Industrial CNC Router
Industrial CNC routers are advanced precision machines designed to automate the process of cutting, shaping, and engraving materials with exceptional accuracy and speed. Ideal for industries such as woodworking, aerospace, automotive, and metalworking, these CNC routers provide reliable and repeatable results for both complex and simple tasks.
Equipped with state-of-the-art technology, our CNC routers are engineered to handle a wide variety of materials including wood, plastics, composites, and metals. They are capable of performing intricate designs, detailed cuts, and smooth finishes, all while maintaining optimal efficiency. Whether you’re manufacturing high-volume products or custom, one-off pieces, these CNC routers deliver the flexibility and versatility required to meet the demands of modern production environments.
With a range of customizable features including automated tool changers, multi-axis capabilities, and user-friendly interfaces, our CNC routers are designed to enhance your production workflows, reduce labor costs, and increase overall throughput. Whether you’re upgrading your existing machinery or building a brand-new production line, our industrial CNC routers provide the performance and precision necessary to stay ahead in today’s competitive marketplace.
-
AKM2030 CNC Router
Rated 5.00 out of 5$6,000.00 Add to cart -
AKM2040 CNC Router
Rated 5.00 out of 5$6,500.00 Add to cart -
AKM2030C CNC Router
Rated 5.00 out of 5$14,600.00 Add to cart -
AKM2040C CNC Router
Rated 5.00 out of 5$15,000.00 Add to cart -
AKM2030-4A CNC Router
Rated 5.00 out of 5$16,200.00 Add to cart -
AKM2040-4A CNC Router
Rated 5.00 out of 5$16,600.00 Add to cart -
AKM2030C-4A CNC Router
Rated 5.00 out of 5$21,200.00 Add to cart -
AKM2040C-4A CNC Router
Rated 5.00 out of 5$21,600.00 Add to cart -
AKM2030-R CNC Router
Rated 5.00 out of 5$6,700.00 Add to cart -
AKM2040-R CNC Router
Rated 5.00 out of 5$7,200.00 Add to cart -
AKM2030-4R CNC Router
Rated 5.00 out of 5$10,200.00 Add to cart -
AKM2040-4R CNC Router
Rated 5.00 out of 5$10,600.00 Add to cart
Tips for Choosing the Right Industrial CNC Router
Choosing the right industrial CNC router is crucial for ensuring optimal productivity, precision, and material compatibility in your operations. With so many options available, it’s important to carefully evaluate your specific needs, the materials you’ll be working with, and the type of production you plan to run.
Identify Your Production Needs
Start by determining the scale of your production. Will you be working on small, custom jobs or high-volume manufacturing? Larger CNC routers are ideal for mass production, while smaller models may be more suitable for specialized tasks or low-volume runs. Choosing the right machine based on your production scale helps maximize efficiency and minimize unnecessary costs.
Assess Material Compatibility
Different CNC routers are suited for different materials. Whether you’re working with wood, plastics, metals, or composites, make sure the CNC router you choose is compatible with the materials you plan to use. Some CNC routers have specialized spindles or cutting tools that are tailored to specific materials, so it’s important to match your material needs with the machine’s capabilities.
Consider Cutting Area and Machine Size
The cutting area, or bed size, is one of the most important factors to consider. Ensure the CNC router can accommodate the largest workpieces you plan to produce. A larger work area allows you to cut larger components without the need for repositioning, improving accuracy and throughput. Make sure the machine size aligns with your workspace and production demands.
Focus on Precision and Tolerances
High precision is crucial for industries requiring intricate designs or fine details. Look for a CNC router that offers tight tolerances and a high degree of accuracy, particularly if you work in sectors like aerospace, automotive, or high-end woodworking. Higher precision machines may come at a premium, but they ensure better-quality results and reduce waste.
Select the Right Spindle Power
The spindle is the heart of the CNC router, driving the cutting process. For materials like metals or composites, you’ll need a higher-powered spindle to maintain cutting efficiency and precision. A more powerful spindle can handle tougher materials and deliver smoother cuts, while less demanding tasks can be handled with lower spindle power.
Evaluate Multi-Axis Functionality
Many CNC routers offer 3-axis, 4-axis, or even 5-axis capabilities. If you need to create complex parts with multiple angles or 3D geometries, opt for a multi-axis CNC router. These models provide the flexibility to execute intricate designs with ease, reducing the need for manual repositioning of parts and increasing production speed.
