Wood CNC Router
Our wood CNC routers are designed to meet the needs of woodworkers, manufacturers, and hobbyists looking for precision, efficiency, and versatility. Whether you’re crafting intricate designs, creating custom furniture, or producing large-scale wood products, our CNC routers deliver the power and accuracy required to elevate your work.
Equipped with advanced technology, these machines offer exceptional detail and consistency, ensuring every cut is perfect. With automated controls, users can easily program and execute complex designs, reducing labor time while increasing production capacity. The CNC routers are compatible with a wide range of materials, from softwoods to hardwoods, plywood, and MDF, making them ideal for a variety of applications, including cabinetry, signage, and decorative woodworking.
Our wood CNC routers are built for long-term reliability, with durable components that withstand the demands of both professional and industrial environments. Whether you’re a small shop looking to streamline operations or a large manufacturer seeking high-volume production, these CNC routers provide a robust solution. Experience the next level of craftsmanship with our state-of-the-art CNC routers, where precision meets performance in every project.
-
AKM1212 CNC Router
Rated 5.00 out of 5$4,400.00 Add to cart -
AKG6090 CNC Router
Rated 5.00 out of 5$3,000.00 Add to cart -
AKG6012 CNC Router
Rated 5.00 out of 5$3,250.00 Add to cart -
AKG1212 CNC Router
Rated 5.00 out of 5$3,800.00 Add to cart -
AKM6090C CNC Router
Rated 5.00 out of 5$6,400.00 Add to cart -
AKM6012C CNC Router
Rated 5.00 out of 5$6,900.00 Add to cart -
AKG1212C CNC Router
$7,200.00 Add to cart
Tips for Choosing the Right Wood CNC Router
Selecting the right wood CNC router is essential for achieving precision, efficiency, and quality in your woodworking projects. Whether you’re a hobbyist, professional, or business owner, choosing a machine that meets your specific needs can greatly impact your workflow and results.
Understand Your Project Needs
Before choosing CNC routers, consider the type of projects you’ll be working on. If you’re focused on large-scale cutting, you need CNC routers with a larger work area. For detailed, intricate designs, a machine with finer precision is essential. Align your CNC router’s capabilities with your project requirements to ensure efficiency and quality.
Consider the Work Area Size
The size of the CNC router’s bed determines the maximum dimensions of the materials you can work with. If you plan to work on large panels or sheets, opt for a larger bed size. For smaller, more intricate projects, a compact machine may suffice and save space in your workshop.
Evaluate Spindle Power
Spindle power directly impacts the cutting speed and material compatibility of your CNC router. A higher spindle horsepower allows you to cut through thicker and denser woods more efficiently. Consider your material types—hardwoods require more power—so choose a spindle that suits the demands of your work.
Assess the Drive System
The type of drive system in your CNC router affects its accuracy and speed. Ball screw systems are ideal for precision and smaller, detailed cuts, while rack-and-pinion systems are better for high-speed performance in larger cuts. Choose a drive system based on the precision needed for your specific applications.
Choose a Router with Reliable Software
The software that comes with your CNC router determines how easily you can integrate designs into your machine. Look for user-friendly software that supports common CAD/CAM programs. This will streamline your design-to-production process and ensure better workflow, reducing the learning curve.
Ensure Robust Build Quality
A CNC router’s build quality affects both its durability and cut quality. Look for a machine with a solid frame made from materials like steel or aluminum to minimize vibrations, which can affect the precision of your cuts. Investing in a well-constructed machine ensures longevity and consistent performance.
Check Customer Support and Training
Good customer support is invaluable when dealing with complex machinery. Choose a CNC router brand that offers responsive technical support, training resources, and easy access to replacement parts. Reliable support ensures that you can address issues quickly and get the most out of your machine.
Understand Maintenance Needs
Different CNC routers have varying maintenance requirements. Consider how much time and effort you’re willing to invest in upkeep. Machines with fewer moving parts and simple lubrication schedules are easier to maintain, while others may require more frequent adjustments or parts replacement to stay in top condition.
