Foam CNC Router
Foam CNC routers are advanced machines designed to precisely cut, shape, and carve foam materials for a wide range of industries. From automotive and aerospace to signage, architecture, and even the entertainment industry, these CNC routers are built to deliver exceptional accuracy, speed, and efficiency. Whether you’re producing prototypes, intricate designs, or large-scale projects, a foam CNC router provides the versatility and reliability needed to meet demanding production standards.
Equipped with robust spindles, advanced control systems, and powerful motors, foam CNC routers can handle various foam materials, including EPS, XPS, EPP, and more. Their high precision ensures clean edges and complex 3D cuts, allowing for the creation of everything from detailed models to large-scale foam structures. With easy-to-use software and automated features, these routers minimize human error and reduce labor costs, making them an essential tool for modern manufacturing.
Built to optimize both speed and quality, foam CNC routers offer a cost-effective solution for businesses looking to enhance their production capabilities. Whether for one-off designs or continuous production runs, our range of foam CNC routers provides the flexibility and performance you need to take your operations to the next level.
-
AKM-4A2 CNC Router
Rated 5.00 out of 5$15,000.00 Add to cart -
AKM-4A3 CNC Router
$22,000.00 Add to cart -
AKM1325-4A CNC Router
Rated 5.00 out of 5$15,000.00 Add to cart -
AKM1530-4A CNC Router
Rated 5.00 out of 5$15,600.00 Add to cart -
AKM2030-4A CNC Router
Rated 5.00 out of 5$16,200.00 Add to cart -
AKM2040-4A CNC Router
Rated 5.00 out of 5$16,600.00 Add to cart -
AKM1325C-4A CNC Router
Rated 5.00 out of 5$20,000.00 Add to cart -
AKM1530C-4A CNC Router
Rated 5.00 out of 5$20,600.00 Add to cart -
AKM2030C-4A CNC Router
Rated 5.00 out of 5$21,200.00 Add to cart -
AKM2040C-4A CNC Router
Rated 5.00 out of 5$21,600.00 Add to cart -
AKM1212-5A CNC Router
Rated 5.00 out of 5$57,500.00 Add to cart -
AKM1224-5A CNC Router
Rated 5.00 out of 5$61,000.00 Add to cart
Tips for Choosing the Right Foam CNC Router
Choosing the right foam CNC router can significantly impact your production efficiency and the quality of your projects. With numerous factors to consider, including material compatibility, precision, and machine features, it’s essential to select a CNC router that aligns with your specific requirements.
Identify the Foam Material Type
Different types of foam materials, such as EPS, XPS, and EPP, require varying levels of cutting power and precision. Make sure the CNC router you choose is compatible with the foam you plan to work with. This ensures smoother cuts and better overall performance, as some machines are better suited for softer or denser foam types.
Evaluate Cutting Precision and Accuracy
Precision is one of the primary benefits of a CNC router. When selecting a machine, ensure it provides the level of accuracy required for your projects. For fine detailing or intricate designs, opt for a CNC router with high-resolution control, fine spindles, and minimal play in the axes to avoid imperfections in the finished product.
Consider the Work Area Size
The size of your foam materials will dictate the work area you need. If you work with large sheets or blocks of foam, choose a CNC router with a generous cutting area that can accommodate your largest pieces. A larger work area allows for more versatility and flexibility in your projects.
Check for Speed and Efficiency
The speed of the CNC router can directly affect production timelines, especially when dealing with high-volume projects. Look for a machine that offers a good balance between cutting speed and precision, particularly if you need to handle large production runs without compromising on quality.
Assess the Machine’s Software Compatibility
The CNC router’s software plays a key role in its ease of operation and compatibility with your existing design tools. Ensure the machine is compatible with popular software like AutoCAD, Rhino, or SolidWorks, and check if the machine includes intuitive, user-friendly control software for smooth operation.