Look for Automation Features
Automation features, such as tool changers and automatic material handling systems, can significantly boost your CNC router’s efficiency. These systems reduce downtime, allowing the CNC router to operate continuously with minimal operator intervention. Investing in automation can improve both productivity and consistency, making it easier to manage high-volume jobs and complex tasks.
Ensure Software Compatibility
Your CNC router must be compatible with the design software you use for creating CAD/CAM files. A machine that integrates smoothly with your existing software will reduce setup time and the likelihood of errors. Check that the CNC router supports industry-standard formats and integrates with your design tools to facilitate a seamless transition from design to production.
Prioritize Ease of Use and Operator Training
The more user-friendly the CNC router, the less time you’ll spend on training and troubleshooting. Look for a machine that offers an intuitive control interface, easy-to-read displays, and simplified setup processes. A user-friendly machine reduces operator errors and minimizes the learning curve, ensuring smoother operation right from the start.
Check for Durability and Build Quality
Industrial CNC routers operate in harsh environments, so durability is essential. A robust build quality, typically made from high-grade steel or aluminum, will ensure the machine stands up to constant use. Choose a machine that offers both sturdiness and precision, as a well-built CNC router will maintain its performance over time and reduce the likelihood of costly repairs.
Factor in Maintenance Requirements
Industrial CNC routers require regular maintenance to ensure optimal performance. Choose a model with easy-to-maintain parts, such as replaceable bearings, accessible motors, and straightforward lubrication systems. Make sure the machine has clear maintenance guidelines, and consider the availability of spare parts to avoid costly downtime or long service delays.
Set a Realistic Budget
While it’s tempting to invest in the most feature-rich CNC router, your budget plays an essential role in your decision. Assess your business’s needs and choose a CNC router that balances features, performance, and cost. Consider not only the upfront cost but also long-term operational expenses, including maintenance, software updates, and energy consumption, to ensure the machine fits your financial goals.
What Materials Can The Industrial CNC Router Cut
Industrial CNC routers are designed to handle a wide range of materials with precision and efficiency. Whether you’re working with softwoods, hardwoods, plastics, metals, or composite materials, these CNC routers offer versatile capabilities to meet your production needs. From intricate woodworking projects to heavy-duty metal cutting, CNC routers can easily adapt to various materials, providing smooth, accurate cuts for both simple and complex designs. The ability to handle multiple material types makes them an ideal solution for industries such as furniture manufacturing, aerospace, automotive, and signage production, ensuring consistent results and high-quality finishes across diverse applications.
Application Industry
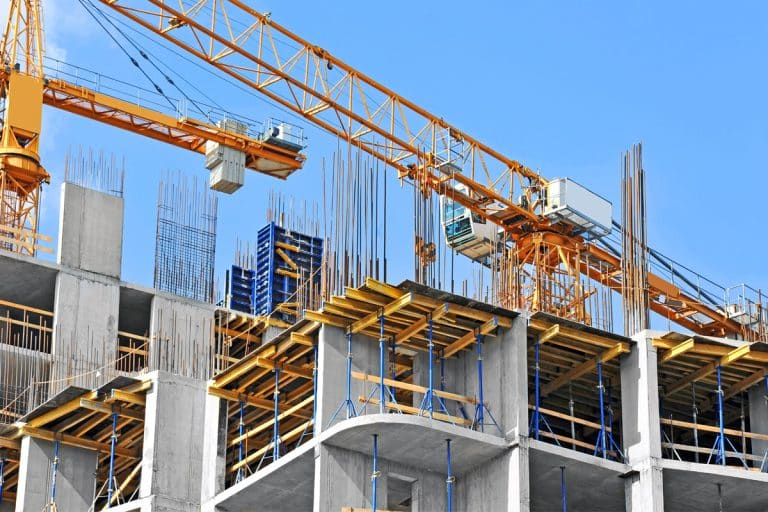
Construction Industry
The integration of CNC routers into construction workflows has ushered in a new era characterized by meticulous detailing, rapid prototyping, and improved material utilization.