Look for Dust Collection Systems
Woodworking generates a lot of dust, which can affect both the quality of your cuts and the longevity of your machine. Look for CNC routers that include built-in dust collection ports or systems. This will keep your workspace clean and prevent dust buildup on the CNC router, improving efficiency and safety.
Prioritize Safety Features
Ensure the CNC router has built-in safety features like emergency stop buttons, protective shields, and automatic shutdown systems. These features help minimize accidents and ensure operator safety during operation. Safety should be a top priority, especially in busy or high-production environments.
Evaluate Speed and Precision Balance
While speed is important for large-volume production, precision is essential for fine woodworking. Look for a machine that offers an optimal balance of both. A fast CNC router can increase efficiency, but a machine that compromises accuracy may lead to costly errors. Prioritize precision if you’re working on intricate or custom designs.
Factor in Your Budget
CNC routers come in a wide range of price points, so it’s important to balance your budget with the features you need. High-end machines may offer advanced features, but they might not be necessary for smaller or less complex jobs. Assess the features that matter most to your business and choose CNC routers that offer the best value.
What Materials Can the Wood CNC Router Cut
The wood CNC router is a versatile tool capable of cutting a wide range of materials beyond just wood. While primarily designed for woodworking, these CNC routers can handle various materials such as MDF, plywood, acrylic, plastic, and even some metals like aluminum. The machine’s precision and power allow it to cut, carve, engrave, and shape materials with exceptional detail and accuracy. This makes it ideal for a variety of applications, from cabinetry and furniture making to signage and decorative pieces. Whether you’re working with softwoods, hardwoods, or composites, CNC routers provide the flexibility to achieve consistent results across multiple material types, enhancing both creative freedom and productivity in your workshop.
Hardwoods
- Oak
- Maple
- Cherry
- Walnut
- Mahogany
- Birch
- Ash
Softwoods
- Pine
- Cedar
- Redwood
- Spruce
- Douglas Fir
Exotic Woods
- Teak
- Rosewood
- Ebony
- Purpleheart
- Zebrawood
Composite Woods
- Plywood
- MDF (Medium-Density Fiberboard)
- Particleboard
- LVL (Laminated veneer lumber)
Application Industry
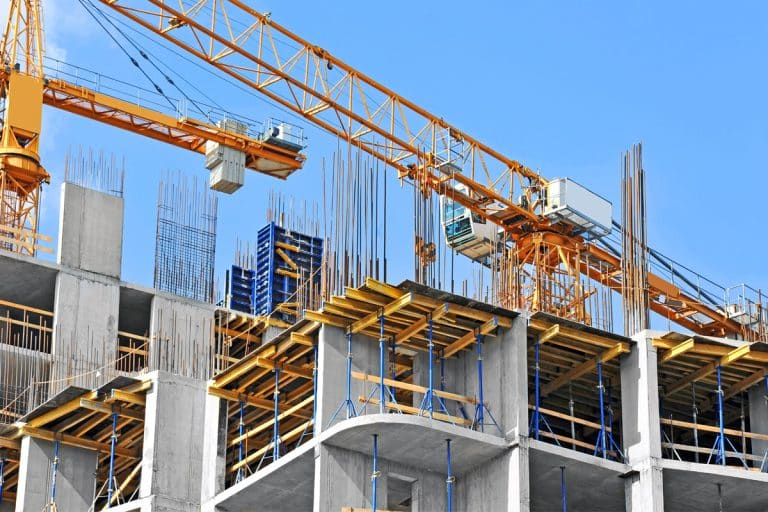
Construction Industry
The integration of CNC routers into construction workflows has ushered in a new era characterized by meticulous detailing, rapid prototyping, and improved material utilization.
