Plastic CNC Router
Plastic CNC routers are precision machines designed specifically for the cutting, engraving, and shaping of plastic materials. Whether you’re working with acrylic, PVC, polycarbonate, or other types of plastic, these routers offer unparalleled accuracy and versatility, making them an essential tool for a wide range of industries including manufacturing, signage, automotive, and prototyping.
Equipped with advanced control systems, high-speed spindles, and robust motors, plastic CNC routers are capable of delivering fine detailing, smooth edges, and complex shapes with ease. They can perform a variety of tasks, such as intricate engraving, high-speed cutting, drilling, and surface finishing, all while maintaining precision throughout the process. The versatility of plastic CNC routers allows them to handle various types of plastic, from rigid sheets to flexible materials, catering to both large production runs and custom jobs.
One of the primary benefits of plastic CNC routers is their ability to optimize production time, reduce waste, and improve consistency. Automation features help eliminate human error, ensuring repeatable and high-quality results with minimal manual intervention. Additionally, their ability to integrate seamlessly with CAD/CAM software makes them ideal for prototyping and rapid production in industries that require high precision and customization. Plastic CNC routers provide the ideal solution for manufacturers looking to enhance their production capabilities, increase efficiency, and create high-quality plastic products with minimal effort and maximum precision.
-
AKM1325 CNC Router
Rated 5.00 out of 5$4,800.00 Add to cart -
AKM1530 CNC Router
Rated 5.00 out of 5$5,400.00 Add to cart -
AKM2030 CNC Router
Rated 5.00 out of 5$6,000.00 Add to cart -
AKM2040 CNC Router
Rated 5.00 out of 5$6,500.00 Add to cart -
AKM-C1 CNC Router
Rated 5.00 out of 5$10,500.00 Add to cart -
AKM-C2 CNC Router
Rated 5.00 out of 5$13,400.00 Add to cart -
AKM-C3 CNC Router
Rated 5.00 out of 5$18,100.00 Add to cart -
AKM1325C CNC Router
Rated 5.00 out of 5$13,400.00 Add to cart -
AKM1530C CNC Router
Rated 5.00 out of 5$14,000.00 Add to cart -
AKM2030C CNC Router
Rated 5.00 out of 5$14,600.00 Add to cart -
AKM2040C CNC Router
Rated 5.00 out of 5$15,000.00 Add to cart -
AKM-4A1 CNC Router
Rated 5.00 out of 5$11,800.00 Add to cart
Tips for Choosing the Right Plastic CNC Router
Selecting the right CNC router for plastic processing is essential for ensuring efficient production, high-quality cuts, and the ability to handle a variety of plastic materials. When choosing a machine, you need to consider multiple factors, including machine capabilities, material compatibility, software integration, and maintenance requirements.
Evaluate Material Compatibility
Different plastics have different machining requirements. Before purchasing a CNC router, ensure it can handle the types of plastic materials you intend to work with, such as acrylic, PVC, polycarbonate, or ABS. Machines designed for multi-material compatibility can offer flexibility for diverse applications.
Choose the Right Spindle Power
The spindle power directly affects cutting performance. Higher spindle power is necessary for cutting through harder plastics without affecting cut quality. For softer plastics, a lower spindle power might suffice. Ensure the spindle power meets the needs of your specific materials.
Consider the Cutting Area
The size of the cutting area impacts the size of the plastic pieces you can work with. Consider the dimensions of the largest materials you plan to process and ensure the machine’s work area is large enough to accommodate them. A larger cutting area increases versatility and future-proofs your setup.
Focus on Precision and Accuracy
Plastic machining often requires tight tolerances and intricate details. Look for a CNC router that offers high precision to ensure that complex designs, such as fine engravings or detailed cuts, are executed flawlessly without deviations or errors.
Prioritize Speed and Efficiency
If high production volume is a key concern, prioritize a CNC router with high cutting speed. Faster machines reduce production time while maintaining quality. Look for a machine that balances speed with precision for optimal efficiency in large-scale or continuous operations.
Check Software Compatibility
The CNC router should be compatible with your preferred CAD/CAM software for seamless design-to-production workflows. Ensure the machine supports industry-standard software, allowing for easy file imports and generating precise cutting instructions without additional conversion work.
