CNC Router
-
AKM1325 CNC Router
Rated 5.00 out of 5$4,800.00 Add to cart -
AKM1530 CNC Router
Rated 5.00 out of 5$5,400.00 Add to cart -
AKM2030 CNC Router
Rated 5.00 out of 5$6,000.00 Add to cart -
AKM2040 CNC Router
Rated 5.00 out of 5$6,500.00 Add to cart -
AKM-C1 CNC Router
Rated 5.00 out of 5$10,500.00 Add to cart -
AKM-C2 CNC Router
Rated 5.00 out of 5$13,400.00 Add to cart -
AKM-C3 CNC Router
Rated 5.00 out of 5$18,100.00 Add to cart -
AKM1325C CNC Router
Rated 5.00 out of 5$13,400.00 Add to cart -
AKM1530C CNC Router
Rated 5.00 out of 5$14,000.00 Add to cart -
AKM2030C CNC Router
Rated 5.00 out of 5$14,600.00 Add to cart -
AKM2040C CNC Router
Rated 5.00 out of 5$15,000.00 Add to cart -
AKM-4A1 CNC Router
Rated 5.00 out of 5$11,800.00 Add to cart
Tips For Choosing The Right CNC Router
Identify Your Application Needs
Select the Appropriate Table Size
Evaluate Cutting Speed and Performance
Ensure Material Compatibility
Prioritize Precision and Accuracy
Consider Spindle Power
Check Software Compatibility
Opt for User-Friendly Features
Assess Build Quality
Evaluate Maintenance Requirements
Stay Within Your Budget
Research Support and Warranty
Advantages of CNC router
Exceptional Precision and Accuracy
CNC routers provide unmatched precision, ensuring intricate designs and exact cuts with minimal error. Advanced control systems and automated toolpaths ensure every project meets exact specifications, making them ideal for industries requiring tight tolerances and complex geometries.
Enhanced Productivity
By automating repetitive and time-consuming tasks, CNC routers significantly increase productivity. Their high-speed operation and ability to work continuously without fatigue help businesses meet tight deadlines while maintaining superior quality output.
Versatility Across Materials
CNC routers are compatible with a wide range of materials, including wood, plastics, metals, and composites. This flexibility allows users to handle diverse projects with a single machine, making them suitable for industries from woodworking to automotive manufacturing.
Reduced Material Waste
CNC routers optimize material use by following precise toolpaths and minimizing errors. This reduces waste, lowers material costs, and supports environmentally sustainable practices, especially in industries where raw material efficiency is critical.
Consistency and Reproducibility
CNC routers can reproduce designs with consistent accuracy across multiple units. This makes them ideal for mass production or creating identical components, ensuring every product meets the same high-quality standards.
User-Friendly Technology
Modern CNC routers come equipped with intuitive software and user-friendly interfaces, making them accessible to both beginners and experienced operators. This reduces the learning curve and allows for seamless integration into workflows.
Time-Saving Capabilities
CNC routers automate complex tasks and execute them faster than manual methods. With high cutting speeds and efficient processes, businesses can complete projects more quickly, boosting overall operational efficiency.
Improved Operator Safety
By automating potentially hazardous tasks, CNC routers reduce direct human interaction with sharp tools. Safety features like emergency stop buttons and enclosed designs further protect operators, creating a safer work environment.
Scalability for Growing Businesses
CNC routers allow businesses to scale production efficiently. Their ability to handle large volumes of work without compromising quality supports business growth and higher output demands over time.
Enhanced Design Flexibility
CNC routers empower users to execute intricate and custom designs with ease. Their compatibility with CAD software allows for the creating of detailed, innovative projects that are difficult or impossible to achieve manually.
Durability and Low Maintenance
Built with high-quality components, CNC routers are designed for long-term performance. Routine maintenance such as cleaning and lubrication is straightforward, ensuring reliable operation and reducing long-term costs.
Cost Efficiency Over Time
Despite initial costs, CNC routers save money through reduced labor, material optimization, and faster project completion. These savings translate into improved profitability and a quicker return on investment for businesses, making CNC routers a valuable asset.
What Materials Can The CNC Router Cut?
