Mini CNC Router
The mini CNC router is a compact, versatile computer numerical control (CNC) machine designed for precision cutting, engraving, and carving on a smaller scale. Despite its small size, it offers impressive features for business enthusiasts, DIY enthusiasts, and small manufacturing.
Equipped with stepper motors, lead screws, and controllers, the mini CNC router follows precise instructions from computer-aided design (CAD) software to create complex designs with high precision. The user-friendly interface allows for easy programming and control, making it suitable for individuals with varying CNC experience levels. Its compact footprint and portability make it suitable for limited workspace environments. Ideal for creating complex prototypes, personalized crafts, and small-scale production, the mini CNC router provides an affordable and efficient solution for those looking to delve deeper into small-scale CNC machining.
Tips for choosing the right mini CNC router
Were you embarking on the journey of selecting a mini CNC router for your projects? Whether you’re a hobbyist, DIY enthusiast, or small-scale manufacturer, we provide valuable insights on key considerations, from materials compatibility to ease of use. Navigate the intricacies of precision and power, explore software compatibility, and uncover the best practices for a seamless CNC experience. Let us help you make an informed decision as you step into the world of mini CNC routers.
Purpose and application
Define the main purpose of the mini CNC router. Decide whether you want to specialize in woodworking, plasticworking, metal carving, or a combination. Consider your intended application, such as prototyping, hobby projects, or small-scale production. Choose a CNC router that meets your specific needs.
Material compatibility
Determine the materials you plan to use, including wood, plastic, or soft metal. Make sure the mini CNC router has the capabilities and tooling options to handle the material of your choice. If you plan to use multiple materials on a single project, check out features like tool-changing capabilities.
Dimensions and workspace
Measure the available space on the shop floor or designated area. Consider the mini CNC router’s footprint to ensure a comfortable fit while enabling efficient material handling. Assess the work area (X, Y, and Z dimensions) to ensure it is appropriate for the project size you intend to undertake.
Accuracy and precision
Check the precision parts of the CNC router, such as stepper motors and linear guides. Higher-resolution components help improve cutting and engraving accuracy. Look for features like ball screws or rack-and-pinion systems that increase the precision of your movements.
Spindle power and speed
Evaluate the spindle power relative to the material you want to cut. Higher power is available for tougher materials, while variable speed options provide versatility. Consider features like a tool cooling system to maintain optimal spindle performance over extended periods of use.
Controllers and software
Check the mini CNC router’s compatibility with your preferred design and toolpath generation software. Ensure seamless communication between your design software and the CNC controller. Evaluate the controller’s user interface and usability of features such as homing and tool detection for efficient setup.
Easy to use
Look for a mini CNC router with an intuitive user interface and controls. Features such as a touchscreen display, a simplified calibration process, and easy tool changes contribute to user-friendly operation. Consider whether there are tutorials, manuals, and online resources for learning and troubleshooting.
Upgradeability
Check if the mini CNC router allows future upgrades. As your skills and project requirements grow, being able to upgrade components such as spindles, controllers, or additional features can expand the capabilities of your machine without requiring a complete replacement.
Build quality and durability
Check the CNC router’s construction materials and build quality. A sturdy frame, quality components, and durable construction help increase operational stability and ensure the machine’s longevity. Check features such as dust collection systems to protect machine components and extend service life.
Support and community
Research the manufacturer’s reputation for customer support. Find ready documentation, online resources, and responsive customer service. Joining a forum or community related to a specific CNC router can provide valuable insights, troubleshooting tips, and user experience.
Budget considerations
Define your budget and compare features within that range. Consider the critical features of your project and prioritize them over unnecessary bells and whistles. Balance cost with the features you need to ensure the CNC router you choose provides the best value for your investment.
Comments and suggestions
Explore customer reviews to learn more about mini CNC router performance. Seek recommendations from users with similar needs. Pay attention to both positive and negative reviews so you can make an informed decision based on the experiences of others.
What materials can a mini CNC router cut?
