Foam CNC Router
The foam CNC router is a special machine designed for the precision cutting and shaping of foam materials. The router utilizes computer numerical control (CNC) technology to automate the cutting process based on digital design files, ensuring accurate and repeatable results. Foam CNC routers are commonly used in industries such as packaging, signage, and manufacturing, where foam is used for insulation, packaging inserts, or complex designs.
The foam CNC router consists of a rigid frame, a cutting spindle or tool, and a computer control system. The cutting spindle moves along multiple axes (usually three or more) based on a digital design generated by CAD (computer-aided design) software. By controlling the speed, depth, and path of the tool, detailed and complex shapes or structures can be created with high precision.
Foam CNC routers are widely used in industries such as manufacturing, automotive, aerospace, packaging, and art. It can be used to produce foam molds, packaging inserts, signage, sculptures, architectural models, and more, facilitating rapid prototyping and production processes.
Tips for choosing the right foam CNC router
Choosing the right foam CNC router can significantly impact the accuracy, productivity, and quality of your foam projects. We’ll guide you through key considerations, from material compatibility and machine size to accuracy, spindle power, and software integration. Whether you’re manufacturing, designing, or prototyping, our insights are designed to simplify the decision-making process and ensure you invest in a foam CNC router that’s perfectly suited to your unique needs.
Material compatibility
Make sure the CNC router is compatible with the type of foam you will be using, such as polystyrene, polyurethane, or expanded polystyrene (EPS). Verify that the machine’s cutting capabilities are consistent with the density and thickness of the foam material.
Machine dimensions and working area
Consider the physical dimensions of the CNC router in your workspace and the dimensions of the foam board you will be working with. Assess the machine’s work area to make sure it can accommodate the maximum foam size you anticipate without affecting movement or cutting capabilities.
Precision and accuracy
Check the machine’s specifications for accuracy, tolerance levels, and cut repeatability. Look for features like high-resolution ball screws, rigid frames, and precision spindle motion that facilitate precise cutting to help achieve complex foam designs.
Spindle power and speed
Evaluate spindle power and speed options. Higher power can cut denser foam, while variable speed options can be adjusted for different cutting requirements. Make sure it meets the needs of your intended project.
Number of axes
Consider the number of axes the machine operates on. More axes (usually three or more) increase flexibility in cutting complex shapes and contours of foam.
Software compatibility
Evaluate the compatibility of the CNC router with CAD/CAM software. Make sure it supports file formats commonly used in design workflows, promoting seamless integration and ease of operation.
Dust removal system
Check to see if there is an effective dust collection system. Foam cutting generates a lot of dust, and a reliable collection system can help maintain a clean working environment, extend tool life, and minimize health and safety issues.
Tool changing ability
If your project involves different cutting tools or requires changing tools to complete different tasks, consider having an automatic tool change feature. This feature enhances versatility and efficiency in handling a variety of foam-cutting requirements.
Machine rigidity and stability
Evaluate the rigidity and stability of the machine frame. The sturdy and stable construction helps achieve precise cuts and minimizes vibrations that can affect cut quality, especially when working with softer foam materials.
Maintenance and support
Consider the CNC router’s maintenance requirements and the availability of technical support, spare parts, and service. Choose machines with user-friendly maintenance features and reliable support systems to minimize downtime.
Budget and ROI
Evaluate the initial cost of the machine against the long-term return on investment. Consider productivity improvements, efficiency gains, and CNC router durability. A well-balanced investment should fit within your budget while providing significant value over time.
Comments and suggestions
Research user reviews and seek recommendations from individuals or businesses in similar industries. Real-world experience can give you insight into the performance, reliability, and overall satisfaction of the foam CNC router you’re considering.
What foam materials can the foam CNC router cut?
