CNC Router Control Systems Comprehensive Guide
- 12-18 Min Read
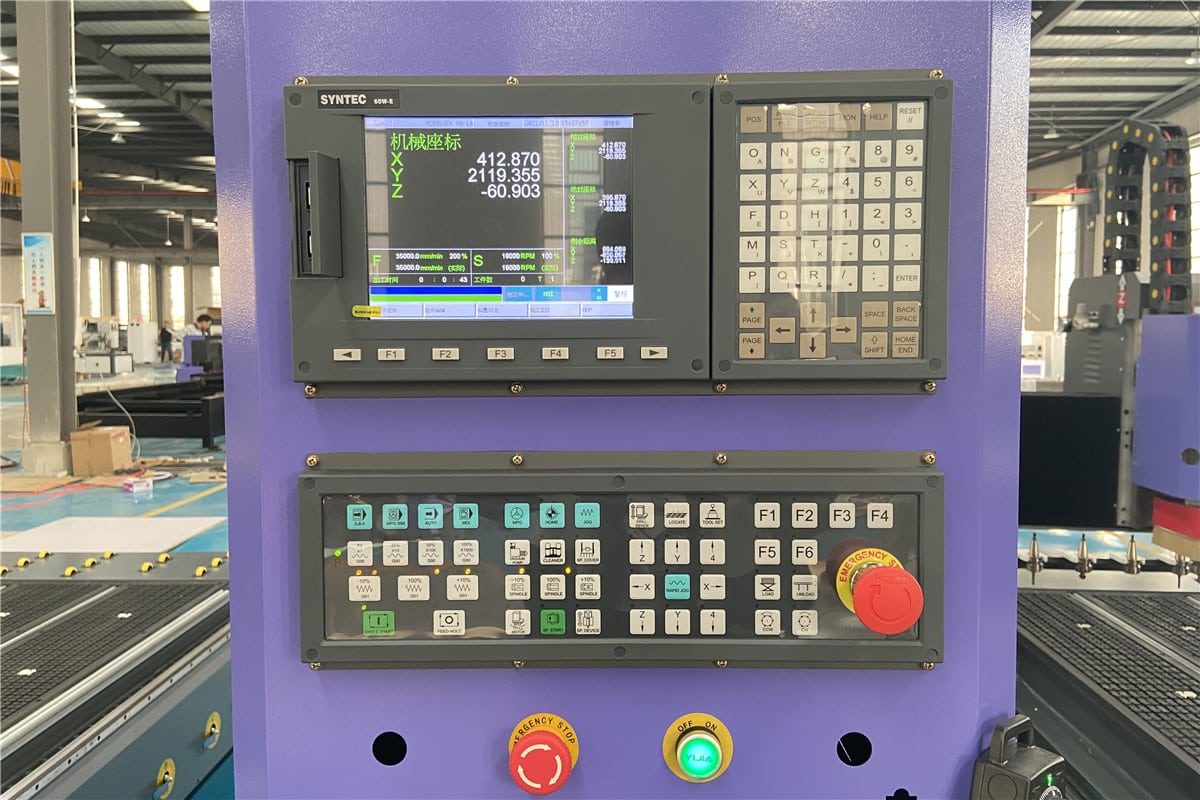
In the realm of modern manufacturing, Computer Numerical Control (CNC) routers stand as stalwarts, revolutionizing the way we shape materials with precision and efficiency. At the heart of these remarkable machines lies a complex network of control systems, orchestrating intricate movements and translating digital designs into tangible creations. Whether as a seasoned professional or an enthusiastic novice, understanding the nuances of these control systems will help you operate your machine properly.
In this article, we embark on a journey through the inner workings of CNC router control systems, unraveling their impact on accuracy and functionality. Join us as we explore the common types of CNC router controllers, from the ubiquitous presence of PC-based controllers to the specialized realm of dedicated motion controllers. Through insightful analysis and practical examples, we seek to demystify the nuances of each controller type, empowering readers to make informed decisions in their pursuit of excellence in computer-controlled machining.
