Aluminum CNC Router
Aluminum CNC routers are high-performance machines designed to meet the precision demands of industries that require intricate machining of aluminum and other non-ferrous metals. Whether you’re in aerospace, automotive, or custom fabrication, these CNC routers provide unmatched accuracy, speed, and versatility. Engineered with advanced technology, our aluminum CNC routers are equipped with powerful spindles, robust frames, and cutting-edge motion control systems to ensure flawless operation. The precision-driven design allows for consistent results, even with complex geometries, reducing material waste and improving productivity.
Ideal for a wide range of applications—from prototyping and product development to large-scale production runs—these CNC routers excel at cutting, engraving, milling, and drilling aluminum. The user-friendly interface and customizable settings make them suitable for both experienced machinists and newcomers alike. Our aluminum CNC routers are built for durability, providing long-lasting performance with minimal maintenance. With cutting-edge features such as high-speed spindle options, automatic tool changers, and precise 3D machining capabilities, they are the perfect choice for businesses looking to improve their operational efficiency while maintaining the highest standards of quality.
-
AK4040 CNC Router
Rated 5.00 out of 5$4,000.00 Add to cart -
AK6060 CNC Router
Rated 5.00 out of 5$4,200.00 Add to cart -
AK4040H CNC Router
Rated 5.00 out of 5$5,600.00 Add to cart -
AK6060H CNC Router
Rated 5.00 out of 5$6,000.00 Add to cart -
AK4040C CNC Router
Rated 5.00 out of 5$10,500.00 Add to cart -
AK6060C CNC Router
Rated 5.00 out of 5$11,100.00 Add to cart
Tips for Choosing the Right Aluminum CNC Router
Selecting the right aluminum CNC router is a critical decision that can significantly impact your production efficiency, precision, and overall business performance. With various machines on the market, it’s essential to understand the specific features and capabilities that align with your needs.
Understand Your Specific Needs
Start by assessing the types of aluminum projects you’ll be working on. Will you be focusing on prototyping, low-volume runs, or large-scale production? Different CNC routers are optimized for specific tasks, so identifying the scope of your work will help you choose the right machine with the necessary speed, power, and precision.
Spindle Power and Speed
The spindle’s power and speed are vital for efficient aluminum cutting. High spindle power enables smoother cuts through thicker aluminum, while higher speeds enhance productivity. Look for a CNC router with adjustable spindle speeds to match the range of materials you plan to process. Faster spindle speeds are particularly useful for intricate designs and high-efficiency production.
Bed Size and Work Area
The CNC router’s bed size directly influences the size of workpieces you can handle. Consider your typical workpiece dimensions and select a machine that accommodates them comfortably. Larger bed sizes offer versatility for various project sizes, but ensure it aligns with your available workspace and project requirements.
Motion Control and Accuracy
Precision is crucial when machining aluminum. A high-quality motion control system, such as precise ball screws, linear guides, and servo motors, ensures accurate movement and repeatability. Look for machines with tight tolerances and minimal backlash to maintain cutting consistency, especially for intricate designs or detailed milling.
Material Handling Features
Consider the material handling capabilities of the CNC router, such as automatic tool changers (ATC) and material clamping systems. These features improve efficiency by reducing the need for manual intervention during setup or operation. Machines with ATC reduce downtime and allow for more complex operations with multiple tool changes in a single cycle.
Software Compatibility
Ensure the CNC router is compatible with your preferred CAD/CAM software. Good software integration ensures smooth file transfers, easy operation, and faster learning curves. Popular software like SolidWorks, Fusion 360, or AutoCAD are common choices, so verify the machine supports your workflow to avoid compatibility issues down the line.
Precision and Repeatability
Precision and repeatability are essential when working with aluminum to ensure tight tolerances and high-quality results. Look for CNC routers with high-resolution encoders and reliable motion systems to maintain repeatability between cuts, reducing errors and the need for rework. High precision guarantees a consistent output and minimizes waste.
Energy Efficiency and Operating Costs
Energy consumption is a significant factor in the long-term cost of ownership. Choose an aluminum CNC router that offers a balance between power and energy efficiency. Look for machines designed to reduce power consumption without compromising on cutting speed or performance, which will help keep your operational costs in check.
Ease of Maintenance
Maintenance can be time-consuming, so select a CNC router that offers easy accessibility for routine checks, cleaning, and servicing. Machines with user-friendly design features like simple lubrication systems, tool changers, and easy-to-replace components reduce downtime and lower long-term maintenance costs, ensuring continuous operation.