Examine Build Quality and Durability
Investing in a durable and reliable machine is essential for minimizing downtime and repair costs. Look for CNC routers made from high-quality materials such as steel or aluminum, which can withstand the stresses of constant operation and ensure long-term durability in a production environment.
Check the Spindle Power and Tooling Options
The spindle power and the type of cutting tools available will determine the versatility of your CNC router. Choose a CNC router with sufficient spindle power for the type of foam you will be cutting, and ensure it offers various tool options like milling cutters and engraving bits to handle different design requirements.
Look for Automation Features
Automated features such as tool changers, vacuum hold-down systems, and automatic material feeders can greatly enhance efficiency. These features reduce manual labor, save time, and improve the overall consistency of your production runs, making them ideal for large-scale or continuous operations.
Consider the Dust and Fume Extraction System
Foam cutting generates dust and fumes that can pose health risks and damage the machine. Choose a CNC router equipped with an efficient dust collection system to ensure a cleaner workspace and reduce maintenance costs. This also contributes to operator safety and ensures compliance with workplace regulations.
Ensure Power Compatibility
Different CNC routers have varying power requirements, so it’s important to ensure that the CNC router is compatible with your facility’s power supply. Some models may require special electrical setups, and failure to meet these requirements could lead to installation issues or poor machine performance.
Check for After-Sales Support and Service
Good after-sales support is crucial to ensure the longevity and smooth operation of your foam CNC router. Before making a purchase, research the manufacturer’s warranty, customer service options, and availability of spare parts. A responsive support team can minimize downtime and help resolve technical issues quickly.
Balance Price with Features and Performance
While cost is always a consideration, it’s important to strike a balance between price and performance. Don’t settle for a cheaper model that compromises essential features such as cutting accuracy or machine durability. Instead, invest in a CNC router that offers the best value for your specific needs, ensuring long-term profitability and quality results.
What Materials Can The Foam CNC Router Cut
Foam CNC routers are highly versatile machines capable of cutting a wide range of foam materials with precision. These routers are designed to handle everything from soft foams like EPS (Expanded Polystyrene) to more rigid types such as XPS (Extruded Polystyrene) and EPP (Expanded Polypropylene). Additionally, they can cut composite foam materials used in industries like automotive, aerospace, and packaging. Whether you’re working with thin sheets or dense foam blocks, foam CNC routers can deliver clean, accurate cuts without compromising material integrity. This flexibility makes them ideal for applications such as model making, signage, prototyping, and custom designs, ensuring exceptional results for various foam-based projects.
- Polystyrene (PS)
- Polyurethane (PU)
- Expanded Polystyrene (EPS)
- Polyethylene (PE)
- Polypropylene (PP)
- Acoustic Foam
- Polyvinyl Chloride (PVC)
- Polyethylene Terephthalate (PET)
- Polyisocyanurate (PIR)
- Polyurethane (PUR)
- High-Density Foam
Application Industry
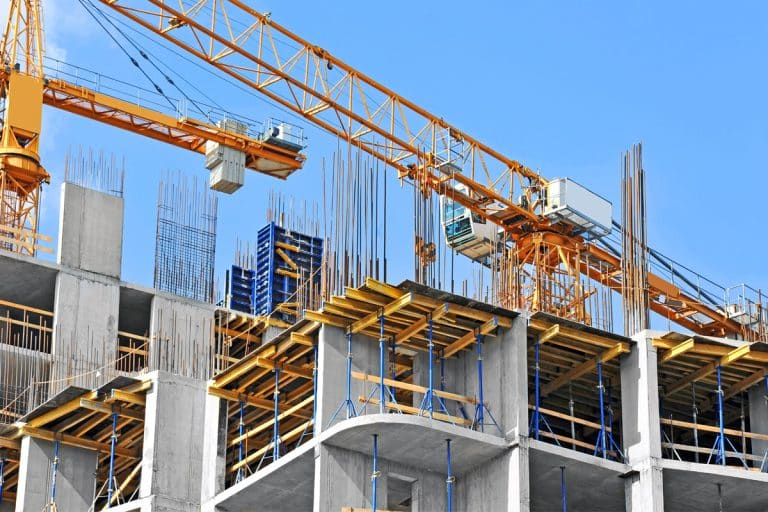
Construction Industry
The integration of CNC routers into construction workflows has ushered in a new era characterized by meticulous detailing, rapid prototyping, and improved material utilization.
