2030 CNC Router
The 2030 CNC router series represents a new benchmark in precision, efficiency, and versatility for both industrial and commercial applications. Engineered with advanced technology and robust materials, these machines cater to a wide range of industries, including woodworking, metalworking, sign-making, and furniture production. Whether you are a seasoned professional or a business looking to scale operations, the 2030 CNC router offers an ideal combination of performance, reliability, and ease of use. At the core of the 2030 CNC router’s appeal is its expansive 2000mm x 3000mm working area, allowing for the seamless processing of large-scale materials without compromising on detail or accuracy. Equipped with high-speed spindles, state-of-the-art drive systems, and intuitive software compatibility, these CNC routers deliver impeccable cuts, engravings, and carvings at unparalleled speeds.
Durability and precision go hand-in-hand with the 2030 CNC series. Built with a heavy-duty frame and innovative motion control systems, these machines ensure stability and accuracy even during intensive use. Customization options like multi-heads, vacuum tables, and dust extraction systems further enhance their versatility, making them adaptable to diverse project needs. Whether your focus is efficiency, precision, or scalability, the 2030 CNC router series is designed to exceed expectations. Step into the future of manufacturing with tools built to empower creativity and optimize production workflows.
-
AKM2030 CNC Router
Rated 5.00 out of 5$6,000.00 Add to cart -
AKM2030C CNC Router
Rated 5.00 out of 5$14,600.00 Add to cart -
AKM2030-4A CNC Router
Rated 5.00 out of 5$16,200.00 Add to cart -
AKM2030C-4A CNC Router
Rated 5.00 out of 5$21,200.00 Add to cart -
AKM2030-R CNC Router
Rated 5.00 out of 5$6,700.00 Add to cart -
AKM2030-4R CNC Router
Rated 5.00 out of 5$10,200.00 Add to cart
Tips for Choosing the Right 2030 CNC Router
Selecting the right 2030 CNC router is an essential decision that can impact your productivity, project quality, and overall business success. With numerous features and configurations available, finding the right match requires understanding your specific needs, from materials and workspace requirements to precision and long-term scalability.
Define Your Application Needs
Identify your primary applications, whether it’s woodworking, metal fabrication, signage, or furniture production. Each industry has unique requirements, such as spindle power for heavy-duty cutting or precise engraving capabilities for intricate designs. Understanding your specific needs helps narrow down models with features tailored to your projects. The right machine ensures optimal results and minimizes the risk of operational inefficiencies.
Confirm Material Compatibility
The materials you plan to use—whether wood, plastics, metals, or composites—dictate the required spindle power, cutting tools, and speed settings. For instance, softer materials benefit from high-speed spindles, while metals demand more robust and slower cutting systems. Ensure the router you choose can handle your materials’ size, density, and specific requirements to maintain accuracy and efficiency.
Evaluate Workspace and Project Sizes
The 2030 CNC router offers a 2000mm x 3000mm working area, ideal for larger projects. Consider whether this workspace is sufficient for your typical material sizes and designs. Account for additional space for clamps, fixtures, or tool setups. Ensuring compatibility with your production environment reduces workflow interruptions and maximizes efficiency.
Assess Spindle Power and Speed
A CNC router’s spindle power impacts its ability to cut through various materials. Higher-power spindles are suited for dense or thick materials, while high-speed spindles are better for fine details on softer substrates. Determine the spindle requirements based on your project demands to ensure consistent performance and minimize wear on tools.
Check the Drive and Motion Systems
The router’s drive system directly affects speed and precision. Rack-and-pinion systems offer fast, efficient movement for general projects, while ball screw systems provide superior accuracy, ideal for intricate detailing. Choose a system that aligns with your project requirements, balancing speed with the level of precision needed.
Review Software Integration
The CNC router should integrate seamlessly with your preferred design software, such as AutoCAD, Fusion 360, or VCarve. Compatibility ensures a smooth transition from design to production, minimizes errors and boosts productivity. If the router includes proprietary software, ensure it supports your project’s complexity and is easy to learn.