Safety Features
Safety is paramount when using high-power machines. Look for a CNC router with built-in safety features such as emergency stop buttons, protective covers, and sensor systems that prevent accidents. Additionally, ensure the machine is compliant with local safety standards to guarantee safe operation for your operators.
Customer Support and Warranty
Reliable customer support and a solid warranty are crucial for minimizing downtime. Choose a manufacturer that offers excellent customer service, prompt response times, and comprehensive warranty coverage. A strong support system ensures quick resolutions to technical issues, helping you avoid costly delays and keep production running smoothly.
Total Cost of Ownership
When evaluating CNC routers, consider the total cost of ownership, which includes initial purchase price, ongoing maintenance, energy consumption, tooling, and software updates. While cheaper machines may have a lower upfront cost, investing in a high-quality machine with better features can lead to lower long-term operating costs and higher returns on investment.
What grades of aluminum can the aluminum CNC router cut?
Aluminum CNC routers are highly versatile machines capable of cutting a wide range of aluminum grades, from lightweight alloys to heavy-duty materials. They can efficiently handle commonly used grades such as 6061, 5052, and 7075, which are popular in industries like aerospace, automotive, and manufacturing. These CNC routers are designed to cut both soft and harder aluminum alloys, offering precise and clean cuts, regardless of material hardness. The CNC router’s spindle power and tool selection allow it to process various aluminum grades, including those used for structural components, marine applications, and custom fabrication. The ability to cut different aluminum grades with high precision makes CNC routers an essential tool for creating parts with varying strength, weight, and corrosion resistance requirements.
- Aluminum 6061
- Aluminum 7075
- Aluminum 2024
- Aluminum 5052
- Aluminum 5083
- Aluminum 3003
- Aluminum 2011
- Aluminum 6063
- Aluminum 7050
Application Industry
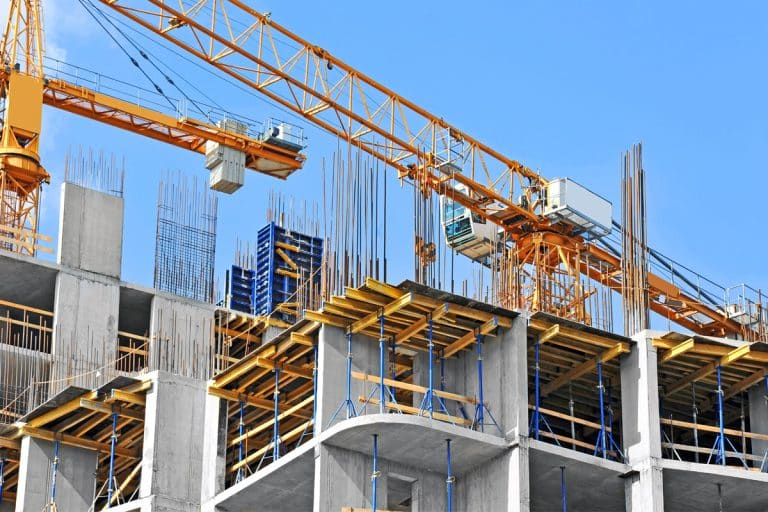
Construction Industry
The integration of CNC routers into construction workflows has ushered in a new era characterized by meticulous detailing, rapid prototyping, and improved material utilization.
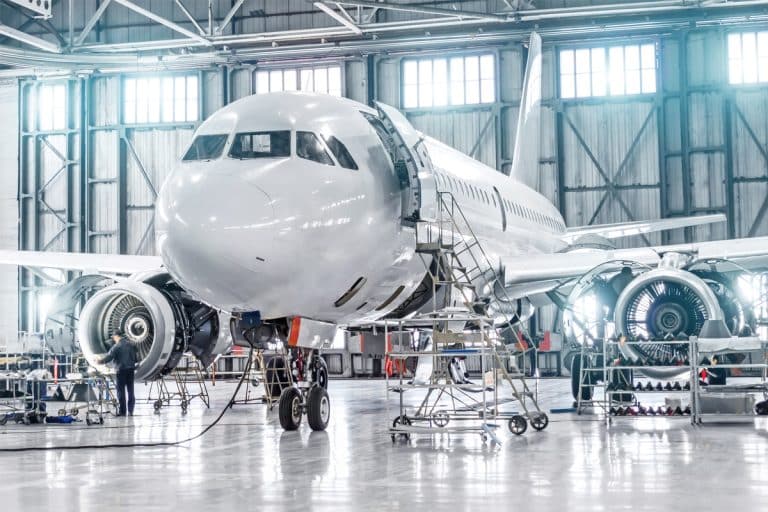
Aerospace Industry
The CNC router is widely used in aerospace engineering due to its unparalleled ability to carve complex designs, manufacture complex parts, and ensure tight tolerances.