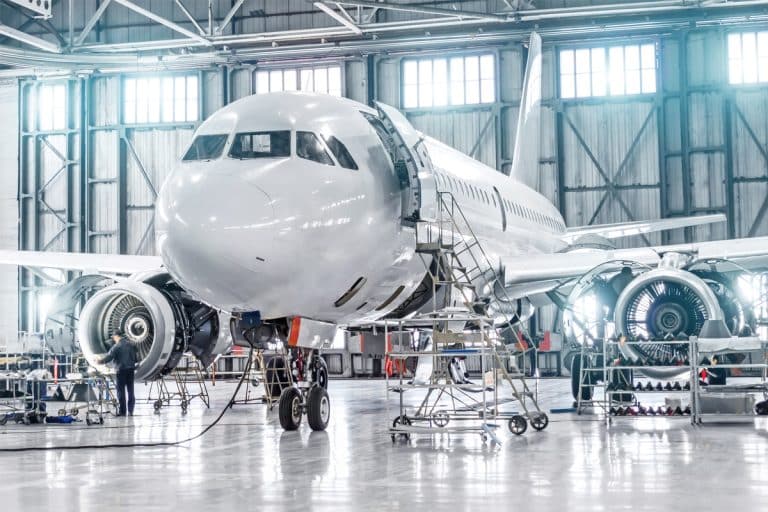
Aerospace Industry
The CNC router is widely used in aerospace engineering due to its unparalleled ability to carve complex designs, manufacture complex parts, and ensure tight tolerances.
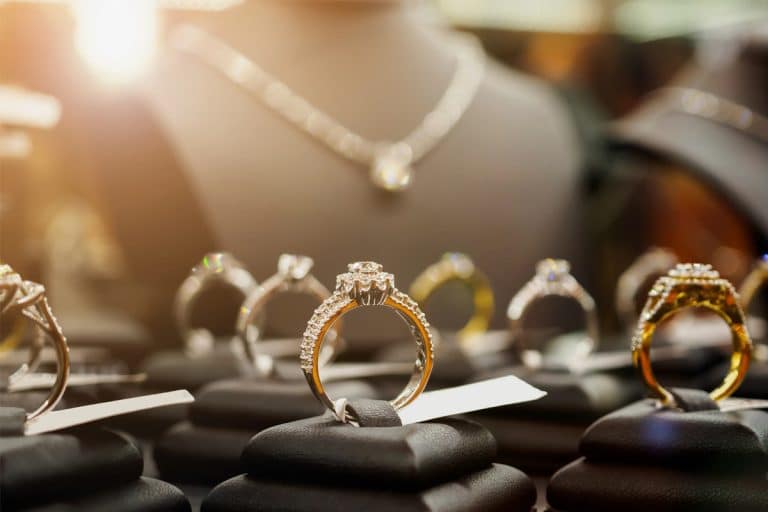
Jewelry Industry
The CNC router revolutionize the way fine jewelry is designed and made by delivering unparalleled precision and efficiency and producing intricate designs with meticulous attention to detail.
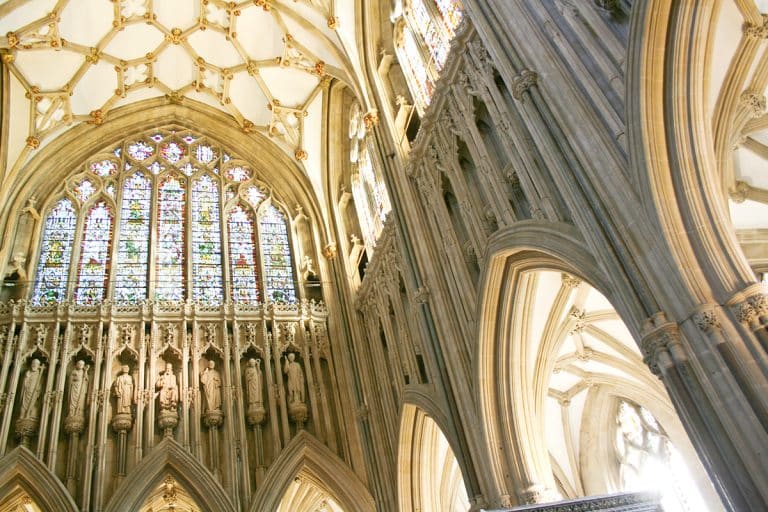
Stone Carving Industry
The integration of CNC routers into the stone carving industry is not only revolutionizing the way craftsmen carve, it is also redefining the boundaries of artistic possibilities in this ancient practice.
