3-Axis CNC Router
3-axis CNC routers are the cornerstone of precision machining, designed to deliver unparalleled accuracy and versatility across a wide range of applications. Whether you’re crafting intricate designs, shaping raw materials, or producing detailed prototypes, these machines provide an efficient and reliable solution for professionals and hobbyists alike. With the ability to manipulate the X, Y, and Z axes, 3-axis CNC routers can handle a variety of tasks, from engraving and cutting to milling and carving. Renowned for their simplicity and user-friendliness, 3-axis CNC routers are ideal for industries such as woodworking, metal fabrication, plastics manufacturing, and more. These machines are compatible with a variety of materials, including wood, aluminum, acrylic, and composites, making them a versatile choice for diverse project needs.
Equipped with advanced software and precision controls, 3-axis CNC routers enable seamless integration with CAD/CAM programs, ensuring that even complex designs are executed with consistency and speed. They are available in a range of sizes and configurations, from compact desktop models for small-scale projects to industrial-grade machines for high-volume production. Whether you’re a business looking to optimize your manufacturing processes or a craftsman seeking to elevate your creative capabilities, 3-axis CNC routers offer the perfect balance of performance, reliability, and affordability. Explore our selection to find the ideal solution for your machining needs.
Tips for Choosing the Right 3-Axis CNC Router
Selecting the perfect 3-axis CNC router requires careful consideration of your specific needs, project requirements, and operational goals. These versatile machines are available in a wide range of sizes, configurations, and price points, making it essential to evaluate the key factors that influence performance and efficiency. From material compatibility to software integration, each element plays a critical role in determining the success of your investment.
Understand Your Applications
Identify the primary tasks your CNC router will handle, such as cutting, engraving, or carving, and the materials you’ll work with. Each machine is designed with specific applications in mind, so understanding your workflow will help narrow your choices. Consider the machine’s capability to handle diverse materials, from softwoods to metals and plastics, to match your operational needs effectively.
Choose the Right Machine Size
Ensure the CNC router fits both your workspace and project dimensions. A compact machine may suit smaller workshops or personal use, while larger, industrial-grade models are better for high-volume or oversized materials. Check the working area and table size to accommodate your most common project sizes with ease.
Evaluate Build Quality
Sturdiness and durability are crucial for long-term performance. A rigid frame made of steel or cast iron minimizes vibrations and enhances cutting accuracy. Inspect the machine’s components, such as linear guides and drive systems, to ensure they are built for reliable, consistent operation over time.
Consider Precision and Accuracy
For intricate designs or projects with tight tolerances, prioritize machines with high repeatability and resolution. Check the specifications for precision metrics to ensure the CNC router meets your quality standards, especially if you work in industries like aerospace or fine woodworking.
Assess Spindle Power and Speed
The spindle’s power determines the types of materials the machine can cut effectively. For hard materials like aluminum, a high-power spindle is essential, while softer materials may require less power. Variable speed settings also provide greater versatility, allowing adjustments based on material type and thickness.
Check Software Compatibility
Your CNC router should integrate smoothly with industry-standard CAD/CAM software. Ensure the software is user-friendly and supports the complexity of your designs. Reliable software compatibility streamlines the design-to-production process, reducing errors and boosting productivity.
Focus on Ease of Use
Ease of use is vital, especially for operators with limited CNC experience. Look for intuitive controls, detailed user manuals, and automated features such as tool changers. Simple operation reduces downtime, enhances efficiency, and ensures quicker project turnaround times.
Review Cutting Speeds and Feed Rates
Fast cutting speeds and feed rates increase productivity, but they should not compromise precision. Evaluate whether the machine can sustain high-speed operation while maintaining the quality of cuts, particularly for repetitive or high-volume tasks.
Inspect Maintenance Requirements
A machine with low maintenance needs is both cost-effective and time-saving. Check for easily accessible components, simple calibration processes, and the availability of replacement parts. A reliable machine minimizes downtime and ensures smooth operation over its lifespan.
Set a Realistic Budget
Balance your investment with the features you need. While budget-friendly options may seem appealing, premium machines often provide better durability, higher precision, and advanced features, ensuring a greater return on investment in the long run.
Look for Advanced Features
Optional features like automatic tool changers, dust collection systems, and safety mechanisms can greatly enhance the functionality and efficiency of your CNC router. Identify which add-ons align with your workflow and production needs for optimal performance.
Research Support and Warranty
A good manufacturer offers robust customer support and a reliable warranty. Comprehensive training, troubleshooting assistance, and easy access to technical help can save time and prevent costly delays. Opt for a trusted brand to ensure peace of mind and dependable service.
What Materials Can the 3-Axis CNC Router Cut?
