- 8-12 Min Read
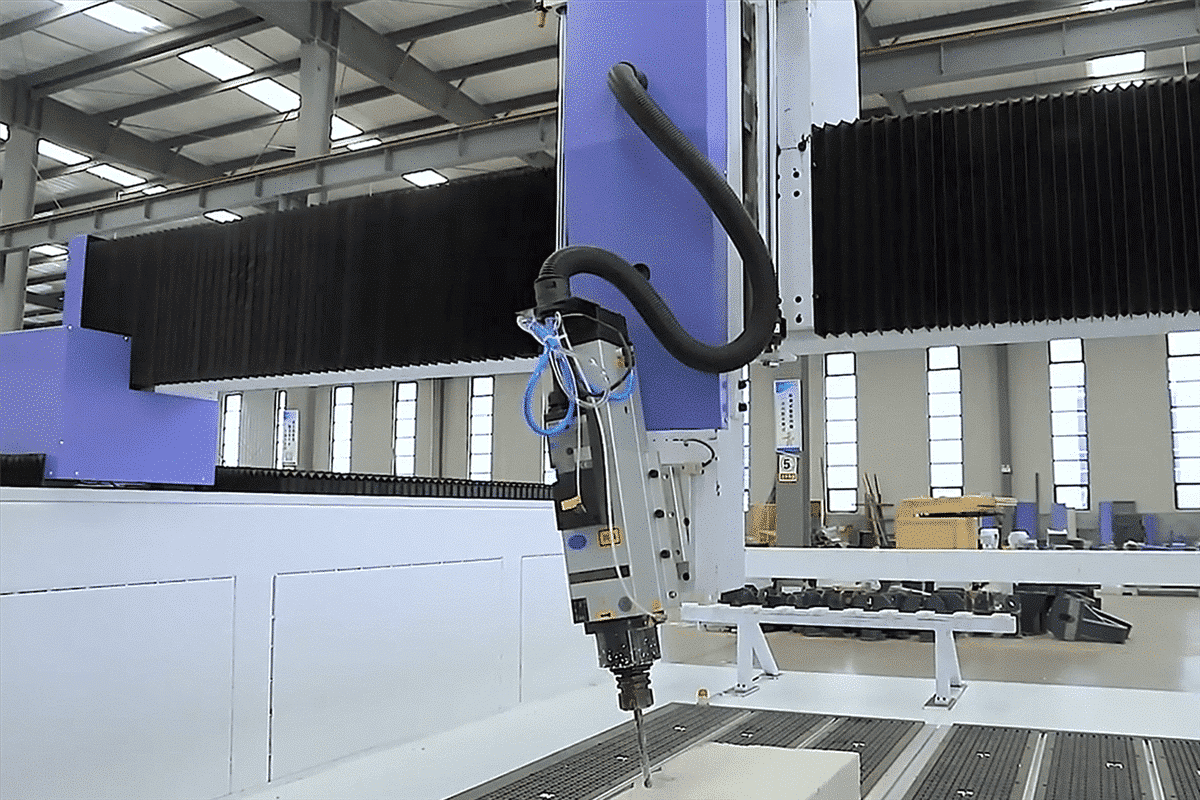
In the ever-evolving landscape of computer numerical control (CNC) machining, router spindles stand as quintessential components, orchestrating precision cutting and carving. Their performance is paramount, dictating the efficiency and accuracy of intricate machining operations. However, the heat generated during operation poses a significant challenge, jeopardizing both performance and longevity. To tackle this challenge, engineers and manufacturers have developed an array of cooling mechanisms tailored to specific spindle designs and applications.
This article delves into the intricacies of cooling mechanisms employed in spindles, aiming to unravel their impact on performance. From traditional air cooling to sophisticated liquid cooling systems, each method carries its unique advantages and limitations, directly influencing the spindle’s thermal stability, precision, and overall performance. By understanding the principles behind these cooling technologies, manufacturers and operators can make informed decisions to optimize spindle functionality, enhance productivity, and prolong operational lifespan.
Effect of Temperature on Spindle Performance
The effects of temperature on the performance of CNC router spindles are multi-faceted and can significantly impact various aspects of their operation.
