Plywood CNC Router
The plywood CNC router is a computer numerical control (CNC) machine specifically designed for precise and efficient cutting and shaping of plywood. The plywood CNC routers utilize computer programs to control the movement of cutting tools, enabling complex designs and precise cuts on the plywood surface. The machine’s bed accommodates standard plywood sizes, and the CNC router can be programmed to cut complex patterns, holes, or contours with high precision.
The plywood CNC routers are widely used in various industries, including carpentry, furniture manufacturing, and architectural model making. The ability to automate and customize cutting makes it valuable for the mass production of complex designs. Users can input digital designs into CNC software, and the CNC router translates these designs into physical cuts on plywood, ensuring consistency and reducing manual labor. Overall, the plywood CNC router increases productivity and enables the creation of complex plywood products efficiently and accurately.
Tips For Choosing The Right CNC Router For Plywood
From assessing work area needs to delving into spindle power, we provide insightful guidance to help you make informed decisions. Whether you’re a seasoned professional or new to CNC routing, discover key considerations to ensure your selection fits your project requirements seamlessly.
Working Area Requirements
Determine the size of the plywood you will be using. Choose a CNC router with a work area that can easily accommodate the largest sheet sizes you anticipate using, allowing for comfortable operation and efficient processing. Consider a machine with a slightly larger work area to allow for flexibility in project size.
Automatic Tool Changer
Evaluate whether your project involves a variety of cuts that require different tools. If so, consider a CNC router with an automatic tool changer (ATC) system. The ATC feature allows for a seamless transition between tools during the cutting process, saving time and improving overall efficiency.
Spindle Power And Speed
Evaluate spindle power and speed based on the thickness and density of the plywood you want to cut. Higher spindle power helps cut thicker materials, while variable speed allows for the versatility to handle different cuts. Choose a spindle power and speed combination that suits the range of materials you plan to machine.
Cutting Accuracy Requirements
Define your cutting accuracy requirements. Consider the precision your projects require, especially if they involve complex designs or fine details. If your project requires intricate details or tight tolerances, prioritize a high-precision CNC router to consistently achieve the desired results.
Advanced Features
Determine if your project requires advanced functionality beyond basic cutting. For example:
- 4or 5-axis functionality: enables more complex multi-faceted machining.
- Rotary axis: Can be used to create cylindrical or curved components.
Other Things To Note
- Check the rigidity and build quality of your CNC milling machine. The sturdy frame helps increase stability and reduce vibration to maintain cutting accuracy.
- Consider a dust collection system. Effective dust removal not only keeps your workspace clean, it also helps extend the life of your machine.
- Evaluate the CNC router’s compatibility with the design software you plan to use.
- Consider the level of customer support and training provided by the manufacturer.
What types of plywood can the plywood CNC router cut?
The wood CNC router can engrave various types of wood, both hardwoods and softwoods. The suitability of a wood type for engraving largely depends on its hardness, grain structure, and the specific CNC router’s capabilities. Here are some common wood types that can be engraved with a CNC router:
- Softwood Plywood
- Hardwood Plywood
- Marine Plywood
- Exterior Plywood
- Interior Plywood
- Baltic Birch Plywood
- MDF Core Plywood
- Melamine-Coated Plywood
- Particleboard-Core Plywood
Application Industry
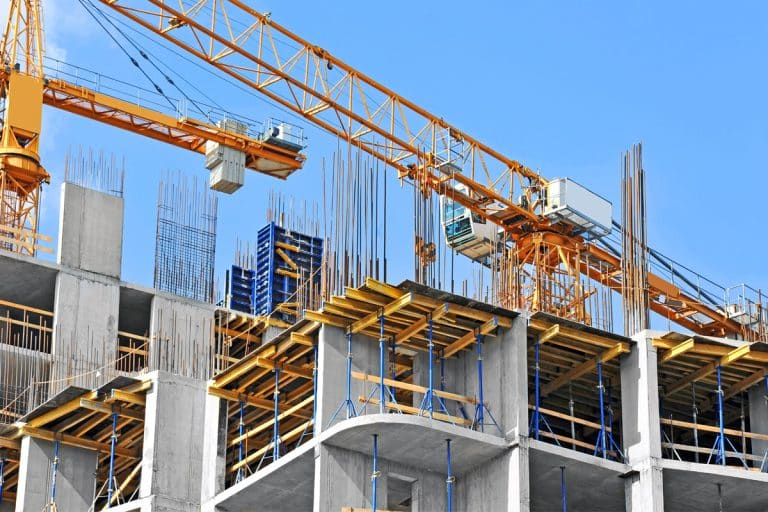
Construction Industry
The integration of CNC routers into construction workflows has ushered in a new era characterized by meticulous detailing, rapid prototyping, and improved material utilization.
