Multi-Head CNC Router
The multi-head CNC router is a versatile and efficient machine used in the manufacturing and woodworking industries. Unlike traditional CNC routers, this advanced equipment features multiple spindles that can be operated simultaneously, increasing productivity and accuracy.
The multi-head CNC router can perform various tasks simultaneously, thus increasing production speed without compromising accuracy. It can perform complex cuts, carvings, engravings, and shapes on different materials such as wood, plastics, and composites.
The multi-head CNC router provides flexibility by enabling different tooling configurations, allowing operators to perform complex designs in a single operation. Whether creating detailed patterns, fabricating furniture components, or prototyping, multi-head CNC routers deliver consistent and high-quality results. Its programmable nature enables automation and repeatability, reducing human error and material waste while optimizing production output. This makes it a valuable asset in industries where precision, efficiency, and versatility are crucial.
Tips For Choosing The Right Multi-Head CNC Router
Choosing the ideal multi-head CNC router is a key decision in optimizing manufacturing efficiency. Whether you’re researching synchronization, evaluating head configurations, or weighing precision and accuracy, our expert insights will help you make informed decisions.
Application requirements
Define the specific tasks that the CNC router will perform. Consider whether your application requires simultaneous or sequential processing of materials. Different materials (wood, metal, plastic, composites) may require specific spindle speeds, cutting tools, and accuracy levels, so make sure your machine’s specifications match your application needs.
Headcount
Analyze the complexity of the production process. Consider whether running multiple heads simultaneously or independently will optimize your workflow. Evaluate the balance between the number of heads and the tasks that need to be accomplished to ensure efficiency and avoid unnecessary complexity.
Head configuration
Explore the versatility of head configurations. Some CNC routers offer interchangeable heads for different tasks, allowing operational flexibility. Evaluate whether the heads can be controlled individually, enabling multiple operations on multiple parts of the workpiece simultaneously.
Workpiece size and worktable capacity
Evaluate the size of the CNC router’s work area and its table capacity. Make sure it fits the dimensions of typical workpieces and allows room for expansion. Consider the load-bearing capacity of your workbench to handle larger, heavier materials without compromising stability.
Precision and accuracy
Check the precision and accuracy specifications of the CNC router. Look for factors like rigid construction, high-quality linear guides, and advanced control systems to achieve consistent and precise machining. Evaluate machines for repeatability and tolerance levels across a variety of tasks to ensure precise results.
Software compatibility
Confirm CNC router compatibility with your preferred design and CAM software. Seamless integration ensures a smooth workflow from design to production. Evaluate the ease of data transfer and communication between software and machine control systems.
Dust removal and chip removal
Consider the efficiency of dust collection and chip removal systems. Well-designed systems help create a cleaner work environment, extend tool life, and reduce maintenance. Evaluate whether the machine has built-in capabilities for waste treatment or if it requires integration with other external systems.
Easy to use and program
Consider the intuitiveness of the user interface and control panel. The easy-to-use interface simplifies programming, toolpath generation, and job setup. Look for features like visual aids, step-by-step guides, and remote monitoring to enhance the user experience and reduce the learning curve.
Tool changing system
Evaluate the efficiency of the tool change system. Automatic tool changers can significantly reduce downtime associated with manual changes, thereby increasing overall productivity. Evaluate tool changer capacity, speed, and compatibility with different tool types to meet your production requirements.
Support and service
Research the manufacturer’s reputation for after-sales support. Make sure they provide comprehensive technical assistance, training, and readily available spare parts. Consider service technician accessibility and customer support responsiveness to minimize potential downtime.
Budget and ROI
Adjust your budget based on the CNC router’s features and capabilities. Evaluate potential return on investment based on increased productivity, reduced material waste, and operational efficiencies. When evaluating your overall budget and ROI, consider the long-term cost implications, including maintenance and potential upgrades.
Comments and suggestions
Seek feedback from industry peers, read reviews, and gather recommendations from users with similar app needs. Real-world experience provides valuable insights into the performance, reliability, and user satisfaction of different multi-head CNC routers.
What materials can a multi-head CNC router cut?