Blog
How to Maintain and Troubleshoot the ATC CNC Router?
This article will walk you through a practical maintenance procedure for your ATC CNC router and instruct you on how to diagnose and repair common problems that may arise.
Read More
What Warranties Are Typically Offered on CNC Routers?
In this article, we'll break down the different types of warranties typically offered on CNC routers, what's included, and how to make sure you're getting the support you need long ...
Read More
How to Choose the Right Motor for a CNC Router?
This guide will walk you through the essential factors to consider when selecting a motor for your CNC router, including machine size, workload demands, material types, and control system compatibility.
Read More
Is the Woodworking CNC Router Worth Buying?
In this article, we'll explore a CNC router's key advantages, cost factors, and suitability to help you decide if it's the right tool for your shop or business based on ...
Read More
Frequently Asked Questions
How Do Wood CNC Routers Work?
The wood CNC router is a computer-controlled machine designed to cut, carve, and shape wood and other materials with high precision. The process begins by creating a design in CAD (Computer-Aided Design) software, which can be drawn or imported. This design is then converted into a machine-readable format, such as G-code, that tells the CNC router how to move and cut.
Once the design is prepared, the material—typically wood, MDF, or plywood—is securely placed on the CNC router’s work table. The CNC router’s cutting tool, such as an end mill or router bit, is set up based on the specific task, and the machine is calibrated to ensure precise movements.
Using the instructions from the G-code, the CNC router moves along the X, Y, and Z axes, gradually removing material in controlled passes. The CNC router performs various operations, including cutting, carving, engraving, and drilling, to create the intended design. If necessary, the machine automatically changes tools to complete different tasks.
To maintain a clean workspace, many CNC routers are equipped with dust collection systems, reducing health risks associated with airborne wood dust. The operator monitors the process to ensure the job is completed to specifications. Once finished, the operator removes the completed piece from the machine.
This level of automation and precision makes wood CNC routers invaluable in industries such as cabinetry, furniture making, and sign-making, where intricate and repetitive designs are needed.
What Are Wood CNC Routers Used For?
Wood CNC routers are highly versatile machines that serve a wide range of applications across various industries, offering precision and repeatability in cutting, carving, and shaping wood. Here are some of the most common uses:
- Woodworking: Woodworkers use CNC routers to create detailed cuts, engravings, and custom designs for a variety of projects. These include furniture, cabinetry, decorative woodwork, and ornamental carvings, all with high precision.
- Cabinetry and Millwork: In the cabinetry and millwork industries, CNC routers are employed to cut and shape wood panels for cabinets, doors, moldings, and other custom wood components, ensuring accuracy and consistency.
- Sign Making: The sign-making industry benefits from CNC routers for crafting intricate, customized signs. These machines can cut letters, logos, and 3D designs, adding detailed carvings to wooden signs.
- Furniture Production: CNC routers are crucial in producing custom furniture such as tables, chairs, and shelves. Their ability to create complex designs with high accuracy makes them ideal for the furniture-making process.
- Wood Crafts: Crafters and artisans use CNC routers to create fine wood crafts like decorative boxes, frames, wooden toys, and custom carvings. These machines allow for the execution of detailed and intricate work.
- Wood Carving: CNC routers are perfect for creating detailed wood carvings, including reliefs and sculptures, often used in the art and craft industry to produce decorative items or artistic pieces.
- Musical Instrument Making: Luthiers use CNC routers to carve and shape parts for musical instruments such as guitars and violins. The precision of the CNC router ensures that each piece meets high-quality standards and exact measurements.
- Model Making: CNC routers are commonly used by architects and designers to create scale models of buildings and structures, providing accurate representations for presentations or design validation.
What Are The Types Of Wood CNC Routers?