Automatic Tool Changer (ATC)
Machines with an automatic tool changer allow for unattended operations, reducing downtime and improving efficiency for complex jobs. With an ATC, the CNC router can automatically switch between different cutting tools, saving time and reducing manual intervention during production.
Effective Dust and Chip Management
Cutting plastics produces significant amounts of dust and chips that can impair machine performance and create hazardous work conditions. Choose a CNC router with an efficient dust collection or chip removal system to keep the work environment clean, improve visibility, and ensure the CNC router operates at peak performance.
Assess Build Quality and Stability
A strong, rigid machine frame is essential for accurate cutting and minimizing vibrations. Look for a CNC router with robust construction to ensure stability during high-speed operations. A solid build guarantees minimal tool deflection, resulting in more precise cuts and a longer lifespan for the machine.
Evaluate Maintenance Requirements
Look for a CNC router that is easy to maintain and comes with clear maintenance instructions. Consider factors like lubrication schedules, ease of access to parts, and the availability of support services. A machine with low maintenance requirements will reduce downtime and improve productivity in the long term.
Consider Energy Efficiency
CNC routers with energy-efficient motors and components can help reduce operating costs over time. If your production volume is high, energy savings can accumulate significantly. Machines with eco-friendly features will contribute to both cost-efficiency and environmental sustainability.
Customer Support and Warranty
Choose a CNC router from a reputable manufacturer that offers comprehensive customer support, including technical assistance and timely parts replacement. A solid warranty can provide peace of mind and protect your investment by ensuring that any technical issues or breakdowns are promptly addressed.
What Materials Can The Plastic CNC Router Cut
Plastic CNC routers are designed to cut a wide range of plastic materials with high precision and efficiency. These machines can process both rigid and flexible plastics, making them ideal for various industries such as signage, automotive, packaging, and product manufacturing. Whether you need to cut, engrave, drill, or shape materials like acrylic, PVC, polycarbonate, ABS, or foam, a plastic CNC router can handle it all. With adjustable speed and power settings, these CNC routers provide versatility, allowing them to adapt to different plastic types and thicknesses. The ability to work with multiple plastic materials in one machine ensures streamlined production processes and enhanced capabilities, making plastic CNC routers an invaluable tool for businesses that require precision and versatility in their machining tasks.
- Acrylic
- PE
- LDPE
- PP
- PC
- PVC
- PETG
- Nylon
- PU
- EPS
- POM
- PET
- HDPE
- PS
Application Industry
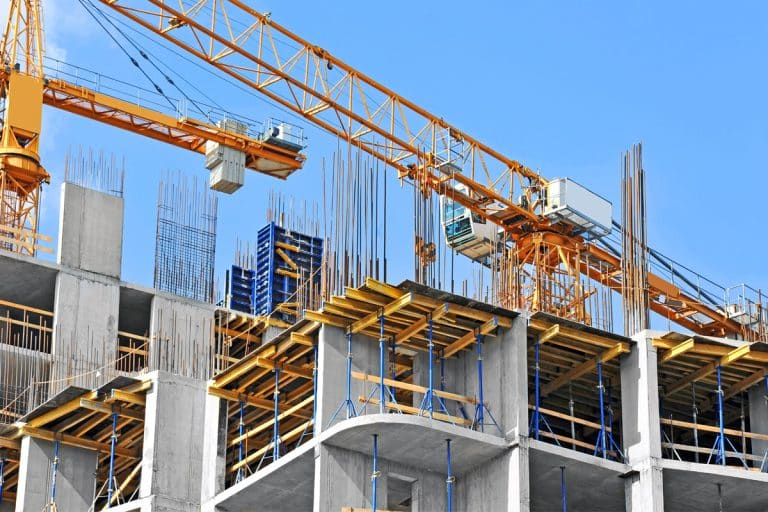
Construction Industry
The integration of CNC routers into construction workflows has ushered in a new era characterized by meticulous detailing, rapid prototyping, and improved material utilization.
