5-Axis CNC Router
The 5-axis CNC router is a precision machining tool used for precision cutting, engraving, and shaping of materials in 3D space. Unlike traditional 3-axis CNC routers that move along the X, Y, and Z axes, a 5-axis CNC router adds two additional axes of rotation to enable more complex machining operations. This versatility allows the machine to approach the workpiece from multiple angles, reducing the need for repositioning and increasing overall efficiency.
This multi-directional motion capability allows the CNC router to approach the workpiece from different angles and directions, allowing complex shapes to be created accurately and efficiently. The additional axis of rotation allows the tool to reach areas that a 3-axis CNC router may not be able to reach, reducing the need for repositioning and improving overall accuracy.
Manufacturers often use 5-axis CNC routers for tasks that require intricate detailing, engraving, and contouring on materials such as wood, plastic, composites, and metal. The versatility and precision of the 5-axis CNC router make it a valuable asset for industries that require complex designs and complex shapes.
Tips for choosing the right 5-axis CNC router
Start your journey to choose a 5-axis CNC router. Navigating the world of advanced processing requires careful consideration. From application details to control system nuances, we provide insights that will empower you to make informed choices and advance your precision machining efforts. Whether you are a seasoned professional or new to CNC technology, join us to learn the key considerations for finding your perfect fit in the world of 5-axis CNC routers.
Application details
When choosing a 5-axis CNC router, consider your specific machining application. Different materials may require different spindle speeds, cutting tools, and machine structure stiffness. For example, machining metal may require greater rigidity and power compared to woodworking applications. Choose a CNC router that suits the material and complexity of your project.
Accuracy and precision
Look for accuracy specifications in terms of repeatability and resolution. High-resolution encoders, rigid machine structures, and high-quality linear guides contribute to increased accuracy. Evaluate the machine’s ability to maintain accuracy over extended periods of use and consider thermal expansion compensation features that may affect accuracy.
Machine dimensions and working area
Evaluate the dimensions of the machine relative to your workspace and the dimensions of the parts you intend to produce. Make sure the machine’s travel distance and working envelope can accommodate the largest expected workpiece, taking into account the machine’s footprint in your facility.
Spindle power and speed
Check the spindle power and speed capabilities of the CNC router. The spindle is a key component that affects cutting efficiency. Choose a machine with a spindle that is powerful enough to run at a speed suitable for your application, balancing the demands of high-speed cutting with the requirements for precision.
Tool changer and compatibility
Investigate tool-changing systems. Look for an automatic tool changer with enough capacity to meet your project needs. Consider the speed of tool changes as this affects overall productivity. Make sure it is compatible with the type and size of the tool you plan to use for your application.
Control system and software
Check control system and software compatibility. Check if the CNC router is compatible with the CAM software you plan to use for programming. Assessing user interface ease of use and programmability, user-friendly control systems can reduce operator learning curves and increase efficiency.
Easy to use and program
Evaluate the overall user experience from machine setup to daily operations. The CNC router simplifies production with its intuitive interface and simple programming capabilities. Look for features like tool path simulation and verification to catch errors before machining.
Support and service
Research the manufacturer’s reputation for customer support and service. Consider the availability of technical assistance, training programs, and response times. A reliable support system helps minimize downtime and resolve issues promptly.
price and value
While cost is a factor, consider the overall value and not just the initial price. Evaluate the features, functionality, and long-term benefits the machine provides. The higher initial investment may be justified by increased productivity, accuracy, and reliability.
Comments and suggestions
Seek user reviews and advice from professionals in your industry. Real-world experience can provide valuable insights into the performance, reliability, and user satisfaction of the CNC router model you are considering.
Options and upgrades
Evaluate the availability of options and upgrades. As your business grows, modular machines that allow for future expansion or enhancement can be a cost-effective option. Consider whether the CNC router can adapt to changing production requirements.
Warranty and maintenance
Check warranty terms and conditions. A comprehensive warranty reflects the manufacturer’s confidence in their product. Additionally, consider ease of maintenance and availability of replacement parts to minimize downtime and ensure smooth operation.
What materials can the 5-axis CNC router cut?