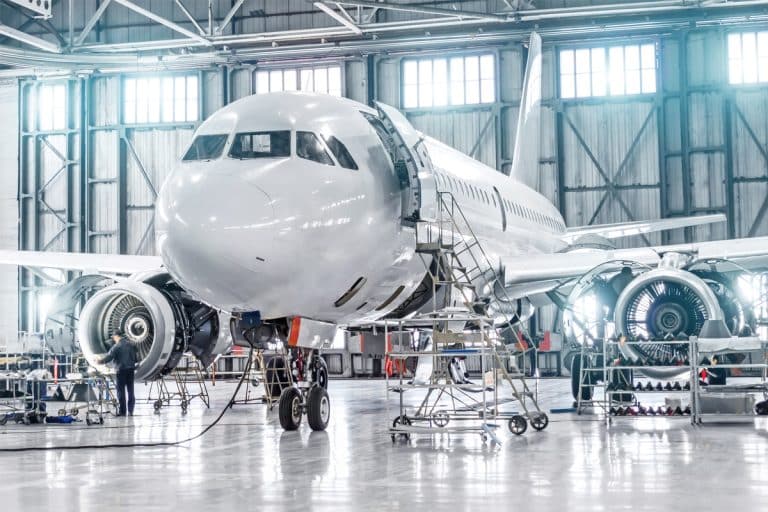
Aerospace Industry
The CNC router is widely used in aerospace engineering due to its unparalleled ability to carve complex designs, manufacture complex parts, and ensure tight tolerances.
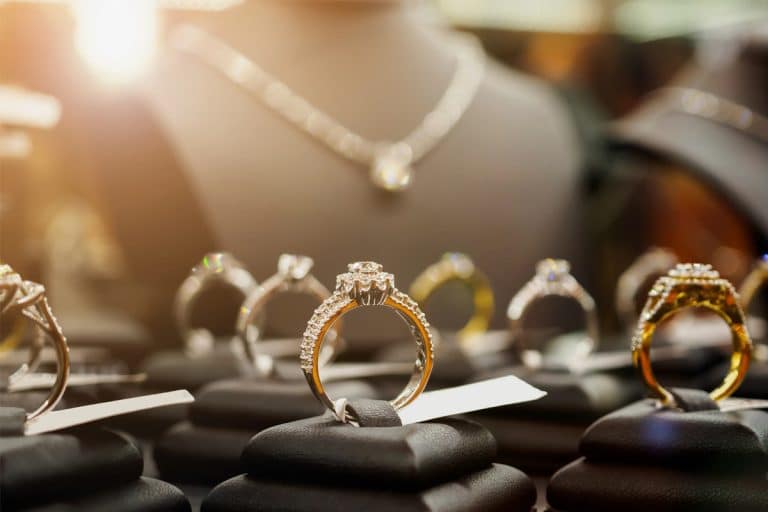
Jewelry Industry
The CNC router revolutionize the way fine jewelry is designed and made by delivering unparalleled precision and efficiency and producing intricate designs with meticulous attention to detail.