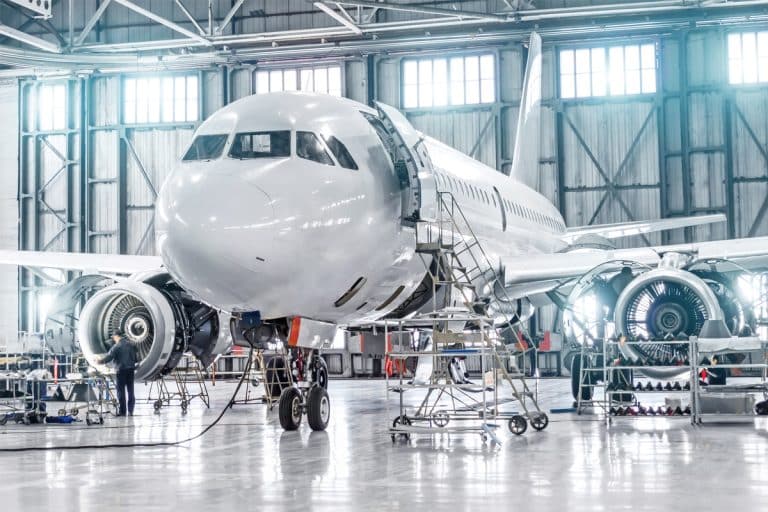
Aerospace Industry
The CNC router is widely used in aerospace engineering due to its unparalleled ability to carve complex designs, manufacture complex parts, and ensure tight tolerances.
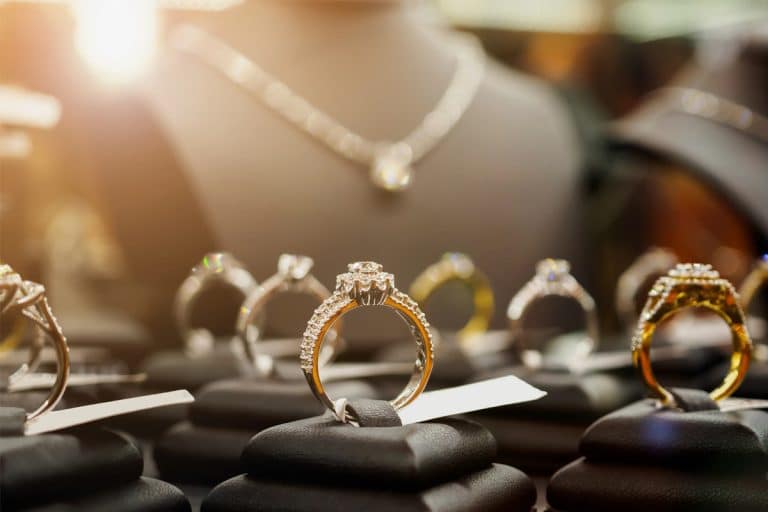
Jewelry Industry
The CNC router revolutionize the way fine jewelry is designed and made by delivering unparalleled precision and efficiency and producing intricate designs with meticulous attention to detail.
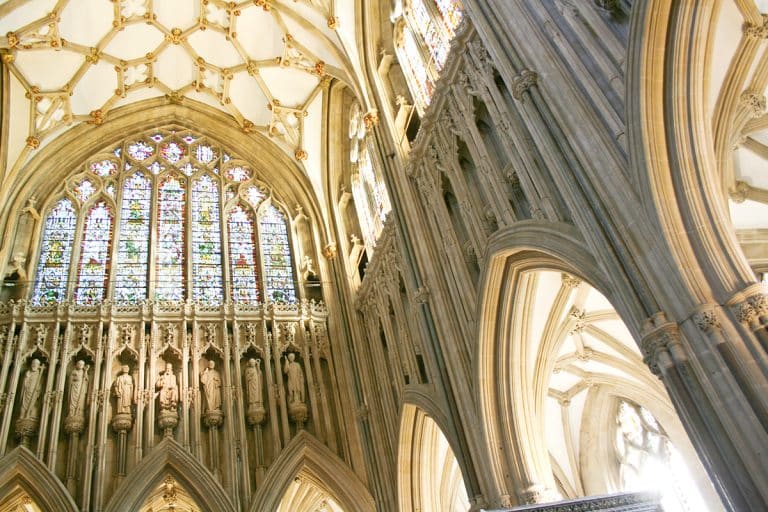
Stone Carving Industry
The integration of CNC routers into the stone carving industry is not only revolutionizing the way craftsmen carve, it is also redefining the boundaries of artistic possibilities in this ancient practice.
Blog
What Causes CNC Router Spindle Overheating?
In this article, we'll explore the common reasons why CNC router spindle temperatures rise beyond safe limits and provide practical solutions to help you prevent or fix the issue before ...
Read More
What is CNC Router Homing and Why is It Important?