The 5-axis CNC router is a versatile machining tool capable of cutting a variety of materials with precision and complexity. The materials that the 5-axis CNC router can cut include:
Wood
- Pine
- Oak
- Maple
- Plywood
- MDF
- Cedar
- Teak
Plastics
- Acrylic
- PVC
- HDPE
- LDPE
- Polycarbonate
- PET
- PU
Metal
- Stainless Steel
- Carbon Steel
- Aluminum
- Brass
- Copper
- Titanium
- Gold
Others
- Rubber
- Carbon Fiber
- Laminates
- Leather
- Glass
- Stone
- Ceramics
Application Industry
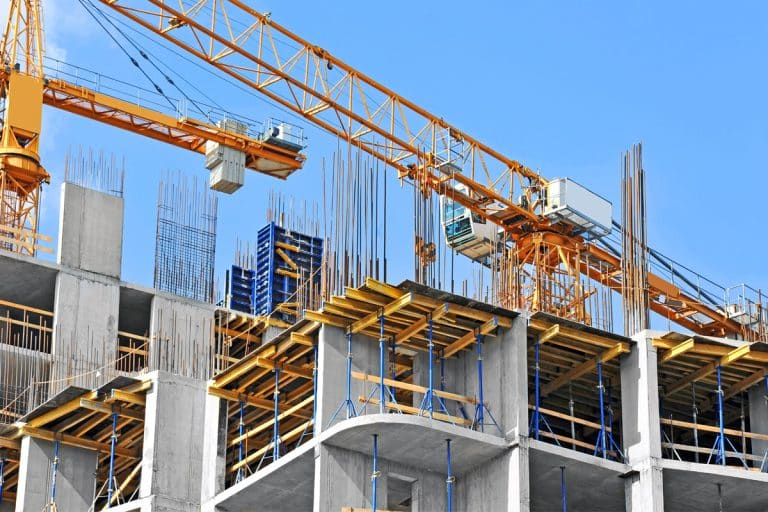
Construction Industry
The integration of CNC routers into construction workflows has ushered in a new era characterized by meticulous detailing, rapid prototyping, and improved material utilization.
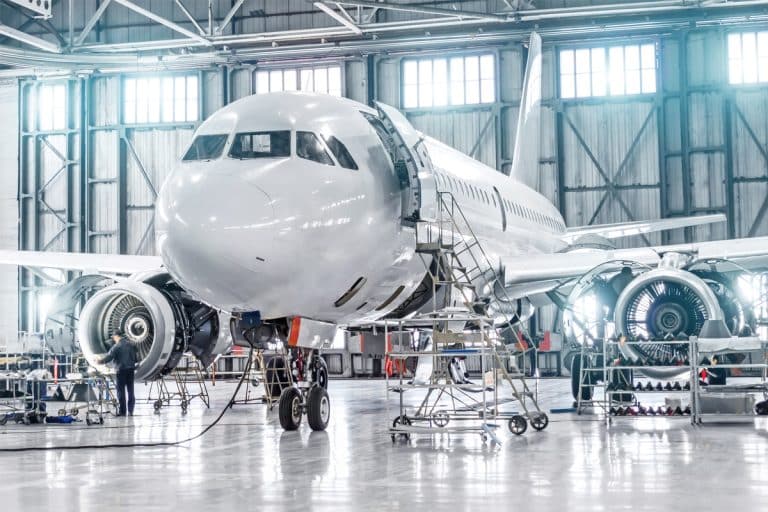
Aerospace Industry
The CNC router is widely used in aerospace engineering due to its unparalleled ability to carve complex designs, manufacture complex parts, and ensure tight tolerances.
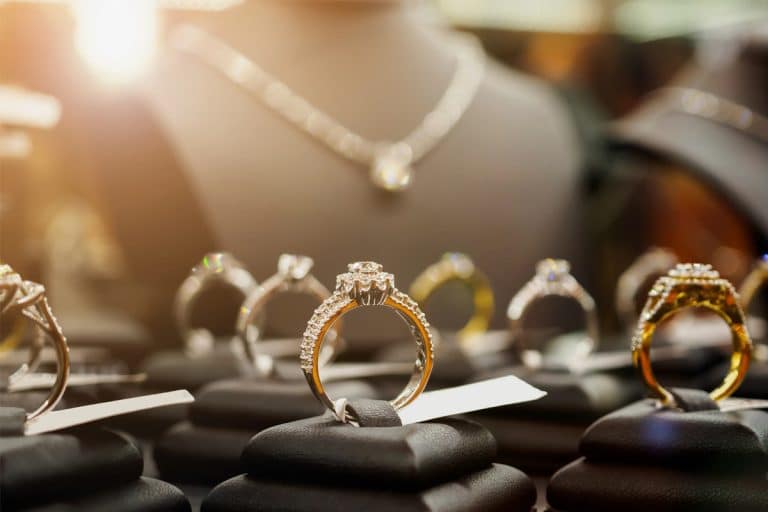
Jewelry Industry
The CNC router revolutionize the way fine jewelry is designed and made by delivering unparalleled precision and efficiency and producing intricate designs with meticulous attention to detail.