Prioritize Build Quality and Rigidity
Durability and stability are critical for reliable performance. Look for a CNC router with a heavy-duty steel or aluminum frame to withstand high-speed operations without vibrations. Structural rigidity ensures accurate cuts, reduces maintenance needs, and prolongs the machine’s lifespan, making it a more cost-effective investment.
Look for Automation Features
Automation features like tool changers, vacuum tables, and dust collection systems enhance efficiency. Tool changers allow smooth transitions between cutting tools, vacuum tables secure materials for precise cuts, and dust collectors maintain a clean workspace. These features streamline workflows and are particularly beneficial for high-volume or complex projects.
Consider Maintenance and Ease of Use
Routine maintenance is crucial for keeping your CNC router in top condition. Look for features like automatic lubrication systems and easy-access components to simplify upkeep. Additionally, ensure the machine’s controls are intuitive and user-friendly, reducing the learning curve and minimizing downtime during operation.
Balance Speed and Precision
For businesses focusing on high-volume production, fast-cutting speeds are essential. Conversely, tasks requiring intricate detailing or tight tolerances demand precision-focused features like advanced motion control and linear guide rails. Choose a router that balances speed and accuracy to suit your specific production needs.
Assess Customization Options
Select a CNC router with customizable features to adapt to evolving project requirements. Add-ons like multi-tool heads, rotary axes, or advanced clamping systems increase versatility and allow the router to handle diverse tasks efficiently. Customization ensures the machine remains a valuable asset as your needs grow.
Compare Costs and ROI
While price is a major factor, prioritize value over upfront cost. Consider features that enhance productivity, minimize operating costs, and ensure durability. Investing in a higher-quality machine may provide a better return on investment through increased efficiency and reduced maintenance expenses over time.
What Materials Can the CNC Router Cut?
The 2030 CNC router is a versatile machine designed to handle a wide variety of materials with precision and efficiency. Its powerful spindle, advanced motion control systems, and customizable tool options make it capable of cutting, carving, and engraving everything from soft materials like wood, foam, and plastics to tougher substrates such as aluminum, brass, and composite panels. This flexibility makes it suitable for diverse industries, including woodworking, metal fabrication, and signage production.
Whether you’re creating intricate designs in hardwood, cutting clean edges on acrylic, or machining durable metal parts, the 2030 CNC router delivers consistent, high-quality results. Its adaptability ensures that regardless of your material choice, it can meet the demands of any project.
Application Industry
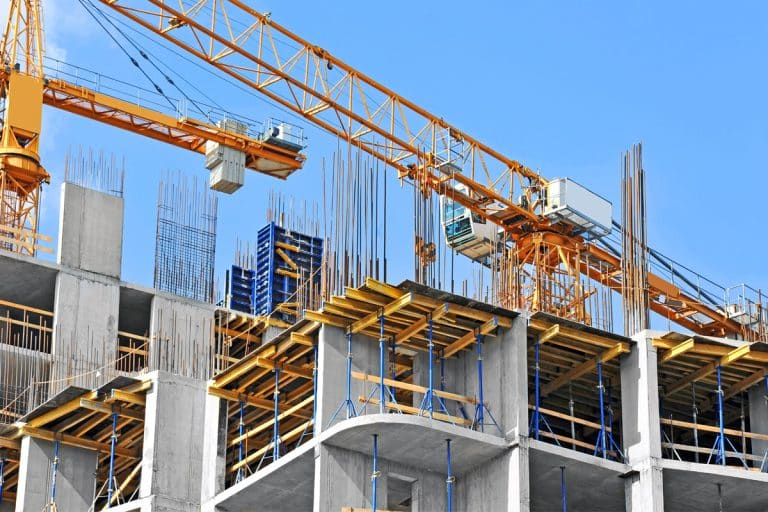
Construction Industry
The integration of CNC routers into construction workflows has ushered in a new era characterized by meticulous detailing, rapid prototyping, and improved material utilization.