The multi-head CNC router is versatile and capable of cutting a wide range of materials. The specific materials depend on the machine’s design, spindle capabilities, and cutting tools. Generally, multi-head CNC routers can cut materials such as:
Wood
- Pine
- Oak
- Maple
- Plywood
- MDF
- Cedar
- Teak
Plastics
- Acrylic
- PVC
- HDPE
- LDPE
- Polycarbonate
- PET
- PU
Metal
- Stainless Steel
- Carbon Steel
- Carbon Steel
- Brass
- Copper
- Titanium
- Gold
Others
- Rubber
- Carbon Fiber
- Laminates
- Leather
- Glass
- Stone
- Ceramics
Application Industry
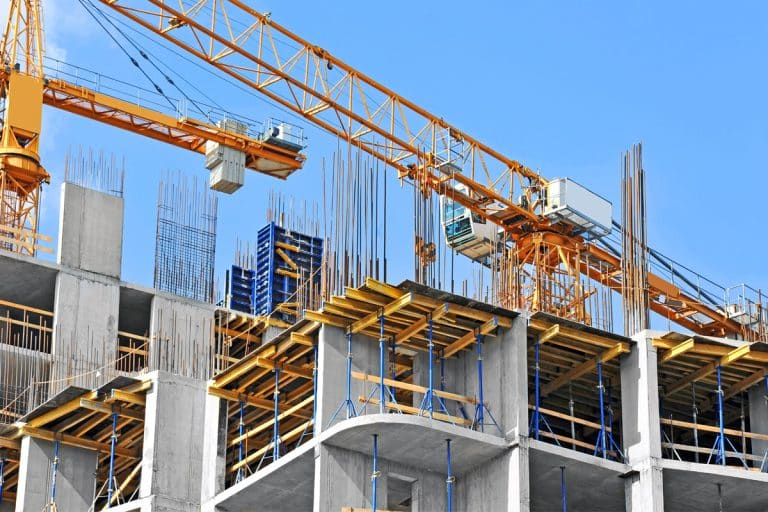
Construction Industry
The integration of CNC routers into construction workflows has ushered in a new era characterized by meticulous detailing, rapid prototyping, and improved material utilization.
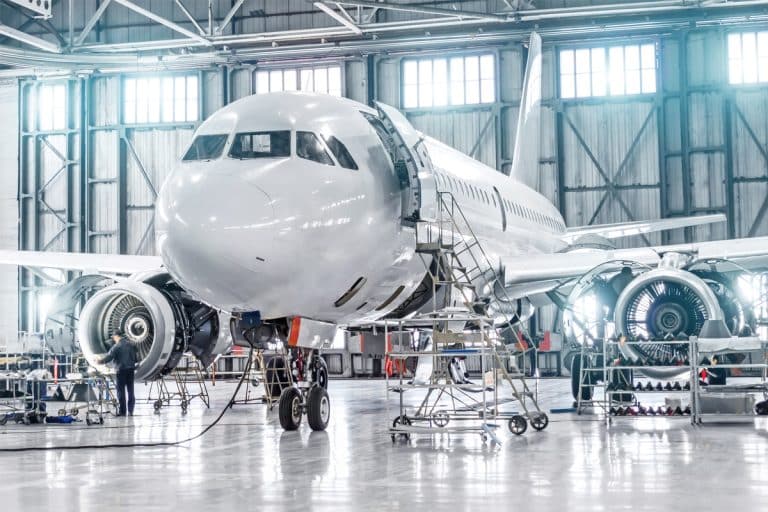
Aerospace Industry
The CNC router is widely used in aerospace engineering due to its unparalleled ability to carve complex designs, manufacture complex parts, and ensure tight tolerances.
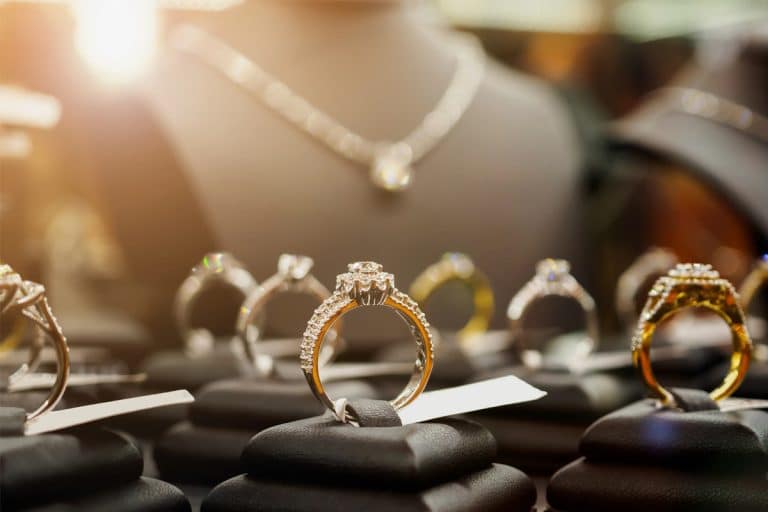
Jewelry Industry
The CNC router revolutionize the way fine jewelry is designed and made by delivering unparalleled precision and efficiency and producing intricate designs with meticulous attention to detail.