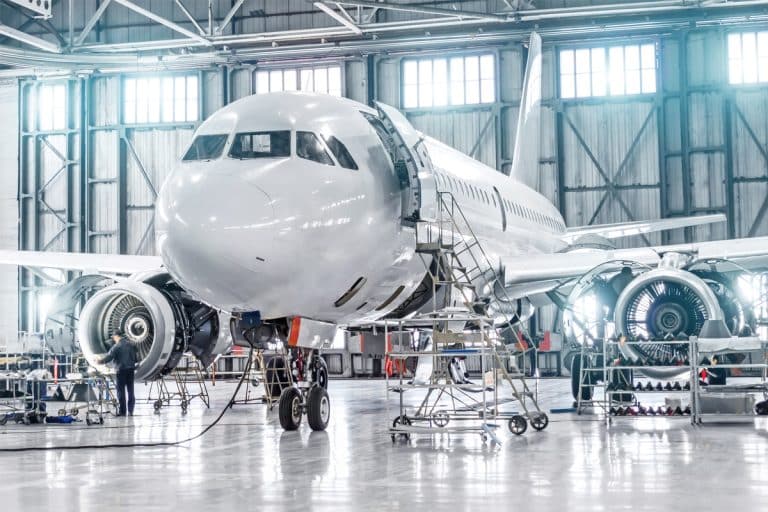
Aerospace Industry
The CNC router is widely used in aerospace engineering due to its unparalleled ability to carve complex designs, manufacture complex parts, and ensure tight tolerances.
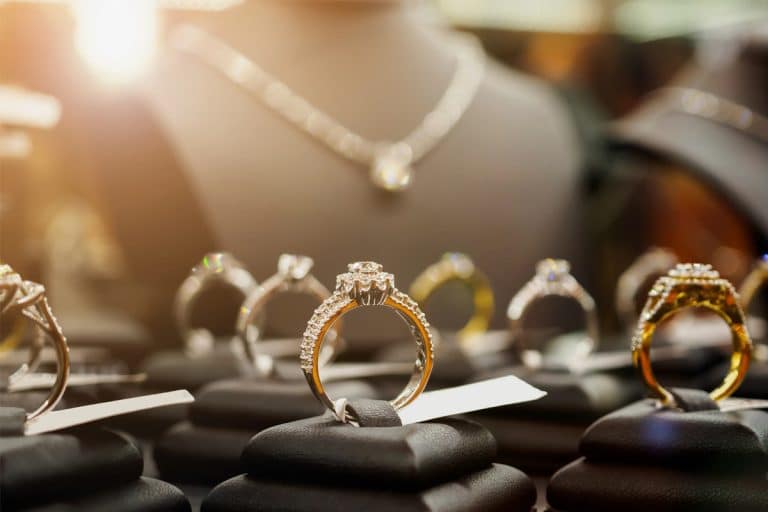
Jewelry Industry
The CNC router revolutionize the way fine jewelry is designed and made by delivering unparalleled precision and efficiency and producing intricate designs with meticulous attention to detail.
