Metal CNC Router
Metal CNC routers are cutting-edge machines designed for precision and efficiency in metalworking applications. Engineered to deliver unparalleled accuracy, these CNC routers are ideal for a wide range of industries, including automotive, aerospace, and manufacturing. Combining advanced computer numerical control (CNC) technology with robust mechanical components, metal CNC routers enable users to cut, carve, and shape various metal materials, such as aluminum, steel, and copper, with exceptional precision and minimal human intervention.
With their ability to automate complex machining processes, metal CNC routers reduce production time, increase consistency, and lower labor costs, all while maintaining high-quality results. These machines feature durable, high-performance spindles, versatile tool changers, and customizable work tables, allowing them to handle both intricate designs and large-scale production runs. Whether you’re working on prototypes, custom components, or large-volume production, metal CNC routers provide the flexibility and reliability needed to meet demanding project specifications. The integration of advanced software also ensures seamless operation, making it easier to program intricate designs and achieve desired outcomes with ease. Discover the power and precision of metal CNC routers and elevate your machining capabilities to the next level.
-
AK4040 CNC Router
Rated 5.00 out of 5$4,000.00 Add to cart -
AK6060 CNC Router
Rated 5.00 out of 5$4,200.00 Add to cart -
AK4040H CNC Router
Rated 5.00 out of 5$5,600.00 Add to cart -
AK6060H CNC Router
Rated 5.00 out of 5$6,000.00 Add to cart -
AK4040C CNC Router
Rated 5.00 out of 5$10,500.00 Add to cart -
AK6060C CNC Router
Rated 5.00 out of 5$11,100.00 Add to cart
Tips for Choosing the Right Metal CNC Router
Choosing the right metal CNC router is essential to optimizing your production process, improving precision, and increasing overall efficiency. With numerous options on the market, it’s important to carefully evaluate key factors such as the type of materials you’ll be working with, the size of your projects, and the features that best suit your specific needs.
Know Your Material Requirements
Understanding the types of metals you plan to cut is essential. Whether you’re working with aluminum, steel, or titanium, different CNC routers are better suited for specific materials. Make sure the CNC router you select has the necessary spindle power, torque, and cutting capabilities for your material types.
Evaluate Machine Size and Work Area
Consider the size of your projects and the CNC router’s available workspace. A larger machine may be required for large metal sheets, while a smaller one is more efficient for precise, intricate parts. Ensure that the CNC router’s table dimensions can accommodate the size and number of parts you intend to produce.
Examine Spindle Power and Speed
The spindle’s power determines the machine’s ability to cut through tough materials. For high-efficiency cutting, choose a CNC router with sufficient horsepower. Additionally, ensure the CNC router has variable speed controls, allowing you to adjust for different material types and cutting conditions.
Check for Precision and Accuracy
Accuracy is critical when working with metals, especially for parts requiring tight tolerances. Review the machine’s precision specifications, such as repeatability and dimensional accuracy, to ensure it meets the demands of your specific application.
Consider Software Compatibility
Ensure the CNC router is compatible with the design and programming software you use. Popular CAD/CAM software like AutoCAD, SolidWorks, and Fusion 360 should integrate seamlessly with the CNC router’s control system for optimal operation and ease of programming.
Look for Automation Features
Automation features such as automatic tool changers, material handling systems, and robotic arms can significantly improve efficiency, especially for large production runs. Consider these features if you need to streamline operations and reduce manual intervention.
Assess Build Quality and Durability
A sturdy and durable machine is crucial for long-term reliability, especially when working with metals. Look for CNC routers made from robust materials like steel or cast iron that can withstand heavy-duty use without sacrificing precision or stability.
Consider Drive Mechanisms
The type of drive mechanism impacts the CNC router’s speed, accuracy, and overall performance. Ball screws offer high precision, while rack and pinion systems provide faster movements for larger parts. Evaluate which system fits your cutting needs and budget.