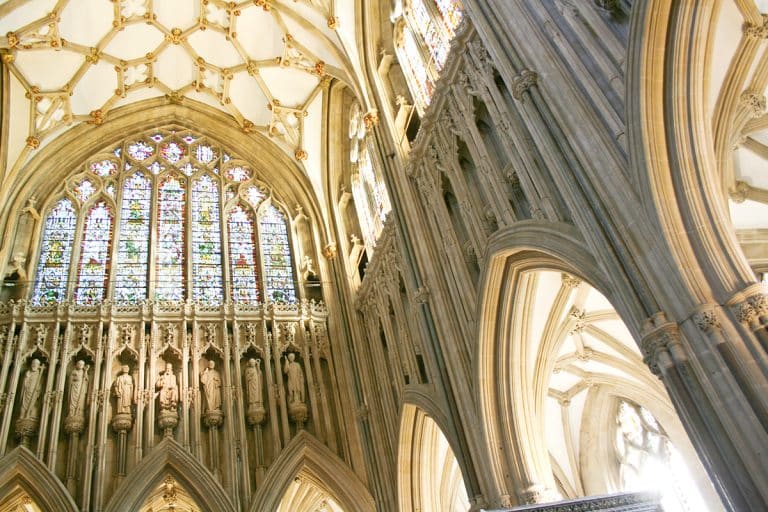
Stone Carving Industry
The integration of CNC routers into the stone carving industry is not only revolutionizing the way craftsmen carve, it is also redefining the boundaries of artistic possibilities in this ancient practice.
Blog
The Impact of Spindle Power on CNC Router Functionality
This article will delve into how spindle power affects the overall functionality of CNC routers, helping users make informed decisions based on their specific production needs.
Read More
How to Evaluate Energy Consumption and Operating Costs of CNC Router?
This article will guide you through the elements to consider when evaluating the energy consumption and operating costs of a CNC router, providing you with strategies to reduce operating costs.
Read More
How do I Choose The Right CNC Router Size and Capacity for a Specific Need?
In this article, we’ll walk you through the key considerations when determining the proper size and capacity of a CNC router, aiming to help you make an informed decision that ...
Read More
How to Choose the Perfect Woodworking CNC Router Bit
In this article, we’ll walk you through the essential factors to consider when choosing the perfect woodworking CNC router bit. We aim to help you choose the best router bit ...
Read More
Building Musical Instrument with CNC Router: A Comprehensive Guide
This article explores the role of CNC routers in musical instrument manufacturing, providing you with the basic knowledge and guidance you need to use a CNC router to manufacture musical ...
Read More
What Should I Know Before Buying a CNC Router?
This article discusses the things you need to know before buying a CNC router from multiple aspects, aiming to help you choose a machine that can improve your productivity and ...
Read More
Frequently Asked Questions
What can a multi-head CNC router do?
The multi-head CNC router is a versatile and powerful machining tool that can perform a variety of tasks in different industries. Here are some common features of multi-head CNC routers:
- Simultaneous Processing: One of its main features is the ability to operate multiple cutting heads simultaneously. This increases productivity by performing multiple tasks simultaneously.
- Versatile Cutting: It can cut a variety of materials, including wood, plastic, composites, foam, and more. This versatility makes it suitable for a variety of applications.
- Complex Carving And Engraving: With precise control, it can create intricate patterns, carving, and engraving on a variety of materials, making it ideal for woodworking, signage, and art applications.
- Routing And Forming: It can perform milling and forming operations, allowing the creation of complex three-dimensional shapes with high precision.
- High-Speed Routing: With its powerful spindle and advanced control system, it can achieve high-speed routing and improve overall production efficiency.
- Automation And Repeatability: It automates the production process, ensuring consistent and repeatable results for large-scale manufacturing.
- Production Optimization: Increase productivity by minimizing material waste, reducing manual labor, and ensuring consistent, high-quality output.
- Customization: Provides flexibility in customization by allowing a variety of tool configurations and the ability to switch between different heads or tools for different operations.
- Prototyping: Rapidly produce prototypes and models for different industries, facilitating design verification and testing.
- Material Finishing: Smoothing a surface, adding a decorative finish, or creating texture on a material to achieve a specific aesthetic or functional effect.