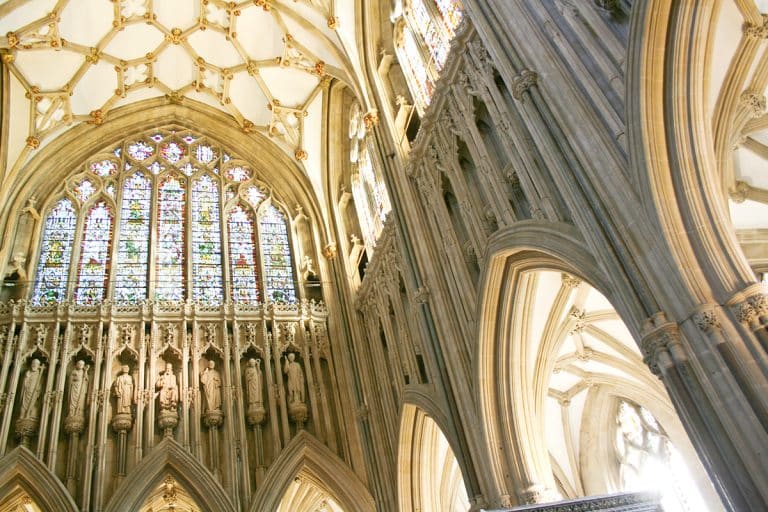
Stone Carving Industry
The integration of CNC routers into the stone carving industry is not only revolutionizing the way craftsmen carve, it is also redefining the boundaries of artistic possibilities in this ancient practice.
Blog
How to Reduce the Impact of Workpiece Adhesion on CNC Router Cutting Quality
This article delves into practical strategies for mitigating the impact of workpiece adhesion on CNC router cutting quality, to improve the performance and reliability of CNC router operations.
Read More
Addressing Environmental Concerns in CNC Router Waste Disposal: A Comprehensive Guide
In this article, we delve into the considerations for the correct disposal of waste materials from CNC router operations, aiming to tackle the environmental challenges posed by CNC waste.
Read More
Guide to Optimizing CNC Router Parameters for Diverse Materials
This article provides a systematic parameter optimization method for CNC routers cutting different materials, aiming to provide users with the necessary knowledge to achieve excellent processing quality.
Read More
Understanding the Perils of Spindle Runout in CNC Routers
This article delves into the causes of spindle runout and strategies for mitigating its effects, aiming to provide you with the knowledge to optimize CNC router performance.
Read More
Mastering CNC Router Worktables: A Comprehensive Guide
This article delves into the CNC router types, operating methods, maintenance, and customization options, providing you with the knowledge to optimize your CNC router settings for superior results.
Read More
CNC Router Bits: Complete Buyer’s Guide
From understanding the different types of CNC router bits to deciphering the nuances of materials and coatings, this guide provides the essential reference for finding the right bit for your ...
Read More
Frequently Asked Questions
Can a CNC router cut plywood?
Yes, CNC routers are specifically designed for precise cutting of plywood and a variety of other materials. In fact, cutting plywood is one of the main applications of CNC routers in woodworking and related industries. CNC routers use computer-controlled precision to cut and shape materials, making them efficient and precise. Here’s how a CNC router cuts plywood:
- Digital design: First, use computer-aided design (CAD) software to create a digital design or model of the desired plywood cut.
- Programming the CNC router: The digital design is then converted into a set of instructions, or G-code, that the CNC router can understand. This code directs the movement of the CNC router, specifying tool path, speed, and depth.
- Fix the plywood: Firmly fix the plywood on the CNC router’s workbench. This is usually done using a vacuum table, clamps, or other methods to ensure stability during the cutting process.
- Tool selection: Select the appropriate cutting tool based on the cut required and the type of plywood. Common tools include straight router bits for straight cuts and ball-head or V-shaped router bits for complex designs.
- Precision cutting: The CNC router then follows the programmed tool path to cut the plywood with high precision. The computer-controlled nature of the process ensures consistency and accuracy across multiple components.
What is the best plywood for CNC cutting?
The best plywood for CNC cutting depends on the specific requirements of your project, but certain types are generally favored due to their consistent quality, stability, and suitability for CNC processing. Here are a few types of plywood that are generally considered suitable for CNC cutting:
- Birch plywood: Birch plywood offers fine grain, stability, and strength. It is a popular choice for CNC cutting due to its smooth surface and ability to retain intricate details.
- Baltic birch plywood: Baltic birch plywood features high-quality veneer and no voids. It is available in a variety of thicknesses and is often used for intricate designs and fine woodwork.