The mini CNC router is versatile and capable of cutting a variety of materials. The specific materials it can handle may vary depending on the machine’s specifications and capabilities. Generally, a mini CNC router can cut materials such as:
Wood
- Pine
- Oak
- Maple
- Plywood
- MDF
- Cedar
- Teak
Plastics
- Acrylic
- PVC
- HDPE
- LDPE
- Polycarbonate
- PET
- PU
Metal
- Stainless Steel
- Carbon Steel
- Aluminum
- Brass
- Copper
- Titanium
- Gold
Others
- Rubber
- Carbon Fiber
- Laminates
- Leather
- Glass
- Stone
- Ceramics
Application Industry
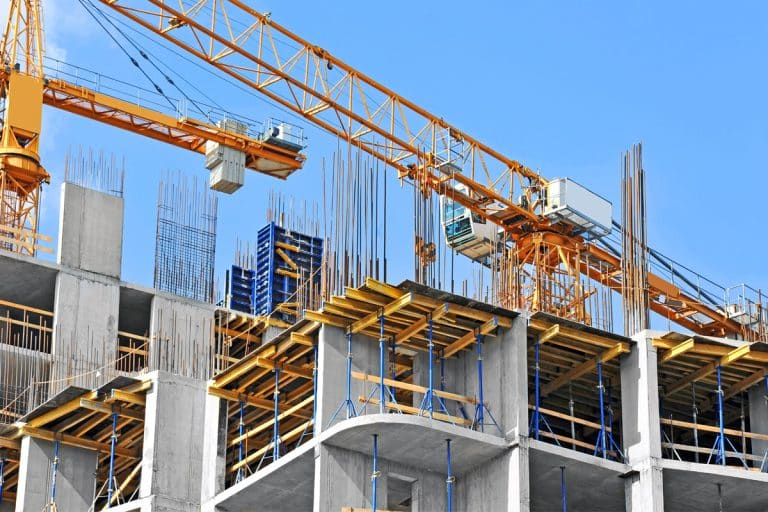
Construction Industry
The integration of CNC routers into construction workflows has ushered in a new era characterized by meticulous detailing, rapid prototyping, and improved material utilization.
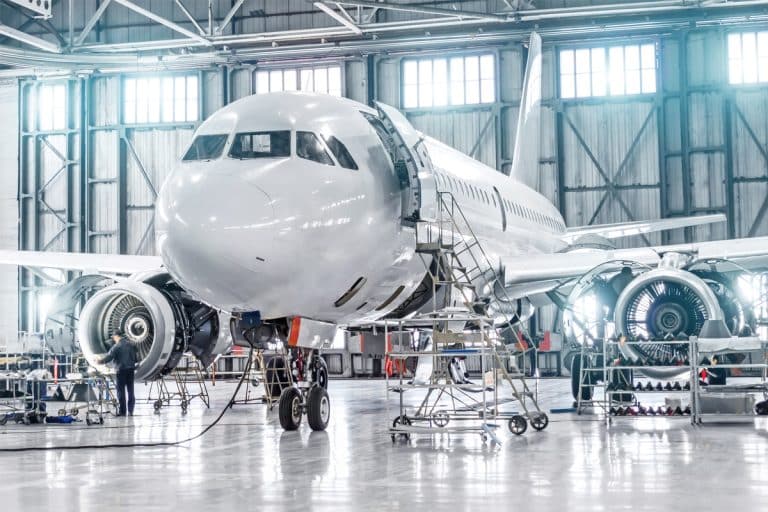
Aerospace Industry
The CNC router is widely used in aerospace engineering due to its unparalleled ability to carve complex designs, manufacture complex parts, and ensure tight tolerances.
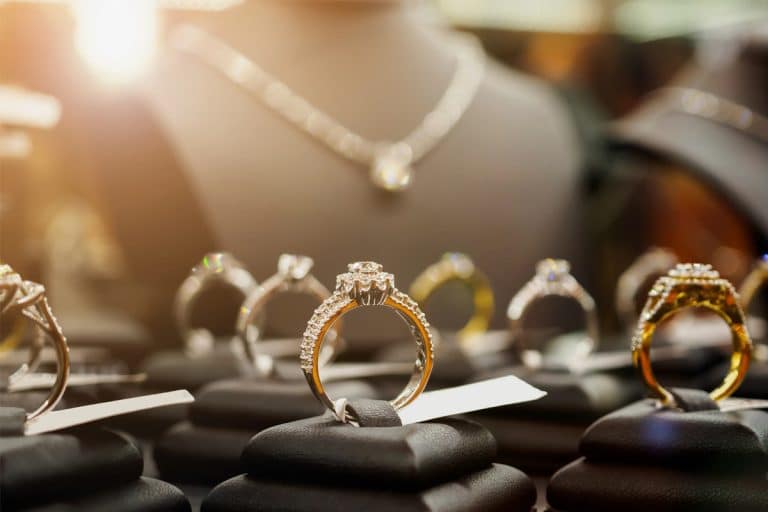
Jewelry Industry
The CNC router revolutionize the way fine jewelry is designed and made by delivering unparalleled precision and efficiency and producing intricate designs with meticulous attention to detail.