What are the types of multi-head CNC routers?
Multi-head CNC routers are available in a variety of configurations to meet different manufacturing requirements:
- Multi-Process (sequential) CNC Router
- Operation: This CNC router utilizes multiple spindles, but each spindle is dedicated to a specific machining step. The machine can switch between spindles for different operations in sequence.
- Advantages: Sequential processing optimizes precision and flexibility, allowing different tasks to be performed without affecting efficiency.
- Multi-Head (synchronous) CNC Router
- Operation: This CNC router has multiple spindles that can be operated simultaneously. Each head can perform independent operations on different parts of the workpiece simultaneously.
- Advantages: Simultaneous processing significantly increases production speed without sacrificing accuracy, allowing it to be efficiently manufactured in high volumes.
- Hybrid Multi-Function CNC Router
- Operation: The hybrid multi-function CNC router combines traditional CNC router functions with additional functions, such as a plasma cutting torch, vibrating knife, Drilling Unit, and other additional functions.
- Advantages: These machines offer versatility in one unit, expanding the range of tasks they can perform. They are versatile and suitable for a variety of applications within a single system.
What is the price of a multi-head CNC router?
Like other CNC routers, the price of a multi-head CNC router depends on the specific machine configuration. Different projects require different spindle power, working dimensions, control systems, etc., so the prices of multi-head CNC routers vary greatly. Many factors will affect the sales price of multi-axis CNC routers. The most important thing is the configuration of the machine. For example, workbench type and area, spindle type and power, motor type and power, etc. The higher the configuration, the higher the price.
Under normal circumstances, the price of a multi-head CNC router averages between US$5,000 and US$20,000. It’s important to note that these price ranges are approximate and actual costs may vary based on specific requirements, customization options, and the manufacturer’s pricing strategy. In addition, costs may increase as features such as automatic tool changers, advanced control systems, precision enhancements, and specialized configurations are added. Please contact our sales staff for specific prices, they will quote based on the machine specifications you need.
Why choose a multi-head CNC router?
Choosing a multi-head CNC router offers multiple advantages to manufacturers in various industries. Here are compelling reasons to choose a multi-head CNC router:
- Increased Productivity: The multi-head CNC router allows simultaneous processing or sequential operations, significantly increasing production speed without compromising accuracy. This feature optimizes workflow efficiency and output.
- Versatility And Flexibility: These machines can accommodate a variety of operations on a variety of materials, from cutting and engraving to drilling and forming. The ability to handle a variety of tasks in a single setup enhances manufacturing versatility.
- Reduce Production Costs: By optimizing production time and minimizing manual intervention, multi-head CNC router helps save costs. It increases productivity, reduces labor expenses, and reduces material waste through efficient processes.
- Precision And Consistency: This CNC router provides high precision and consistency during machining. Whether performing sequential or simultaneous operations, the precision of each head ensures consistent results across the entire workpiece.
- Parallel Processing: Multiple heads operate simultaneously to achieve parallel processing. This is especially beneficial for large-scale production runs, as multiple identical or similar parts can be produced simultaneously.
- Adaptability To Various Materials: The multi-head CNC router can process a variety of materials, including wood, plastics, and composite materials. This adaptability makes them suitable for industries with different material requirements.
- Optimized Workflow: The multi-head CNC router can perform multiple operations in one setup, simplifying production workflow. This smoothes the process, reduces bottlenecks, and increases overall throughput.
- Simplified Prototyping: For industries involving prototyping, it speeds up the iterative design process. Synchronized operations and rapid production capabilities help quickly produce and test prototypes.
- Competitive Advantages: Investing in advanced processing technologies such as multi-head CNC routers can provide faster turnaround times, higher precision, and stronger production capabilities than traditional single-head CNC routers, thus providing competitive advantages.
- Scalability And Customization: This CNC router offers customizable configurations, allowing users to adapt the machine to changing production needs. This scalability supports enterprise growth and business diversification.
How to maintain the multi-head CNC router?
Proper maintenance helps ensure the longevity, accuracy, and efficiency of your multi-head CNC router. The following are basic tips for maintaining a multi-head CNC router:
- Regular Cleaning: Clean the machine regularly to remove dust, debris, and residue. Use compressed air, brushes, or a vacuum system to clean the work area, spindle, guide rails, and ball screws.
- Lubrication: Follow the manufacturer’s lubrication schedule guidelines. Apply appropriate lubricants to the machine’s moving parts, such as rails, bearings, and ball screws, to reduce friction and wear.
