A Guide to Selecting the Right ATC CNC Router for Your Needs
- 7-10 Min Read
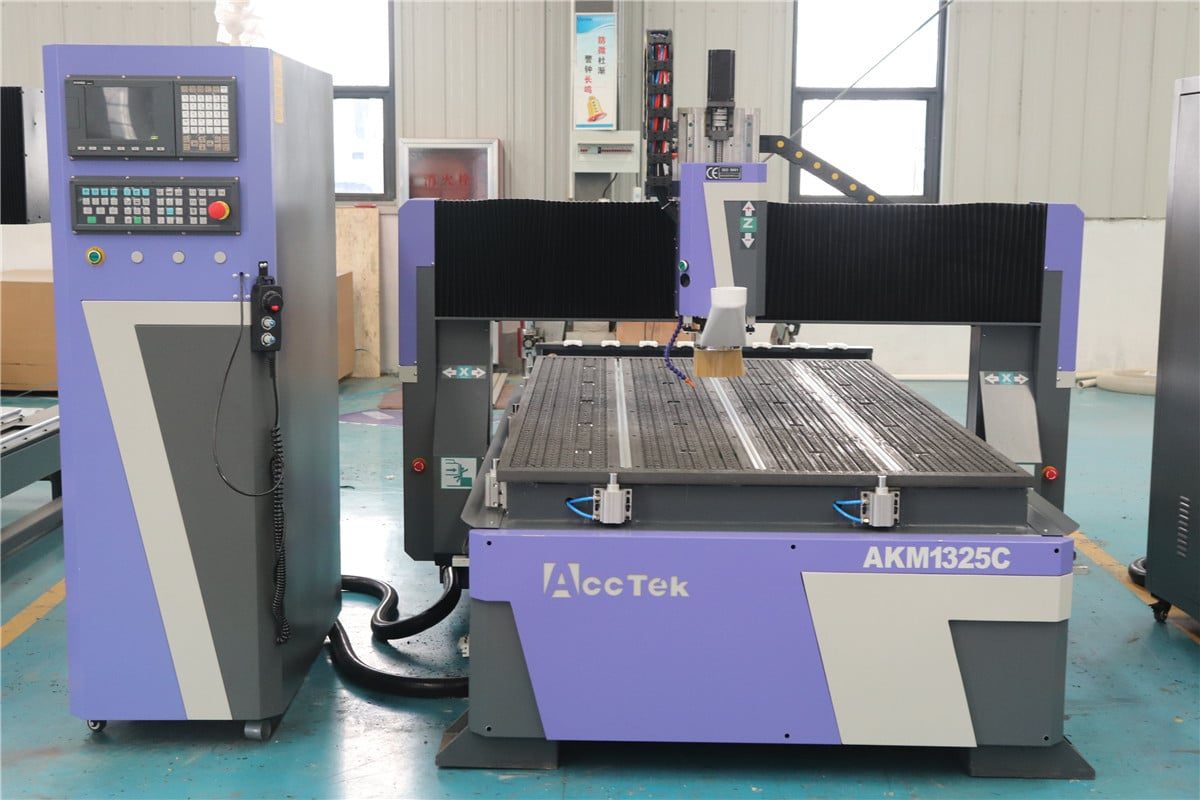
In the ever-evolving landscape of manufacturing and woodworking, Computer Numerical Control (CNC) routers have emerged as indispensable tools, offering precision, efficiency, and versatility. Among these, Automatic Tool Changer (ATC) CNC routers stand out for their ability to streamline production processes by swiftly changing cutting tools, minimizing downtime, and maximizing productivity. Choosing the right ATC CNC router can be a daunting task, given the myriad of options available in the market today. Factors such as budget, intended use, technical specifications, and after-sales support all play key roles in determining which machine best suits your needs.
In this comprehensive guide, we aim to analyze the process of selecting the ideal ATC CNC router for your unique needs. From understanding the significance of ATC in CNC routers to evaluating critical factors such as spindle power, tool capacity, and software compatibility, we will equip you with the knowledge and insights necessary to make an informed decision. Whether you’re a seasoned professional looking to upgrade your workshop or a newcomer eager to delve into the world of CNC machining, this guide will serve as your manual, guiding you through the intricate landscape of ATC CNC routers.
The Significance of ATC on CNC Router
ATC has many advantages in the field of CNC routing, which can significantly improve efficiency, accuracy, and productivity. From minimizing downtime and maximizing uptime to ensuring consistent tool alignment and reducing human error, the advantages of ATC extend far beyond mere convenience. The significance of ATC on CNC routers can be understood through several key points:
- Increased Productivity: Traditional CNC routers require manual tool changes, which interrupt the machining process, leading to downtime and decreased productivity. ATC CNC routers automate this process, enabling seamless tool changes within seconds, thereby maximizing uptime and ensuring a continuous workflow. This leads to increased productivity as jobs can be completed faster with fewer interruptions.
