process.
- Programmed Tool Selection: The CNC router’s program, which is based on the design or task requirements, dictates the specific tools needed at different points during machining. The tool paths in the program indicate which tool is required for each operation, such as cutting, drilling, or engraving.
- Tool Change Command: When the program reaches a point where a different tool is needed, it sends a command to the ATC system. This triggers the automatic tool change process, with the system selecting the appropriate tool based on the program’s instructions.
- Tool Retrieval: Once the tool change command is issued, the tool magazine or turntable moves or rotates to bring the correct tool into position. The ATC system ensures that the tool is correctly aligned and ready for retrieval.
- Spindle Engagement: The CNC router’s spindle moves to the tool changer position, where it engages with the selected tool. Most spindles use clamps or collets to securely hold the tool in place.
- Tool Removal and Replacement: The spindle removes the tool from the magazine and inserts it into the machine. The previously used tool is placed back into the tool storage system, and ready for the next use.
- Continued Machining: With the new tool securely in place, the CNC router continues the machining process, following the programmed instructions to perform tasks like cutting, drilling, or shaping.
- Repeat the Process: Throughout the machining cycle, the ATC system repeats this tool-changing process as needed, ensuring the right tool is always available for each task without manual intervention.
How to Safely Operate ATC CNC Routers?
Operating ATC CNC routers safely is crucial to avoid accidents, ensure equipment longevity, and maintain high-quality production. Below are key safety practices to follow when using an ATC CNC router:
- Proper Training: Ensure that all operators are properly trained in both the general operation of CNC routers and the specifics of the ATC system. Operators should understand the tool-changing process, machine functions, and emergency procedures.
- Wear Personal Protective Equipment (PPE): Always wear the necessary PPE, including safety glasses, ear protection, and gloves. PPE helps protect against flying debris, loud noises, and accidental tool contact.
- Keep the Work Area Clean and Organized: A clean and organized workspace reduces the risk of tripping, tool misplacement, and other accidents. Ensure the area around the CNC router is free of debris, tools, or materials that might obstruct operations.
- Inspect the Machine Before Use: Before starting any machining process, always conduct a thorough pre-operation inspection. Check for tool wear, machine calibration, and loose parts, and ensure the ATC system is working properly. Pay attention to any error messages or alerts from the control system.
- Check the Tooling System: Ensure that the tools are correctly placed in the magazine and are securely mounted. A loose or improperly stored tool can cause malfunction or accidents when the ATC system operates.
- Understand the CNC Program: Review the machining program to ensure it is accurate and has no errors. Ensure the ATC system is programmed with the correct tool paths and that the tool changes are properly scheduled.
- Test Run the Machine: Before beginning full production, run a dry or test cycle without material to confirm the ATC system changes tools as expected and that the machine operates smoothly.
- Do Not Bypass Safety Features: Do not disable or bypass safety features, such as emergency stops, sensors, or covers. These are in place to protect both the operator and the machine.
- Monitor the Machine During Operation: Even though the ATC system automates tool changes, operators should remain attentive during the entire machining process. Watch for any signs of malfunction, unusual sounds, or error codes that may require immediate action.
- Regular Maintenance: Regularly maintain and service the ATC CNC router, including cleaning the tool magazine, inspecting the tool changer mechanism, lubricating moving parts, and ensuring the machine’s electrical system is functioning properly. A well-maintained machine is less likely to malfunction and more efficient to operate.
- Use Correct Cutting Parameters: Ensure that the appropriate cutting parameters—such as feed rates, spindle speeds, and tool choices—are correctly set in the program to match the material being processed. Incorrect settings can cause the tools to wear out quickly, increasing the likelihood of accidents.
- Know Emergency Procedures: Be familiar with the emergency stop procedures in case of a malfunction or safety issue. In addition to the physical emergency stop button, know how to quickly reset or pause the machine from the control panel.
What Customer Support Do ATC CNC Routers Provide?
ATC CNC routers come with reliable customer support options to ensure smooth operation and user satisfaction:
- Free Online Technical Support: Customers can access complimentary technical assistance through online platforms, including email, chat, or video support. This service is ideal for troubleshooting, software setup, or resolving operational issues remotely.
- Paid On-Site Training: For users requiring hands-on guidance, on-site training sessions are available at an additional cost. These sessions cover installation, operation, and maintenance to ensure optimal use of the machine.
What Is The Warranty Period of ATC CNC Routers?
Our CNC router is backed by a comprehensive warranty designed to give you peace of mind and protect your investment:
- 3-Year Warranty for the Entire Machine: This full warranty covers any defects or malfunctions in the machine as a whole, ensuring reliable performance and longevity over time.
- 5-Year Warranty for Core Components: Key components essential for optimal machine operation are covered for 1.5 years. This includes parts that may experience wear and tear with regular use, ensuring you have support for the most vital parts of the machine.