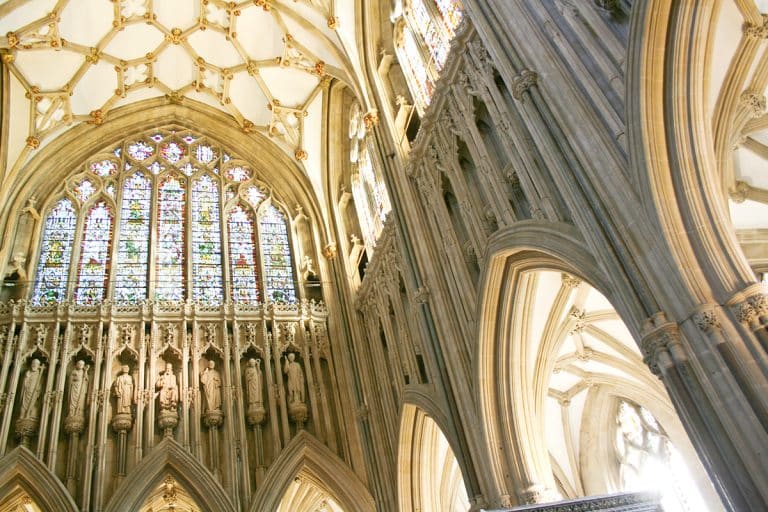
Stone Carving Industry
The integration of CNC routers into the stone carving industry is not only revolutionizing the way craftsmen carve, it is also redefining the boundaries of artistic possibilities in this ancient practice.
Blog
How to Reduce the Impact of Workpiece Adhesion on CNC Router Cutting Quality
This article delves into practical strategies for mitigating the impact of workpiece adhesion on CNC router cutting quality, to improve the performance and reliability of CNC router operations.
Read More
Addressing Environmental Concerns in CNC Router Waste Disposal: A Comprehensive Guide
In this article, we delve into the considerations for the correct disposal of waste materials from CNC router operations, aiming to tackle the environmental challenges posed by CNC waste.
Read More
Guide to Optimizing CNC Router Parameters for Diverse Materials
This article provides a systematic parameter optimization method for CNC routers cutting different materials, aiming to provide users with the necessary knowledge to achieve excellent processing quality.
Read More
Understanding the Perils of Spindle Runout in CNC Routers
This article delves into the causes of spindle runout and strategies for mitigating its effects, aiming to provide you with the knowledge to optimize CNC router performance.
Read More
Mastering CNC Router Worktables: A Comprehensive Guide
This article delves into the CNC router types, operating methods, maintenance, and customization options, providing you with the knowledge to optimize your CNC router settings for superior results.
Read More
CNC Router Bits: Complete Buyer’s Guide
From understanding the different types of CNC router bits to deciphering the nuances of materials and coatings, this guide provides the essential reference for finding the right bit for your ...
Read More
Frequently Asked Questions
What is a 5-axis CNC Router?
The 5-axis CNC (Computer Numerical Control) router is a sophisticated machining tool that operates in 3D spaces, capable of moving a cutting tool along five different axes. Unlike traditional 3-axis CNC routers that move along the X, Y, and Z axes, a 5-axis CNC router adds two more rotational axes to the system. These additional axes enable the cutting tool to approach the workpiece from different angles and orientations.
The five axes in a 5-axis CNC router are typically defined as follows:
- X-Axis: Horizontal movement from left to right.
- Y-Axis: Horizontal movement from front to back.
- Z-Axis: Vertical movement up and down.
- A-Axis: Rotation around the X-axis.
- B-Axis: Rotation around the Y-axis.
How does the 5-axis CNC Router work?
A 5-axis CNC router operates by using computer-controlled movements across five axes to precisely cut, carve, or shape materials in three-dimensional space. Here’s a breakdown of how it works:
- Tool Setup: The desired cutting tool (such as an end mill or router bit) is mounted on the machine’s spindle.
- Computer-Aided Design (CAD): A digital 3D model of the object to be machined is created using CAD software.