- Versatility: ATC CNC routers can accommodate multiple cutting tools simultaneously, ranging from end mills and drills to router bits and engraving tools. This versatility allows users to execute complex machining operations with ease, such as intricate carving, precise drilling, and detailed engraving, without the need for manual intervention.
- Precision and Accuracy: By eliminating the need for manual tool changes, ATC CNC routers reduce the risk of human error, ensuring consistent and precise machining results. The automated tool change mechanism maintains optimal tool alignment and eliminates discrepancies between tool changes, resulting in higher accuracy and repeatability in finished products.
- Improved Workpiece Quality: The precision and consistency provided by ATC systems contribute to improved workpiece quality. With accurate tool changes and optimal tool alignments, ATC CNC routers produce smoother surfaces, sharper edges, and finer details in finished products.
- Time Savings: Compared to manual methods, ATC CNC routers minimize setup time and tool changeover time, accelerating production cycles and enabling users to meet tight deadlines without compromising on quality. The rapid tool change capability of ATC CNC routers translates into significant time savings over the course of a project, enhancing overall operational efficiency.
- Reduced Labor Costs: By automating the tool change process, ATC CNC routers reduce the reliance on manual labor for tool setup and changeover. This not only frees up personnel to focus on other tasks but also minimizes labor costs associated with manual machining operations, making ATC CNC routers a cost-effective solution for businesses of all sizes.
- Enhanced Flexibility: With the ability to store multiple tools in the tool magazine, ATC CNC routers offer enhanced flexibility in tool selection and machining strategies. Users can easily switch between different tools and cutting profiles during a job without the need for manual adjustments, allowing for greater adaptability to changing project requirements and design specifications.
The significance of ATC on CNC routers lies in its ability to optimize efficiency, enhance precision, reduce costs, and improve overall performance in a wide range of machining applications. Whether in a small-scale workshop or a large-scale manufacturing facility, ATC CNC routers empower users to unleash their creativity and achieve unparalleled efficiency in CNC machining applications.
Factors to consider when choosing ATC CNC router
Choosing the right ATC CNC router involves considering several factors to ensure that the machine meets your specific needs and requirements. This pivotal decision involves a thorough evaluation of various aspects to guarantee optimal performance and efficiency in your machining operations. Here are the key factors to consider:
Understand The Needs
- Material and Application Requirements: Begin by identifying the types of materials you’ll be machining, such as wood, plastic, metal, or composites. Different materials require different cutting speeds, spindle powers, and tooling options. Consider the specific applications you’ll be undertaking, whether it’s basic profiling, intricate carving, 3D machining, or engraving. This will help determine the level of precision and versatility needed from the CNC router.
- Production Volume: Determine whether you’ll be using the CNC router for small-scale projects or large-scale production runs. Choose a machine with appropriate size, speed, and tool capacity to match your production volume. Assess the typical batch sizes of your projects and the frequency of job changes. A fast and reliable ATC system becomes more beneficial for high-volume production with frequent tool changes.
- Speed Requirements: Determine the desired cutting speeds and feed rates based on the materials and cutting depths involved in your projects. Choose a CNC router with a powerful spindle and high-speed machining capabilities to achieve optimal efficiency. Calculate the expected cycle times for your projects and ensure that the CNC router can meet your production deadlines without compromising on quality.
Machine Specifications
- Spindle Power: The spindle power of a CNC router directly impacts its cutting capabilities and efficiency. Evaluate the spindle power based on the materials you’ll be machining and the desired cutting capabilities. Higher spindle power enables faster material removal rates and the ability to handle tougher materials effectively.
- Spindle Speed Range: Consider the spindle speed range offered by the CNC router. A wider range allows for greater flexibility in selecting cutting speeds to optimize performance for different materials and cutting operations.
- Working Size: The working size, or the dimensions of the machine’s work area, is a critical consideration. Assess the size of the workpieces you’ll be machining and ensure that the CNC router’s working size can accommodate them comfortably. Additionally, consider the space available in your workshop or production facility to determine the maximum footprint the machine can occupy.
- Tool Capacity: The tool capacity of an ATC CNC router refers to the number of tools it can hold in its tool magazine or carousel. Evaluate the variety of cutting tools you’ll need for your applications, such as end mills, drills, and engraving bits, and ensure that the machine’s tool capacity meets your requirements. A higher tool capacity allows for greater versatility and flexibility in machining operations.