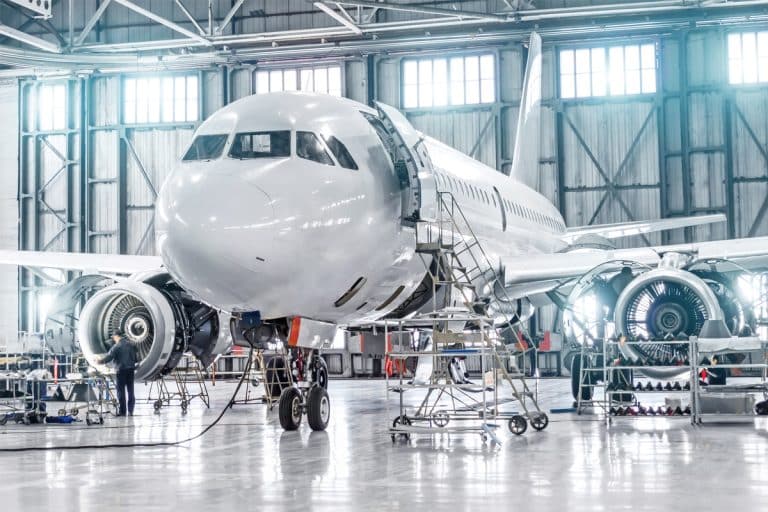
Aerospace Industry
The CNC router is widely used in aerospace engineering due to its unparalleled ability to carve complex designs, manufacture complex parts, and ensure tight tolerances.
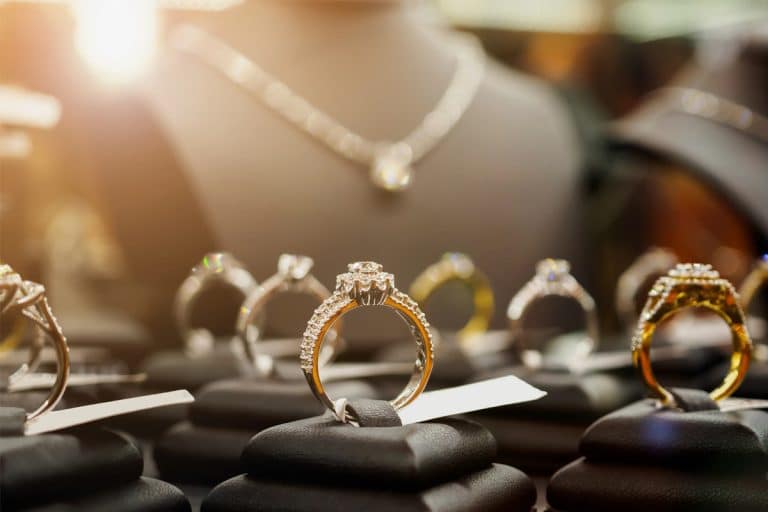
Jewelry Industry
The CNC router revolutionize the way fine jewelry is designed and made by delivering unparalleled precision and efficiency and producing intricate designs with meticulous attention to detail.
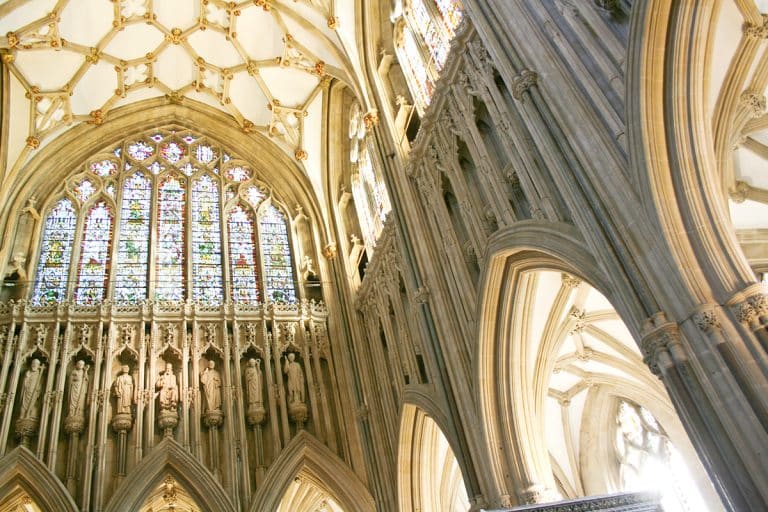
Stone Carving Industry
The integration of CNC routers into the stone carving industry is not only revolutionizing the way craftsmen carve, it is also redefining the boundaries of artistic possibilities in this ancient practice.
Blog
What Power CNC Router Spindle Should I Choose?
In this article, we'll explore how spindle power works, what factors you should consider, and how to choose the right CNC router spindle power based on your materials and application ...
Read More
How to Choose the Right Stone CNC Router for Your Workshop?
This guide will walk you through the key factors to consider when choosing a stone CNC router, designed to help you invest wisely in a machine that delivers reliable performance ...