A 3-axis CNC router is a versatile tool capable of cutting, engraving, and shaping a wide range of materials with precision and efficiency. These machines are designed to handle both soft and hard materials, making them ideal for diverse industries such as woodworking, metal fabrication, and plastics manufacturing. Commonly processed materials include wood, aluminum, acrylic, foam, composites, and even softer metals.
Whether you’re crafting intricate designs in hardwood, creating prototypes from plastic sheets, or milling lightweight metals, a 3-axis CNC router delivers consistent results. Its adaptability allows users to switch between materials with ease, optimizing workflow and enabling the production of everything from decorative pieces to functional components.
Application Industry
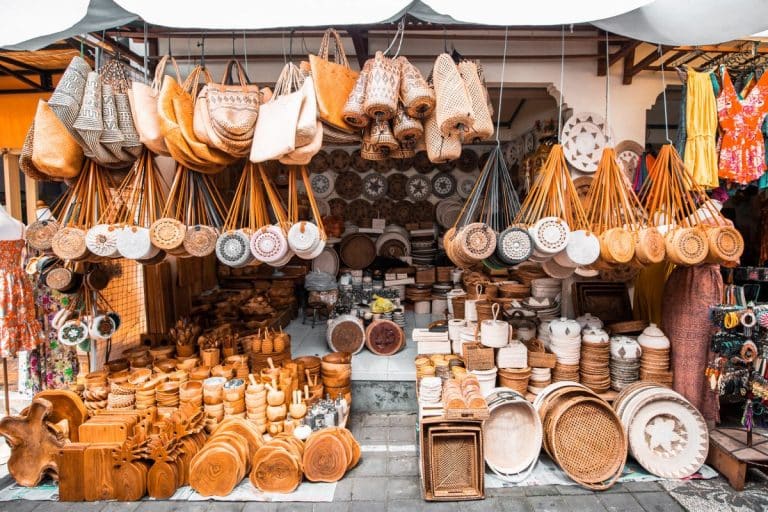
Handicraft Industry
The application of CNC routers in the handicraft industry transcends tradition and opens new doors to creativity while retaining the essence of handcrafted excellence.
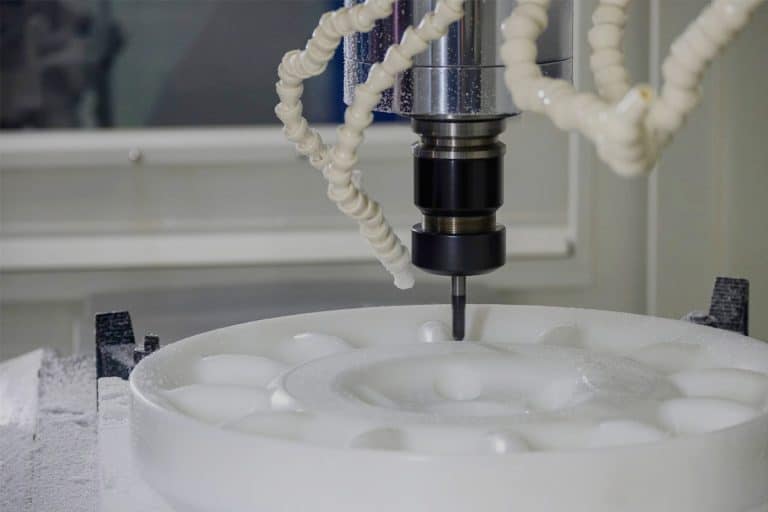
Plastic Fabrication Industry
The CNC router is capable of precision engraving, routing, and cutting of various types of plastics, allowing manufacturers to easily implement complex designs and meet strict specifications.
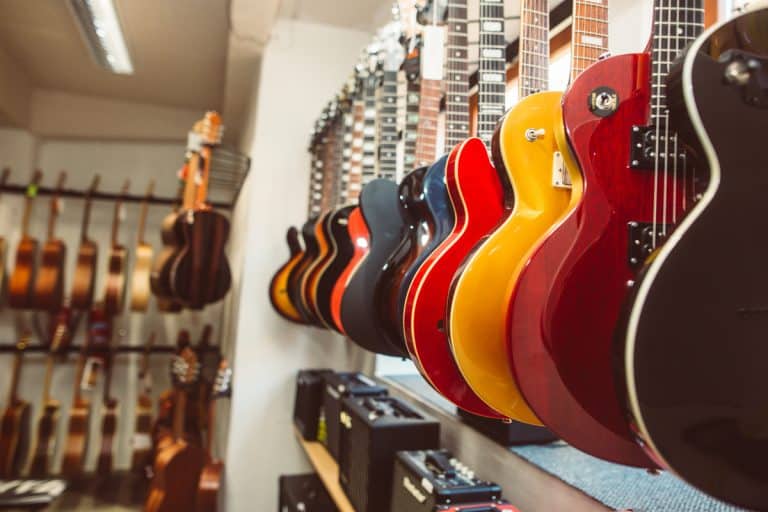
Musical Instrument Industry
The CNC router operates with unparalleled precision and efficiency, transforming raw materials into finely detailed components that give each instrument its unique character and sound.