Factor in Maintenance Needs
Maintenance requirements can impact the overall cost and downtime. Choose a machine with easy-to-access parts and simple maintenance routines. Some models come with automatic lubrication systems or self-diagnostic capabilities, reducing the need for manual intervention.
Evaluate Power and Energy Consumption
Metal CNC routers require substantial power to operate effectively. Check the power specifications and ensure your facility can accommodate the machine’s needs. Additionally, consider energy-efficient models to reduce operational costs over time.
Check Warranty and Support
A comprehensive warranty and strong customer support are essential for peace of mind. Ensure the manufacturer provides adequate support, including training, troubleshooting, and part replacements, in case issues arise. A good warranty helps protect your investment and minimize downtime.
Consult Reviews and User Feedback
Before making a purchase, research user reviews and seek advice from others in the industry. Peer feedback can provide insight into the machine’s real-world performance, reliability, and ease of use, helping you make a more informed decision.
What Materials Can the Metal CNC Router Cut
Metal CNC routers are highly versatile machines capable of cutting a wide range of metals with precision and efficiency. These CNC routers can handle materials such as aluminum, steel, stainless steel, copper, brass, titanium, and even specialized alloys. The machine’s ability to work with both soft and hard metals makes it ideal for industries like aerospace, automotive, and manufacturing. Whether you’re cutting thin sheets or thick plates, a metal CNC router can provide the power, speed, and accuracy needed for diverse applications. From intricate details to large-scale parts, these CNC routers deliver exceptional results on virtually any metal, ensuring high-quality finishes and tight tolerances for a variety of machining needs.
- Stainless Steel
- Carbon Steel
- Gold
- Silver
- Aluminum
- Copper
- Platinum
- Brass
- Cast Iron
- High-Speed Steel
- Bronze
- Iron
- Titanium
Application Industry
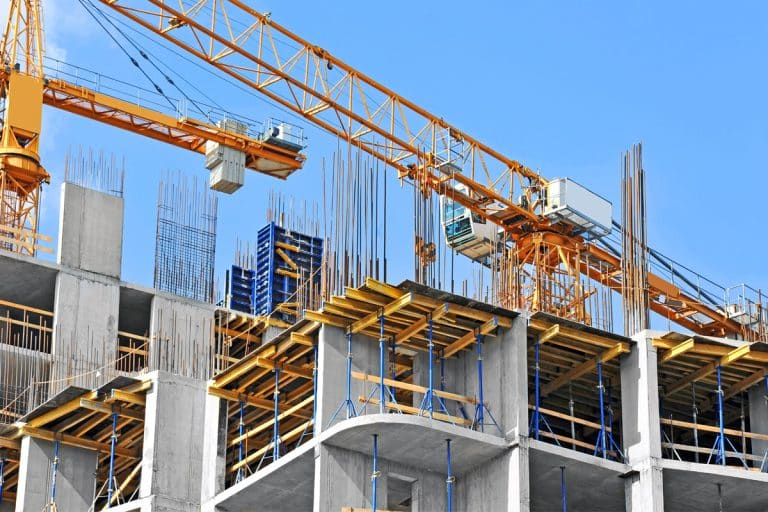
Construction Industry
The integration of CNC routers into construction workflows has ushered in a new era characterized by meticulous detailing, rapid prototyping, and improved material utilization.