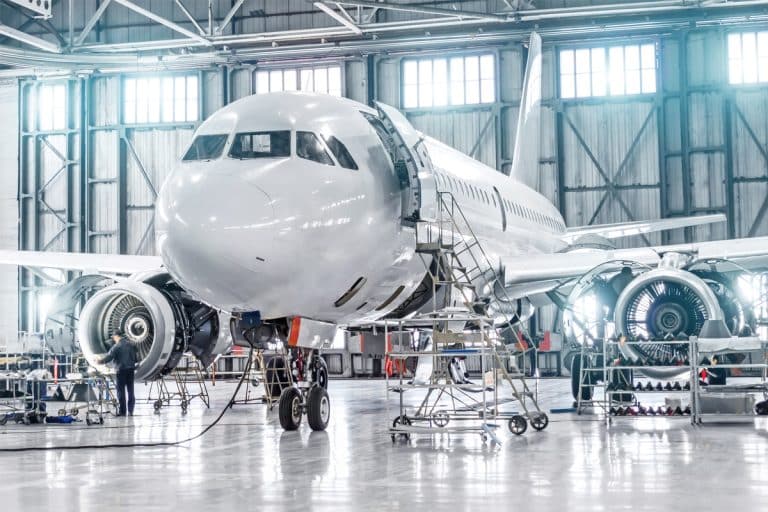
Aerospace Industry
The CNC router is widely used in aerospace engineering due to its unparalleled ability to carve complex designs, manufacture complex parts, and ensure tight tolerances.
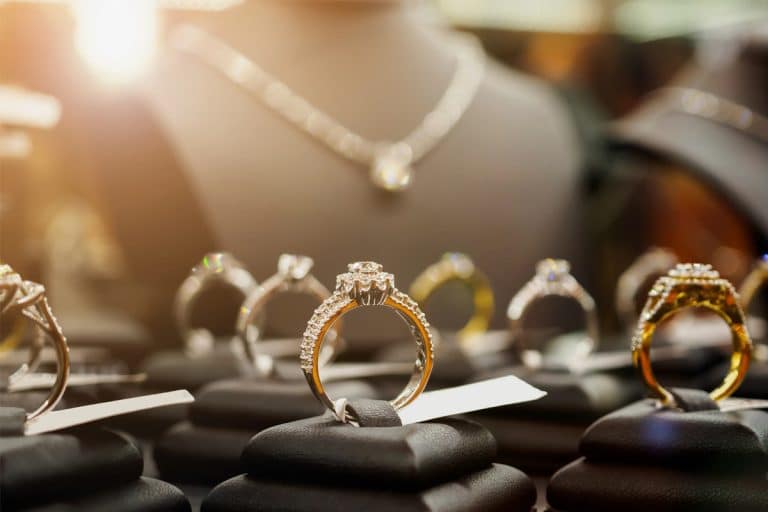
Jewelry Industry
The CNC router revolutionize the way fine jewelry is designed and made by delivering unparalleled precision and efficiency and producing intricate designs with meticulous attention to detail.