CNC router homing is a fundamental process. In this article, we'll break down what CNC router homing is, how it works, and why it's an indispensable part of every machining ...
Read More
What Should I Consider When Buying a CNC Router from an Overseas Supplier?
In this guide, we’ll walk you through the key considerations when buying a CNC router from an overseas supplier to help you make a confident and informed decision.
Read More
How to Choose the Right Vacuum Pump for a CNC Router Vacuum Table?
This guide will walk you through the factors to consider when choosing a vacuum pump for your CNC router vacuum table, helping you make an informed decision based on your ...
Read More
Frequently Asked Questions
How Do Plastic CNC Routers Work?
Plastic CNC routers operate through a combination of computer-controlled movements and cutting tools to precisely shape and carve plastic materials. The process begins by creating a design in CAD (Computer-Aided Design) software, which is then converted into G-code using CAM (Computer-Aided Manufacturing) software. The G-code contains instructions that guide the CNC router’s movements. Here’s a step-by-step overview of how plastic CNC routers work:
- Design Creation: A digital design is created or imported into the CNC system, detailing the geometry, dimensions, and features of the part or product to be made.
- Tool Selection: Based on the material and the design’s complexity, an appropriate cutting tool or router bit is selected. CNC routers often use various tools such as end mills, ball nose bits, or engraving tools.
- Programming the Machine: The design is processed into machine-readable G-code, which provides exact movement instructions for the CNC router. This code tells the machine how fast to move, where to cut, and the tool paths to follow.
- Material Setup: The plastic material is securely placed on the CNC router’s work surface, often with clamps or vacuum systems to hold it in place.
- Cutting Process: The CNC router’s spindle, which holds the tool, moves along multiple axes (usually X, Y, and Z) based on the programmed G-code. The cutting tool engages the plastic material, cutting it to the desired shape with high precision.
- Finishing Touches: Depending on the job, the CNC router may perform additional operations such as engraving, drilling, or sanding for finishing purposes. Dust collection systems are often used to keep the work area clean.
- Final Product: Once the programmed steps are completed, the finished plastic part or component is removed from the machine.
What is the Best Plastic for CNC Routing?
The best plastic for CNC routing largely depends on your project requirements, as different plastics offer varying benefits such as durability, ease of machining, and resistance to wear. However, several plastics are known for their suitability and ease of processing with CNC routers. Here are some of the top options:
- Acrylic (PMMA): Acrylic is a popular choice for CNC routing due to its transparency, ease of processing, and availability in various colors. It’s ideal for applications like signage, displays, and decorative elements.
- Polyethylene (PE): Known for its flexibility and impact resistance, polyethylene is a great option for CNC routing in applications like packaging, containers, and plastic bags.
- Polypropylene (PP): With good chemical resistance and a low moisture absorption rate, polypropylene is often used for CNC routing in automotive parts, packaging, and textiles.
- Polyvinyl chloride (PVC): PVC is cost-effective, rigid, and versatile, making it perfect for applications like signage, modeling, and general industrial use. It’s easy to machine and can be cut, routed, or engraved without much difficulty.
- Polycarbonate (PC): Offering high impact resistance and optical clarity, polycarbonate is used for protective shields, machine guards, and automotive parts that require both strength and transparency.
- High-density polyethylene (HDPE): HDPE is highly durable and resistant to impact, moisture, and chemicals. It’s ideal for cutting boards, general machining, and outdoor applications.
- Polyethylene terephthalate (PET): PET is lightweight, clear, and easy to machine. It’s often used in packaging, beverage bottles, and textiles.
- Polyoxymethylene (POM/Delrin): Known for its strength and excellent machining properties, POM is commonly used in engineering applications, such as gears, bearings, and precision components.
- Nylon (Polyamide): Nylon is known for its high strength, flexibility, and abrasion resistance, making it ideal for CNC routing of mechanical parts like gears and bearings.
- Polyurethane (PU): PU is versatile and has excellent wear resistance, commonly used for prototypes, molds, and parts exposed to high friction or wear.
How Much Do Plastic CNC Routers Cost?
The cost of plastic CNC routers can vary significantly depending on several factors, including the machine’s specifications, size, features, and the complexity of the tasks it is designed for. Generally, plastic CNC routers are priced within the following ranges:
- Entry-Level Plastic CNC Routers: These machines, suitable for small businesses or hobbyists, typically range from $3,000 to $10,000. They are usually smaller in size and offer basic features for cutting and engraving softer plastics like acrylic, PVC, and polyethylene.