What is a CNC router controller?
A CNC router controller is the central component of a computer numerical control (CNC) router system, responsible for interpreting digital instructions and translating them into precise movements and operations. Essentially, it serves as the brain of the CNC router, orchestrating the coordination of motors, drives, and other mechanical components to execute commands accurately.
The CNC router controller receives instructions in the form of numerical data from computer-aided design (CAD) or computer-aided manufacturing (CAM) software. These instructions typically include details about toolpaths, cutting parameters, and other specifications for the desired machining operation. Once the controller receives the instructions, it processes the data and generates signals to drive the motors that control the movement of the router’s axes (X, Y, and Z). Additionally, the controller may manage auxiliary functions such as spindle speed control, tool changes, and coolant systems, depending on the complexity of the CNC router setup.
There are various types of CNC router controllers available, ranging from simple open-loop controllers to more sophisticated closed-loop systems. Each type offers different levels of precision, speed, and functionality, catering to a wide range of applications and user requirements. The CNC router controller is an essential component in the realm of computer-controlled machining.
Impact of CNC router controller on accuracy and functionality
The CNC router controller significantly influences both the accuracy and functionality of the machine, impacting its ability to produce precise parts efficiently and reliably. Specifically reflected in the following aspects:
Accuracy
- Motion Control: The controller governs the movement of the machine’s axes, dictating the precision with which it follows the programmed toolpaths. Controllers with advanced motion control algorithms can minimize errors such as backlash and vibration, resulting in higher overall accuracy.
- Repeatability: A good controller maintains consistent positioning across multiple runs, ensuring that the CNC router consistently produces accurate cuts or carvings.
- Feedback Systems: Some controllers incorporate feedback mechanisms, such as encoders or linear scales, to provide real-time positional feedback. This feedback allows for closed-loop control, where the controller can adjust the movement of the axes to compensate for any deviations from the desired positions, thereby improving accuracy.
- Interpolation: Sophisticated controllers can perform high-level interpolation algorithms to generate smooth and precise toolpaths, especially when executing complex curves or arcs. This capability enhances the accuracy of the machined parts.
Functionality
- Compatibility: The controller’s compatibility with different software and file formats determines the range of designs and projects it can execute. Controllers with versatile communication protocols and software interfaces offer greater flexibility in integrating with various CAD/CAM systems.
- Tool Management: Advanced controllers support features such as automatic tool change and tool length compensation, enhancing the CNC router’s functionality and productivity by allowing for seamless transitions between different machining operations.
- Multi-Axis Control: Controllers capable of managing multi-axis setups enable the machining of complex geometries and contours, expanding the range of applications and design possibilities.
- Speed and Feed Control: The controller manages the speed and feed rate of the CNC router, optimizing cutting parameters for different materials and cutting tasks. This functionality directly affects efficiency and surface finish.
- Safety Features: Controllers often include safety features such as emergency stop buttons, limit switches, and collision detection systems to protect both the machine and the operator.
- Interface and User Experience: The controller’s user interface affects the ease of operation and programming. Intuitive interfaces and features like simulation modes can streamline setup and troubleshooting.
- Integration of Additional Systems: Some controllers can integrate with auxiliary systems such as probing systems for part inspection, automatic material feeders, or robotic arms for material handling, further enhancing the functionality and versatility of the CNC router system.
What are the common types of CNC router controllers?
Several types of CNC router controllers are commonly used in the industry, each with its own features and capabilities. Here are some of the most common types:
Computer Controllers
- Computer controllers, also known as PC-based controllers, utilize a standard computer or PC as the control system for the CNC router.
- These systems run specialized CNC control software, such as Mach3, Mach4, or LinuxCNC, which interprets G-code commands and generates control signals for the machine’s motors.
- Computer controllers offer flexibility, as users can choose from a variety of software options to suit their specific needs.
- They typically feature a graphical user interface (GUI) for programming and control, allowing users to visualize toolpaths and monitor machine status in real time.