- Dimensional Accuracy: Temperature fluctuations can cause thermal expansion or contraction of spindle components, leading to deviations in dimensional accuracy. As components expand or contract unevenly, it can result in misalignment or changes in tolerances, ultimately affecting the precision of machined parts.
- Tool Wear and Breakage: Elevated temperatures at the tool-workpiece interface can accelerate tool wear and increase the risk of tool breakage. Heat buildup can soften cutting edges, leading to faster tool degradation and reduced machining quality. Thermal stresses induced by rapid temperature changes may also contribute to tool breakage or chipping.
- Surface Finish: Temperature variations can affect the surface finish of machined parts. Excessive heat can cause material deformation or thermal distortion, leading to rougher surface textures or poor surface quality. Maintaining stable temperatures within the spindle is beneficial for achieving consistent surface finishes across various machining operations.
- Bearing Performance: Bearings are critical components of CNC router spindles, and their performance is sensitive to temperature changes. High temperatures can accelerate bearing wear and lubricant breakdown, leading to reduced operational lifespan and increased friction. Overheating can also cause thermal expansion or distortion of bearing components, compromising their functionality and contributing to premature failure.
- Dynamic Stability: Temperature fluctuations can impact the dynamic stability of CNC router spindles during machining operations. Thermal expansion of spindle components can induce vibrations or chatter, leading to poor surface finish and dimensional inaccuracies in machined parts. Maintaining consistent temperatures helps mitigate dynamic instability and ensures smoother cutting processes.
- Electronics Reliability: Many CNC router spindles incorporate electronic components such as motors, sensors, and control systems. High temperatures can degrade the performance and reliability of these electronics, leading to malfunctions or system failures. Proper thermal management is beneficial to safeguard electronic components and maintain optimal spindle functionality.
- Overall Efficiency: Heat buildup within the spindle can decrease overall machining efficiency. As temperatures rise, thermal energy is dissipated inefficiently, leading to reduced energy transfer and increased power consumption. Cooling mechanisms help dissipate excess heat, improving thermal efficiency and preserving energy resources.
Types of Spindle Cooling Mechanisms
CNC router spindle cooling mechanisms encompass a range of technologies designed to dissipate heat generated during machining operations and maintain optimal operating temperatures. Among the diverse array of cooling solutions available, three primary types stand out: air cooling, liquid cooling, and hybrid cooling systems. Each type offers unique advantages and considerations, shaping the landscape of spindle thermal management in CNC machining. Let’s explore these cooling mechanisms from the perspectives of air cooling, liquid cooling, and hybrid systems.
Air Cooling System
The principle behind CNC router air cooling system spindles revolves around convective heat transfer, where heat is removed from the spindle assembly through the circulation of ambient air. Fans or blowers mounted on the spindle assembly facilitate airflow, drawing in cool air and expelling hot air to dissipate heat generated during machining operations. As the airflow passes over heat-generating components such as the motor and bearings, heat is transferred to the surrounding air and carried away, helping to maintain stable operating temperatures within the spindle assembly.
Advantages
- Cost-Effectiveness: Air cooling systems are generally more cost-effective to implement and maintain compared to liquid cooling alternatives. They require minimal infrastructure and can be easily integrated into existing CNC router setups without significant modifications.
- Simplicity and Reliability: Air cooling systems are relatively simple in design and operation, relying on basic components such as fans or blowers to generate airflow. This simplicity often translates to greater reliability and reduced risk of system malfunctions, contributing to uninterrupted machining operations.
- Suitability for Various Environments: Air cooling systems are well-suited for a wide range of machining environments, including industrial settings with varying ambient temperatures and humidity levels. They are less susceptible to environmental factors compared to liquid cooling systems, making them versatile and adaptable to different operating conditions.
Limitations
- Limited Cooling Efficiency: Air cooling systems may have limited cooling efficiency, especially in high-temperature environments or under heavy machining loads. The convective heat transfer process is inherently less efficient than liquid cooling methods, resulting in slower heat dissipation and potentially higher operating temperatures.
- Inconsistent Cooling: Air cooling systems may struggle to provide consistent cooling across all components within the spindle assembly. Components located further from the airflow source may experience higher temperatures, leading to uneven thermal distribution and potential performance degradation.