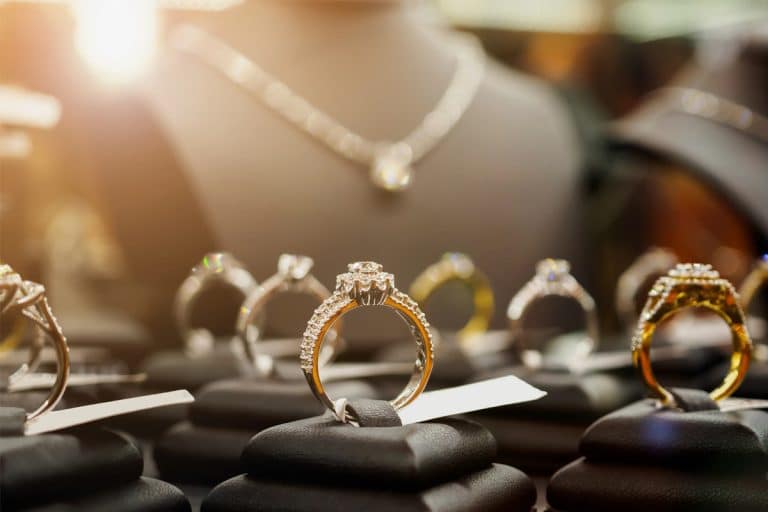
Jewelry Industry
The CNC router revolutionize the way fine jewelry is designed and made by delivering unparalleled precision and efficiency and producing intricate designs with meticulous attention to detail.
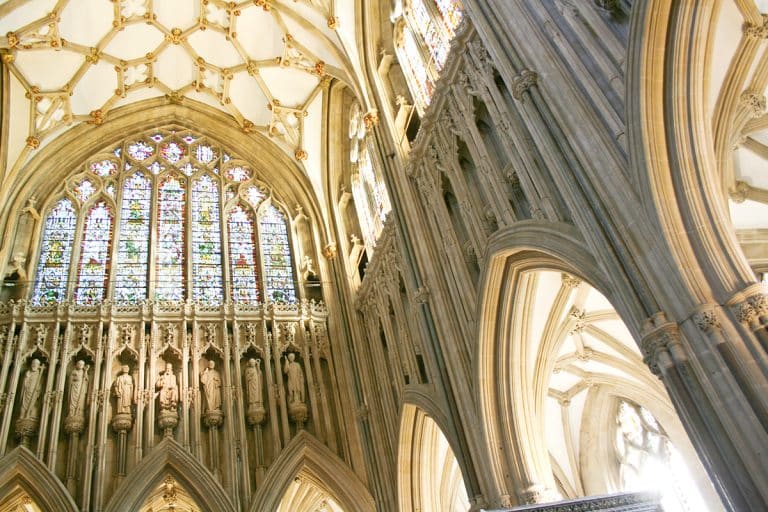
Stone Carving Industry
The integration of CNC routers into the stone carving industry is not only revolutionizing the way craftsmen carve, it is also redefining the boundaries of artistic possibilities in this ancient practice.
Blog
How to Choose the Right Stone CNC Router for Your Workshop?
This guide will walk you through the key factors to consider when choosing a stone CNC router, designed to help you invest wisely in a machine that delivers reliable performance ...
Read More
Best Budget CNC Router for Making Outdoor Signs?
In this guide, we'll break down the key features to look for, explore different models under a variety of price points, and help you choose the best budget CNC router ...
Read More
How to Maintain and Troubleshoot the ATC CNC Router?
This article will walk you through a practical maintenance procedure for your ATC CNC router and instruct you on how to diagnose and repair common problems that may arise.
Read More
What Warranties Are Typically Offered on CNC Routers?
In this article, we'll break down the different types of warranties typically offered on CNC routers, what's included, and how to make sure you're getting the support you need long ...
Read More
Frequently Asked Questions
How Do Aluminum CNC Routers Work?