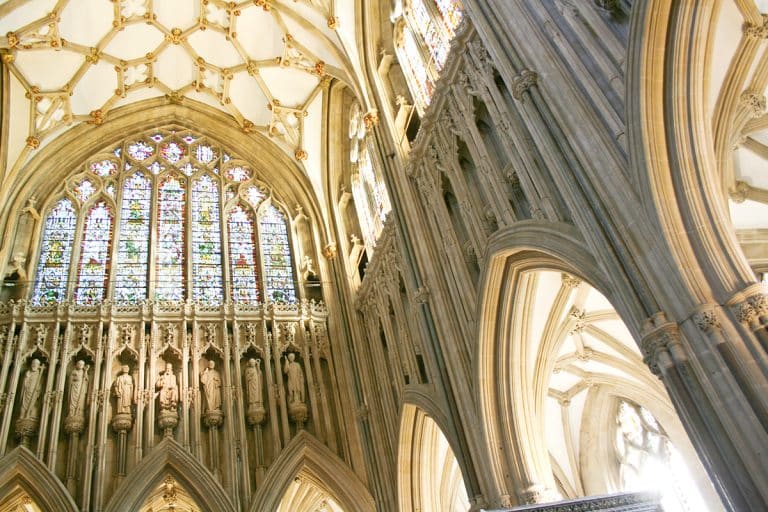
Stone Carving Industry
The integration of CNC routers into the stone carving industry is not only revolutionizing the way craftsmen carve, it is also redefining the boundaries of artistic possibilities in this ancient practice.
Blog
How to Reduce the Impact of Workpiece Adhesion on CNC Router Cutting Quality
This article delves into practical strategies for mitigating the impact of workpiece adhesion on CNC router cutting quality, to improve the performance and reliability of CNC router operations.
Read More
Addressing Environmental Concerns in CNC Router Waste Disposal: A Comprehensive Guide
In this article, we delve into the considerations for the correct disposal of waste materials from CNC router operations, aiming to tackle the environmental challenges posed by CNC waste.
Read More
Guide to Optimizing CNC Router Parameters for Diverse Materials
This article provides a systematic parameter optimization method for CNC routers cutting different materials, aiming to provide users with the necessary knowledge to achieve excellent processing quality.
Read More
Understanding the Perils of Spindle Runout in CNC Routers
This article delves into the causes of spindle runout and strategies for mitigating its effects, aiming to provide you with the knowledge to optimize CNC router performance.
Read More
Mastering CNC Router Worktables: A Comprehensive Guide
This article delves into the CNC router types, operating methods, maintenance, and customization options, providing you with the knowledge to optimize your CNC router settings for superior results.
Read More
CNC Router Bits: Complete Buyer’s Guide
From understanding the different types of CNC router bits to deciphering the nuances of materials and coatings, this guide provides the essential reference for finding the right bit for your ...
Read More
Frequently Asked Questions
What is a mini CNC router?
The mini CNC router is a compact computer numerical control (CNC) machine tool designed for precision machining on a smaller scale. These machines are typically smaller in size compared to standard CNC routers, making them suitable for hobbyists, DIY enthusiasts, and small-scale manufacturing. Mini CNC routers are versatile tools capable of cutting, engraving, and carving a variety of materials such as wood, plastic, soft metals, and composites. Despite their reduced footprint, they offer a reasonable level of precision, making them suitable for complex designs and projects.
The mini CNC router has a user-friendly interface, making it accessible to individuals with limited CNC experience. Due to their affordability, these CNC routers provide an entry point for those wishing to explore CNC technology without having to consider the space and cost associated with larger industrial machines. They find application in handcrafting, prototyping, and small-scale production of individual or custom-made projects.
What does a mini CNC router do?
The mini CNC router is a versatile machine that performs precision cutting, engraving, and carving on a variety of materials. Here are some of the key features and capabilities of the mini CNC router:
- Cutting: It is capable of precise cutting of materials such as wood, plastic, and soft metals. This makes them suitable for creating shapes, patterns, and components for a variety of applications.
- Carving And Carving: It is good at carving and carving detailed designs on materials. Users can create works of art, personalized crafts, or decorations with exquisite details.
- Milling: The mini CNC router can perform milling operations to shape the material to the desired shape by removing excess material. This is typically used in the production of custom parts and assemblies.
- Prototyping: Hobbyists and makers use the mini CNC router to prototype small projects. Its precision allows for the creation of precise prototypes before scaling up production.
- Signage Production: Due to its precision and versatility, mini CNC routers are popular for creating custom signage. It can engrave letters, logos, and graphics on materials such as wood or acrylic.
- DIY Projects: Hobbyists and DIY enthusiasts use the mini CNC router for a variety of projects, including crafting, model making, and home improvement. It enables individuals to turn their ideas into reality.
- Small-Scale Production: Although not designed for mass production, the mini CNC router can handle small-scale production runs, making it suitable for producing limited quantities of custom components or products.
- Educational Purposes: The mini CNC router is a valuable tool for educational purposes, providing hands-on experience in CNC technology, design, and manufacturing. It is frequently used in schools, seminars, and training programs.
What are the risks of using a mini CNC router?