- CAM Programming: The CAD model is translated into tool paths and instructions for the CNC machine using CAM (Computer-Aided Manufacturing) software. This generates the code that controls the machine’s movements.
- Workpiece Fixturing: The material or workpiece is securely fixed onto the CNC router’s worktable or bed using clamps, vacuum systems, or other fixturing methods.
- Machine Setup: The CNC operator loads the CNC program into the machine’s control unit and sets the machining parameters such as cutting speeds, toolpaths, and tool changes.
- Multi-Axis Machining: During operation, the CNC router moves the cutting tool along the X, Y, and Z axes while simultaneously employing the A and B axes for rotation and tilting of either the tool or the workpiece.
- A-Axis: Rotates the tool or workpiece from side to side, allowing it to tilt at an angle relative to the work surface.
- B-Axis: Rotates the tool or workpiece around its horizontal axis, enabling additional rotational movement.
- Material Removal: The cutting tool removes material based on the programmed tool paths, following precise instructions from the CNC program.
- Sequential Operations: The CNC router executes a sequence of movements and tool changes as specified in the program, repeating the process until the desired shape or object is fully machined.
- Finishing And Quality Control: Once machining is complete, the finished part undergoes inspection to ensure it meets the required specifications for accuracy, surface finish, and dimensional tolerance.
How much does a 5-axis CNC router cost?
The cost of a 5-axis CNC router can vary greatly depending on factors such as brand, size, specifications, and features. A basic 5-axis CNC router may start between $60,000 and $100,000. However, more advanced, larger machines with additional features or specialized capabilities can cost hundreds of thousands of dollars or more.
Several factors will affect the cost:
- Size And Work Scope: Larger machines designed to process larger workpieces generally cost more.
- Accuracy And Precision: Machines with higher accuracy and tighter tolerances generally cost more.
- Spindle Power And Speed: Machines with more powerful spindles and higher speed capabilities may be more expensive.
- Tool Change System: CNC milling machines equipped with automatic tool changers enable efficient multi-tool operations, thereby increasing costs.
- Brands And Manufacturers: Well-known and reputable brands are likely to have higher prices due to their track record, build quality, and customer support.
- Extras: Professional features, such as enhanced dust collection systems, advanced control interfaces, and customization, may increase the overall cost.
- Industry And Application: Machines designed for specific industries (such as aerospace or automotive) may have special features tailored to those applications, affecting price.
What are the pros and cons of a 5-axis CNC router?
Advantages of 5-Axis CNC Router
- Enhanced Versatility: The ability to move in five axes allows complex shapes and angles to be machined in a single setup, reducing the need for repositioning and increasing accuracy.
- Reduce Setup Time: With multi-axis motion, the 5-axis CNC router can approach the workpiece from different angles, reducing the need for repositioning and setup changes.
- High Precision: Additional axes allow the machine to reach inaccessible areas, allowing machined parts to be machined with greater precision and finer detail.
- Improved Surface Finish: Multi-axis motion enables smoother tool paths, reducing tool marks and improving the overall surface finish of machined parts.
- Increased Efficiency: Completing complex cuts and contours in one operation increases overall efficiency and reduces production time.
- Extended Tool Life: By maintaining a consistent tool angle relative to the workpiece, 5-axis machining reduces wear and extends the life of cutting tools.
- Easier Reach And Reach: Additional axes allow the tool to reach areas that traditional 3-axis CNC routers cannot, allowing for more complex designs.
- Complex Programming: Operating a 5-axis CNC router may require more advanced programming skills than a simple machine, which may increase the operator’s learning curve.
- Higher Initial Cost: A 5-axis CNC router typically has a higher upfront cost compared to a 3-axis CNC router, making it a significant investment.
- Maintenance And Calibration: With more moving parts and axes, maintenance and calibration can become more complex and may require specialized expertise.
- Space Requirements: Larger machines may require more space in the workshop or factory, affecting the layout and available work area.
- Steep Learning Curve: Operating a 5-axis CNC router requires a higher level of skill and understanding of the machine’s capabilities, which can result in a steeper learning curve for the operator.
- Tool Interference: In certain configurations, especially when machining complex parts, there is a risk of tool interference, where tools, fixtures, or machine parts can collide.
- Toolpath Complexity: Generating tool paths for 5-axis machining can be more complex, requiring advanced CAM software and experienced programmers.