- Mid-Range Plastic CNC Routers: These models, designed for medium-sized businesses or industrial applications, can cost between $10,000 and $30,000. They offer better precision, higher spindle speeds, and more advanced features like multi-axis control and automatic tool changers, allowing for more versatile processing of a wider range of plastics.
- High-End Plastic CNC Routers: These machines are often custom-built for specific industrial or production purposes. Prices typically range from $30,000 to $100,000+ depending on the machine’s size, complexity, and advanced features such as multi-head systems, high-speed spindles, precision control, and integration with automated workflows.
What Are the Risks of Using Plastic CNC Routers?
While plastic CNC routers offer numerous advantages for precise cutting, engraving, and shaping of various plastics, their use comes with certain risks. Understanding these risks and taking appropriate precautions can help ensure safe and effective operation. Below are some of the key risks associated with using plastic CNC routers:
- Dust and Debris Hazards: Plastic materials can produce fine dust particles during machining, especially with certain plastics like PVC or acrylic. These particles can be hazardous to health if inhaled and may pose fire risks when accumulated in large quantities. Proper dust extraction systems and personal protective equipment (PPE), such as dust masks and eye protection, are essential to minimize these risks.
- Fire Risk: Some plastics, such as PVC, can release flammable gases and fumes when cut, especially if the cutting parameters (speed, feed rate, etc.) are not properly adjusted. This can increase the risk of fires. It is critical to use the correct cutting parameters, ensure proper ventilation, and have a fire extinguisher or suppression system in place.
- Injury from Moving Parts: CNC routers contain moving parts, such as the spindle and moving axes, which can pose a risk of injury if proper safety protocols are not followed. Operators must be trained in the safe operation of the machine, and safety features like emergency stop buttons, interlocks, and guards should always be in place and functional.
- Material Handling Risks: Improper handling or securing of plastic sheets or workpieces during the machining process can lead to material slippage, resulting in injury or damage to the router. Using appropriate clamps, and fixtures, and ensuring proper material alignment are essential to prevent accidents.
- Electrical Hazards: As CNC routers are electrically powered, there is a risk of electrical shock if proper maintenance and safety procedures are not followed. Regular inspection of electrical wiring, grounding, and safe operation practices are necessary to prevent electrical hazards.
- Heat and Overheating: The cutting process generates heat, and plastic materials like acrylic or polycarbonate can become soft or even melt if not properly managed. Overheating can damage both the material and the CNC router, potentially leading to fire risks. Cooling systems, proper ventilation, and choosing the right spindle speeds can mitigate these issues.
- Chemical Exposure: Certain plastics, like PVC, can release harmful chemicals such as chlorine gas when cut. Prolonged exposure to such chemicals can be harmful to the operator’s health. A well-ventilated workspace and the use of proper filtration systems can help reduce chemical exposure risks.
- Inaccurate Cuts and Machine Damage: Improper machine setup, incorrect cutting parameters, or a lack of calibration can lead to inaccurate cuts, which may result in material wastage or damage to both the workpiece and the machine. Regular maintenance, calibration, and using the correct tools and settings are essential to avoid these risks.
- Tool Wear and Breakage: Plastic CNC routers rely on high-speed cutting tools that can wear out or break over time, especially when machining harder plastics. Using dull tools can lead to poor-quality finishes, increased machine load, and a greater risk of tool failure. Regular tool inspections and replacements are necessary to prevent these issues.
- Noise Pollution: CNC routers can generate high levels of noise, especially when cutting harder plastics. Prolonged exposure to high noise levels can lead to hearing damage for operators. Use of noise-reducing enclosures or ear protection is recommended in such environments.
How Precise Are Plastic CNC Routers?
Plastic CNC routers are renowned for their high precision and ability to produce detailed, intricate designs with remarkable accuracy. The precision of these machines largely depends on the machine type, tooling, and material being used. However, with modern advancements, plastic CNC routers are capable of achieving tolerances as tight as 0.001 inches (0.025mm), ensuring that parts are cut or shaped with great consistency. The following are the key factors that affect accuracy:
- Machine Design & Build Quality: High-quality CNC routers with stable frames, advanced motors, and precision linear guides ensure that the machine can maintain consistent positioning during the routing process. A well-built machine will experience minimal deflection or vibration, which can affect the precision of the cuts.