The foam CNC router is versatile and capable of cutting a variety of foam materials. The specific types of foam that a CNC router can cut depend on the machine’s design, cutting capabilities, and the nature of the foam material. Common foam materials that can be processed using a foam CNC router include:
- Polystyrene (PS)
- Polyurethane (PU)
- Expanded Polystyrene (EPS)
- Polyethylene (PE)
- Polypropylene (PP)
- Acoustic Foam
- Polyvinyl Chloride (PVC)
- Polyethylene Terephthalate (PET)
- Polyisocyanurate (PIR)
- Polyurethane (PUR)
- High-Density Foam
Application Industry
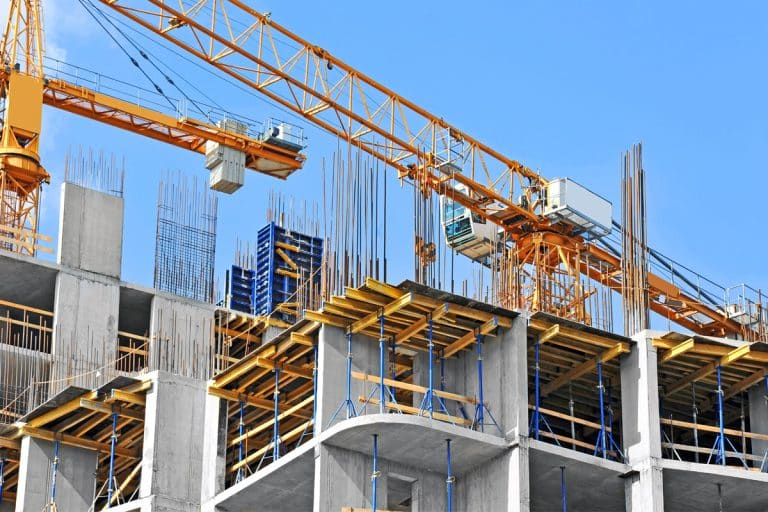
Construction Industry
The integration of CNC routers into construction workflows has ushered in a new era characterized by meticulous detailing, rapid prototyping, and improved material utilization.
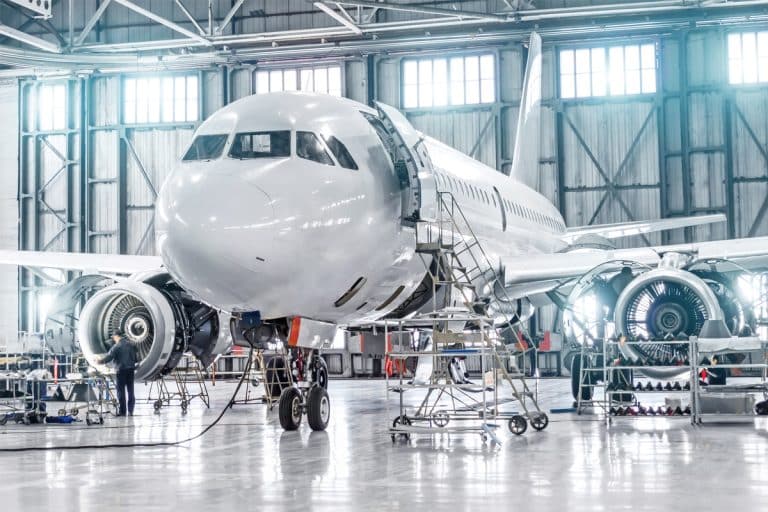
Aerospace Industry
The CNC router is widely used in aerospace engineering due to its unparalleled ability to carve complex designs, manufacture complex parts, and ensure tight tolerances.
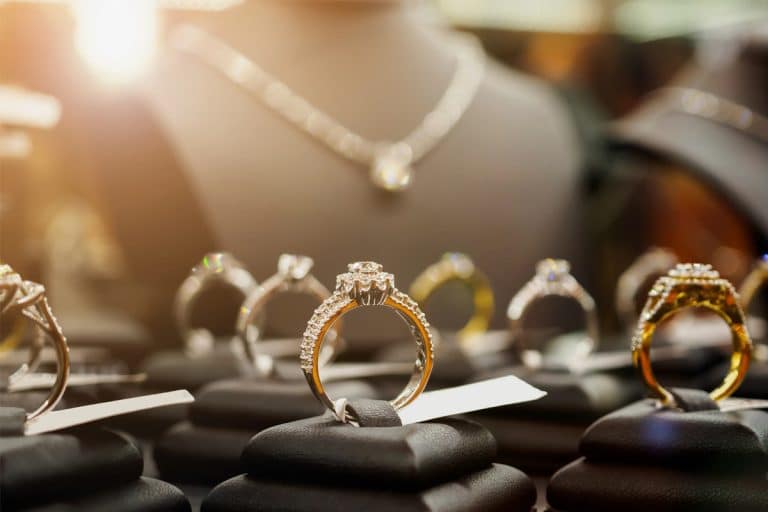
Jewelry Industry
The CNC router revolutionize the way fine jewelry is designed and made by delivering unparalleled precision and efficiency and producing intricate designs with meticulous attention to detail.