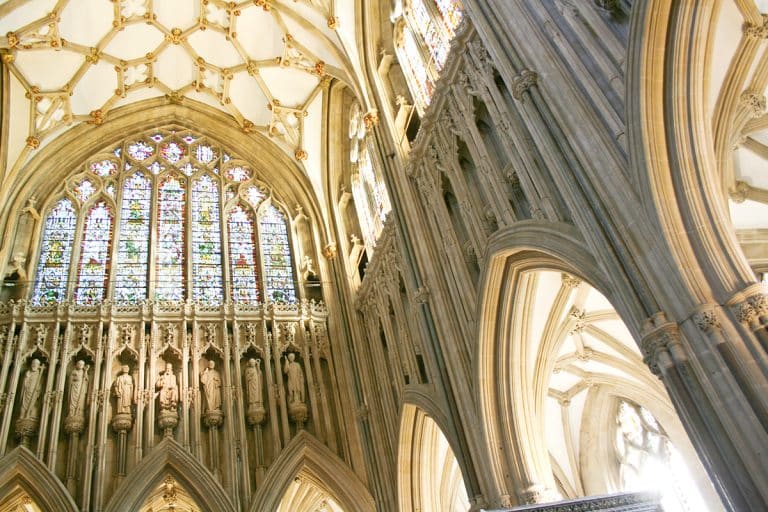
Stone Carving Industry
The integration of CNC routers into the stone carving industry is not only revolutionizing the way craftsmen carve, it is also redefining the boundaries of artistic possibilities in this ancient practice.
Blog
Is the Woodworking CNC Router Worth Buying?
In this article, we'll explore a CNC router's key advantages, cost factors, and suitability to help you decide if it's the right tool for your shop or business based on ...
Read More
How Deep Can a CNC Router Cut?
In this article, we'll break down the elements that influence CNC router cutting depth, typical values across different materials, and how to approach deep cutting safely and effectively.
Read More
What PPE is Recommended When Operating a CNC Router?
In this article, we'll go over the essential PPE recommended for CNC router use and explain how each item contributes to a safer and more comfortable working environment.
Read More
What Cooling Methods Are Needed for Metal CNC Routers?
This article explores the key cooling methods used in metal CNC routers and provides practical insights into selecting the right cooling system for your specific machining environment.
Read More
Frequently Asked Questions
How Do You Cut Foam with Foam CNC Routers?
Cutting foam with a CNC router involves a series of precise steps to ensure accurate and efficient results. Here’s an overview of the process:
- Design Preparation: Begin by creating or obtaining a digital design of the foam object using CAD (Computer-Aided Design) software. The design outlines the shape and dimensions of the foam part to be cut.
- Software Settings: Load the CAD file into the CNC router’s control software. The software then translates the design into tool path instructions, directing the CNC router on how to cut the foam.
- Material Preparation: Secure the foam material onto the CNC router bed. Depending on the machine, you may need clamps, adhesives, or other methods to ensure the material remains stationary during cutting.
- Tool Selection: Choose the appropriate cutting tool based on the type and density of foam you are working with. Common tools include straight mills or specialized foam cutters, each suited for different foam materials.
- Set Cutting Parameters: Input cutting parameters such as speed, spindle rotation, and cutting depth into the CNC software. Adjust these settings based on the material’s properties to achieve the best-cut quality.
- CNC Operation: Start the CNC router. The machine will follow the programmed tool paths, using precise movements along multiple axes to carve the foam as per the design.
- Quality Inspection and Finishing: After cutting, inspect the foam for accuracy and quality. Depending on the desired outcome, additional finishing like sanding or edge smoothing may be required.
- Cleanup: Once the cutting is completed, remove the foam parts from the CNC router and clean the machine to maintain optimal performance for future jobs.
What Speed is Foam Routing?
The speed of foam routing with a CNC router can vary significantly based on several factors, including the type of foam, its density, the specific CNC router model, the cutting tool being used, and the desired finish. Typically, foam routing speeds can range from just a few inches per minute (IPM) for denser materials to several hundred IPM for softer, more easily cut foams.
Cutting speed is a critical parameter in the CNC routing process and is determined by factors like material properties, the CNC router’s capabilities, and the intended cut quality. Operators need to strike a balance between cutting speed, spindle speed, depth of cut, and feed rate for optimal results. Softer foams, such as EPS (Expanded Polystyrene), generally allow for faster cutting speeds due to their lower density and ease of machining. On the other hand, denser foams like XPS (Extruded Polystyrene) or EPP (Expanded Polypropylene) require slower cutting speeds to maintain cutting accuracy, prevent tool wear, and avoid excessive heat buildup, which could affect foam quality.