- Computer controllers are popular for their versatility and ability to integrate with other software tools and peripherals.
DSP (Digital Signal Processor) Controllers
- DSP controllers are standalone units that incorporate a digital signal processor to handle the control tasks of the CNC router.
- These controllers are specifically designed for CNC applications and typically come with built-in motion control algorithms.
- DSP controllers often feature a dedicated interface for programming and operation, making them straightforward to use without the need for a separate computer.
- They offer reliability and ease of setup, making them popular choices for hobbyists and small-scale production environments.
- DSP controllers are known for their robustness and suitability for demanding machining tasks.
All-in-One Controllers
- All-in-one controllers, also known as integrated controllers or motion control systems, combine the functionality of both computer controllers and DSP controllers into a single unit.
- These controllers typically feature a built-in computer or microcontroller for running control software and processing G-code commands.
- They also incorporate dedicated motion control hardware, such as stepper motor drivers or servo drives, to generate precise control signals for the router’s axes.
- All-in-one controllers offer the benefits of both computer-based and DSP-based systems, providing flexibility, reliability, and ease of use in a compact package.
- They are often preferred for applications where space is limited or where a standalone computer may not be practical or cost-effective.
Popular CNC router controller recommendation
Mach3 Controller
Mach3 is a software package developed by ArtSoft that serves as a complete CNC control solution for a wide range of machines. It runs on Windows-based computers and interfaces with the machine’s hardware via parallel port, USB, or Ethernet connection. Mach3 translates G-code instructions into motion commands, allowing users to control the movement of the machine’s axes and execute machining operations with precision.
Features and Functions
- Mach3 is a popular CNC controller software designed to control CNC machines using a personal computer.
- It offers a user-friendly interface with customizable screens, making it suitable for both novice and experienced users.
- Mach3 supports various input methods including G-code, DXF files, and manual input.
- It provides real-time control over CNC routers, allowing for precise and efficient machining operations.
Advantages
- Versatility: Mach3 is compatible with various CNC routers and can be customized to suit different machining needs.
- Customizability: Mach3’s customizable GUI and support for macros and plugins allow users to tailor the software to their specific needs and workflow.
- Cost-Effective: Mach3 is available at a relatively low cost compared to some other CNC control software options, making it an attractive choice for budget-conscious users.
Disadvantages
- Compatibility Limitations: Mach3 is primarily designed for use with Windows-based systems, limiting its compatibility with other operating systems.
- Hardware Requirements: Mach3 requires a computer with sufficient processing power and compatible hardware interfaces, which may necessitate additional investment.
- Parallel Port Dependence: While Mach3 can interface with machines via USB or Ethernet, its original design relied on the now-obsolete parallel port, which may pose compatibility issues with modern computers.
Fangling Control System
Fangling control systems are a series of CNC (Computer Numerical Control) systems developed and manufactured by Fangling Technology Co., Ltd., a leading Chinese company specializing in CNC technology. These control systems are designed to provide reliable and precise control for CNC routers, engraving machines, milling machines, and other CNC equipment.
Features and Functions
- Fangling controllers are standalone units that do not require a separate computer to operate. They have built-in processing capabilities and run proprietary control software.
- These controllers often feature an intuitive user interface with a touchscreen or keypad for easy programming and operation.
- They support various input methods such as G-code, DXF files, and manual input, enabling precise control over machining operations.
Advantages
- Reliability: Fangling controllers are known for their reliability and stability, ensuring consistent performance even in demanding production environments.
- Ease of Use: The user-friendly interface makes programming and operating the CNC router straightforward, reducing setup time and training requirements.
- Cost-Effective: Fangling controllers offer a good balance of performance and affordability, making them suitable for both hobbyists and small to medium-sized businesses.
Disadvantages
- Limited Customization: While Fangling controllers offer a range of features, they may have limited customization options compared to more advanced controllers.