Application Industry
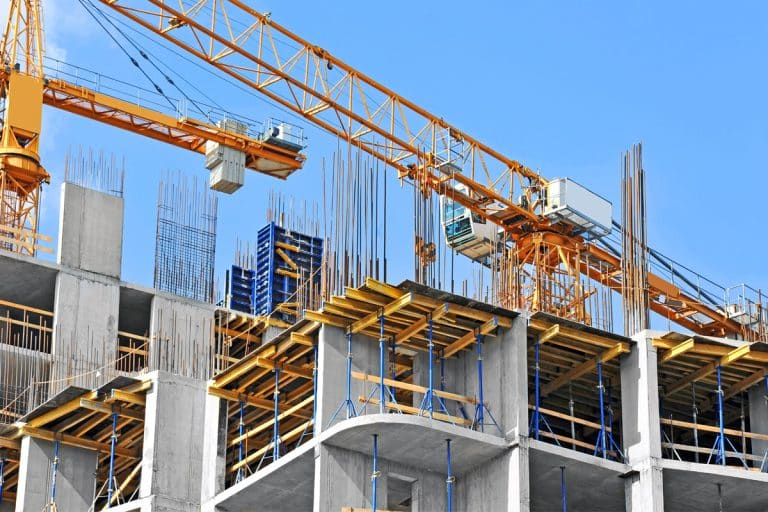
Construction Industry
The integration of CNC routers into construction workflows has ushered in a new era characterized by meticulous detailing, rapid prototyping, and improved material utilization.
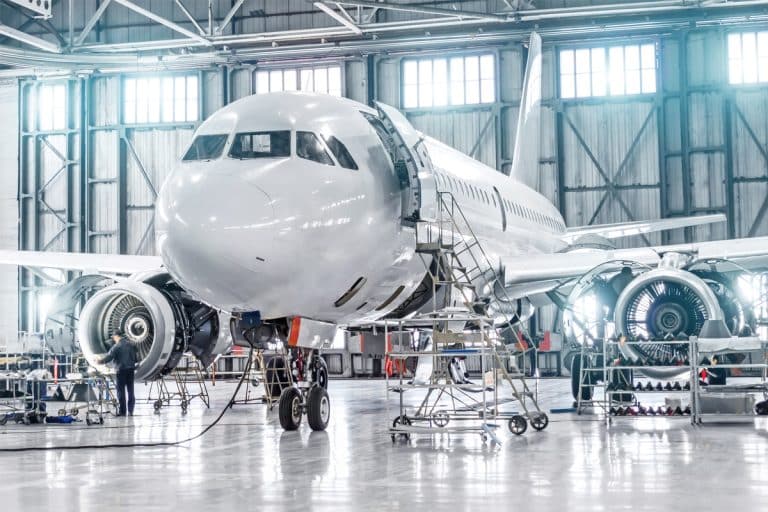
Aerospace Industry
The CNC router is widely used in aerospace engineering due to its unparalleled ability to carve complex designs, manufacture complex parts, and ensure tight tolerances.
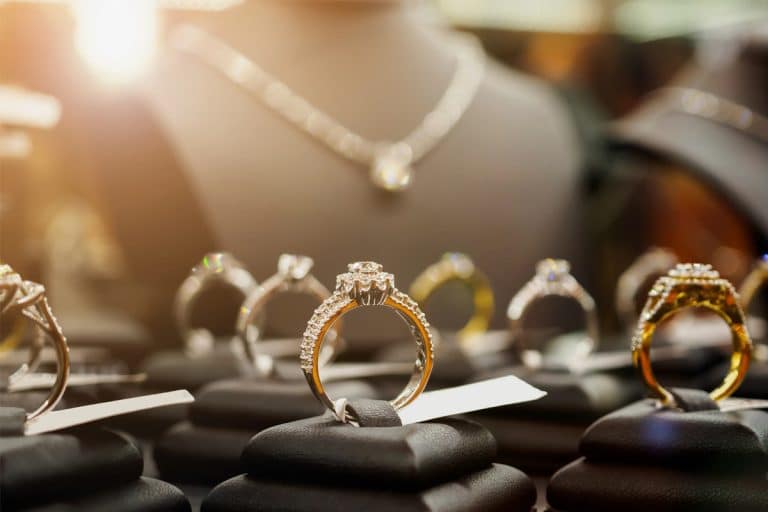
Jewelry Industry
The CNC router revolutionize the way fine jewelry is designed and made by delivering unparalleled precision and efficiency and producing intricate designs with meticulous attention to detail.