- Reduced Thermal Capacity: Air cooling systems may have a reduced thermal capacity compared to liquid cooling alternatives, limiting their ability to handle high-power spindles or prolonged machining tasks that generate significant heat. In such cases, additional cooling measures or periodic cooldown periods may be necessary to prevent overheating and maintain spindle performance.
Liquid Cooling System
The principle behind the CNC router liquid cooling system spindle revolves around the circulation of coolant fluids, typically water or specialized cooling liquids, to absorb and carry away heat from the spindle assembly. A closed-loop circuit is established, comprising a coolant pump, heat exchanger, and coolant reservoir. As the spindle operates, heat is transferred from the heat-generating components to the coolant fluid, which then flows through the heat exchanger to dissipate heat before returning to the spindle assembly. This continuous flow of coolant helps maintain stable operating temperatures within the spindle, enhancing thermal stability and minimizing the risk of thermal-induced distortions or component failures.
Advantages
- Superior Thermal Efficiency: CNC router liquid cooling systems offer superior thermal efficiency compared to air cooling mechanisms. The high specific heat capacity of liquid coolant allows for efficient heat absorption and dissipation, ensuring rapid cooling of the spindle assembly.
- Precise Temperature Control: Liquid cooling systems enable precise temperature control, allowing operators to maintain stable operating temperatures within tight tolerances. This level of temperature control is beneficial for achieving consistent machining performance and optimizing tool life.
- Enhanced Spindle Performance: By effectively dissipating heat, liquid cooling systems help prevent thermal-induced distortions and minimize the thermal expansion of spindle components. This enhances spindle performance, resulting in improved machining accuracy, surface finish, and dimensional stability of machined parts.
- Quiet Operation: Compared to air-cooled spindles, liquid-cooled spindles typically operate more quietly. The absence of noisy fans or blowers contributes to a quieter working environment, which can be advantageous in settings where noise levels need to be minimized.
Limitations
- Complex Installation and Maintenance: Liquid cooling systems require additional components such as pumps, heat exchangers, and coolant reservoirs, which can increase system complexity and installation requirements. Regular maintenance is also necessary to ensure proper functioning and prevent coolant contamination or system leaks.
- Risk of Coolant Leakage: The use of liquid coolant introduces the risk of coolant leakage, which can lead to damage to the spindle or surrounding machinery if not promptly addressed.
- Higher Initial Cost: CNC router liquid cooling systems typically incur higher initial costs compared to air cooling mechanisms due to the need for additional components and infrastructure.
Hybrid Cooling System
The principle behind the CNC router hybrid cooling system spindle is to optimize thermal management by strategically integrating air and liquid cooling technologies. Typically, air cooling is employed for certain components, such as the spindle motor and bearings, while liquid cooling is utilized for critical areas like the tool interface or other heat-sensitive components. This hybrid approach allows for precise temperature control and efficient heat dissipation, enhancing spindle performance and reliability during machining operations.
Advantages
- Enhanced Thermal Efficiency: By combining air and liquid cooling, hybrid systems offer superior thermal efficiency compared to individual cooling methods. Liquid cooling provides rapid heat dissipation and precise temperature control, while air cooling helps to maintain stable temperatures for essential spindle components.
- Customization and Flexibility: Hybrid cooling systems offer flexibility and customization options to meet the specific requirements of different machining applications. Operators can tailor the cooling configuration based on factors such as spindle power, machining environment, and heat generation characteristics, optimizing thermal management for optimal performance.
- Improved Reliability: The hybrid cooling approach helps to minimize the risk of overheating and thermal-induced failures in CNC router spindles. By distributing cooling resources strategically, hybrid systems can maintain stable operating temperatures, prolonging spindle lifespan and reducing the likelihood of downtime due to thermal issues.
Limitations
- Complexity and Cost: Implementing a hybrid cooling system requires additional components and integration efforts, which can increase system complexity and cost compared to standalone cooling methods. The installation, maintenance, and troubleshooting of hybrid systems may also require specialized expertise, adding to operational overhead.
- Maintenance Requirements: Hybrid cooling systems may have more demanding maintenance requirements compared to single cooling methods.