Read More
Best Budget CNC Router for Making Outdoor Signs?
In this guide, we'll break down the key features to look for, explore different models under a variety of price points, and help you choose the best budget CNC router ...
Read More
How to Maintain and Troubleshoot the ATC CNC Router?
This article will walk you through a practical maintenance procedure for your ATC CNC router and instruct you on how to diagnose and repair common problems that may arise.
Read More
Frequently Asked Questions
What Is The Difference Between Desktop and Industrial CNC Routers?
While both desktop and industrial CNC Routers are used for cutting, shaping, and engraving materials, they differ significantly in terms of size, capability, performance, and intended use. Below are the key differences:
- Size and Build
- Desktop CNC Routers: As the name suggests, these machines are compact and designed to fit into smaller workspaces. They are typically lighter and have smaller cutting areas, making them suitable for hobbyists, small businesses, and low-volume production.
- Industrial CNC Routers: These machines are large, heavy-duty systems designed for high-volume, large-scale production. They offer expansive work surfaces, enabling the processing of large sheets of material and larger, more complex parts.
- Material Compatibility
- Desktop CNC Routers: Desktop models are primarily used for cutting softer materials such as wood, plastics, and foam. While some may be able to handle light metals, their limited power and speed make them less suitable for harder, more durable materials.
- Industrial CNC Routers: Industrial CNC routers are built to handle a wider range of materials, including wood, metal, plastics, composites, and even glass. They can cut through tougher materials like aluminum, steel, and thick composites, thanks to more powerful spindles and robust construction.
- Cutting Speed and Precision
- Desktop CNC Routers: These CNC routers are typically slower and may not achieve the same level of precision as industrial models. They are fine for projects that require lower tolerance and less detail, such as prototypes or small custom items.
- Industrial CNC Routers: Industrial machines are engineered for high-speed and high-precision cutting, offering superior accuracy, tight tolerances, and faster processing times. These machines are used for mass production where speed and consistency are paramount.
- Power and Spindle Capacity
- Desktop CNC Routers: Desktop models have smaller spindles with lower horsepower, limiting their ability to cut thicker materials or make heavy-duty cuts. They are typically designed for light-duty tasks.
- Industrial CNC Routers: These CNC routers come with high-powered spindles and motors, allowing them to cut through thicker and harder materials with greater force. Their power capacity ensures they can handle demanding tasks in production environments.
- Automation and Features
- Desktop CNC Routers: Desktop models usually have basic features, with fewer automation options. They may lack advanced functions like automatic tool changers or material handling systems, which limits their use in large-scale production.
- Industrial CNC Routers: Industrial CNC routers are equipped with advanced automation features, such as automatic tool changers, material loaders, and part-off systems. These features help minimize manual labor, reduce downtime, and increase productivity.
- Cost
- Desktop CNC Routers: Due to their smaller size and simpler features, desktop CNC routers are much more affordable, making them ideal for hobbyists, education, and small-scale businesses with limited budgets.
- Industrial CNC Routers: Industrial models are a significant investment, with costs that can range from tens of thousands to hundreds of thousands of dollars, depending on the complexity and features. However, their high performance, durability, and efficiency justify the cost for large-scale manufacturers.
- Applications
- Desktop CNC Routers: Ideal for small-scale applications such as custom woodworking, prototyping, jewelry making, and light engraving. They are commonly used in education, startups, and DIY projects.
- Industrial CNC Routers: These machines are designed for industries that require heavy-duty, high-volume production, such as aerospace, automotive, furniture manufacturing, signage, and metalworking.
- Maintenance and Longevity
- Desktop CNC Routers: Desktop machines generally require less maintenance but also have a shorter lifespan due to their lighter construction and less durable components.
- Industrial CNC Routers: Industrial CNC routers are built for long-term, continuous use, but they require regular maintenance to keep them in optimal condition. They are designed to withstand the wear and tear of heavy-duty operation over many years.
What Can Industrial CNC Routers Do?
Industrial CNC routers are versatile, high-precision machines designed to automate the process of cutting, shaping, and finishing a wide variety of materials. They are widely used in industries such as woodworking, aerospace, automotive, and signage due to their ability to handle complex tasks with accuracy and speed. Some of the key capabilities of industrial CNC routers include:
- Cutting & Shaping: CNC routers are capable of cutting materials like wood, metal, plastic, and composites into intricate shapes, curves, and patterns with high precision. This makes them ideal for producing everything from custom furniture to industrial parts.