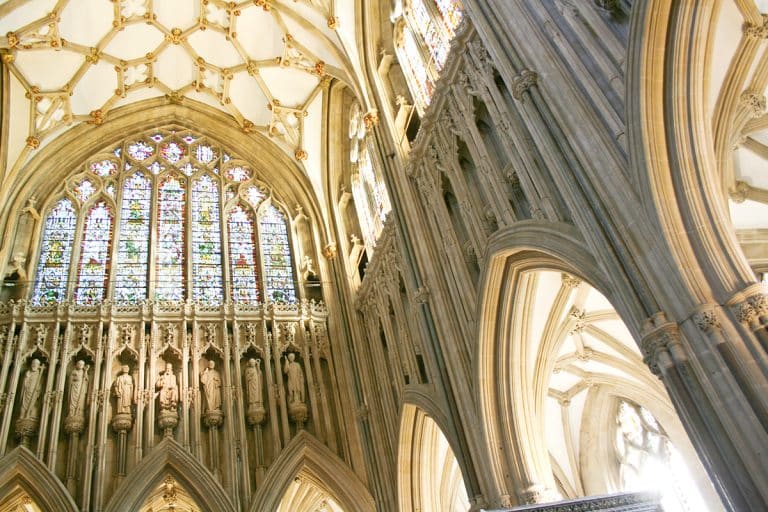
Stone Carving Industry
The integration of CNC routers into the stone carving industry is not only revolutionizing the way craftsmen carve, it is also redefining the boundaries of artistic possibilities in this ancient practice.
Blog
How to Reduce the Impact of Workpiece Adhesion on CNC Router Cutting Quality
This article delves into practical strategies for mitigating the impact of workpiece adhesion on CNC router cutting quality, to improve the performance and reliability of CNC router operations.
Read More
Addressing Environmental Concerns in CNC Router Waste Disposal: A Comprehensive Guide
In this article, we delve into the considerations for the correct disposal of waste materials from CNC router operations, aiming to tackle the environmental challenges posed by CNC waste.
Read More
Guide to Optimizing CNC Router Parameters for Diverse Materials
This article provides a systematic parameter optimization method for CNC routers cutting different materials, aiming to provide users with the necessary knowledge to achieve excellent processing quality.
Read More
Understanding the Perils of Spindle Runout in CNC Routers
This article delves into the causes of spindle runout and strategies for mitigating its effects, aiming to provide you with the knowledge to optimize CNC router performance.
Read More
Mastering CNC Router Worktables: A Comprehensive Guide
This article delves into the CNC router types, operating methods, maintenance, and customization options, providing you with the knowledge to optimize your CNC router settings for superior results.
Read More
CNC Router Bits: Complete Buyer’s Guide
From understanding the different types of CNC router bits to deciphering the nuances of materials and coatings, this guide provides the essential reference for finding the right bit for your ...
Read More
Frequently Asked Questions
Can a CNC router cut foam?
Yes, a CNC router is great for cutting foam materials. CNC routers are versatile machines that can be used to precision cut, engrave, and shape a variety of materials, including foam. Foam materials such as polystyrene, polyurethane, and expanded polystyrene (EPS) are often cut using a CNC router.
The process involves using CAD (computer-aided design) software to program the CNC router according to specific instructions. The CNC router then follows these programming instructions to precisely cut and shape the foam material. The cutting tool, typically a milling cutter or a specialized foam cutting tool, is controlled by a CNC system and moves along multiple axes to create complex designs or cut-specific patterns.
CNC routers are widely used in industries such as packaging, signage, automotive, aerospace, and manufacturing to perform tasks involving cutting foam for prototyping, modeling, or production. Their high accuracy, efficiency, and ability to replicate designs consistently make them an excellent choice for foam-cutting applications.
How do You Cut Foam with a Foam CNC Router?
Cutting foam using a foam CNC router involves multiple steps to ensure precision and accuracy. Here are the general guidelines:
- Design Preparation: Start by designing or getting a digital design or model of the foam object or pattern you want to cut. The design was created using CAD (Computer Aided Design) software.
- Software Settings: Load the design file into the CNC router’s control software. The software converts the design into tool path instructions that the CNC router will follow.
- Material Preparation: Fix the foam material on the CNC router. Depending on the machine, this may require clamps, adhesives, or other securing methods to prevent the material from moving during the cutting process.
- Tool Selection: Choose the right foam cutting tool. Common options include a straight mill or a specialized foam cutter. Tool selection depends on the type and density of the foam material.
- Set Cutting Parameters: Input cutting parameters such as cutting speed, spindle speed, cutting depth, tool path strategy, etc. into the CNC control software. These settings ensure optimal cutting results based on foam material properties.