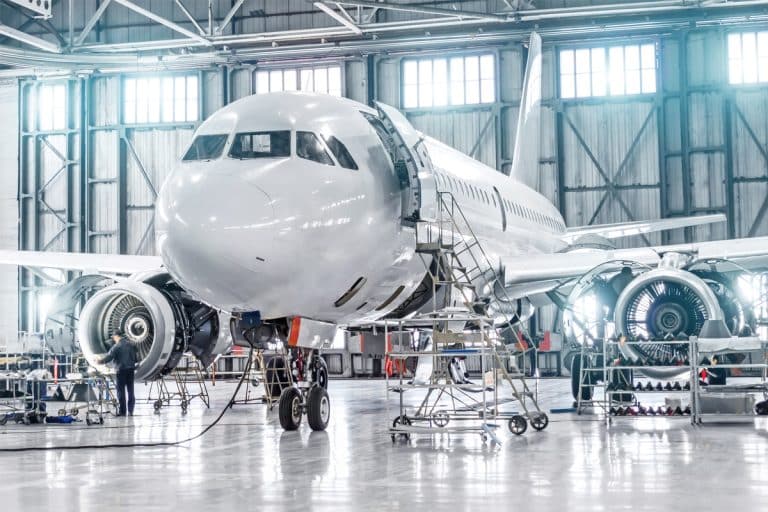
Aerospace Industry
The CNC router is widely used in aerospace engineering due to its unparalleled ability to carve complex designs, manufacture complex parts, and ensure tight tolerances.
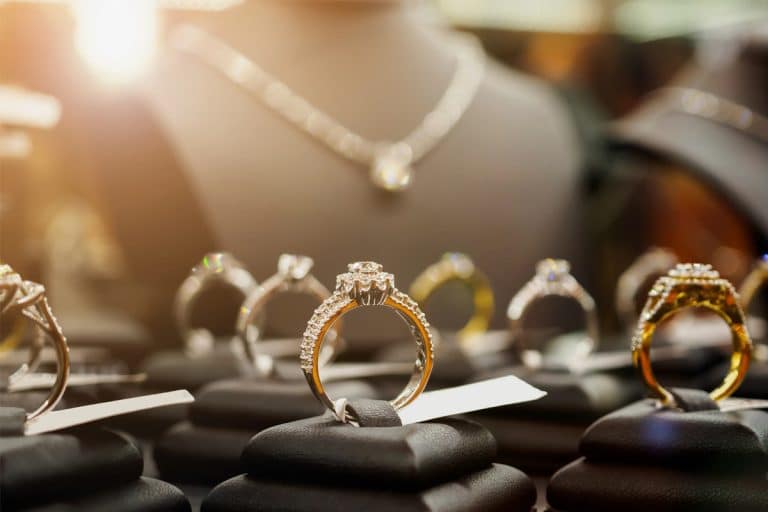
Jewelry Industry
The CNC router revolutionize the way fine jewelry is designed and made by delivering unparalleled precision and efficiency and producing intricate designs with meticulous attention to detail.
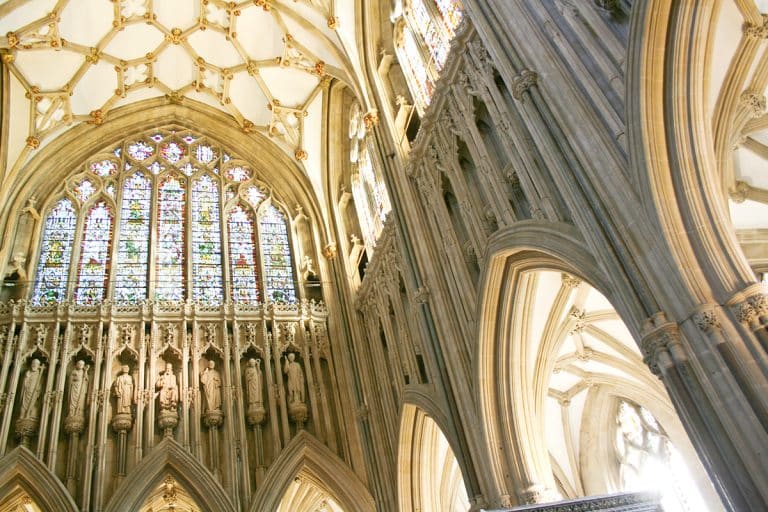
Stone Carving Industry
The integration of CNC routers into the stone carving industry is not only revolutionizing the way craftsmen carve, it is also redefining the boundaries of artistic possibilities in this ancient practice.
Blog
How to Choose the Right Stone CNC Router for Your Workshop?