- Engraving & Etching: They can engrave detailed logos, text, and patterns on surfaces, providing high-quality finishes for signs, plaques, and decorative items.
- 3D Milling & Prototyping: With multi-axis capabilities, CNC routers can create three-dimensional objects, enabling the production of prototypes, molds, and complex geometries used in various industries.
- Drilling & Boring: CNC routers can also drill precise holes and slots in materials, ensuring consistency for parts that require exact measurements.
- Edge Finishing: For applications like cabinetry and furniture production, CNC routers offer precise edge finishing, giving products a smooth, professional appearance.
What Industries Are Industrial CNC Routers Used In?
Industrial CNC routers are versatile machines that are used across a wide range of industries due to their precision, efficiency, and ability to handle various materials. Below are some of the primary industries that rely on CNC routers for production:
- Woodworking: CNC routers are widely used in the woodworking industry for tasks such as cabinetry, furniture making, and custom wood designs. They can cut, shape, carve, and engrave wood with high precision, enabling both mass production and custom projects.
- Aerospace: The aerospace industry uses CNC routers to machine lightweight composites, aluminum, and other materials used in aircraft and spacecraft manufacturing. These CNC routers help produce complex, high-precision parts that meet strict industry standards.
- Automotive: CNC routers are essential in automotive manufacturing for creating prototype parts, custom components, and tooling. Their ability to work with metals, plastics, and composites makes them ideal for the precision needed in automotive production.
- Signage: CNC routers are frequently used to create custom signs, letters, and logos from materials like acrylic, wood, and metal. The ability to engrave and cut intricate designs makes them perfect for the signage industry.
- Furniture Manufacturing: In furniture production, CNC routers streamline the creation of detailed designs, precise cuts, and fine finishes. They are used for making everything from decorative inlays to large production runs of furniture components.
- Packaging: In packaging, CNC routers are used to cut and shape materials like cardboard, foam, and plastic. This allows for the creation of custom packaging solutions, including boxes, inserts, and displays.
- Metalworking: CNC routers are also utilized in the metalworking industry to cut, engrave, and machine various metals like aluminum, brass, and steel. They can handle both simple and complex metal fabrication tasks with precision.
- Prototyping & Tooling: The versatility of CNC routers makes them invaluable in prototyping industries. They are used to quickly create models, prototypes, and tooling components for testing and design validation.
- Marine: CNC routers play a role in the marine industry, particularly in the production of boat components, hulls, and custom parts from materials like fiberglass and composite materials.
- Architectural: In architecture, CNC routers are used to carve detailed features in wood, stone, and other materials. They help in the production of decorative elements for buildings, interiors, and custom furniture.
How Much Do Industrial CNC Routers Cost?
The cost of an industrial CNC router can vary significantly, ranging from approximately $10,000 to several hundred thousand dollars. The price depends on several key factors, including the machine’s size, cutting capabilities, brand, and additional features.
- Entry-Level Models: Suitable for smaller or specific applications, entry-level industrial CNC routers typically cost between $6,000 and $15,000. These machines may have more basic features but still provide the precision and functionality required for lighter tasks.
- Mid-Range Models: For those needing a larger cutting area, higher precision, and additional features, mid-range models generally range from $15,000 to $30,000. These CNC routers can handle more complex tasks and are ideal for businesses with moderate production requirements.
- High-End & Specialized Models: Industrial CNC routers equipped with advanced technology, larger work areas, and specialized cutting capabilities can cost $50,000 or more. These CNC routers are designed for heavy-duty applications requiring high precision, speed, and flexibility.
Can The Industrial CNC Router Be Customized to Meet Specific Needs?
Yes, industrial CNC routers can be highly customized to meet specific operational requirements, offering a range of flexible options to adapt to various applications across different industries. Customization is one of the key benefits of industrial CNC routers, allowing businesses to enhance their productivity and precision by tailoring the machine to their unique needs. Here are some common customization options:
- Cutting Area and Size: The cutting area of an industrial CNC router can be customized to accommodate larger or smaller workpieces. Machines can be built with longer, wider, or deeper workbeds, depending on the type of material being processed and the scale of production.
- Material Handling and Automation: Industrial CNC routers can be equipped with additional automation features such as robotic arms, automatic tool changers, and material feeders. These additions help streamline the manufacturing process, reduce manual labor, and improve efficiency for high-volume operations.