- MDF core plywood: Plywood with a medium-density fiberboard (MDF) core provides a smooth and consistent surface. The MDF core provides stability and reduces the risk of voids, making it suitable for CNC cutting applications requiring a smooth surface.
- Marine plywood: Marine plywood is designed to resist moisture and is suitable for projects where the material may be exposed to water. It features high-quality veneer and durable glue, making it a good choice for CNC cutting in applications that require waterproofing.
- Melamine-coated plywood: Melamine-coated plywood has a durable and smooth surface due to its melamine covering. This type of plywood is often chosen for projects where the finished look is important, such as cabinets and furniture.
- Hardwood plywood: Hardwood plywood, such as oak, maple, and walnut, is chosen for its durability and beauty. It can be adapted for CNC cutting when a specific wood surface treatment is required.
- Plywood with veneer options: Certain projects may benefit from plywood with veneer options such as cherry, mahogany, or teak. These veneers can add decorative elements to CNC-cut parts.
What kind of router bit for plywood?
Choosing the right router bit for plywood depends on the specific requirements of your project, including the type of cuts you need and the characteristics of the plywood. Here are some common types of router bits suitable for working with plywood:
- Straight router bit: This is a versatile option for straight cuts and basic edge profiles. It is suitable for cutting plywood sheets to size or creating straight edges on the material.
- Spiral upcut router bit: A spiral upcut bit is excellent for chip evacuation, making it suitable for deep cuts and slots in plywood. It pulls chips away from the workpiece, reducing the risk of chip buildup.
- Spiral downcut router bit: This bit is suitable for achieving clean top surfaces on plywood. It pushes the chips down into the cut, minimizing chip-out on the top side of the material. It’s often used when a clean finish is essential.
- Compression router bit: Compression bits have both upcut and downcut sections. They are effective for reducing chip-out on both the top and bottom surfaces of plywood, making them suitable for projects where a clean finish is crucial.
- Flush trim router bit: Flush trim bits are ideal for trimming the edges of plywood to match a template or to achieve a precise edge. They come in top-bearing and bottom-bearing styles.
- V-groove router bit: V-groove bits are used for creating decorative grooves or chamfers in plywood. They can add design elements to your projects.
- Spoil board surfacing bit: When working on a spoil board or sacrificial surface beneath the plywood, a spoil board surfacing bit is used to level and flatten the surface for consistent cuts.
- Rabbeting router bit: Rabbeting bits are suitable for creating rabbets or recessed edges in plywood. They are commonly used for joining pieces of plywood together.
- Ball nose router bit: Ball nose router bits are ideal for 3D contouring and carving in plywood. They are suitable for creating rounded or curved features in the material.
How do you router plywood without splintering?
When routing plywood, minimizing or preventing splintering helps achieve a feel and professional-looking cut. Here are some tips to help you route plywood without cracking:
- Use a high-quality router bit: Purchase a high-quality router bit designed for woodworking, preferably one with a sharp carbide blade. Blunt router bits are more likely to tear wood fibers, causing splits. If necessary, replace or sharpen the router bit.
- Choose the right type of router bit: Choose a router bit that is suitable for plywood cutting. Spiral upcut or compression router bits are usually the first choices to reduce cracking on the top surface, while spiral downcut router bits help reduce cracking on the bottom surface.
- Adjust the feed speed: Adjust the CNC router’s feed speed to match the type and thickness of the plywood. Feeding too fast can cause tearing, while feeding too slow can cause burning. It is recommended to try different feed speeds to find the best speed for your specific plywood and router bit.
- Use backing board: Place a piece of sacrificial backing board or scrap under the plywood to support the wood fibers and reduce tearing on the bottom surface. Replace the backing plate as needed to maintain its effectiveness.
- Apply masking tape: Applying masking tape to the area you plan to cut can help reduce splintering by providing extra support for the wood fibers. Make sure to score the tape along the cut line to prevent it from lifting.
- Downcut helical router bit: Consider using a downcut helical router bit, especially for cuts that exit material from the bottom. The cutting bit pushes the wood fibers downward, minimizing splitting on the top surface.
- Multiple routing: If you want to make deep cuts, consider dividing the routing process into multiple times. Taking a shallow path reduces stress on the wood fibers and minimizes the chance of splintering.