To determine the ideal speed, it’s best to consult the CNC router manufacturer’s guidelines, follow tool specifications, and perform test cuts tailored to your specific foam material and project needs. This ensures an efficient, high-quality finish while maximizing machine longevity.
What CNC Router Bits Can Be Used to Cut Foam?
Choosing the right CNC router bit is crucial for achieving clean, precise cuts when using a CNC router to cut foam. Different types of foam require different tools, and each bit has specific advantages for different applications. Here are some common CNC router bits used for cutting foam:
- Straight Flute Bits: These are ideal for general foam cutting applications and come in various sizes to suit different foam thicknesses. They offer a straightforward cutting experience and are great for simple, straight cuts.
- Upcut Spiral Bits: Upcut spiral bits pull chips upward and out of the cut, which helps reduce heat buildup. These bits are particularly suitable for softer foams and ensure efficient chip evacuation, preventing clogging during cutting.
- Downcut Spiral Bits: These bits push chips downward, creating a smoother top surface on the foam. They are effective for preventing chipping or tear-out on the foam’s top layer, making them ideal for applications requiring a clean surface finish.
- Compression Bits: Compression bits combine upcut and downcut flutes, making them perfect for cutting through laminated materials or foam with varying densities. They help maintain smooth surfaces on both the top and bottom, ensuring clean cuts through multi-layered foams.
- Ball Nose Bits: Ball nose bits are used for 3D carving and contouring in foam, allowing for rounded edges and smooth, intricate surface textures. These bits are ideal for sculpting complex shapes and designs.
- V-Bits: V-bits are great for detailed carving and chamfering. They are often used in signage or artistic foam projects, allowing for precise angular cuts and intricate detailing.
- Tapered Ball Nose Bits: Tapered ball nose bits are similar to ball nose bits but feature a tapered end. These are excellent for creating detailed 3D carvings and fine surface contours, ideal for projects requiring high precision.
- Fish Tail Bits: Featuring a flat end with a tapered edge, fishtail bits provide a good balance between cutting speed and surface finish. They are often used for general foam cutting and offer versatility in various applications.
- Diamond-Coated Bits: Designed for cutting harder foam materials, diamond-coated bits offer extended tool life and reduce friction. These are excellent for tougher foams and provide clean, smooth cuts even under demanding conditions.
How Much Do Foam CNC Routers Cost?
The cost of foam CNC routers can vary widely based on factors such as size, features, brand, and the specific requirements of your cutting projects. Here’s a breakdown of typical price ranges:
- Entry-Level Models: Small CNC routers designed for light-duty applications and hobbyist use typically start around $3,000 to $5,000. These machines have smaller work areas and fewer advanced features, making them ideal for basic foam-cutting tasks.
- Mid-Range Models: These offer larger work areas, more precise cutting capabilities, and additional features like improved software and automation. Prices typically range from $5,000 to $20,000. These are suitable for small to medium-sized businesses that require a balance of affordability and performance.
- High-End Industrial Models: Industrial-grade CNC routers built for large-scale operations, high precision, and heavy-duty use range from $20,000 to $50,000 or more. These machines come with advanced features, such as larger workspaces, high-speed motors, and rugged construction, designed to meet the needs of high-volume production.
What Precautions Should Be Taken When Using Foam CNC Routers?
Using a foam CNC router requires adhering to several safety precautions to ensure both machine performance and operator safety. Below are essential steps to follow:
- Read The Manual: Familiarize yourself with the CNC router’s manual and guides to understand the machine’s specifications, safety features, and recommended operating procedures.
- Personal Protective Equipment (PPE): Always wear the appropriate PPE, including safety glasses to protect your eyes from debris, hearing protection to guard against high noise levels, and a dust mask to avoid inhaling foam dust, which can be harmful.