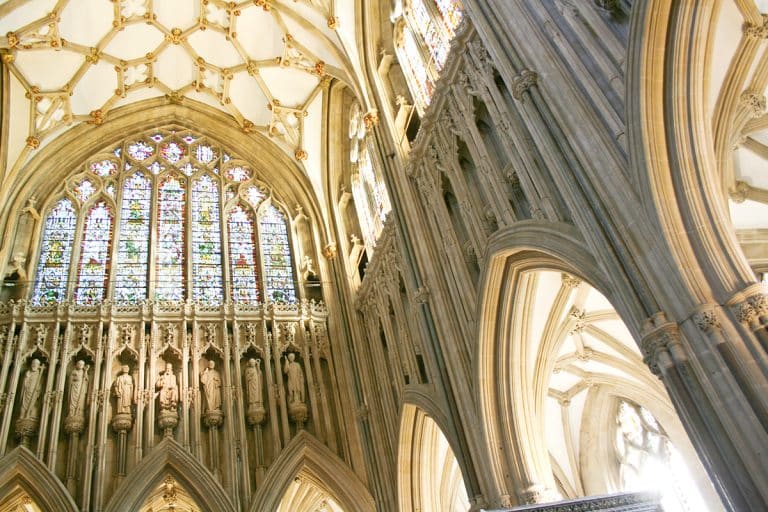
Stone Carving Industry
The integration of CNC routers into the stone carving industry is not only revolutionizing the way craftsmen carve, it is also redefining the boundaries of artistic possibilities in this ancient practice.
Blog
What Power CNC Router Spindle Should I Choose?
How to Choose the Right Stone CNC Router for Your Workshop?
Best Budget CNC Router for Making Outdoor Signs?
How to Maintain and Troubleshoot the ATC CNC Router?
Frequently Asked Questions
What does a CNC router do?
- Cutting and Shaping: CNC routers can create complex cuts, contours, and shapes in materials like wood, plastic, metal, and foam.
- Engraving and Carving: They are used to etch intricate patterns, designs, or text onto surfaces with high precision.
- Drilling and Grooving: Ideal for creating clean, uniform holes, slots, or channels in materials.
- Prototyping and Mass Production: They replicate designs consistently, making them valuable for both one-off projects and large-scale manufacturing.
How much does a CNC router cost?
- Hobby CNC Routers
- Cost: Around $3,000 to $8,000
- Description: Hobby CNC routers are designed for DIY enthusiasts, hobbyists, and small-scale workshops. These machines are compact and lightweight, suitable for light-duty tasks like woodworking, plastic carving, and foam cutting.
- Features: Basic precision, smaller working areas, and limited power. Typically, they don’t support advanced automation or handle dense materials like metals.
- Applications: Personal projects, home decoration, crafting, and prototyping.
- Standard 3-Axis CNC Routers
- Cost: Approximately $5,000 to $7,000
- Description: A versatile and widely used type of CNC router, the 3-axis model moves in the X, Y, and Z planes. It’s ideal for general-purpose cutting, engraving, and carving on flat surfaces.
- Features: Moderate power, standard table sizes, and good precision for small to medium-scale projects. Supports basic materials like wood, plastics, and light metals.
- Applications: Small businesses, sign-making, furniture production, and custom crafting.
- ATC (Automatic Tool Changer) CNC Routers
- Cost: Approximately $11,000 to $22,000
- Description: These machines are equipped with an Automatic Tool Changer (ATC) system, allowing them to switch between tools during operation without manual intervention. This feature enhances efficiency and productivity in complex projects.
- Features: Advanced tool management, high cutting speeds, and support for heavier workloads and diverse materials. Often paired with industrial-grade spindles for precision.
- Applications: Industrial manufacturing, cabinetry, furniture production, and projects requiring multiple tool changes.
- 4-Axis CNC Routers
- Cost: Approximately $13,000 to $23,000
- Description: The 4-axis CNC router introduces a rotational axis, enabling it to work on curved surfaces and cylindrical objects. This makes it suitable for creating more intricate 3D designs.