- CNC Operation: Start the CNC router and start the cutting process. The machine will follow a programmed tool path, moving the cutting tool precisely along multiple axes to carve out the foam according to the design.
- Quality Inspection And Finishing: After the cutting process, inspect the foam cuts for accuracy and quality. Depending on the desired result, sanding or finishing may be required to smooth edges or refine surface texture.
- Cleanup: Remove the cut foam blocks from the CNC router table and clean the machine to maintain its performance for future use.
Why choose the foam CNC router?
The foam CNC router offers several advantages that make it the first choice for cutting foam materials:
- Precision And Accuracy: The foam CNC router provides high precision and accuracy cutting, enabling complex designs and detailed patterns with consistent results.
- Versatility: It can cut a variety of foam materials, including polystyrene, polyurethane, and expanded polystyrene (EPS), making it suitable for a variety of applications across a variety of industries.
- Efficiency And Speed: The foam CNC router automates the cutting process, increasing efficiency and reducing production time compared to manual cutting methods. This is especially beneficial for large-scale or repetitive tasks.
- Complex Shapes And Designs: The ability to handle multiple axes and follow complex tool paths enables the foam CNC router to cut complex shapes and designs that may be challenging or time-consuming with manual methods.
- Customization And Complexity: It can cut complex shapes, patterns, and designs, allowing for customization and creativity in foam-based projects.
- Repeatability: Once a design is programmed, the CNC router can replicate it consistently, maintaining accuracy and quality throughout the production process.
- Reduced Labor Costs: Automating the cutting process reduces reliance on manual labor, saving labor-hour costs and minimizing the risk of human error.
- Material Optimization: The CNC router optimizes material usage by strategically planning cuts, reducing waste, and maximizing foam board production.
- Integrated With CAD/CAM Software: The CNC router is seamlessly integrated with CAD/CAM software, allowing users to easily design and program cutting paths and improve workflow efficiency.
- Scalability: Whether it’s a small project or large-scale production, the foam CNC router offers scalability to meet the needs of different manufacturing or creative jobs.
- Safety And Cleanliness: The foam CNC router is often equipped with dust collection systems, promoting a cleaner work environment and reducing the health risks associated with frothy dust.
- Wide Range of Applications: The foam CNC router is suitable for various industries, including packaging, signage, automotive, aerospace, and art industries, making it a versatile tool for different production needs.
What speed is foam routing?
The speed of routing foam with a CNC router can vary depending on several factors, including the type of foam material, the density of the foam, the specific CNC router used, the cutting tool, and the desired finish. Generally speaking, foam routing speeds can range from a few inches per minute (IPM) to hundreds of IPM.
Cutting speed is a key parameter in CNC routing and is usually determined by the CNC router operator or programmer based on factors such as material properties, tool specifications, and required cut quality. Cutting speed must be balanced with factors such as spindle speed, depth of cut, and feed rate to get the best results.
Higher cutting speeds may be appropriate for softer foams, while denser foams may require slower speeds to maintain accuracy and prevent excessive tool wear. It is recommended to refer to the CNC router manufacturer’s guidelines and tool specifications and make test cuts to determine the most efficient cutting speed for your specific foam material and project requirements.
What router bits can be used to cut foam?
When cutting foam with a CNC router, choosing the right router bits is crucial for achieving clean and precise results. Here are some common types of router bits used for cutting foam:
- Straight Flute Bits:
- Ideal for general foam-cutting applications.
- Available in various sizes to accommodate different foam thicknesses.
- Upcut Spiral Bits:
- Pulls chips up and out of the cut, reducing the risk of heat buildup.
- Suitable for softer foam materials and allows for efficient chip evacuation.
- Downcut Spiral Bits:
- Pushes chips downward, providing a smoother top surface.
- Suitable for preventing chipping or tear-out on the top surface of the foam.
- Compression Bits:
- Feature a combination of upcut and downcut flutes, designed for laminated materials.
- Ideal for cutting through materials with varying densities, like layered foam.
- Ball Nose Bits:
- Useful for 3D carving and contouring in foam.
- Creates rounded edges and smooth surfaces.
- V-Bits:
- Ideal for carving detailed designs or creating chamfers.
- Commonly used for signage and artistic projects involving foam.
- Tapered Ball Nose Bits:
- Similar to ball nose bits but with a tapered end.
- Useful for intricate 3D carving and detailing in foam.
- Fish Tail Bits:
- Feature a flat end with a tapered edge, suitable for general foam cutting.