This guide will walk you through the key factors to consider when choosing a stone CNC router, designed to help you invest wisely in a machine that delivers reliable performance ...
Read More
Best Budget CNC Router for Making Outdoor Signs?
In this guide, we'll break down the key features to look for, explore different models under a variety of price points, and help you choose the best budget CNC router ...
Read More
How to Maintain and Troubleshoot the ATC CNC Router?
This article will walk you through a practical maintenance procedure for your ATC CNC router and instruct you on how to diagnose and repair common problems that may arise.
Read More
What Warranties Are Typically Offered on CNC Routers?
In this article, we'll break down the different types of warranties typically offered on CNC routers, what's included, and how to make sure you're getting the support you need long ...
Read More
Frequently Asked Questions
How Do Metal CNC Routers Work?
Metal CNC routers operate through a combination of advanced computer programming, precise mechanical components, and powerful cutting tools. The process begins by loading a design or blueprint into the CNC (Computer Numerical Control) system, usually created in CAD/CAM software. The CNC router then translates this design into a series of precise movements, controlling the routing machine’s motors, spindle, and cutting tools.
The CNC router’s computer controls guide the movement of the tool along multiple axes—typically X, Y, and Z—enabling the cutting of intricate shapes, holes, and contours in the metal material. The material is securely held in place on the worktable, while the cutting tool, which can vary in size and type depending on the material and design, is driven by the router’s spindle. The spindle rotates at high speeds to efficiently cut through the metal.
By following the pre-programmed instructions, the CNC router ensures consistent, high-precision cuts with minimal human intervention. This allows for high-quality production of complex metal parts, whether for prototyping, custom designs, or large-scale manufacturing runs. The process is automated, reducing errors and increasing efficiency while maintaining high levels of accuracy.
What Industries Are Metal CNC Routers Used In?
Metal CNC routers are utilized across a wide range of industries due to their precision, versatility, and efficiency in metalworking. Some of the key industries that rely on these machines include:
- Aerospace: In the aerospace industry, metal CNC routers are used to produce high-precision parts, such as aircraft components, engine parts, and structural elements. The ability to handle lightweight and strong materials like aluminum and titanium makes these CNC routers essential for aerospace manufacturing.
- Automotive: The automotive industry uses CNC routers for manufacturing intricate parts such as engine components, brackets, and custom automotive trims. The high-speed cutting and precision provided by these CNC routers help in mass production as well as prototype development.
- Manufacturing: Metal CNC routers are a staple in various manufacturing processes, used for creating custom parts, molds, and tooling. They are crucial in industries like heavy equipment, consumer electronics, and machinery production.
- Defense: Military and defense sectors rely on CNC routers for crafting precision parts for defense systems, weapons, and vehicles. The accuracy and durability of the components produced ensure high-performance standards in critical applications.
- Medical Devices: In the medical field, CNC routers are used to create parts for surgical instruments, implants, and devices. The precision required in this industry ensures the safety and functionality of the products.
- Metal Fabrication: For general metal fabrication, CNC routers streamline the production of structural components, sheet metal parts, and other metal structures used in construction, architecture, and more.
How Much Do Metal CNC Routers Cost?
The cost of a metal CNC router varies depending on its size, features, and capabilities. Below is a general price range for different types of metal CNC routers:
- Standard Metal CNC Router: Typically priced between $3,500-4,000, these CNC routers are ideal for smaller projects and lighter materials. They offer precision cutting for basic metalworking tasks, making them suitable for smaller businesses or hobbyists.
- Heavy Metal CNC Router: Ranging from $5,500-6,500, these CNC routers are designed for more demanding tasks, handling thicker and harder metals. They provide enhanced durability and higher performance for larger-scale projects in industries like automotive and aerospace.
- Metal ATC CNC Router: Advanced models with Automatic Tool Changers (ATC) cost between $10,500-12,000. These CNC routers are perfect for high-volume production environments where quick tool changes and continuous operation are required. They are ideal for industries that need precision and efficiency in cutting complex designs and materials.