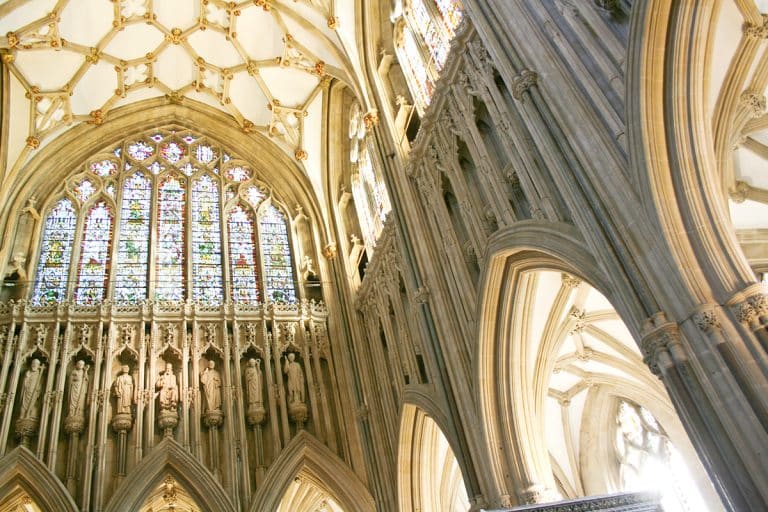
Stone Carving Industry
The integration of CNC routers into the stone carving industry is not only revolutionizing the way craftsmen carve, it is also redefining the boundaries of artistic possibilities in this ancient practice.
Blog
What is CNC Router Homing and Why is It Important?
CNC router homing is a fundamental process. In this article, we'll break down what CNC router homing is, how it works, and why it's an indispensable part of every machining ...
Read More
What Should I Consider When Buying a CNC Router from an Overseas Supplier?
In this guide, we’ll walk you through the key considerations when buying a CNC router from an overseas supplier to help you make a confident and informed decision.
Read More
How to Choose the Right Vacuum Pump for a CNC Router Vacuum Table?
This guide will walk you through the factors to consider when choosing a vacuum pump for your CNC router vacuum table, helping you make an informed decision based on your ...
Read More
How Do I Ensure Electrical Safety with a CNC Router?
In this article, we'll explore the key steps to ensure the electrical safety of CNC routers, from proper installation to operator training, to provide you with guidance to ensure electrical ...
Read More
Frequently Asked Questions
What Are 2030 CNC Routers Used For?
2030 CNC routers are highly versatile machines used across a wide range of industries for cutting, carving, engraving, and machining various materials. With their large 2000mm x 3000mm working area, they are ideal for producing large-scale projects with precision and efficiency. These routers are widely employed in woodworking for crafting furniture, cabinetry, and decorative panels.
They are also popular in sign-making, where they create intricate designs on plastics, acrylics, and composites. Additionally, industries like prototyping, aerospace, and manufacturing use these routers to produce accurate components and detailed prototypes.
What Types of 2030 CNC Routers Are There?
2030 CNC routers come in various configurations to meet different operational needs and levels of complexity. Each type has distinct features and capabilities:
- 3-Axis CNC Router: The most basic and widely used type, perfect for cutting, engraving, and carving flat materials in 2D applications.
- ATC CNC Router: Featuring an Automatic Tool Changer, this CNC router is designed for high efficiency, allowing seamless tool changes during complex workflows.
- 4-Axis CNC Router: Provides rotational capabilities, enabling the machining of curved and cylindrical surfaces for more intricate projects.
- 4-Axis ATC CNC Router: Combines the versatility of a 4-axis CNC router with the efficiency of automatic tool changes, ideal for advanced multi-tool operations.
- 5-Axis CNC Router: The most versatile option, allowing simultaneous movement along five axes for creating complex, multi-dimensional parts and designs.
- Rotary Axis CNC Router: Equipped with a dedicated CNC rotary axis, this router specializes in carving cylindrical objects like columns, and poles.
How Much Are 2030 CNC Routers?
The cost of a 2030 CNC router depends on the type, features, and capabilities. Here’s an overview of price ranges for different models:
- 3-Axis CNC Router: Ranges from $3,000 to $6,500, offering affordability for basic cutting, carving, and engraving tasks.
- ATC CNC Router: Priced between $6,000 and $20,000, featuring an Automatic Tool Changer for enhanced productivity and multi-tool workflows.
- 4-Axis CNC Router: Costs $10,000 to $18,000, providing rotational capabilities for machining curved and cylindrical surfaces.