- Secure The Workpiece: Ensure that the foam material is securely fastened to the workbench using clamps or a vacuum holding system. This prevents the material from shifting during cutting, ensuring accuracy and safety.
- Dust Collection: Use an effective dust collection system to minimize foam dust, which can be hazardous to inhale. Maintaining a clean workspace also reduces the risk of fire or machine malfunction.
- Tool Inspection: Regularly inspect cutting tools for wear or damage. Dull or broken tools can compromise the quality of the cut and pose a safety risk. Replace tools as needed.
- Emergency Stops And Controls: Familiarize yourself with the machine’s emergency stop buttons or switches. In case of malfunction or irregularities, you must be able to shut down the machine quickly.
- Supervision: Always supervise the CNC router during operation, especially when running new programs or during the initial setup. Stay close to the machine to intervene if any issues arise.
- Spindle Speed and Feed Rate: Follow the manufacturer’s recommendations for spindle speed and feed rate settings based on the foam material being cut. Over-speeding can overheat the tool, while a low speed can lead to poor cuts.
- Tool Changing: When changing tools, ensure the machine is powered off. Properly secure and calibrate the new tool before resuming operation.
- Ventilation: Ensure your workspace is well-ventilated to reduce the accumulation of fumes and dust generated during cutting. Proper ventilation minimizes health risks and keeps the environment clean.
- Training: Provide thorough training to operators, covering safe operation practices, machine functions, and troubleshooting procedures. Well-trained operators are key to maintaining safety.
- Fire Safety: Be cautious of heat generated during foam cutting, especially with dense foam materials. Keep flammable materials away from the machine and have fire-extinguishing equipment readily available.
What Is the Expected Lifespan of Foam CNC Routers?
The lifespan of a foam CNC router can vary significantly based on factors such as the quality of the machine, frequency of use, maintenance practices, and the environment in which it operates. However, on average, foam CNC routers can last anywhere from 5 to 15 years with proper care. Several factors influence the longevity of a CNC router:
- Quality of the Machine: High-end, industrial-grade CNC routers typically last longer due to their robust construction, advanced components, and precision engineering. Entry-level or lower-cost models may have a shorter lifespan, particularly if used heavily.
- Maintenance: Regular maintenance plays a crucial role in extending the lifespan of the machine. This includes routine inspections, lubrication of moving parts, replacing worn tools, and checking the alignment and calibration of components.
- Frequency of Use: Machines that are used more frequently in high-demand environments, such as commercial production facilities, will experience more wear and tear. Conversely, machines used less often or in smaller workshops may last longer.
- Material Types: Cutting denser or harder materials, or using the CNC router in a more demanding application, can contribute to faster wear on the machine’s components. Foam, being a relatively softer material, tends to be gentler on the CNC router, allowing for a longer lifespan when compared to cutting harder materials.
- Environmental Factors: Operating the CNC router in a clean, well-ventilated area with proper humidity and temperature controls can prevent unnecessary strain on the machine and reduce wear.
What Customer Support Do Foam CNC Routers Provide?
Foam CNC routers come with reliable customer support options to ensure smooth operation and user satisfaction:
- Free Online Technical Support: Customers can access complimentary technical assistance through online platforms, including email, chat, or video support. This service is ideal for troubleshooting, software setup, or resolving operational issues remotely.
- Paid On-Site Training: For users requiring hands-on guidance, on-site training sessions are available at an additional cost. These sessions cover installation, operation, and maintenance to ensure optimal use of the machine.
What Is The Warranty Period of Foam CNC Routers?
Our CNC router is backed by a comprehensive warranty designed to give you peace of mind and protect your investment:
- 3-Year Warranty for the Entire Machine: This full warranty covers any defects or malfunctions in the machine as a whole, ensuring reliable performance and longevity over time.
- 5-Year Warranty for Core Components: Key components essential for optimal machine operation are covered for 1.5 years. This includes parts that may experience wear and tear with regular use, ensuring you have support for the most vital parts of the machine.