What Materials Cannot Be Processed Using Metal CNC Routers?
While metal CNC routers are highly effective for a wide range of metalworking applications, certain metals pose challenges or are not suitable for processing with these machines. Below are some metal materials that cannot be processed effectively using metal CNC routers:
- Titanium Alloys (in high thicknesses): Titanium is a strong, lightweight metal used in aerospace and medical applications. However, it is difficult to machine, especially in thicker sections. Metal CNC routers may struggle with the high heat buildup and the wear on cutting tools, making them less ideal for large-scale titanium processing.
- High Carbon Steel: High-carbon steel is incredibly hard, making it challenging to cut with standard CNC routers. It requires specialized tools with enhanced durability and high cutting speeds, which are typically found in machines designed specifically for hard materials.
- Tool Steel (High-Speed Steel, M2, etc.): Tool steels, which are used in the production of cutting tools and dies, are too hard for standard metal CNC routers. The hardness of tool steels can quickly dull cutting tools, leading to reduced efficiency and precision when processed on CNC routers not designed for this purpose.
- Inconel and Other Superalloys: Superalloys such as Inconel, used in high-temperature applications like turbine engines, require specific, high-performance cutting tools and machinery. Metal CNC routers, with their standard tooling and power capabilities, may not effectively process these tough materials.
- Cobalt Alloys: Cobalt-based alloys are known for their strength and heat resistance, typically used in aerospace, medical, and defense industries. These alloys can be extremely difficult to machine using conventional CNC routers, requiring specialized equipment designed to handle high cutting forces and temperatures.
- Lead and Lead Alloys: Lead is a relatively soft material, but it can be hazardous due to its toxic properties. Due to its softness and environmental concerns, it’s typically not processed with metal CNC routers. Lead also generates excess dust, which can pose a risk to both machinery and operators.
- Soft Metals with High Tendency to Warp (e.g., Copper in thin sheets): Copper is highly conductive and malleable, which means it can easily warp or deform when machined. When dealing with thin copper sheets, CNC routers may struggle with maintaining precision due to thermal expansion and the material’s softness.
What Are The Risks of Using Metal CNC Routers?
While metal CNC routers offer precision, efficiency, and versatility, there are several risks associated with their use. Understanding these risks can help in taking necessary precautions to ensure safety and optimal machine performance. Here are some common risks:
- Injury from Moving Parts: The moving components of metal CNC routers, such as the spindle, cutting tools, and axes, pose a risk of injury if operators come into contact with them. Accidental contact with these moving parts can result in cuts, bruises, or more serious injuries. Proper safety training and protective equipment, such as gloves and goggles, are essential.
- Tool Wear and Failure: Metal CNC routers rely on cutting tools that can wear out over time, especially when machining hard metals. If tools are not regularly inspected and replaced, they can fail during operation, causing damage to the machine, loss of precision, or even accidents. Regular maintenance and tool monitoring are crucial to avoid tool-related issues.
- Material Deformation and Warping: Thin or highly flexible metals like copper or aluminum can warp or deform during the cutting process. Inadequate clamping, improper machine settings, or the wrong cutting tools can exacerbate this issue, leading to inaccurate cuts and wasted material. Ensuring proper fixturing and machine calibration is important to prevent deformation.
- Machine Overheating: Extended use or incorrect settings can cause metal CNC routers to overheat, especially when cutting tough materials at high speeds. Overheating can lead to equipment failure, decreased cutting efficiency, and potential hazards like fire or smoke. Proper ventilation, cooling systems, and regular machine checks help mitigate this risk.
- Dust and Debris Hazards: CNC machining produces metal chips, dust, and debris that can pose risks to both operators and the machine. Fine metal particles can be inhaled, causing respiratory issues, or accumulate in the machine, leading to clogging and decreased efficiency. Regular cleaning, dust extraction systems, and proper ventilation are necessary to maintain a safe working environment.