- Software Dependence: Users are reliant on the proprietary control software provided by Fangling, which may have limitations in terms of features or compatibility with third-party software.
- Technical Support: Depending on the region and distributor, technical support for Fangling controllers may vary, potentially causing challenges in troubleshooting or resolving issues.
Weihong Controller
Weihong CNC controllers are produced by Beijing FANCH Machinery Co., Ltd., a leading manufacturer of CNC control systems and equipment. Weihong controllers are known for their reliability, performance, and cost-effectiveness, making them popular choices for CNC machines across various industries.
Features and Functions
- Versatility: They can handle various CNC machining tasks, including milling, turning, drilling, and more.
- User Interface: Many Weihong controllers feature user-friendly interfaces with LCD displays and keypad inputs for easy programming and operation.
- Customization Options: Users can often customize parameters and settings to optimize performance for specific applications and machining tasks.
Advantages
- Reliability: Weihong controllers are known for their reliability and durability, making them suitable for continuous operation in industrial environments.
- Cost-Effectiveness: They offer good value for money, providing advanced features and performance at competitive prices.
- Ease of Use: Many Weihong controllers feature intuitive interfaces and user-friendly programming tools, reducing the learning curve for operators.
Disadvantages
- Limited Availability: While Weihong controllers are popular in certain regions, they may be less commonly available in other parts of the world, which could affect support and spare parts availability.
- Compatibility Issues: There may be compatibility issues with certain CNC machines or software packages, particularly in more specialized or niche applications.
FANUC Control System
The FANUC Control System is a widely used CNC control system developed by FANUC Corporation, a leading manufacturer of factory automation and industrial robotics systems. It is a comprehensive CNC control solution designed for a wide range of machining and manufacturing applications. FANUC offers several generations of control systems, each with its own features and capabilities, catering to different levels of complexity and performance requirements.
Features and Functions
- High-Speed Processing: FANUC Control Systems are known for their high-speed processing capabilities, enabling rapid execution of complex machining operations.
- Advanced Capabilities: These systems often feature advanced functionalities such as toolpath optimization, adaptive control, and real-time monitoring.
- Integration with FANUC Robotics: For manufacturers employing both CNC machining and robotic automation, FANUC Control Systems can seamlessly integrate with FANUC robots and automation solutions, enabling efficient production workflows.
Advantages
- Reliability and Durability: FANUC Control Systems are renowned for their reliability and durability, with robust hardware and software designed to withstand the demands of industrial machining environments.
- Wide Range of Applications: The versatility of FANUC Control Systems makes them suitable for machining tasks ranging from simple milling and drilling to complex multi-axis machining and high-speed contouring.
- Global Support Network: FANUC has a global network of service and support centers, ensuring prompt assistance and maintenance services wherever the equipment is deployed.
Disadvantages
- Cost: FANUC Control Systems can be relatively expensive compared to some other CNC control solutions, particularly for entry-level or hobbyist applications.
- Complexity for Novice Users: While FANUC Control Systems offer advanced capabilities, they may have a steeper learning curve for novice users, requiring training and experience to fully utilize their features.
SYNTEC Control System
SYNTEC is a Taiwanese company that specializes in manufacturing CNC controllers for a variety of machining applications, including milling, turning, and routing. The SYNTEC Control System is a comprehensive solution that includes hardware components, such as motion control cards and operator panels, as well as software for programming and operating CNC machines.
Features and Functions
- Advanced Features: SYNTEC controllers offer advanced motion control capabilities, intuitive programming interfaces, and extensive customization options, allowing users to optimize machine performance and productivity.
- Multi-axis control: They support multi-axis control, allowing for complex machining operations and increased productivity.
- Remote Monitoring and Diagnostics: Some SYNTEC controllers offer remote monitoring capabilities, allowing users to monitor machine performance and troubleshoot issues from a remote location using network connectivity.
Advantages
- Precision: SYNTEC control systems are known for their high precision and accuracy in controlling machine movements, resulting in superior machining quality.