- Monitor The Cooling System: Check coolant levels and make sure the cooling system is operating properly, especially on machines with high-speed spindles. Clean or replace filters to prevent overheating and maintain spindle performance.
- Collet And Tool Holder Maintenance: Inspect and clean the chuck and tool holder and replace them if worn. Proper tool holder maintenance facilitates precise machining.
- Check Runout: Regularly check and measure spindle runout to ensure concentricity. Promptly correct any problems to maintain the accuracy of machining operations.
- Check Alignment And Calibration: Periodically check and recalibrate the machine to ensure accurate positioning and alignment. Verify spindle alignment, axis squareness, and overall machine geometry.
- Electrical Component Inspection: Check electrical connections, cables, and wiring regularly. Tighten loose connections and replace damaged cables to prevent electrical problems that may affect machine performance.
- Dust Removal System: If equipped with a dust removal system, clean or replace the filter regularly to ensure effective removal of chips and dust. Clean systems promote a healthier work environment.
- Software Updates And Backups: Keep your machine’s control software up to date with the latest version from the manufacturer. Regularly back up important machine settings and programs.
- Operator Training And Education: Operators are trained in proper machine operation, maintenance procedures, and safety protocols. Well-trained operators can help prevent problems and perform routine maintenance efficiently.
- Axis Movement Inspection: Check the movement of each axis regularly. Verify that movement is smooth and resolve any abnormalities promptly to prevent mechanical problems.
- Safety Measures: Ensure safety features such as emergency stops, interlocks, and guards are in place and functioning properly. Test these security measures regularly to ensure they are working as expected.
- Tool Inspection And Replacement: Regularly monitor tool wear and replace cutting tools as needed. Worn knives affect cut quality and increase the load on the machine.
- Coolant And Lubricant Levels: Check coolant and lubricant levels regularly. Make sure they are at recommended levels for optimal performance and service life of your machine components.
- Operator Training: Ensure operators are adequately trained in machine operation and maintenance procedures. Well-trained operators facilitate proper maintenance and efficient use of CNC routers.
- Professional Repairs: When necessary, hire professional technicians to perform in-depth inspections or repairs beyond routine maintenance tasks.
What are the differences between an ordinary CNC router and a multi-head CNC router?
The main difference between a regular CNC router and a multi-head CNC router is their configuration, functionality, and the types of tasks they can perform. Here’s a breakdown of these differences:
- Number of Heads/Axes
- Ordinary CNC router: Usually equipped with a single spindle, which is limited to performing one operation on the workpiece at a time.
- Multi-head CNC router: has multiple spindles, allowing simultaneous or sequential operations on the same or multiple workpieces.
- Processing Capacity
- Ordinary CNC router: performs one task at a time, requiring multiple settings or tool changes for different operations.
- Multi-head CNC router: Supports concurrent processing or sequential operations, reducing production time by performing various tasks simultaneously or switching between different operating heads without manual intervention.
- Versatility And Flexibility
- Ordinary CNC router: has limited ability to handle multiple operations at the same time, and usually requires multiple settings for different tasks.
- Multi-head CNC router: Provides greater versatility because each head can be dedicated to a specific task or material, reducing the need for frequent tool changes.
- Efficiency And Speed
- Regular CNC router: Processes tasks sequentially, which can extend production time for complex projects.
- Multi-head CNC router: Provides greater efficiency and speed through parallel processing, significantly reducing the time required to complete multiple tasks.
- Complexity And Precision
- Ordinary CNC router: suitable for simpler operations, which may require additional settings to complete complex or multi-step processes.
- Multi-head CNC router: Able to handle complex tasks and designs with precision thanks to the ability to perform multiple operations in a single setup.
- Cost And Space Requirements
- Regular CNC router: Typically more cost-effective and requires less space due to the single spindle.
- Multi-head CNC router: This may involve a higher initial investment cost, but can increase productivity and efficiency, potentially offsetting the investment through increased output.
- Material Handling:
- Ordinary CNC router: suitable for a variety of materials, but may require more tool changes for different materials.
- Multi-head CNC router: It can efficiently process various materials simultaneously or sequentially, providing flexibility in material processing.
What are the differences between an ATC CNC router and a multi-head CNC router?
The main differences between automatic tool changer (ATC) CNC routers and multi-head CNC routers are their tool-changing mechanisms, machining capabilities, and versatility:
- Tool Changing Mechanism
- ATC CNC router: Equipped with an automatic tool changer that can quickly and automatically change between different cutting tools or drill bits. It typically houses multiple tools in a turntable or rack, allowing tools to be quickly changed during operation without manual intervention.