- Space and Packaging Constraints: Integrating multiple cooling technologies into a hybrid system may pose challenges in terms of space and packaging constraints, especially in compact CNC router designs. Careful consideration of system layout and component placement is necessary to maximize cooling efficiency while minimizing space requirements.
How to choose the right spindle cooling mechanism
Selecting the right spindle cooling mechanism for a CNC router is a critical decision that directly impacts machining performance, precision, and efficiency. To make an informed choice, several key factors must be carefully considered. Here, we introduce the essential factors to bear in mind when selecting an appropriate spindle cooling mechanism:
- Application Requirements: Start by thoroughly understanding the specific requirements of your machining application. Consider factors such as the type of materials being machined (e.g., wood, metal, plastics), the complexity of machining operations (e.g., roughing, finishing, engraving), and the desired precision and surface finish of machined parts. Determine the spindle power, speed, and torque requirements based on the material properties, cutting parameters, and production demands of your application.
- Material Compatibility: Consider the thermal properties and heat sensitivity of the materials being machined. Certain materials may be more prone to heat-related issues such as thermal distortion, melting, or degradation. Choose a cooling mechanism that is compatible with the materials being processed. For example, liquid cooling may be more suitable for heat-sensitive materials, while air cooling may suffice for less demanding applications.
- Accuracy and Performance Requirements: Define the required level of machining accuracy and performance for your application. Consider factors such as dimensional tolerances, surface finish requirements, and machining speed and efficiency. Choose a cooling mechanism that can maintain stable operating temperatures and minimize thermal variations to ensure consistent machining accuracy and performance.
- Space and Installation Requirements: Consider the physical space available for installing the cooling system within the CNC router setup. Evaluate the space requirements and installation considerations for different cooling mechanisms, taking into account factors such as system size, component placement, and compatibility with existing machine configurations.
- Environmental Factors: Take into account the environmental conditions in which the CNC router will operate. Factors such as ambient temperature, humidity levels, and the presence of contaminants can influence the effectiveness of cooling mechanisms. Choose a cooling solution that can maintain stable temperatures and withstand the environmental challenges of your machining environment.
- Energy Efficiency: Assess the energy efficiency of different cooling mechanisms to minimize operational costs and reduce environmental impact. Look for systems that optimize energy usage and minimize heat dissipation to achieve efficient spindle cooling.
- Maintenance Requirements: Prioritize reliability and ease of maintenance when selecting a cooling mechanism. Choose a system that is robust, durable, and easy to maintain to minimize downtime and ensure consistent performance over the lifespan of the CNC router.
- Ease of Troubleshooting: Consider the ease of troubleshooting and diagnosing issues with each cooling mechanism to minimize downtime and maintain productivity. Look for systems with built-in diagnostic features, such as fault indicators or error codes, that facilitate quick identification of problems.
- Cost and Budget: Assess the cost implications of different cooling mechanisms, including initial investment, installation costs, and ongoing maintenance expenses. Consider your budget constraints and weigh the upfront costs against long-term performance and reliability benefits. Remember that while some cooling systems may have higher initial costs, they may offer greater efficiency and longevity over time.
- Seek Expert Advice: Consult with CNC machine manufacturers, cooling system suppliers, or industry experts to gain insights and recommendations tailored to your specific application requirements. They can provide valuable guidance on choosing the right cooling mechanism based on their expertise and experience in the field.
Summarize
As CNC machining technologies continue to evolve, spindle cooling mechanisms will remain a critical aspect of enhancing productivity, minimizing downtime, and maximizing return on investment. By leveraging advanced cooling technologies and implementing proactive maintenance practices, CNC router operators can unlock the full potential of spindle cooling systems and redefine the boundaries of machining excellence. In this dynamic landscape, the pursuit of optimal spindle cooling solutions remains an ongoing journey towards achieving precision, efficiency, and competitiveness in CNC machining.
At AccTek CNC, we pride ourselves on offering a diverse range of industrial CNC routers tailored to meet the unique needs of our customers. Our spindle systems feature various power ranges and cooling mechanisms, ensuring versatility and performance across a wide spectrum of machining applications. If you’re unsure about which spindle cooling mechanism is best suited for your needs, don’t hesitate to reach out to us. Our experienced and professional sales team is here to assist you every step of the way.