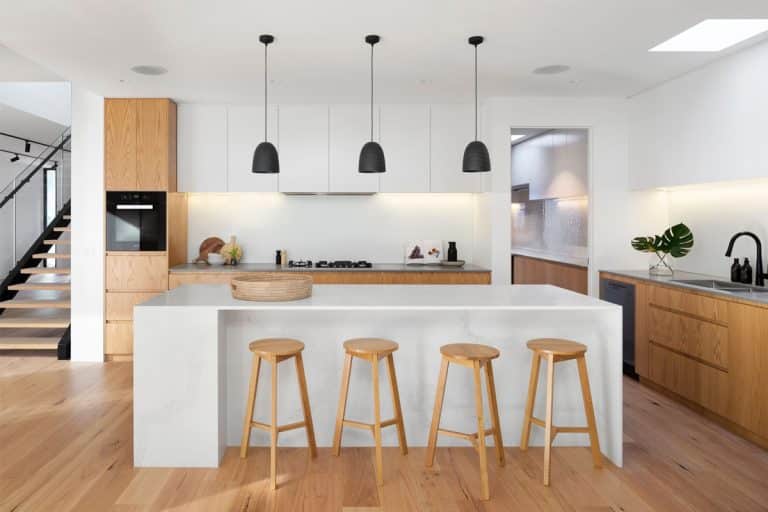
Furniture Manufacturing
With its ability to cut, engrave, and shape materials with unparalleled precision, CNC routers have opened up a world of opportunities for designers and manufacturers in the furniture industry.
Blog
What Cooling Methods Are Needed for Metal CNC Routers?
This article explores the key cooling methods used in metal CNC routers and provides practical insights into selecting the right cooling system for your specific machining environment.
Read More
What Causes CNC Router Spindle Overheating?
In this article, we'll explore the common reasons why CNC router spindle temperatures rise beyond safe limits and provide practical solutions to help you prevent or fix the issue before ...
Read More
What is CNC Router Homing and Why is It Important?
CNC router homing is a fundamental process. In this article, we'll break down what CNC router homing is, how it works, and why it's an indispensable part of every machining ...
Read More
What Should I Consider When Buying a CNC Router from an Overseas Supplier?
In this guide, we’ll walk you through the key considerations when buying a CNC router from an overseas supplier to help you make a confident and informed decision.
Read More
Frequently Asked Questions
How Do 3-Axis CNC Routers Work?
3-axis CNC routers operate by moving a cutting tool along three primary axes: X (horizontal), Y (vertical), and Z (depth). This allows the tool to precisely cut, engrave, or shape materials in three dimensions. The process begins with a design created in CAD (Computer-Aided Design) software, which is then converted into machine-readable instructions via CAM (Computer-Aided Manufacturing) software.
The CNC router’s controller interprets these instructions and directs the movements of the spindle, which houses the cutting tool. The material is secured on the work table, and the tool moves across the axes to carve out the programmed design. This setup enables the creation of intricate and accurate cuts on a wide range of materials.
What Are 3-Axis CNC Routers Used For?
3-axis CNC routers are versatile machines used across various industries for precision cutting, engraving, and shaping. They are commonly employed in woodworking to create intricate furniture designs, cabinetry, and decorative carvings. In metal fabrication, they handle softer metals like aluminum for machining components and prototypes.
These CNC routers are also popular in plastics manufacturing, where they cut and shape acrylics, PVC, and other polymers for signage, displays, and product enclosures. In model making and prototyping, they bring complex designs to life with precision. Additionally, hobbyists and artists use them for crafting, engraving, and custom designs. Their flexibility makes them a go-to solution for both functional and artistic applications.
How Much Are 3-Axis CNC Routers?
The cost of a 3-axis CNC router varies based on its type, features, and intended application:
- Hobby CNC Routers: $3,000 – $5,000. Affordable and compact, these are ideal for DIY enthusiasts and small projects.
- Industrial CNC Routers: $4,000 – $7,000. Built for high-volume production, offering durability and precision.
- ATC CNC Routers: $10,000 – $15,000. Equipped with automatic tool changers for efficiency in complex tasks.
- Stone CNC Routers: $5,500 – $7,000. Designed specifically for engraving and cutting stone materials.
- Metal CNC Routers: $4,000 – $12,000. Suitable for cutting and milling metals like aluminum and brass.
How Precise Are 3-Axis CNC Routers?
3-axis CNC routers are renowned for their precision, with typical tolerances ranging from 0.001 to 0.005 inches (0.025 to 0.127 mm), depending on the machine’s quality and setup. This level of accuracy makes them ideal for detailed cutting, engraving, and shaping tasks in industries like woodworking, plastics, and light metal fabrication.