- Offers a balance between cutting speed and surface finish.
- Diamond-Coated Bits:
- Specifically designed for cutting harder foam materials.
- Provide extended tool life and reduced friction.
How Much Does A Foam CNC Router Cost?
The cost of a foam CNC router can vary greatly based on a variety of factors, including the machine’s size, capabilities, brand, and additional features. Here’s a general overview:
- Entry-Level or Small Machines: These machines have a smaller work area and basic features and start at around $3,000 to $5,000.
- Mid-Range CNC Router: A machine with a larger work area, higher accuracy, and additional features that range in price from $5,000 to $20,000.
- High-End Industrial-Grade CNC Routers: Equipped with advanced features, larger work areas, greater precision, and rugged construction, these machines range in price from $20,000 to $50,000 or more, depending on size and features.
What precautions should be taken when using a foam CNC router?
Using a foam CNC router requires the use of certain safety precautions for machinery and materials. Here are key precautions to consider:
- Read The Manual: Familiarize yourself with the CNC router’s manuals and guides. Understand the machine’s specifications, safety features, and recommended operating procedures.
- Personal Protective Equipment (PPE): Wear appropriate PPE, such as safety glasses, hearing protection (if the machine is loud), and a dust mask (if required) to minimize exposure to foamy dust. PPE requirements may vary depending on the specific machine and material being cut.
- Secure The Workpiece: Be sure to secure the foam material securely to the workbench using a clamp or vacuum holding system to prevent movement during cutting.
- Dust Collection: Use a dust collection system to minimize the generation of foamy dust. Inhaling foam dust can be harmful and may create a messy work environment.
- Tool Inspection: Check cutting tools regularly for wear and damage. Replace dull or damaged tools to ensure clean, safe cuts.
- Emergency Stops And Controls: Familiarize operators with emergency stop buttons or switches on the machine. Be prepared to shut down the machine quickly if any problems arise.
- Supervision: Stay near the machine and supervise the cutting process, especially during initial setup or when running a new program. Be prepared to intervene if anything goes wrong.
- Spindle Speed And Feed Rate: Follow the recommended spindle speed and feed rate settings for the specific foam material being cut. Too high a speed can result in overheating, while not enough speed can result in a poor cut.
- Tool Changing: If replacing cutting tools, follow proper tool changing procedures, including turning off the power to the machine, securing the tool, and calibrating as needed.
- Ventilation: Make sure your work space is well-ventilated to minimize exposure to fumes or dust generated during the cutting process.
- Training: Ensure operators receive adequate training on the operation of the CNC router. Training should cover the functionality and safe operating procedures of the machine.
- Fire Safety: Be aware of the heat that may be generated during cutting. Keep flammable materials away from the machine and have fire-extinguishing equipment nearby.
How to Use the Foam CNC Router Machine to Make Money?
Using a foam CNC router can be a lucrative investment if done strategically. Here are some ways to profit from your foam CNC router:
- Custom Signage & Lettering: Personalized and intricate foam signage for businesses, events, or individuals. Custom logos, lettering, and designs can be created with precision.
- Architectural Models: Provide architectural firms with detailed foam models for use in presentations and client meetings. CNC routers can accurately replicate complex architectural designs.
- Packaging Inserts And Prototyping: Work with manufacturers to create custom bubble wrap inserts for delicate items. In addition, prototyping services are provided for product development.
- Art And Sculpture: Cater to the needs of artists or art institutions by creating foam sculptures and works of art. The precision of the CNC router enables complex and detailed designs.
- Event Decoration And Theming: Provides event planners and decorators with custom foam props, decorations, and themed elements for parties, weddings, or corporate events.
- Education Model: Work with educational institutions to create bubble models for science, geography, or history courses. CNC routers can produce accurate and visually appealing models.
- Custom Foam Padding For Cases: Work with your device manufacturer or photographer to create custom foam padding for your case to ensure a snug fit on your valuable device.
- Automotive Interiors: Work with an automotive enthusiast or custom shop to create custom foam inserts for interior components such as armrests, center consoles, or storage bins.
- Custom Foam Cushions And Pillows: Customized foam cushions and pillows for furniture or bedding to meet the needs of individuals seeking unique, comfortable home décor.
- Themed Retail Displays: Work with retail businesses to create eye-catching foam displays for storefronts, trade shows, or product displays.
- Insulation And Building Components: Provides custom foam insulation or building components for construction projects.
- Work With Designers And Artists: Work with designers and artists to bring their foam concepts to life, providing a valuable resource for your CNC routing services.