- Spindle Quality & Speed: The spindle is a crucial part of CNC routers. Higher-speed spindles (typically ranging from 12,000 to 24,000 RPM) allow for cleaner, finer cuts in plastic. A precise spindle with minimal runout ensures that the tool maintains accuracy throughout the machining process.
- Tooling and Tool Wear: The cutting tools used in CNC routers must be sharp and designed for plastic processing. Dull or worn tools can lead to inconsistent cuts, rough edges, or even material deformation. Regular tool maintenance is essential for maintaining high precision.
- Material Properties: Plastics, such as acrylic, polycarbonate, or PVC, have different behaviors when machined, which can impact the CNC router’s ability to achieve precise cuts. Softer plastics may cut more easily and with higher precision, while tougher plastics might require more adjustments in machine settings to achieve the desired precision.
- Software and Control Systems: Advanced software and CNC controllers enable accurate programming and control of the CNC router. CNC programs are responsible for the precision of tool paths, and properly configured software ensures that the cuts follow the exact design specifications.
- Calibration and Maintenance: Regular calibration and maintenance of the CNC router, including checking alignment, ensuring correct tool offsets, and updating machine parameters, will keep precision levels high. Periodic recalibration guarantees that the CNC router stays true to its design specifications over time.
What Is The Expected Lifespan of Plastic CNC Routers?
The expected lifespan of a Plastic CNC router depends on a variety of factors, including machine quality, maintenance practices, and operating conditions. On average, a well-maintained plastic CNC router can last anywhere from 10 to 20 years or more. However, the actual lifespan can vary significantly based on how the machine is used and cared for over time. The following are the key factors that affect the life of plastic CNC routers:
- Build Quality and Design: High-quality machines made from durable materials and superior craftsmanship tend to last longer. Industrial-grade CNC routers with solid frames, advanced motors, and precision components are built to endure longer periods of high-performance use compared to lower-end models designed for lighter workloads.
- Regular Maintenance: Proper and regular maintenance is crucial to extending the lifespan of a CNC router. This includes routine cleaning, lubrication, calibration, and replacing worn parts such as cutting tools, bearings, and spindles. Machines that are well-maintained experience fewer breakdowns, maintaining their accuracy and functionality over a longer period.
- Operational Environment: The environment in which the CNC router is operated significantly affects its longevity. A clean, dry, and controlled environment will prevent excessive wear from dust, humidity, and temperature fluctuations, which can shorten the lifespan of the machine. Proper ventilation is also critical to prevent overheating, especially for spindles and motors.
- Usage Frequency: Machines used frequently in heavy-duty applications will generally wear down faster than those used for light, occasional tasks. Frequent operations in high-load applications, such as cutting dense or tough plastics, can accelerate wear on key components, reducing the overall lifespan of the machine.
- Software and Technology: Over time, software and control systems can become outdated, which may limit the machine’s functionality or compatibility with new technologies. Regular software updates and keeping the system in sync with modern advancements can help ensure a longer productive life for the CNC router.
- Tooling and Spindle Care: The spindle and cutting tools are some of the most important and frequently replaced components of a CNC router. Proper care, such as monitoring spindle performance and using the correct tools for specific tasks, can greatly impact the longevity of the machine. Regular inspection and timely replacement of worn parts can avoid damaging the entire system.
What Customer Support Do Plastic CNC Routers Provide?
Plastic CNC routers come with reliable customer support options to ensure smooth operation and user satisfaction:
- Free Online Technical Support: Customers can access complimentary technical assistance through online platforms, including email, chat, or video support. This service is ideal for troubleshooting, software setup, or resolving operational issues remotely.
- Paid On-Site Training: For users requiring hands-on guidance, on-site training sessions are available at an additional cost. These sessions cover installation, operation, and maintenance to ensure optimal use of the machine.
What Is The Warranty Period of Plastic CNC Routers?
Our CNC router is backed by a comprehensive warranty designed to give you peace of mind and protect your investment:
- 3-Year Warranty for the Entire Machine: This full warranty covers any defects or malfunctions in the machine as a whole, ensuring reliable performance and longevity over time.
- 5-Year Warranty for Core Components: Key components essential for optimal machine operation are covered for 1.5 years. This includes parts that may experience wear and tear with regular use, ensuring you have support for the most vital parts of the machine.