- Versatility: They are suitable for various machining applications across different industries, from woodworking to metalworking.
- User-friendly: The intuitive interface of SYNTEC control systems reduces the learning curve for operators, improving efficiency and productivity.
Disadvantages
- Cost: SYNTEC control systems may come with a higher initial cost compared to some other alternatives, which could be a drawback for budget-conscious users.
- Complexity: While they offer advanced features, the complexity of SYNTEC systems may require additional training for operators to fully utilize their capabilities.
LNC Control System
LNC Control Systems are popular CNC control systems developed by LNC Technology Co., Ltd., a Taiwanese company specializing in CNC controllers and automation solutions. LNC Control Systems are comprehensive CNC control solutions designed to drive various types of CNC machines, including milling machines, lathes, routers, and more. They encompass both hardware and software components, offering a complete package for controlling machine tools and automation equipment.
Features and Functions
- Real-time optimization: The adaptive control features can optimize machining parameters on-the-fly, leading to improved efficiency and reduced machining times.
- Diagnostic capabilities: Built-in diagnostic tools help identify and address issues quickly, minimizing machine downtime and increasing productivity.
- Advanced features may include toolpath optimization, adaptive control, and error compensation algorithms to enhance machining accuracy and efficiency. LNC software may also support integration with CAD/CAM systems and networking capabilities for data exchange and remote monitoring.
Advantages
- High Performance: LNC Control Systems deliver high-speed and high-precision motion control, enabling efficient machining of complex parts with tight tolerances.
- Versatility: They are suitable for a wide range of CNC applications, from simple milling and turning operations to complex multi-axis machining and automation tasks.
- Reliability and Durability: LNC Control Systems are built to withstand the demands of industrial machining environments, offering reliable performance and long-term durability.
Disadvantages
- Cost: Compared to some entry-level CNC control solutions, LNC Control Systems may have a higher initial cost, particularly for advanced configurations with additional features.
- Initial setup complexity: Setting up and configuring LNC systems to work optimally with specific machines and applications may require technical expertise, which could be a challenge for some users.
DSP Control System
DSP Control Systems are standalone units designed specifically for controlling CNC machinery. They employ digital signal processing technology to execute motion control algorithms and generate precise control signals for the CNC router’s motors. DSP controllers typically feature dedicated hardware for motion control tasks, offering reliability and performance optimized for CNC applications.
Features and Functions
- Real-time Processing: DSPs are capable of real-time processing, allowing for fast and precise control of the CNC router’s motors.
- High-Speed Communication: DSPs can communicate with external devices and peripherals at high speeds, enabling seamless integration with other components of the CNC system.
Advantages
- Ease of Use: Many DSP controllers feature a user-friendly interface, making them easy to program and operate without extensive technical knowledge.
- Compact Design: DSP controllers are often compact in size, making them suitable for installation in space-constrained environments.
- Cost-Effectiveness: DSP control systems can offer a cost-effective solution for CNC control, particularly for smaller-scale applications.
Disadvantages
- Limited Flexibility: DSP controllers may have limited flexibility compared to computer-based control systems, particularly in terms of customization and software options.
- Dependency on Hardware: DSP controllers rely on dedicated hardware for motion control tasks, which may limit the ability to upgrade or modify the system easily.
- Programming Constraints: While DSP controllers offer ease of use, they may have limitations in terms of programming capabilities compared to computer-based systems.
Siemens Control System
Siemens offers a range of CNC control systems for various machining applications, including CNC routers. One of their popular offerings is the SINUMERIK line of control systems. Siemens SINUMERIK CNC control systems are known for their precision, reliability, and advanced features.
Features and Functions
- Integrated Safety Functions: These control systems come with integrated safety functions to ensure operator and machine safety, including collision avoidance and emergency stop features.
- Tool Management: SINUMERIK control systems support advanced tool management features, including tool length measurement, tool wear compensation, and automatic tool change.
- Simulation and Visualization: They offer simulation and visualization tools to preview machining operations, detect errors, and optimize toolpaths before actual machining.