Key factors influencing precision include the machine’s rigidity, spindle quality, and drive systems (e.g., ball screws or linear guides). Regular calibration, proper maintenance, and using high-quality cutting tools further ensure consistent results. While 3-axis CNC routers are not as precise as some multi-axis machines, they offer more than enough accuracy for most applications.
How to Safely Operate 3-Axis CNC Routers?
Operating a 3-axis CNC router safely requires proper preparation, adherence to safety protocols, and regular maintenance. Here are key guidelines:
- Wear Personal Protective Equipment (PPE): Always wear safety goggles, hearing protection, and appropriate clothing to protect against debris, noise, and accidental contact.
- Ensure Proper Training: Familiarize yourself with the machine’s user manual and operating procedures. Adequate training helps prevent accidents and ensures efficient operation.
- Secure the Workpiece: Use clamps or a vacuum table to firmly hold the material in place, preventing shifting during operation.
- Inspect the Machine: Regularly check for loose bolts, worn parts, and proper alignment of components. Replace damaged tools immediately.
- Set Correct Parameters: Input appropriate feed rates, spindle speeds, and cutting depths to avoid tool breakage and ensure safe operation.
- Maintain a Clean Workspace: Remove dust and debris regularly, as accumulated materials can pose fire hazards and impact precision.
- Use Dust Collection Systems: Proper ventilation and dust collection minimize exposure to harmful particles and keep the machine running efficiently.
- Avoid Manual Adjustments During Operation: Never attempt to adjust or touch the workpiece, tool, or router while the machine is running.
- Activate Emergency Stops: Ensure the emergency stop button is functional and easily accessible in case of unexpected issues.
- Monitor Operations: Stay attentive while the machine is running to identify and address problems promptly. Never leave the machine unattended.
How to Maintain 3-Axis CNC Routers?
Proper maintenance of a 3-axis CNC router is crucial for ensuring its longevity, accuracy, and efficient performance. Regular maintenance helps prevent breakdowns, reduce downtime, and improve cutting precision. Here are some essential maintenance steps:
- Clean the Machine Regularly: Remove dust, debris, and swarf from the machine after each use to prevent buildup that can affect the router’s performance. Clean the rails, spindle, and work area to maintain smooth operation.
- Lubricate Moving Parts: Apply lubrication to the linear guides, ball screws, and other moving components to reduce friction and wear. Use high-quality lubricants recommended by the manufacturer.
- Inspect and Replace Worn Tools: Regularly check the condition of cutting tools. Replace any dull or damaged tools to maintain cutting quality and avoid damaging the workpiece or the machine.
- Check Alignment and Calibration: Ensure the machine is properly aligned. Perform regular checks on the machine’s axes to maintain accuracy. Misalignment can lead to poor cut quality and reduced precision over time.
- Tighten Loose Parts: Periodically inspect all fasteners and parts to ensure they are securely tightened. Loose components can affect machine accuracy and safety.
- Examine Electrical Components: Check wiring, connectors, and control panels for any signs of wear or damage. Any electrical issues should be addressed immediately to prevent operational failures.
- Monitor Spindle Health: Regularly check the spindle for signs of wear, overheating, or unusual vibrations. Proper spindle maintenance is key to ensuring smooth cutting and avoiding tool damage.
- Test Emergency Stop Functionality: Verify that the emergency stop button and other safety features are functioning properly before each use.
- Perform Software and Firmware Updates: Keep your CNC router’s software and firmware up to date. This ensures that the machine operates with the latest features and improvements, preventing software-related malfunctions.
- Inspect Cooling Systems: If the machine uses a cooling system, such as for cooling the spindle, ensure that it’s clean and operational. Proper cooling prevents overheating and prolongs the life of components.
What Customer Support Do 3-Axis CNC Routers Provide?
3-Axis CNC Routers come with reliable customer support options to ensure smooth operation and user satisfaction:
- Free Online Technical Support: Customers can access complimentary technical assistance through online platforms, including email, chat, or video support. This service is ideal for troubleshooting, software setup, or resolving operational issues remotely.
- Paid On-Site Training: For users requiring hands-on guidance, on-site training sessions are available at an additional cost. These sessions cover installation, operation, and maintenance to ensure optimal use of the machine.
What Is The Warranty Period of 3-Axis CNC Routers?
Our CNC router is backed by a comprehensive warranty designed to give you peace of mind and protect your investment:
- 3-Year Warranty for the Entire Machine: This full warranty covers any defects or malfunctions in the machine as a whole, ensuring reliable performance and longevity over time.
- 5-Year Warranty for Core Components: Key components essential for optimal machine operation are covered for 1.5 years. This includes parts that may experience wear and tear with regular use, ensuring you have support for the most vital parts of the machine.