Wood CNC routers come in various types, each designed for specific tasks and levels of complexity. Below are some of the most common types, each offering unique features to suit different woodworking needs:
- 3-Axis CNC Router: The most basic type, 3-axis CNC routers operate along three axes: X (left and right), Y (front and back), and Z (up and down). These CNC routers are perfect for 2D cutting, engraving, and carving tasks. They’re commonly used in sign-making, cabinetry, and general-purpose woodworking.
- 4-Axis CNC Router: In addition to the standard X, Y, and Z axes, a 4-axis CNC router includes an additional rotary axis (A-axis) that rotates ±90°. This added capability allows for basic 3D cutting, carving, and engraving. It’s ideal for creating decorative patterns and textures and is often used for more detailed woodwork.
- 5-Axis CNC Router: A 5-axis CNC router offers two additional rotary axes (A and B), allowing for even greater precision and the ability to create complex 3D shapes. These CNC routers are often used in industries like aerospace, automotive, and mold-making, where intricate, high-precision designs are essential.
- ATC CNC Router: Equipped with a tool changer, the ATC CNC router automatically swaps cutting tools during a job. This feature reduces downtime and improves efficiency, especially for projects that require multiple tools of different sizes or types. It’s commonly used in high-volume production environments.
- Rotary Axis CNC Router: A rotary axis CNC router includes a dedicated rotary fixture to hold and rotate cylindrical workpieces. This type of CNC router is used for 4th-axis indexing or continuous rotary carving, making it ideal for tasks like engraving or cutting on round objects, such as posts or spindles.
- Multi-Head CNC Router: Multi-head CNC routers feature multiple cutting heads that allow the machine to perform multiple operations simultaneously. This configuration boosts efficiency and is typically used in high-production environments where reducing cycle time is critical, such as in large-scale furniture or cabinetry production.
How Much Do Wood CNC Routers Cost?
The cost of wood CNC routers can vary significantly based on factors such as machine size, capabilities, brand, features, and whether the CNC router is new or used. Here’s an overview of general price ranges to help you get an idea of what to expect:
- Hobbyist or Small Desktop CNC Routers: These compact machines, designed for home use or small-scale projects, typically cost between $500 and $3,000. They are ideal for DIY enthusiasts or hobbyists working on smaller tasks such as sign-making, engraving, or simple carvings.
- Entry-Level CNC Routers: These mid-sized models, suited for small businesses and workshops, generally range from $3,000 to $15,000. They offer more advanced features and can handle medium-sized projects, including basic cabinetry, woodworking, and small-batch production.
- Mid-Range CNC Routers: Machines with larger working areas and enhanced capabilities, such as higher precision and improved automation, usually fall in the range of $15,000 to $40,000. These CNC routers are perfect for established businesses that need to scale up production or work with more complex designs.
- Professional and Industrial CNC Routers: High-end machines equipped with advanced features, including automatic tool changers, multiple axes, and larger workspaces, start at $40,000 and can cost several hundred thousand dollars. These are designed for large-scale operations requiring precision and heavy-duty capabilities, such as in aerospace, automotive, or high-volume furniture production.
What RPM Is Needed For CNC Cutting Wood?
The required RPM (Revolutions Per Minute) for CNC cutting wood depends on several factors, such as the type of wood, the cutting tool being used, and the desired cutting speed. Typically, the RPM range for cutting wood with a CNC router or milling machine is between 12,000 and 24,000 RPM. Here are some general guidelines to help determine the correct RPM:
- Router Bits and End Mills: Standard router bits and end mills for woodcutting usually have recommended RPM ranges indicated on the tool or in the manufacturer’s documentation. It is important to follow these recommendations for safe and efficient cutting.
- Wood Density: Softer woods (e.g., pine, cedar) can be cut at higher RPM values, typically between 18,000 and 24,000 RPM. Harder woods, like oak or maple, generally require lower RPMs in the range of 12,000 to 18,000 RPM.