While mini CNC routers are generally safe when used correctly, like any machinery, they also pose certain risks. Users need to be aware of these risks and take necessary precautions to ensure safety. Here are some common risks associated with using a mini CNC router:
- Mechanical Hazards: Moving parts such as spindles, cutting tools, and other components can pose a risk of entanglement or injury. Users should avoid placing hands or other objects near moving parts during operation.
- Material Hazards: Materials being processed may generate harmful dust, chips, or fumes. Proper ventilation, dust collection systems, and the use of appropriate respiratory protection may be required when handling certain materials.
- Electrical Hazards: The mini CNC router is powered by electricity, and there is a risk of electric shock if the machine is not properly grounded or the electrical components are damaged. Users should follow electrical safety guidelines.
- Tool Hazard: The cutting tools (drills) used in CNC routers can be sharp and can cause injury if not handled properly. Users should follow correct procedures for installing, changing, and securing tools and wear appropriate personal protective equipment (PPE) such as safety glasses.
- Noise and vibration: CNC router will produce noise and vibration during operation, which may cause discomfort or hearing damage if used for a long time. These risks can be mitigated by using ear protection and ensuring the machine is properly secured.
- Programming and Operating Errors: Improper programming or operating errors can cause unexpected movement or collision, which may damage the machine or cause injury. Users should carefully check their programs and operate the CNC router with caution.
- Read and understand the user manual provided by the manufacturer.
- Wear appropriate personal protective equipment (PPE), including safety glasses, hearing protection, and respiratory protection.
- Keep hands and other body parts away from moving parts during operation.
- Ensure proper ventilation when working with materials that may generate dust or fumes.
- Secure workpieces and machine components to prevent accidental movement.
- Follow proper tool replacement and tool maintenance procedures and guidelines.
- Check the machine regularly for any signs of wear, damage, or malfunction.
How much does a mini CNC router cost?
The mini CNC router costs between $3,000 and $8,000, depending on factors such as brand, specifications, and additional features. Entry-level models or basic configurations typically start around $3,000, making them affordable for hobbyists and DIY enthusiasts. When you move to higher-end models with advanced features, larger work areas, and greater accuracy, the price can go as high as $8,000.
Factors that influence cost include construction quality, spindle power, cutting speed, software compatibility, and overall machine functionality. When selecting a mini CNC router, your specific needs and budget constraints need to be carefully evaluated to ensure a balance between affordability and functionality required for the intended application.
How long does a mini CNC router last?
The lifespan of a mini CNC router can vary depending on a variety of factors, including the quality of the machine, frequency of use, maintenance practices, and the type of materials being processed. Generally speaking, a mini CNC router that is well maintained and used properly can last from 5 to 15 years or more.
The following are some factors that may affect the service life of your mini CNC router:
- Frequency of Use: Heavy continuous use may cause more wear and tear, potentially shortening the life of the machine. Occasional or moderate use may extend service life.
- Maintenance: Regular and correct maintenance, including cleaning, lubricating, and inspecting components, can significantly extend the life of your CNC router. To extend the life of your machine follow the manufacturer’s maintenance guidelines.
- Build Quality: The overall structure and build quality of the machine play an important role. CNC router made of durable materials and precision components has a longer service life.
- Environmental Conditions: The operating environment will affect the service life. Extreme temperatures, humidity, or exposure to dust and debris can affect the performance and life of your machine.
- Upgradeability: Some mini CNC routers are designed with upgradability in mind, allowing users to replace or upgrade certain components. Machines with this kind of flexibility are likely to have a longer effective life because they can adapt to changing needs.
Do I need to calibrate the mini CNC router?
Yes, calibrating the mini CNC router is an important step to ensure accurate machining. Calibration helps align the machine’s movements with programmed instructions, minimizing errors and improving finished product quality. Here are some key aspects of calibration:
- Mechanical Alignment: Verify that the machine’s mechanical components, such as lead screws, guides, and bearings, are in good condition and properly aligned. Any misalignment will affect the accuracy of the CNC router.
- Steps Per Unit: This parameter defines the number of steps required by the stepper motor to move the machine a specific distance. Precise calibration of steps per unit ensures the machine moves exactly as programmed.
- Acceleration And Deceleration: Adjusting the acceleration and deceleration settings will affect the speed at which the CNC router accelerates or decelerates during movement. Proper calibration can prevent problems like overshooting or uneven cuts.
- Tool Length Offset Calibration: Calibrate the tool length offset to accurately represent the length of the cutting tool. This ensures that the tool engages the material at the correct depth during machining.
- Origin Calibration: Establish a reliable origin position for the CNC router. This reference point helps ensure a consistent and repeatable starting position across machining projects.
- Software Settings Calibration: Verify that the CNC controller software settings match the physical characteristics of the machine. This includes specifying the correct number of motor steps, acceleration, and other parameters.