- Features: Supports cutting and carving on multiple planes, moderate to high spindle power, and high precision. Can work with wood, plastics, and metals.
- Applications: Artistic projects, mold-making, sign-making, and creating decorative elements on furniture or sculptures.
- 5-Axis CNC Routers
- Cost: Approximately $63,000 to $75,000
- Description: These advanced machines allow for simultaneous movement across five axes, making them ideal for creating complex geometries and intricate 3D designs. Often used in high-end industrial applications requiring extreme precision.
- Features: Exceptional versatility, cutting-edge technology, and the ability to handle challenging tasks like undercutting and sculpting dense materials.
- Applications: Aerospace, automotive, advanced manufacturing, and high-precision prototyping.
- Rotary Axis CNC Routers
- Cost: Approximately $3,500 to $10,000
- Description: Rotary axis CNC routers specialize in working with cylindrical objects, such as poles, tubes, or columns. They are perfect for detailed carving or engraving on round surfaces.
- Features: A dedicated rotary axis attachment, moderate to high precision, and support for diverse materials, including wood, foam, and lightweight metals.
- Applications: Creating decorative columns, artistic carvings, and round furniture elements.
- Multi-Head CNC Routers
- Cost: About $7,000 to $12,000
- Description: Multi-head CNC routers feature multiple spindles that can work simultaneously, allowing for faster production and increased efficiency. These are particularly useful for projects requiring repetitive cuts or mass production.
- Features: Multiple cutting heads, moderate to high power, and the ability to handle several identical parts in one operation.
- Applications: Mass production of furniture parts, signage, and repetitive designs.
Why are CNC routers so expensive?
- High-Quality Components: CNC routers are built with durable and high-performance parts to ensure precision, longevity, and reliability. Key components like spindles, stepper or servo motors, linear guides, and ball screws are costly but essential for smooth, accurate operation and repeatability.
- Precision Engineering: CNC routers are designed for high-precision tasks, often with tolerances as tight as fractions of a millimeter. Achieving such accuracy requires meticulous engineering, superior manufacturing processes, and rigorous quality control, all of which add to the cost.
- Advanced Software Integration: The software used to control CNC routers, such as CAD/CAM programs, is often complex and expensive to develop. This software translates digital designs into machine-readable instructions and requires compatibility with multiple file formats and precise toolpath generation, adding to the overall price.
- Versatility Across Materials: CNC routers are engineered to work with a wide range of materials, from soft woods and plastics to metals and composites. This versatility requires powerful spindles, adaptable cutting tools, and robust designs that can withstand high forces during operation.
- Automation Features: Modern CNC routers often come with advanced automation features, such as:
- Automatic Tool Changers (ATC): Streamline processes by switching tools automatically during operation.
- Vacuum Tables: Secure materials during cutting, improving precision and efficiency.
- Dust Collection Systems: Enhance safety and reduce cleanup efforts.
- Large and Durable Framework: CNC routers need a stable, vibration-resistant frame, often made from steel or aluminum, to maintain precision during operation. The materials and construction techniques used to ensure durability and stability are expensive.
- Research and Development: Manufacturers invest heavily in research and development to improve machine accuracy, speed, efficiency, and compatibility with the latest materials and technologies. These R&D costs are factored into the price of the machines.
- Customization Options: CNC routers often allow for extensive customization, such as larger working areas, additional axes, or specialized tool heads. While this adaptability is a significant advantage, it increases the cost due to specialized design and manufacturing requirements.
- Labor and Manufacturing Costs: CNC routers are manufactured using precise machining and assembly processes, often requiring skilled labor and specialized equipment. This labor-intensive production process adds to the cost, especially for industrial-grade machines.
- Import Duties and Shipping: For CNC routers imported from overseas, shipping fees, import taxes, and tariffs can contribute significantly to the price. Larger machines are particularly expensive to transport due to their weight and size.
- After-Sales Support and Warranty: Reputable CNC router manufacturers offer robust customer support, training, and comprehensive warranties. These services add value but also contribute to the overall cost of the machine.
- Scalability and Longevity: While the upfront cost is high, CNC routers are built to handle demanding workloads and last for years with proper maintenance. Their ability to scale production and provide consistent results over time makes them a worthwhile, long-term investment.