What is the depth of cut for CNC plywood?
The appropriate cutting depth for CNC plywood depends on several factors, including the type of plywood, the specific characteristics of the CNC router, and the type of cut you are making. Here are some general guidelines to help determine the depth of CNC plywood cuts:
- Material thickness: Cutting depth should be adjusted based on the thickness of the plywood. Typically when cutting plywood it is recommended to make multiple shallow passes rather than one deep pass, especially if you are cutting the entire thickness of the material.
- Routerbit diameter: The diameter of the mill bit you use plays a vital role in determining the maximum depth of cut. Larger-diameter drill bits can usually handle deeper cuts. Check the manufacturer’s recommendations for your specific router bit.
- Machine power: Consider the power of the CNC router. A more powerful machine may be able to handle deeper cuts more efficiently. However, pushing the machine beyond its limits can cause problems such as burning, chattering, or reduced cut quality.
- Material type: The type of plywood will affect the depth of the cut. Some plywood may have harder or softer layers, affecting how the router bit interacts with the material. Adjust the depth to the specific characteristics of the plywood being used.
- Router bit type: Different types of router bits may have specific cutting depth recommendations. Please refer to the manufacturer’s guidelines for the router bit you are using to ensure optimal performance.
- Cutting strategy: The type of cut you make also affects the depth. For roughing passes, you can use deeper cuts, while finishing passes typically involve shallower cuts to achieve a smooth surface.
- Multiple passes: To minimize the risk of tearing and get a cleaner finish, consider making multiple passes at increasing depths. This helps reduce the load on the router bit and minimizes the risk of tearing.
- Router bit engagement: Consider the engagement of the router bit in the material. Excessive engagement will cause excessive heating and wear of the router bit. Adjust the depth of the cut to ensure proper chip evacuation and cooling.
- Toolpath complexity: Toolpath complexity and design complexity may also affect the depth of the cut. Complex designs may require shallower cuts to maintain accuracy.
Does plywood dull router bits?
Yes, plywood can cause router bits to dull over time. Plywood is made from layers of wood veneers bonded together with adhesives, resins, or abrasive hard particles. These particles wear away at the cutting edge of the router bit. Here are some factors that can cause your router bits to become dull when working with plywood:
- Adhesives and resins: The glue used in plywood often contains hard particles that can wear down the router bit’s cutting edge. Repeated exposure to these abrasive particles can cause darkening over time.
- Hard particles in the wood: Some plywood may have layers of harder particles, which can be more abrasive and cause the router bit to wear out faster.
- Material density: The density of plywood varies depending on the type of wood used and the manufacturing process. Dense plywood may exert greater force on the router bit’s cutting edge, causing faster wear.
- Chip removal: If chips and debris are not effectively removed during the routing process, they will accumulate around the cutting edge, causing friction and heat, which can lead to dulling.
- Frequency of use: The more frequently you use a CNC router to cut plywood, the faster the router bits will become dull. Heavy or continuous use will accelerate wear.
- Improper feed or speed: Using the wrong feed or cutting speed for a specific plywood and CNC router can cause premature dulling. Feed rates that are too high or cutting speeds that are too low can generate too much heat, causing faster wear.
- Use a high-quality router bit: Buy a high-quality router bit made of durable materials such as carbide. Carbide router bits are known for their hardness and wear resistance.
- Use the correct router bit type: Choose a router bit designed for cutting plywood. Spiral top-cut router bits are often used on plywood because they aid in chip evacuation.
- Inspect and maintain router bits: Check router bits regularly for signs of wear, such as dull or chipped edges. Sand or replace them as needed to ensure optimal cutting performance.
- Adjust speed and feed rate: Optimize the speed and feed rate of the CNC router to prevent overheating and excessive wear of the milling cutter. Running the machine at the correct speed helps extend tool life.
- Consider coated router bits: Coated router bits, such as those with carbide coatings or special coatings like titanium nitride, can provide additional protection against wear and extend service life.
- Use lubrication: Lubricating the cutting area with a suitable cutting fluid or lubricant can help reduce friction and heat, potentially extending the life of the router bit.