- 4-Axis ATC CNC Router: Ranges from $19,000 to $25,000, combining 4-axis functionality with an Automatic Tool Changer for complex operations.
- 5-Axis CNC Router: The most advanced option, priced between $55,000 and $70,000, is ideal for multi-dimensional and high-precision machining.
- Rotary Axis CNC Router: Costs $5,000 to $15,000, specializing in carving cylindrical objects like posts and columns.
What Is the Spindle Power of 2030 CNC Routers?
The spindle power of 2030 CNC routers varies depending on the type of machine and its intended applications. Here’s a breakdown of spindle power for different models:
- 3-Axis CNC Router: Features a spindle power of 3.0-3.5KW, suitable for basic cutting and carving tasks on a variety of materials.
- ATC CNC Router: Equipped with a 9KW spindle, offering robust power for efficient, multi-tool operations.
- 4-Axis CNC Router: Comes with a spindle power range of 6.0-9.0KW, ideal for machining curved and cylindrical surfaces.
- 4-Axis ATC CNC Router: Includes a 9.0KW spindle, combining high power and automated tool-changing capabilities.
- 5-Axis CNC Router: Powered by a 10KW spindle, providing exceptional strength for complex, multi-dimensional machining.
- Rotary Axis CNC Router: Features a spindle power of 2.2-3.5KW, specializing in carving cylindrical objects with precision.
How Precise Are 2030 CNC Routers?
2030 CNC routers are renowned for their exceptional precision, making them ideal for projects requiring detailed cuts, carvings, and engravings. These machines typically achieve accuracy levels of ±0.01mm to ±0.03mm, depending on the model and configuration.
Features such as high-quality linear guide rails, advanced motion control systems, and rigid frames contribute to their accuracy by minimizing vibrations and ensuring stable operation. Additionally, models with ball screw drive systems provide enhanced precision, particularly for intricate designs and tight tolerances.
Whether you’re crafting detailed woodwork, machining metal components, or creating intricate prototypes, 2030 CNC routers deliver consistent, high-precision results across a variety of materials.
Do 2030 CNC Routers Support Adding Accessories?
Yes, 2030 CNC routers support a variety of accessories to enhance their versatility and efficiency for different applications. These add-ons allow users to expand the machine’s capabilities and tailor it to specific project requirements. Commonly supported accessories include:
- Rotating Axis: Enables precise machining of cylindrical objects like columns and posts.
- 360° Rotating Cutting Saw: Ideal for complex angular cuts and unique design requirements.
- Drilling Unit: Adds high-speed drilling capabilities for creating clean, accurate holes.
- Oscillation Knife Head: Perfect for cutting soft and flexible materials like foam, leather, or rubber.
- Plasma Cutting Head: Allows for high-precision cutting of metal sheets, expanding the router’s material compatibility.
- Auto Loading & Unloading Device: Streamlines material handling, improving efficiency in high-volume production environments.
What Customer Support Do 2030 CNC Routers Provide?
2030 CNC routers come with reliable customer support options to ensure smooth operation and user satisfaction:
- Free Online Technical Support: Customers can access complimentary technical assistance through online platforms, including email, chat, or video support. This service is ideal for troubleshooting, software setup, or resolving operational issues remotely.
- Paid On-Site Training: For users requiring hands-on guidance, on-site training sessions are available at an additional cost. These sessions cover installation, operation, and maintenance to ensure optimal use of the machine.
What Is The Warranty Period of 2030 CNC Routers?
Our CNC router is backed by a comprehensive warranty designed to give you peace of mind and protect your investment:
- 3-Year Warranty for the Entire Machine: This full warranty covers any defects or malfunctions in the machine as a whole, ensuring reliable performance and longevity over time.
- 5-Year Warranty for Core Components: Key components essential for optimal machine operation are covered for 1.5 years. This includes parts that may experience wear and tear with regular use, ensuring you have support for the most vital parts of the machine.