Aluminum CNC routers use computer numerical control (CNC) technology to automate the process of cutting, engraving, milling, and drilling aluminum and other materials. These machines are equipped with a precise, motor-driven system that follows programmed instructions to carry out intricate and repeatable tasks with minimal human intervention.
The process begins by loading a CAD (Computer-Aided Design) file into the CNC router’s software. This design file is converted into machine-readable instructions (G-code) by the CAM (Computer-Aided Manufacturing) software. The CNC router’s controller reads these instructions, directing the machine’s movements along the X, Y, and Z axes to execute the programmed cut.
A powerful spindle, equipped with the appropriate tool (such as an end mill or drill bit), spins at high speeds to cut through the aluminum. The material is securely clamped to the CNC router bed, ensuring precision during the cutting process. The CNC router’s motion system moves the tool with extreme accuracy, achieving fine details, sharp edges, and smooth surfaces.
CNC routers are also equipped with advanced features like automatic tool changers (ATC) for seamless tool swaps, dust collection systems to keep the workspace clean, and cooling systems to prevent heat buildup, ensuring smooth and efficient operation. This automation results in high-quality, repeatable cuts with minimal errors, making aluminum CNC routers ideal for complex and high-precision tasks in industries like aerospace, automotive, and custom manufacturing.
What Are Aluminum CNC Routers Used For?
Aluminum CNC routers are widely used in industries that require precision machining of aluminum and other non-ferrous materials. These versatile machines are ideal for a variety of applications, ranging from prototyping to large-scale production. Here are some common uses:
- Custom Part Manufacturing: Aluminum CNC Routers are used to create custom parts for industries such as aerospace, automotive, and electronics, where precision and material strength are critical.
- Prototyping: Designers and engineers use CNC routers to quickly create prototypes of parts and products, allowing for rapid testing and modification.
- Signage: In industries like advertising and branding, aluminum CNC routers are used to carve out signage and decorative elements, providing high-quality, intricate designs.
- Tooling and Fixture Creation: They are used to create specialized tools, jigs, and fixtures required in manufacturing, ensuring accuracy and repeatability.
How Much Are Aluminum CNC Routers?
The price of an aluminum CNC router can vary significantly depending on the machine’s capabilities, size, and features. Here’s a general price range to help you understand the costs involved:
- Standard Aluminum CNC Router: These models, suitable for light to medium-duty tasks, typically range from $3,500 to $4,000. They offer great precision for basic cutting, engraving, and milling needs.
- Heavy-Duty Aluminum CNC Router: For more demanding applications, such as high-volume production or working with thicker materials, heavy-duty CNC routers are priced between $5,500 and $6,000. These models are designed to handle larger workloads and deliver superior durability and power.
- ATC Aluminum CNC Router: If you require advanced automation and increased efficiency, an automatic tool changer (ATC) aluminum CNC router can cost anywhere from $10,000 to $11,000. These CNC routers come with automatic tool-changing systems, making them ideal for complex, multi-step processes without manual intervention.
What is the Spindle Power of Aluminum CNC Routers?
The spindle power of an aluminum CNC router is a key factor in determining its cutting capabilities, especially when working with dense materials like aluminum. The spindle power influences the speed, efficiency, and precision of the cuts. Here’s a breakdown of the typical spindle power for various types of aluminum CNC routers:
- Economic Aluminum CNC Router: These CNC routers are designed for lighter applications and typically feature a 2.2KW spindle. This power level is ideal for general cutting, engraving, and light milling tasks on aluminum and softer materials.
- Heavy-duty Aluminum CNC Router: For more demanding tasks, such as cutting thicker aluminum or running at higher speeds, heavy-duty CNC routers usually come with a 3.2KW spindle. This extra power allows for faster cutting and the ability to handle tougher materials with greater precision.
- ATC Aluminum CNC Router: Automatic Tool Changer (ATC) aluminum CNC routers also typically feature a 3.2KW spindle. The added power ensures efficient multi-tool operations and high-speed milling, making these CNC routers perfect for more complex machining tasks and continuous production.
How Precise Are Aluminum CNC Routers?
Aluminum CNC routers are known for their exceptional precision, making them ideal for industries that require tight tolerances and high-quality finishes. The precision of a CNC router depends on several factors, including the machine’s design, motion control system, and the quality of its components. Here’s a breakdown of the precision typically offered by these machines:
- Tolerance: Most aluminum CNC routers can achieve tolerances as tight as ±0.1 mm (0.004 inches), which is suitable for most applications, including cutting, engraving, and milling. High-end models can achieve even finer tolerances of ±0.05 mm (0.002 inches), ideal for intricate designs and high-precision parts.