- Cutting Speed: The cutting speed, typically specified in inches per minute (IPM) or millimeters per minute (mm/min), impacts the RPM. Adjusting the spindle speed to match the cutting speed ensures the proper chip load and cutting quality. Faster cutting speeds often require higher RPMs.
- Tool Diameter: Smaller-diameter tools can operate at higher RPMs, while larger-diameter tools require lower RPMs to achieve the same cutting speed. A proper balance is necessary for achieving optimal results.
- Material Thickness: Thicker wood materials may require slower cutting speeds and lower RPMs to avoid overheating and ensure proper chip evacuation during the cutting process.
What Are The Disadvantages of Wood CNC Routers?
While wood CNC routers are powerful and versatile tools, they come with a few challenges that might not make them suitable for every user or application. Here are the main disadvantages of using wood CNC routers:
- High Initial Cost: CNC routers can be expensive. The cost of the machine itself, along with the software and tools you need, can quickly add up. Smaller, hobbyist models might cost a few thousand dollars, but larger, professional models can cost tens of thousands of dollars. This can be a significant investment, especially for small businesses or hobbyists.
- Complexity in Operation: Using a CNC router requires some training. You need to understand how to set up the machine, create designs, and adjust settings. For beginners, this can be overwhelming, and mistakes can be costly. Even though some models have user-friendly software, it still takes time to learn.
- Space Requirements: CNC routers are large machines that need a lot of space in your workshop. You’ll also need extra space for materials, tools, and finished projects. If you have a small workspace, fitting in a CNC router can be a challenge.
- Ongoing Maintenance and Costs: CNC routers need regular maintenance to keep them working properly. This includes cleaning, lubrication, and replacing worn parts. Over time, the machine may need repairs, which can be costly. Also, you’ll need to replace cutting tools regularly.
- Risk of Breakdowns: Like any machine, CNC routers can break down. If a part fails, it can stop production and cause delays. Fixing the problem might take time and money. For businesses that rely on continuous production, this could lead to financial losses.
- Noise and Vibration: CNC routers can be quite noisy, and the vibrations from the machine can affect cutting accuracy. Workers may need to wear ear protection, and excessive vibrations can cause wear on both the machine and the workpieces.
- Limited Material Compatibility: CNC routers are primarily designed for wood. While some can handle plastics and soft metals, they aren’t ideal for all types of materials. If you plan to work with a wide range of materials, you may need additional machines, which increases costs.
- Power Consumption: CNC routers use a lot of electricity. If you use the machine frequently, this can increase your energy bills. The machine also needs a stable power supply, so a power surge or outage could damage the CNC router or interrupt your work.
- Decreased Craftsmanship: Some traditional woodworkers prefer the hands-on aspect of woodworking. Using a CNC router means less manual work and more automation, which can feel like it takes away from the personal touch of crafting pieces by hand.
- Safety Risks: CNC routers can be dangerous if not used correctly. The spinning tools can cause serious injuries, especially if materials are not secured properly. Proper training and safety gear, like goggles and ear protection, are essential.
What Customer Support Do Wood CNC Routers Provide?
Wood CNC routers come with reliable customer support options to ensure smooth operation and user satisfaction:
- Free Online Technical Support: Customers can access complimentary technical assistance through online platforms, including email, chat, or video support. This service is ideal for troubleshooting, software setup, or resolving operational issues remotely.
- Paid On-Site Training: For users requiring hands-on guidance, on-site training sessions are available at an additional cost. These sessions cover installation, operation, and maintenance to ensure optimal use of the machine.
What Is The Warranty Period of Wood CNC Routers?
Our CNC router is backed by a comprehensive warranty designed to give you peace of mind and protect your investment:
- 3-Year Warranty for the Entire Machine: This full warranty covers any defects or malfunctions in the machine as a whole, ensuring reliable performance and longevity over time.
- 5-Year Warranty for Core Components: Key components essential for optimal machine operation are covered for 1.5 years. This includes parts that may experience wear and tear with regular use, ensuring you have support for the most vital parts of the machine.