- Electrical Risks: Metal CNC routers are powered by electricity and contain complex wiring systems. Faulty wiring or improper grounding can result in electrical shocks or fire hazards. Routine electrical inspections, proper grounding, and adherence to safety protocols are vital to prevent electrical accidents.
- Software and Programming Errors: CNC routers rely on software to guide the machine’s operations. Mistakes in programming, incorrect toolpaths, or software malfunctions can lead to inaccuracies in cutting or damage to the material. Regular software updates, error checks, and operator training can help prevent these issues.
- Vibration and Noise: Metal CNC routers can generate significant noise and vibrations, especially when cutting through tougher metals. Prolonged exposure to high noise levels can cause hearing damage, while vibrations can lead to inaccuracies in machining. Using proper ear protection and stabilizing the machine can help minimize these risks.
- Tool Changer Malfunctions: Many metal CNC routers, especially those with Automatic Tool Changers (ATC), can experience malfunctions in their tool-changing mechanisms. This can lead to improper tool selection, interrupted operations, and potentially damage the machine or workpiece. Regular maintenance and tool changer inspections are essential to avoid malfunctions.
- Environmental Hazards: The heat and pressure generated during metal machining processes can create hazardous fumes, especially when working with metals like aluminum or steel. Proper ventilation systems, air filters, and protective masks are necessary to avoid exposure to potentially harmful fumes or gases.
What Is The Expected Lifespan of Metal CNC Routers?
The expected lifespan of metal CNC routers depends on various factors, including the quality of the machine, how often it is used, and how well it is maintained. On average, a well-maintained metal CNC router can last anywhere from 10 to 20 years or even longer. However, there are key factors that influence this lifespan:
- Machine Quality and Build: Higher-quality CNC routers made by reputable manufacturers tend to have a longer lifespan. Machines built with robust components, such as high-grade spindles, motors, and precision parts, are more durable and can withstand years of heavy use.
- Frequency of Use: The more frequently a CNC router is used, the more wear and tear it will experience. A machine used daily in high-demand applications will likely require more frequent maintenance and parts replacement, which can affect its overall lifespan. Machines used less often in lighter applications may last longer without significant degradation.
- Maintenance and Upkeep: Regular maintenance is critical for extending the lifespan of any CNC router. Keeping the machine clean, lubricating moving parts, calibrating components, and replacing worn-out tools all contribute to preserving the machine’s functionality. Neglecting maintenance can lead to premature wear, breakdowns, and a shorter lifespan.
- Operating Conditions: The environment in which the CNC router operates also plays a role. Machines used in clean, controlled environments tend to last longer than those exposed to extreme temperatures, humidity, or excessive dust. Proper ventilation and a dust-free workspace help protect the router’s internal components.
- Technological Advancements: As technology advances, older CNC routers may become outdated in terms of software, control systems, and speed. While this doesn’t directly affect the machine’s physical lifespan, it could lead to the decision to upgrade to a more modern machine that offers improved performance and capabilities.
What Customer Support Do Metal CNC Routers Provide?
Metal CNC routers come with reliable customer support options to ensure smooth operation and user satisfaction:
- Free Online Technical Support: Customers can access complimentary technical assistance through online platforms, including email, chat, or video support. This service is ideal for troubleshooting, software setup, or resolving operational issues remotely.
- Paid On-Site Training: For users requiring hands-on guidance, on-site training sessions are available at an additional cost. These sessions cover installation, operation, and maintenance to ensure optimal use of the machine.
What Is The Warranty Period of Metal CNC Routers?
Our CNC router is backed by a comprehensive warranty designed to give you peace of mind and protect your investment:
- 3-Year Warranty for the Entire Machine: This full warranty covers any defects or malfunctions in the machine as a whole, ensuring reliable performance and longevity over time.
- 5-Year Warranty for Core Components: Key components essential for optimal machine operation are covered for 1.5 years. This includes parts that may experience wear and tear with regular use, ensuring you have support for the most vital parts of the machine.