- Remote Monitoring and Diagnostics: SINUMERIK control systems support remote monitoring and diagnostics, allowing operators to monitor machine performance and troubleshoot issues remotely.
Advantages
- Reliability: SINUMERIK control systems are highly reliable, with robust hardware and software designed to withstand the demands of industrial machining environments.
- Global Support: Siemens provides extensive global support and service for their control systems, ensuring prompt assistance and maintenance wherever needed.
- Integration with CAD/CAM Systems: SINUMERIK control systems seamlessly integrate with Siemens CAD/CAM software and other third-party software solutions, streamlining the programming and machining workflow.
Disadvantages
- Cost: Siemens control systems tend to have a higher initial cost compared to some other options in the market.
- Complexity: The advanced features and capabilities of SINUMERIK control systems may require some learning curve for operators and programmers.
How to choose CNC router controller?
Choosing the right CNC router controller involves considering several key factors to ensure it meets your specific needs and requirements. Here’s a step-by-step guide to help you make an informed decision:
Understand Your Requirements
- Determine the type of materials you’ll be working with (wood, plastics, metals, etc.).
- Consider the size and complexity of the projects you’ll be undertaking.
- Identify any specific features or capabilities you need, such as multi-axis control, high-speed processing, or compatibility with certain software.
Research Available Options
- Explore the various types of CNC router controllers available in the market, including PC-based controllers, DSP controllers, PLC controllers, and integrated controllers.
- Look for controllers that offer features and capabilities that align with your requirements. Consider factors such as motion control accuracy, compatibility with CAD/CAM software, speed and feed control, tool management capabilities, and safety features.
Evaluate Compatibility
- Ensure that the controller you choose is compatible with your CNC router hardware, including stepper motors, servo motors, spindle motors, and other components.
- Check for compatibility with your existing CAD/CAM software or any third-party software tools you plan to use for programming and toolpath generation.
Consider Support and Maintenance
- Look for manufacturers or suppliers that offer comprehensive technical support, including documentation, tutorials, and troubleshooting resources.
- Check the availability of software updates, firmware upgrades, and spare parts.
- Consider the warranty and after-sales service provided by the manufacturer.
Factor in Cost
- Determine your budget for the CNC router controller, taking into account not just the initial cost of the controller itself but also any additional costs for software, accessories, and ongoing maintenance and support.
- Balance the cost of the controller against its features, capabilities, and potential return on investment in terms of increased productivity and efficiency.
Seek Recommendations and Advice
- Consult with industry experts, fellow CNC router users, or online communities to get recommendations and advice on choosing the right controller.
- Attend trade shows, exhibitions, or seminars where you can see demonstrations of different controllers and ask questions directly to the manufacturers.
Demo or Trial Period
- If possible, request a demo or trial period for the CNC router controller to test its performance and suitability for your specific needs.
- Use this opportunity to evaluate its ease of use, compatibility, and overall functionality before making a final decision.
By following these steps and carefully evaluating your options, you can choose a CNC router controller that meets your specific needs and helps you achieve your machining goals effectively and efficiently.
Summarize
Selecting the right CNC router control system is a crucial step in ensuring the success and efficiency of your machining operations. Therefore, it’s essential to invest time in researching and evaluating different options before making a final decision. Whether you prioritize reliability, precision, affordability, or advanced features, there’s a CNC router control system out there to meet your needs. By following the guidelines outlined in this comprehensive guide and leveraging your knowledge and expertise, you can confidently choose the right CNC router control system to propel your machining endeavors to new heights of success.
One of the most striking aspects of AccTek CNC’s offerings is its range of CNC routers equipped with various types of controllers. This diversity allows our customers to select the precise combination that meets their specific processing requirements. Whether it’s the intricacies of intricate designs or the efficiency demanded by high-volume production, AccTek CNC ensures that there’s a suitable solution available. Contact us today to learn more about our CNC routers and how we can help elevate your machining capabilities.