- 7-10 Min Read
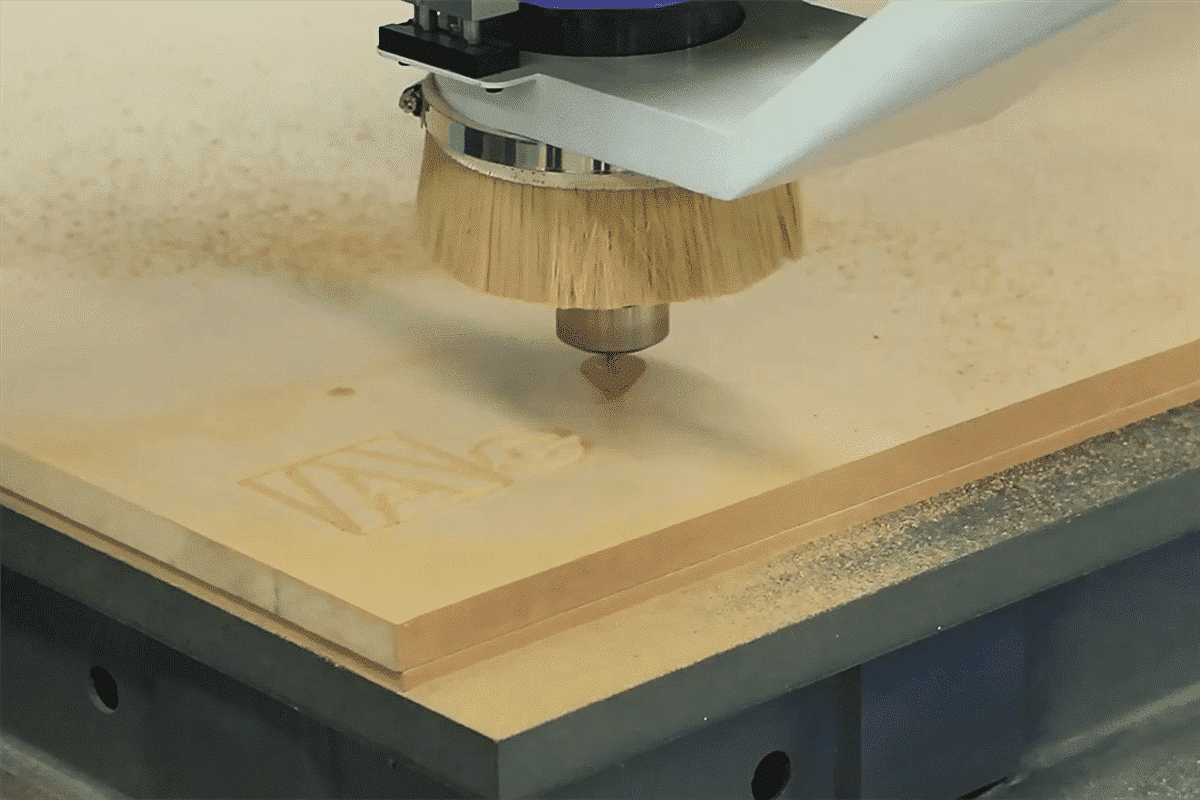
In the realm of modern manufacturing, efficiency is the cornerstone of success. CNC routers have revolutionized the manufacturing industry, offering unparalleled precision and versatility. Whether you’re a seasoned professional or a newcomer to the world of computer numerical control (CNC) machining, one universal goal remains: to optimize the speed and productivity of your operations. However, maximizing their machining speed without compromising quality requires a strategic approach. From fine-tuning toolpath parameters to implementing advanced technologies, there are various tactics at your disposal to enhance efficiency and throughput.
In this article, we delve into the realm of CNC router machining speed, exploring various strategies and techniques to enhance efficiency without sacrificing precision. Whether you’re looking to accelerate production times, reduce lead times, or simply streamline your workflow, these proven strategies will propel your machining operations to new heights. Read on as we unravel the intricacies of maximizing CNC router machining speed, uncovering actionable tips, innovative technologies, and best practices that promise to propel your manufacturing endeavors to new heights of efficiency and effectiveness.