What is the lifespan of a CNC router?
- Build Quality
- High-End Models: Industrial-grade CNC routers, built with robust materials like steel or aluminum and precision-engineered components, often have a longer lifespan. These machines are designed to withstand heavy, continuous use.
- Entry-Level Models: Hobby-grade or lower-cost routers may have a shorter lifespan due to less durable materials and components.
- Frequency and Type of Use
- Heavy-Duty Use: CNC routers used in industrial or high-volume production environments experience more wear and tear and may need component replacements sooner.
- Light Use: Machines used occasionally for hobby projects or small-scale tasks can last significantly longer, as they endure less operational stress.
- Maintenance
- Lubrication: Regularly lubricating moving parts reduces friction and wear.
- Cleaning: Keeping the machine free of dust, debris, and residue prevents damage to components.
- Component Replacements: Timely replacement of worn-out parts like spindle bearings, belts, or cutting tools ensures smooth operation.
- Calibration: Routine calibration maintains precision and reduces stress on components.
- Operating Environment
- Clean and Stable Conditions: Operating in a controlled, clean environment minimizes exposure to dust, moisture, and temperature fluctuations, extending the machine’s life.
- Harsh Conditions: Machines exposed to high humidity, dust, or extreme temperatures may experience faster wear and tear.
- Component Durability
- Spindles: Typically last 2,000 to 10,000 hours of use, depending on the type and quality.
- Motors and Drives: High-quality motors can last several years with proper maintenance.
- Technological Advancements
- Key Tips to Maximize Lifespan
- Follow the manufacturer’s maintenance schedule.
- Use the machine within its specified limits (e.g., material type, cutting speed, spindle power).
- Invest in high-quality replacement parts when needed.
- Store the machine in a clean and stable environment.
- Train operators to use the machine correctly to avoid unnecessary wear.
What are the risks of using a CNC router?
- Physical Injuries
- Contact with Moving Parts: Accidental contact with the router’s spinning spindle or moving axes can cause severe injuries.
- Sharp Cutting Tools: Handling router bits without care during setup or changes can result in cuts or punctures.
- Flying Debris: Material fragments, especially from hard materials, can be ejected at high speeds, causing eye or skin injuries.
- Respiratory Risks
- Dust and Particulate Matter: CNC routers generate significant dust, especially when cutting wood, MDF, or plastics. Prolonged exposure can lead to respiratory problems.
- Toxic Fumes: Some materials release harmful fumes when cut, such as treated wood or certain plastics.
- Electrical Hazards
- Electrical Shocks: CNC routers operate on high voltage, posing risks of electric shock during improper handling or faulty wiring.
- Short Circuits or Fires: Poor maintenance or damage to electrical components can lead to dangerous malfunctions.
- Tool and Equipment Failures
- Tool Breakage: Overloading the cutting tool or using the wrong tool for the material can cause it to break, leading to equipment damage or injuries.
- Machine Malfunctions: Improper maintenance or excessive wear on components like spindles, belts, or drives can lead to operational failure.
- Fire and Heat Risks
- Friction Ignition: Improper speed or excessive friction during cutting can ignite flammable materials, such as wood dust or plastic.
- Overheating: Prolonged use without breaks can cause the spindle or motor to overheat.
- Programming and Operational Errors
- Incorrect Toolpaths: Programming mistakes or design errors can cause crashes, ruining materials, breaking tools, or damaging the machine.
- Operator Errors: Inexperienced or untrained operators may misuse the machine, leading to safety risks or poor results.
- Noise Hazards
- CNC routers can produce high noise levels, especially during high-speed operations, which may cause hearing damage over time.
- Ergonomic Strain
- Repeated manual handling of heavy materials for loading and unloading can lead to musculoskeletal strain or injuries.
- Environmental Contamination
- Improper Disposal: Waste materials like dust, chips, and toxic residues can harm the environment if not handled properly.
- Lack of Emergency Response Preparedness
- In emergencies, such as a fire, tool breakage, or machine crash, a lack of preparedness can lead to injuries or damage.
What is the difference between a CNC router and a CNC machine?
- Definition
- CNC Router: The CNC router is a specific type of CNC machine designed primarily for cutting, engraving, and shaping softer materials such as wood, plastic, foam, and sometimes soft metals like aluminum.