How is a 5-axis CNC router operation?
Operating a 5-axis CNC router involves multiple steps, from designing the part in CAD (computer-aided design) to setting up the machine, running the CNC program, and inspecting the finished part. Here is an overview of a typical process:
- Design The Part: Use CAD software to create a 3D model of the part. Specify dimensions, features, and tolerances.
- CAM Programming: Use CAM (Computer Aided Manufacturing) software to generate tool paths from CAD models. Specify cutting tools, speeds, feeds, and other machining parameters.
- Machine Setup: Use clamps, vacuum systems, or other fixing methods to securely secure the material or workpiece to the CNC router.
- Tool Loading: Mount the appropriate cutting tool on the CNC router’s spindle. The choice of tool depends on the material and type of cutting required.
- Load CNC Program: Load the generated CNC program (G code) into the control unit of the CNC router. The program contains instructions for tool movement, speed, and other parameters.
- Tool Calibration: Calibrate tools and check tool length offset to ensure accurate machining. This step ensures that the machine knows the exact length of each tool.
- Work Coordinate Setup: Establish work coordinates by indicating the position of the material relative to the machine axes. This step helps align the CNC program with the actual workpiece.
- Run A Homing Cycle: Perform a homing cycle to establish the machine’s reference position. This ensures that the machine knows its starting point before executing the CNC program.
- Dry Run: Before actual machining, a dry run is performed to simulate the movement of the tool without cutting. This helps identify any potential problems and ensures the program is error-free.
- Start Processing: Start the CNC program and the machine starts executing the tool path. The 5-axis CNC router simultaneously moves the cutting tool along the X, Y, and Z axes, while using the A and B axes for rotation and tilt.
- Monitoring: Monitor whether there are any abnormalities during the processing. Some operators use software capabilities to simulate tool paths in real-time.
- Tool Change (If Necessary): If the CNC program requires multiple tools, the CNC router will automatically perform tool change according to the program instructions.
- Quality Check: After processing is complete, the finished parts are checked for accuracy, surface finish, and any other quality parameters.
- Unload Parts: Remove finished parts from the CNC router and, if necessary, prepare the machine for the next job.
How to maintain a 5-axis CNC router?
Maintaining a 5-axis CNC router is crucial for ensuring optimal performance, accuracy, and longevity. Here are key maintenance steps to follow:
Daily Maintenance
- Cleaning: Regularly clean the worktable, tool holders, and surrounding areas to remove chips, dust, and debris. Use air blowers, brushes, or vacuum systems. Clean and lubricate guide rails and ball screws to prevent buildup and ensure smooth movement.
- Check Coolant Levels: Ensure an adequate supply of coolant for cooling and lubricating the cutting tool during machining. Check coolant levels and top up if necessary.
- Inspect Toolholders: Examine tool holders for any signs of wear, damage, or contamination. Replace or clean them as needed.
- Verify Axis Movement: Manually jog each axis to confirm smooth and unrestricted movement. Check for any unusual noises or resistance.
- Lubrication: Regularly lubricate the machine’s moving parts according to the manufacturer’s recommendations. Pay attention to bearings, ball screws, and other critical components.
- Tool Inspection: Inspect cutting tools for wear, chipping, or damage. Replace worn or damaged tools promptly to maintain machining accuracy.
- Check Air Pressure: Ensure that the air pressure for the pneumatic systems is within the recommended range. Check for leaks and address any issues.
- Inspect Spindle: Check the spindle for any unusual noise, vibrations, or runout. Perform any required maintenance or, if necessary, consult with the manufacturer for professional servicing.
- Calibration: Perform routine calibration checks to ensure accurate tool positioning. Verify the accuracy of the A and B axes by measuring their movements against the programmed values.
- Review and Update Software: Keep CNC control software and firmware up to date. Check for updates or patches provided by the manufacturer and apply them as needed.
- Bearing and Ball Screw Inspection: Inspect and, if necessary, replace bearings and ball screws. Regular maintenance of these components is essential for long-term precision.
- Backup Parameters and Programs: Regularly back up machine parameters, tool libraries, and CNC programs. This ensures that important data can be restored in case of a machine malfunction or data loss.
- Professional Inspection: Schedule an annual professional inspection by a qualified technician. This may involve more in-depth checks, alignments, and adjustments that require specialized knowledge and tools.
- Replace Wear Parts: Replace any parts that have reached the end of their service life, including belts, seals, and other worn components.