The significance of improving CNC router processing speed
Increasing the processing speed of a CNC router holds immense significance for manufacturers across industries. It enables manufacturers to meet customer demands more effectively, optimize resource utilization, and drive overall business growth. Details are as follows:
- Enhanced Productivity: Faster machining speeds translate directly to increased productivity. By reducing cycle times, manufacturers can produce more parts in less time, thereby maximizing output without compromising on quality.
- Reduced Lead Times: In today’s fast-paced market, customers demand quick turnaround times. By accelerating CNC router processing speed, manufacturers can significantly reduce lead times, meet customer deadlines more effectively, and gain a competitive edge in the market.
- Cost Savings: Time is a valuable resource in manufacturing. By decreasing machining times, manufacturers can lower production costs associated with labor, energy consumption, and machine wear. This cost efficiency contributes to higher profitability and sustainability.
- Streamlined Workflow: Speeding up CNC router operations helps streamline the manufacturing process by reducing bottlenecks and optimizing workflow. With faster processing times, production schedules become more predictable, allowing for better resource planning and smoother operations.
- Expanded Capacity: Increased machining speed allows manufacturers to handle higher volumes of work without the need for additional equipment or manpower. This scalability is beneficial for meeting fluctuating demand and accommodating growth opportunities.
- Improved Quality Control: Contrary to the common misconception that faster machining compromises quality, optimizing CNC router speed can actually enhance precision and consistency. Advanced technologies and optimized toolpaths ensure that high-speed machining maintains or even enhances precision and consistency, resulting in superior product quality.
- Scalability and Flexibility: Higher processing speeds enable manufacturers to scale their production capacity more effectively to meet fluctuating demand. This flexibility allows businesses to respond quickly to market changes and capitalize on growth opportunities without significant investments in additional equipment or manpower.
- Competitive Advantage: In today’s competitive market landscape, efficiency is key to staying ahead of the competition. Companies that can deliver products faster and more cost-effectively gain a significant competitive advantage. Increasing CNC router processing speed enables manufacturers to stay ahead of the competition, attract more customers, and drive business growth.
Factors Affecting CNC Router Processing Speed
The processing speed of a CNC router is affected by many factors. By dissecting these factors and understanding their implications, manufacturers can gain insights into optimizing their machining operations for enhanced productivity and superior results. The specific factors are analyzed as follows:
Machine Specifications
- Machine Rigidity and Stability: The rigidity and stability of the CNC router machine itself affect its ability to maintain high speeds and precision during cutting operations. Stiffer and more robust machines can typically handle higher cutting speeds with minimal vibration and deflection, resulting in better surface finish and accuracy.
- Spindle Power and Torque: The power and torque capabilities of the spindle motor determine the maximum cutting forces that can be applied during machining. Higher spindle power allows for faster cutting speeds and deeper cuts, particularly when working with harder materials or larger tools.
- Axis Configuration: The number and configuration of axes (e.g., 3-axis, 4-axis, 5-axis) impact the complexity of cuts that can be achieved and, consequently, the processing speed. More advanced axis configurations offer greater versatility but may require additional setup time and slower cutting speeds for intricate operations.
Router Bit Selection
- Router Bit Quality and Material: The quality and material composition of router bits significantly affect cutting performance and longevity. High-quality carbide or diamond-coated bits are more durable and can maintain sharp cutting edges longer, allowing for faster and more consistent machining speeds.
- Router Bit Diameter and Geometry: The diameter and geometry of the router bit determine the cutting efficiency and surface finish achievable. Larger diameter bits can remove material more quickly but may require lower feed rates to prevent excessive tool wear. Additionally, the flute geometry (e.g., upcut, downcut, compression) affects chip evacuation and cutting forces, influencing machining speed.