- Tool Changing Methods: The method used for tool changing significantly impacts the efficiency and productivity of the milling process. Common tool changing methods include linear ATC and disc ATC. Linear ATC systems are generally less expensive, while disc ATC systems can offer high tool capacities. When choosing an ATC CNC router, please consider which factors are your priorities.
Software Compatibility and Control Systems
- Compatibility with CAM Software: Evaluate the compatibility of the CNC router with Computer-Aided Manufacturing (CAM) software. Ensure that theCNC router supports common file formats (e.g., DXF, DWG, STL) and can seamlessly import toolpaths generated by your preferred CAM software.
- User-Friendly Interface: Assess the user interface (UI) of the CNC router’s control system. Look for an intuitive and easy-to-navigate interface that allows for straightforward setup, programming, and operation.
Construction and Build Quality
- Rigidity and Structure: Evaluate the rigidity and stability of the CNC router’s structure. A robust frame and gantry construction are beneficial for maintaining accuracy and precision during machining operations.
- Drive System: Assess the type of drive system employed by the CNC router, such as ball screws, rack and pinion, or linear guides. Consider the performance characteristics of the drive system, including backlash, positioning accuracy, and repeatability. A high-quality drive system is beneficial for achieving precise and consistent results in machining.
Automation and Efficiency
- Tool Changing Speed and Accuracy: Assess the speed and accuracy of the ATC system in changing tools. Consider factors such as tool change time, tool-to-tool change repeatability, and the reliability of the tool clamping mechanism. These factors directly impact the efficiency and precision of machining operations.
- Dust Removal System: Evaluate the effectiveness of the dust removal system integrated into the CNC router. Consider the type of dust collection system employed, such as vacuum-based systems or dust shrouds with integrated extraction ports. Ensure that the dust removal system can effectively capture dust and debris generated during machining operations.
- Tool Setter and Measurement: Assess the presence of a tool setter and measurement system on the CNC router. A tool setter allows for automatic tool length measurement and tool offset calibration, streamlining the setup process and ensuring accurate machining results.
Support and Service
- After-Sales Support: Evaluate the quality of after-sales support provided by the manufacturer or distributor. Ensure that they offer timely technical assistance, troubleshooting, and maintenance services to address any issues that may arise during machine operation.
- Warranty Coverage: Check the warranty coverage offered for the CNC router, including the duration and extent of coverage for parts and labor. A comprehensive warranty provides peace of mind and protection against unexpected repair costs.
- Reviews and References: Seek out reviews and references from other users or industry professionals who have experience with the specific ATC CNC router you’re considering. User reviews can provide valuable insights into the machine’s performance, reliability, and overall satisfaction.
Consider Costs and Budget
- Initial Investment: Assess the initial investment required for purchasing the ATC CNC router, taking into account the machine’s specifications, features, and capabilities. Compare prices from multiple manufacturers or distributors to ensure that you’re getting the best value for your investment.
- Long-Term Costs: Evaluate the long-term costs associated with owning and operating the ATC CNC router. Consider factors such as maintenance expenses, tooling costs, energy consumption, and potential downtime for repairs or upgrades.
Other Factors
- Environmental Considerations: Assess the energy efficiency of the CNC router, including its power consumption during operation. Choose a machine that minimizes energy usage to reduce environmental impact and operating costs.
- Future Expansion and Upgrades: Assess the modularity and scalability of the CNC router, including its compatibility with future upgrades and expansions. Choose a machine that allows for easy integration of additional features, accessories, and capabilities as your needs evolve.
Summarize
Selecting the right Auto Tool Change CNC router is a pivotal decision that can significantly impact the success of your machining endeavors. With the right machine at your disposal, you can unlock a world of precision, productivity, and endless possibilities in CNC machining. In this comprehensive guide, we’ve explored a multitude of factors to consider. By following the steps outlined in this guide and taking a systematic approach to the selection process, you can ensure that the ATC CNC router you choose aligns perfectly with your specific requirements and sets you up for success in your machining endeavors.
When it comes to selecting the right Auto Tool Change CNC router for your machining needs, AccTek CNC stands out as a reliable and versatile choice. We offer users a diverse range of ATC CNC routers, including both linear ATC systems and disc ATC systems, catering to various machining requirements. The tool magazine is capable of holding up to 12 tools, these CNC routers offer versatility and flexibility for a wide range of applications, from basic profiling to intricate carving and 3D machining. Whether you’re a hobbyist, a small business owner, or a large-scale manufacturer, AccTek CNC has the right ATC CNC router to take your machining capabilities to the next level.