- Repeatability: CNC routers are capable of high repeatability, ensuring that each cut or operation is consistent across multiple pieces. High-quality machines can repeat movements with precision to within 0.01 mm (0.0004 inches), which reduces errors and increases efficiency in mass production environments.
- Accuracy Factors: The accuracy of the CNC router depends on components like linear guides, ball screws, and servo motors. Machines with high-end motion control systems, precise linear bearings, and backlash-free mechanisms offer better precision, especially for fine-detail work.
- Cut Quality: CNC routers are capable of producing smooth, clean edges with minimal burrs, reducing the need for post-processing. The precision ensures that the final product meets the required specifications for industries such as aerospace, automotive, and electronics.
How to Safely Operate Aluminum CNC Routers?
Operating aluminum CNC routers requires attention to safety due to the powerful machinery and the potential hazards of working with sharp tools and fast-moving parts. Following proper safety protocols ensures not only the protection of the operator but also the longevity and efficiency of the machine. Here are key safety practices to follow when operating aluminum CNC routers:
- Wear Personal Protective Equipment (PPE): Always wear appropriate PPE, including safety glasses, hearing protection, gloves, and dust masks. Protective eyewear shields against flying debris, while hearing protection helps mitigate noise exposure, especially when working with high-speed spindles.
- Ensure Proper Machine Setup: Before starting any job, double-check that the CNC router is correctly set up. This includes securing the material on the bed, ensuring that the tool is properly installed, and verifying the calibration of the machine. Improper setup can cause the machine to malfunction, leading to accidents.
- Keep the Work Area Clean and Organized: A clutter-free workspace reduces the risk of accidents. Ensure that the area around the CNC router is clean and free from obstacles that could cause trips, slips, or interference during operation. Also, make sure that the machine’s cooling system is functioning properly to avoid overheating.
- Use Machine Guards and Safety Covers: Never bypass or remove safety guards. These features protect the operator from sharp tools, spinning spindles, and debris during operation. Always ensure that safety covers are in place, especially during high-speed operations or while the machine is running.
- Follow Manufacturer Guidelines: Refer to the user manual for specific operational and safety guidelines. Each CNC router may have unique features or safety requirements that are vital for safe and efficient operation. Ensure you’re familiar with the machine’s specific needs.
- Perform Routine Maintenance: Regular maintenance, including checking the machine’s lubricating system, tightening bolts, and inspecting the tool and spindle, is essential for safe operation. A poorly maintained machine can malfunction, causing accidents or damage.
- Never Leave the Machine Unattended: Always monitor the machine during operation, especially when running complex cuts or heavy-duty tasks. Leaving the machine unattended can result in unnoticed issues such as tool wear, material movement, or other malfunctions.
- Use the Correct Tool for the Job: Using the right cutting tool for the material and task ensures safer, more efficient operation. Incorrect tool selection can lead to excessive force, tool breakage, or inaccurate cuts, increasing the risk of accidents.
- Be Mindful of Emergency Stop Mechanisms: Familiarize yourself with the location of the emergency stop button and emergency shut-off procedures. In case of a malfunction or emergency, stopping the machine immediately can prevent further damage or harm.
- Calibrate and Test Cuts Before Full Production: Always run test cuts on scrap material before starting your main project. This helps identify potential issues such as improper speeds, feeds, or tool settings, reducing the chance of accidents during full-scale production.
What Customer Support Do Aluminum CNC Routers Provide?
Aluminum CNC routers come with reliable customer support options to ensure smooth operation and user satisfaction:
- Free Online Technical Support: Customers can access complimentary technical assistance through online platforms, including email, chat, or video support. This service is ideal for troubleshooting, software setup, or resolving operational issues remotely.
- Paid On-Site Training: For users requiring hands-on guidance, on-site training sessions are available at an additional cost. These sessions cover installation, operation, and maintenance to ensure optimal use of the machine.
What Is The Warranty Period of Aluminum CNC Routers?
Our CNC router is backed by a comprehensive warranty designed to give you peace of mind and protect your investment:
- 3-Year Warranty for the Entire Machine: This full warranty covers any defects or malfunctions in the machine as a whole, ensuring reliable performance and longevity over time.
- 5-Year Warranty for Core Components: Key components essential for optimal machine operation are covered for 1.5 years. This includes parts that may experience wear and tear with regular use, ensuring you have support for the most vital parts of the machine.