Material Factors
- Material Type and Density: Different materials have varying cutting properties and densities, which can affect machining speed. Harder materials typically require slower cutting speeds to maintain accuracy and prevent tool wear, while softer materials may allow for faster machining.
- Material Removal Rate: The rate at which material can be removed during cutting directly affects processing speed. Factors influencing material removal rate include spindle power, feed rate, depth of cut, and cutting tool geometry. Optimizing these parameters for efficient chip evacuation and minimal tool wear is beneficial for maximizing material removal rates.
CNC Programming Efficiency
- Toolpath Optimization: The efficiency of the toolpath generated by the CAM software significantly influences machining speed. Optimized toolpaths minimize unnecessary tool movements, reduce air cutting, and maximize chip load, allowing for faster and more efficient machining.
- Program Complexity: The complexity of the CNC machining program impacts processing speed, as more intricate toolpaths and operations may require slower feed rates and additional tool changes. Simplifying program complexity through efficient nesting, toolpath optimization, and tool selection can help minimize processing time and increase productivity.
Other Factors
- Coolant and Chip Evacuation: Proper coolant application and chip evacuation are beneficial for maintaining cutting efficiency and prolonging tool life. Effective chip evacuation prevents chip recutting and tool overheating, enabling higher machining speeds and better surface finish.
- Cutting Parameters: Parameters such as spindle speed (RPM), feed rate, depth of cut, and stepover directly influence machining speed. Optimizing these parameters based on material type, tooling, and desired surface finish is beneficial for achieving efficient and effective machining.
- Workholding and Fixturing: Secure and stable workholding setups are necessary to prevent part movement or vibration during machining. Poor workholding can lead to chatter, tool deflection, and inaccuracies, ultimately limiting machining speed and quality.
- Tool Wear and Maintenance: Regular tool inspection, maintenance, and replacement are beneficial for ensuring consistent machining performance. Worn or damaged tools can lead to poor surface finish, dimensional inaccuracies, and reduced machining speeds.
- Operator Skill: The skill and experience of the CNC operator play a key role in optimizing processing speed. Experienced operators can fine-tune cutting parameters, troubleshoot issues quickly, and make adjustments on the fly to maximize efficiency and productivity. Training and ongoing skill development are beneficial for ensuring optimal CNC router performance.
Strategies to Improve CNC Router Processing Speed
Improving CNC router processing speed requires a proactive approach that addresses various aspects of machine operation and workflow optimization. Here are several strategies to enhance processing speed. Embrace these strategies to unlock the full potential of CNC routers and maintain a competitive edge in today’s fast-paced manufacturing environment.
Machine Specification Optimization
- Enhance Machine Rigidity and Stability: Ensure your CNC router is properly calibrated, maintained, and equipped with adequate vibration damping mechanisms to minimize tool chatter and vibration during high-speed machining. Upgrading machine components, such as spindle motors, bearings, and drive systems, can also improve rigidity and stability, enabling higher processing speeds and accuracy.
- Upgrading the Spindle: Upgrading the spindle is a foundational step in enhancing CNC router performance. High-speed spindles with increased horsepower and torque capabilities enable faster cutting speeds and improved material removal rates. When selecting a spindle upgrade, consider factors such as maximum RPM, power output, and compatibility with existing machine configurations. Upgrading to a high-performance spindle can significantly boost processing speed and overall machining efficiency.
- Selecting High-Speed Router Bits: High-speed router bits, specifically designed for fast material removal and precision machining, offer superior cutting efficiency and extended tool life. Choose router bits with advanced geometries, specialized coatings, and carbide materials capable of withstanding high-speed cutting conditions. Additionally, consider factors such as flute design, flute length, and tool diameter to match the requirements of your machining applications.