- CNC Machine: The CNC machine is a broader term encompassing all types of computer numerical control equipment, including routers, mills, lathes, plasma cutting machines, and laser cutting machines, each tailored for different machining tasks.
- Applications
- CNC Router: CNC routers excel in tasks requiring intricate designs or large, flat workpieces. Common applications include furniture making, cabinetry, sign-making, and decorative carvings. They are ideal for lightweight projects and high-speed processing.
- CNC Machine: CNC machines like mills and lathes are used for heavy-duty tasks such as manufacturing mechanical parts, aerospace components, and precision engineering. They handle complex shapes and tighter tolerances, making them suitable for industrial and engineering applications.
- Material Compatibility
- CNC Router: Typically used for softer materials like wood, plastics, composites, and lightweight metals. Routers are optimized for speed and large-scale material processing.
- CNC Machine: Designed to handle both soft and hard materials, including metals like steel, titanium, and brass. CNC machines are more powerful and suitable for dense materials that require significant cutting force.
- Design and Construction
- CNC Router: Features a gantry-style design with a large, flat table to accommodate large sheets of material. It is built for high-speed operations with lighter cutting forces.
- CNC Machine: Includes rigid and often enclosed designs to withstand higher torque and force. Examples include vertical and horizontal mills or lathes that provide precision and durability for heavy-duty operations.
- Precision and Tolerance
- CNC Router: Offers moderate precision, suitable for tasks where tolerances range around ±0.1mm to ±0.5mm. It prioritizes speed and versatility over extreme precision.
- CNC Machine: Provides high precision and tight tolerances, often down to ±0.01mm or better, making it ideal for applications requiring meticulous accuracy.
- Speed and Power
- CNC Router: Operates at higher speeds, often exceeding 20,000 RPM, but with lower torque. This allows for the fast processing of lightweight materials.
- CNC Machine: Operates at slower speeds, usually between 4,000–12,000 RPM, with significantly higher torque for cutting through dense and tough materials.
- Cost
- CNC Router: Generally less expensive due to its focus on lighter-duty tasks. Hobby-grade routers start at around $3,000, while industrial models can cost up to $30,000.
- CNC Machine: More expensive because of their advanced capabilities and durability. CNC mills or lathes can range from $20,000 to over $200,000.
- Use Cases
- CNC Router: Best for artistic, creative, or lightweight industrial projects like signage, furniture, or foam prototypes.
- CNC Machine: Essential for engineering-focused tasks like manufacturing metal parts for aerospace, automotive, or medical industries.
What PPE is needed for a CNC router?
- Eye Protection
- Type: Safety goggles or safety glasses with side shields.
- Purpose: Protects eyes from flying debris, dust, and chips that may be ejected during cutting.
- Additional Option: A full-face shield can provide extra protection for the entire face, particularly during high-speed operations or when working with brittle materials.
- Respiratory Protection
- Type: Dust masks (N95 or higher) or respirators with particulate filters.
- Purpose: Prevents inhalation of fine dust and harmful fumes, especially when cutting materials like MDF, plastics, or treated wood.
- Additional Tips: For operations involving toxic fumes, use a respirator with chemical cartridges and ensure proper ventilation in the workspace.
- Hearing Protection
- Type: Earplugs or earmuffs with a Noise Reduction Rating (NRR) suitable for high-decibel environments.
- Purpose: CNC routers can produce noise levels above safe thresholds (85 dB), which can cause hearing damage with prolonged exposure.
- Additional Tips: Choose comfortable hearing protection, especially for long operation sessions, and consider dual protection (earplugs and earmuffs) for extremely noisy environments.
- Hand Protection
- Type: Cut-resistant gloves or work gloves (only for material handling).
- Purpose: Protects hands from cuts, abrasions, and splinters when handling materials or changing tools.
- Important Note: Gloves should never be worn near moving parts or spinning tools to avoid entanglement risks.
- Protective Clothing
- Type: Fitted, long-sleeved clothing or lab coats.
- Purpose: Prevents loose fabric from being caught in the router’s moving parts. Protects skin from dust and minor debris.
- Additional Tips: Avoid loose clothing, scarves, jewelry, or accessories. Secure long hair to avoid entanglement.