- Spindle and Motor Power: The CNC router’s spindle can be customized to provide higher torque and speed, enabling the machine to handle more demanding tasks such as cutting through harder materials (like metals or composites). The motor power can also be upgraded to achieve faster processing speeds and greater precision.
- Tooling Options: Custom tooling setups, such as specialized cutters, drills, and engraving tools, can be designed for specific tasks or materials. This ensures that the machine can produce the desired results with the highest level of quality.
- Control Systems and Software: The CNC control system and software can be tailored to match the specific requirements of your production process. Advanced software features such as 3D modeling, multi-axis control, or custom macros can be integrated to handle more complex tasks.
- Vacuum Tables and Clamping Systems: To hold materials securely during the cutting process, CNC routers can be customized with different vacuum table configurations or clamping systems. These modifications are particularly useful for handling irregularly shaped or delicate materials.
- Dust Collection and Safety Features: For industries dealing with dust-intensive materials (such as wood or plastics), CNC routers can be customized with advanced dust collection systems to maintain a clean and safe work environment. Additionally, safety features like emergency stop buttons, safety covers, and sensors can be added to meet specific regulatory requirements.
- Multi-Axis Capability: Industrial CNC routers can be customized to include multi-axis capabilities, such as 5-axis or 6-axis machining. This allows for more complex geometries, 3D designs, and intricate contours that are not possible with standard 3-axis systems.
What Is The Expected Lifespan of Industrial CNC Routers?
The lifespan of an industrial CNC router can vary significantly depending on several factors, such as the machine’s build quality, maintenance, usage intensity, and the type of materials being processed. On average, industrial CNC routers are designed to last between 10 to 20 years, with many lasting even longer if properly maintained. Here’s a breakdown of the factors that influence their lifespan:
- Build Quality and Manufacturer: The quality of materials used in the construction of the CNC router plays a critical role in its longevity. High-end, industrial-grade CNC routers from well-known manufacturers tend to be built with durable components that can withstand years of heavy use. Cheaper, entry-level models may have a shorter lifespan due to lower-quality parts and design.
- Frequency and Intensity of Use: The more frequently and intensely a CNC router is used, the faster it will experience wear and tear. For instance, a CNC router used for continuous production in a high-demand environment will require more maintenance and may wear out quicker than one used sporadically or for less demanding tasks.
- Maintenance and Care: Regular maintenance is key to extending the life of your CNC router. You need to regularly clean and lubricate moving parts and replace worn tools or parts as needed. Proper maintenance can significantly extend the life of the machine and reduce the likelihood of failure or performance degradation.
- Type of Materials Processed: The types of materials being cut can impact the wear on the CNC router. For example, cutting harder materials like metals or composites can put more strain on the machine’s components compared to softer materials like wood or foam. Specialized machines designed for metalworking or other heavy-duty tasks may experience more wear, but they’re also built to endure this kind of stress.
- Upgrades and Technology Changes: Over time, technological advancements may make older CNC routers less efficient or obsolete. While this doesn’t affect the physical lifespan of the machine, it may influence the decision to replace the equipment. However, many industrial CNC routers allow for upgrades to control systems, motors, and software, which can extend their useful life in terms of performance.
- Environmental Conditions: The operating environment also impacts the lifespan. Machines exposed to excessive moisture, heat, or dust without proper ventilation may experience faster degradation. It is essential to keep the CNC router in a controlled environment where temperature, humidity, and cleanliness are carefully regulated.
What Customer Support Do Industrial CNC Routers Provide?
Industrial CNC routers come with reliable customer support options to ensure smooth operation and user satisfaction:
- Free Online Technical Support: Customers can access complimentary technical assistance through online platforms, including email, chat, or video support. This service is ideal for troubleshooting, software setup, or resolving operational issues remotely.
- Paid On-Site Training: For users requiring hands-on guidance, on-site training sessions are available at an additional cost. These sessions cover installation, operation, and maintenance to ensure optimal use of the machine.
What Is The Warranty Period of Industrial CNC Routers?
Our CNC router is backed by a comprehensive warranty designed to give you peace of mind and protect your investment:
- 3-Year Warranty for the Entire Machine: This full warranty covers any defects or malfunctions in the machine as a whole, ensuring reliable performance and longevity over time.
- 5-Year Warranty for Core Components: Key components essential for optimal machine operation are covered for 1.5 years. This includes parts that may experience wear and tear with regular use, ensuring you have support for the most vital parts of the machine.