- Upgrade Automatic Tool Changer: Invest in tool changers and quick-change systems that enable rapid swapping of cutting tools, reducing the idle time between machining operations. Utilize preset tooling offsets and fixture setups to minimize manual adjustments and streamline production workflow. By optimizing tool change and setup processes, manufacturers can increase spindle utilization and overall productivity.
Operation Process Optimization
- Optimizing Toolpaths: Toolpath optimization is a fundamental aspect of increasing CNC router processing speed. By utilizing advanced CAM software and optimizing toolpath strategies, operators can minimize unnecessary tool movements, reduce air cutting, and maximize chip load for efficient material removal. Employing adaptive clearing, trochoidal milling, and other high-speed machining techniques can further enhance cutting efficiency and reduce cycle times.
- Selecting Appropriate Materials and Feed Speeds: The choice of materials and feed speeds directly impacts CNC router processing speed. Opt for materials that are well-suited to CNC machining processes, considering factors such as hardness, density, and machinability. Additionally, selecting appropriate feed speeds based on material properties and cutting conditions is beneficial for achieving optimal cutting efficiency and surface finish. Experimentation and testing with different material-feed speed combinations can help identify the most effective parameters for maximizing processing speed while maintaining cutting quality.
- Optimizing CNC Programs: Utilize advanced CAM software to generate optimized toolpaths and machining strategies tailored to specific part geometries and material characteristics. Optimize cutting parameters such as spindle speed, feed rate, depth of cut, and toolpath strategies to minimize cycle times and maximize material removal rates. Regularly review and refine CNC programs to incorporate best practices and accommodate changes in production requirements, ensuring continuous improvement in processing speed and overall efficiency.
- Parallel Processing and Multi-Tasking: Explore opportunities to divide machining tasks into parallel operations that can be performed simultaneously on different areas of the workpiece. Additionally, consider integrating multi-tasking features such as dual-spindle or multi-axis machining to perform multiple operations in a single setup. By maximizing machine utilization and minimizing idle time, parallel processing and multi-tasking enable faster cycle times and increased production throughput.
Training and Maintenance
- Operator Training and Skill Development: Provide operators with hands-on training on machine operation, tooling selection, programming, and troubleshooting techniques. Emphasize the importance of proper setup, tool maintenance, and adherence to safety protocols to minimize downtime and optimize production throughput. Empowered and knowledgeable operators can identify inefficiencies, troubleshoot issues, and implement best practices to optimize processing speed and overall productivity.
- Regular Preventive Maintenance: Implement a comprehensive maintenance schedule that includes routine inspections, lubrication, and calibration of machine components such as bearings, drive systems, and spindle assemblies. Addressing issues proactively can minimize downtime, reduce the risk of unexpected breakdowns, and maintain consistent processing speed and cutting quality.
- In the dynamic world of manufacturing, maximizing processing speed is beneficial for achieving competitive advantage and driving business success. By incorporating these strategies into your CNC routing operations, you can effectively increase processing speed, reduce cycle times, and maximize efficiency, ultimately driving greater throughput and profitability in your manufacturing endeavors.
Summarize
In the ever-evolving landscape of manufacturing, the quest for increased efficiency and productivity remains constant. As technology advances and market demands evolve, the pursuit of increased processing speed will continue to drive innovation in CNC machining. The strategies outlined in this article offer a guide for maximizing the processing speed of CNC routers, empowering manufacturers to meet the demands of today’s fast-paced market. By embracing these strategies and leveraging the full capabilities of CNC technology, manufacturers can stay ahead of the curve and thrive in the dynamic world of modern manufacturing.
In our commitment to producing excellent CNC routers, we understand the importance of maximizing processing speed for business productivity and efficiency. Therefore at AccTek CNC, we insist on using high-quality components and implement strict quality control, to ensure that each CNC router is designed to meet the highest standards of performance, durability, and reliability. For businesses seeking CNC routers that are high-performance and efficient, AccTek CNC stands as the trusted partner of choice. We look forward to helping you unlock the full potential of your CNC router and achieve your machining goals with precision and efficiency.