- Multi-head CNC router: Having multiple spindles or routing heads operating simultaneously or sequentially. Tool changing involves moving between different spindles rather than changing tools on a single spindle during operation.
- Number of Heads/Spindle
- ATC CNC router: uses a single spindle, but can automatically switch between various tools stored in the tool magazine.
- Multi-head CNC router: Contains multiple spindles, each dedicated to a specific task or able to operate simultaneously to increase productivity.
- Processing Capacity
- ATC CNC router: Optimized for handling a variety of tools within a single spindle, allowing it to perform different operations without the need to manually change tools.
- Multi-head CNC router: Uses multiple spindles to achieve simultaneous or sequential machining, allowing various operations to be performed in parallel on the workpiece.
- Efficiency And Speed
- ATC CNC router: Increase efficiency by reducing downtime associated with manual tool changes. Tools can be preloaded in the tool magazine, and the CNC router can automatically select and replace tools as needed.
- Multi-head CNC router: Increase efficiency by using multiple spindles to perform operations simultaneously or switch between heads for different operations without having to manually change tools.
- Versatility And Flexibility
- ATC CNC router: Provides versatility by allowing a variety of tools to be used within a single spindle, expanding the range of tasks it can perform without stopping the machining process.
- Multi-head CNC router: Provides versatility by allowing simultaneous or sequential machining with different spindles (each spindle dedicated to a specific operation).
- Tool Capacity
- ATC CNC router: The tool magazine can usually accommodate multiple tools, and the CNC router can automatically select tools from the tool magazine during operation.
- Multi-head CNC router: The number of tools is determined by the number of spindles. Each spindle has its dedicated tool, and the machine can switch between spindles to perform different operations.
- Complexity And Precision
- ATC CNC router: Ideal for a variety of operations, but complex or multi-step processes may require additional tool changes.
- Multi-head CNC router: Using multiple spindles to perform different operations simultaneously or sequentially, complex tasks can be handled accurately.
- Cost And Space Requirements
- ATC CNC router: Usually the initial investment is higher due to the automatic tool-changing mechanism. Additional magazine space is required.
- Multi-head CNC router: This may have a lower initial investment compared to an ATC CNC mill, but still requires space for multiple spindles.
What are the causes of multi-head CNC spindle vibration?
Spindle vibration in a multi-head CNC router can be caused by a variety of factors. Identifying and resolving the root cause helps maintain accuracy and ensure the longevity of your machine. Here are some common causes of spindle vibration:
- Unbalanced Tools
- Reason: Uneven mass distribution in the cutting tool or tool holder can cause imbalance.
- Solution: Balance and properly install cutting tools. Regularly inspect and replace worn or damaged tools.
- Tools Worn or Damaged
- Reason: Worn or damaged cutting tools can cause uneven cutting forces, resulting in vibration.
- Solution: Regularly inspect and replace worn or damaged cutting tools. Ensure correct tool selection and quality.
- Worn Bearings
- Cause: Over time, spindle bearings wear, causing increased play and vibration.
- Solution: Monitor bearing condition and replace as needed. Regular spindle maintenance includes lubrication and bearing inspections.
- Tool Runout
- Cause: When rotating, the tool axis deviates from the true centerline, causing beat and vibration.
- Solution: Check the tool runout regularly. Tools with excessive runout should be replaced or reground. Ensure proper tool holder and chuck maintenance.
- Loose Fasteners
- Cause: Loose bolts, nuts, or other fasteners in the spindle assembly can cause instability.
- Solution: Regularly inspect and tighten all fasteners in the spindle assembly and tool holder to eliminate any play.
- Cutting Force is Too Large
- Reason: Trying to remove too much material in one pass or using incorrect cutting strategies can result in excessive cutting forces and vibration.
- Solution: Optimize cutting parameters, tool paths, and depth of cut to reduce cutting forces. Consider removing heavy material in multiple passes.
- Material Properties
- Reason: Machining certain materials with poor damping properties may result in increased vibration.
- Solution: Adjust cutting parameters and strategies for vibration-prone materials. Consider using a vibration-damped tool holder.
- Insufficient Cooling
- Reason: Insufficient cooling of the spindle will cause thermal expansion and affect spindle performance.
- Solution: Ensure good cooling and ventilation of the spindle. Monitor and maintain cooling systems regularly.