- Foot Protection
- Type: Closed-toe, steel-toe, or anti-slip safety shoes.
- Purpose: Protects feet from falling materials or tools and ensures stability on potentially slippery surfaces.
- Additional Tips: Ensure shoes are resistant to oils or coolants commonly found in workshops.
- Optional PPE
- Face Shield: Provides extra protection against large debris or sparks during high-intensity cutting operations. Use in conjunction with safety goggles.
- Heavy-Duty Apron: Protects the torso and clothing from flying chips, debris, and sparks.
- Anti-Slip Footwear: Helps prevent slips in environments with oil, dust, or wet surfaces.
What limitations does a CNC router have?
- Material Constraints
- Limited Hard Material Processing: CNC routers are primarily designed for softer materials like wood, plastics, foam, and light metals such as aluminum. They struggle with harder materials like steel, titanium, or high-strength composites, which require the torque and rigidity of a CNC mill.
- Material Thickness: The thickness of the material a CNC router can handle is limited by its spindle power and gantry clearance.
- Precision and Tolerance
- Lower Tolerances: CNC routers generally provide less precision compared to other CNC machines like mills or lathes. Their tolerances typically range around ±0.1mm to ±0.5mm, which may not be suitable for applications requiring extreme accuracy.
- Vibration Issues: The gantry-style design of CNC routers can introduce vibrations during operation, slightly reducing accuracy, especially for detailed cuts on dense materials.
- Power and Torque
- Lower Cutting Force: CNC routers use high spindle speeds but generate less torque, limiting their ability to cut dense or thick materials efficiently. This makes them unsuitable for heavy-duty machining tasks.
- Shallow Cutting Depths: Routers often require multiple passes to cut through thick or hard materials, increasing production time.
- Durability Under Heavy Use
- Wear and Tear: Prolonged heavy-duty use can lead to faster wear on the spindle, belts, and other components. This is especially true when pushing a CNC router to handle tasks beyond its intended design.
- Component Longevity: The lighter construction of some CNC routers means they are not as durable as CNC mills or industrial-grade machines, particularly in demanding environments.
- Limited Versatility in 3D Machining
- Restricted Axes Movement: Most CNC routers are 3-axis machines, which are great for flat or slightly contoured designs but struggle with complex 3D geometries or undercuts. Advanced 4-axis or 5-axis CNC machines are needed for such tasks.
- Complex Shapes: While CNC routers can produce some 3D designs, they are less capable than CNC mills in achieving detailed, intricate 3D forms.
- Noise and Dust
- High Noise Levels: CNC routers can be noisy, especially during high-speed operations, requiring hearing protection and sound management in the workspace.
- Dust and Debris: Cutting wood, plastics, and similar materials generates significant dust, which requires effective dust collection systems. Without these, the environment can become hazardous and require frequent cleaning.
- Software Limitations
- Learning Curve for CAD/CAM Software: While user-friendly software is available, beginners may face challenges in designing complex toolpaths or translating ideas into executable code.
- File Compatibility: Some CNC routers may not support all file formats or advanced design features, limiting their flexibility in handling complex projects.
- Space Requirements
- Large Footprint: CNC routers, especially those with larger work areas, require significant space in a workshop. This can be a limitation for users with smaller setups.
- Weight and Mobility: Larger machines are heavy and difficult to move, making them less flexible in dynamic work environments.
- Cost of Entry
- Initial Investment: While hobby-grade routers are affordable, high-quality industrial CNC routers can be expensive. Add-ons like dust collection systems, advanced software, and maintenance costs increase the overall expense.
- Maintenance Costs: Replacement of worn items like spindles, belts, and cutting tools adds ongoing costs.
- Operator Expertise
- Skill Requirements: Operating a CNC router effectively requires knowledge of CAD/CAM software, machine calibration, and material properties. Beginners may face a steep learning curve before achieving optimal results.
- Error Sensitivity: Programming errors in toolpaths or material setups can lead to wasted materials, damaged tools, or machine crashes.
- Speed vs. Quality
- Trade-Offs in Cutting Speed: While CNC routers are fast for softer materials, high speeds may compromise cut quality, requiring additional sanding or finishing.
- Surface Finishing: The finishes achieved by CNC routers may require manual polishing or sanding for high-quality results, particularly for complex designs.