- 9-13 Min Read
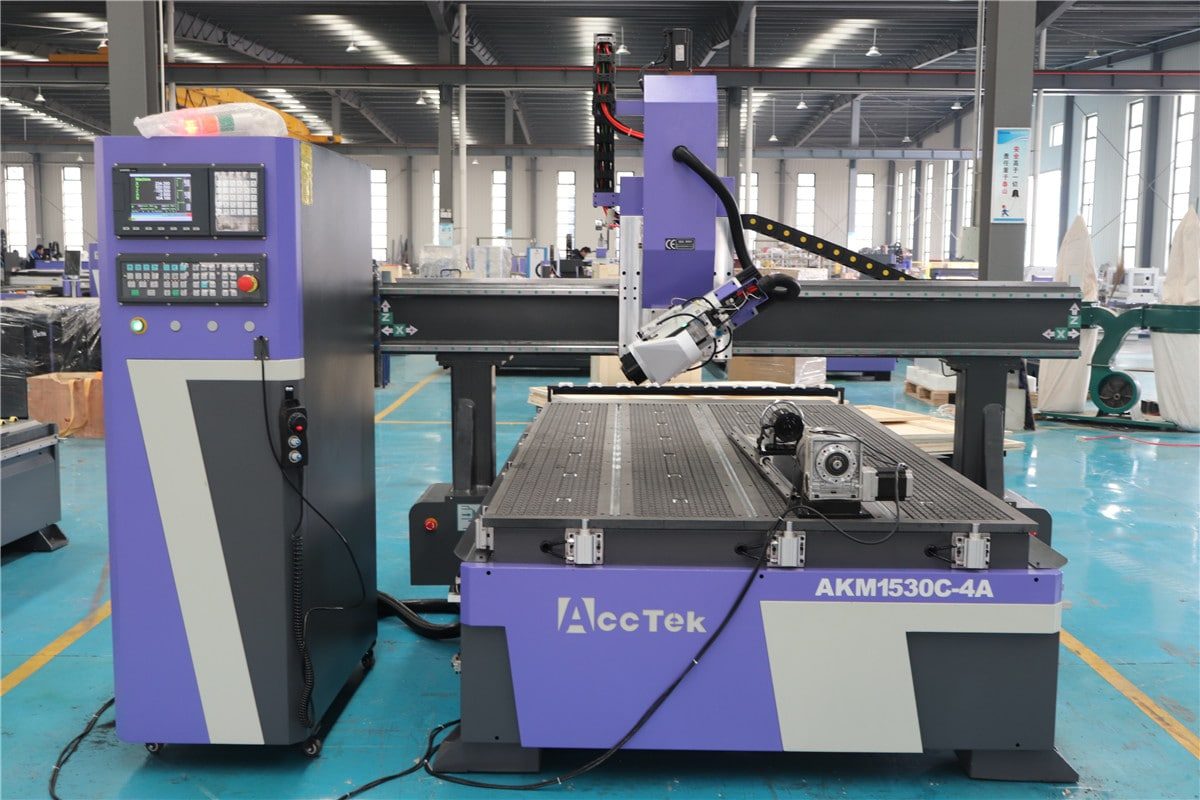
In the realm of modern manufacturing and design, Computer Numerical Control (CNC) routers stand as indispensable tools, revolutionizing the way intricate designs are crafted with precision and efficiency. From woodworking to prototyping, and everything in between, CNC routers have become a cornerstone technology, empowering artisans, engineers, and hobbyists alike to bring their ideas to life with unparalleled accuracy. One of the key factors that make CNC routers such versatile tools is the array of options they support. These options, ranging from materials and cutting tools to software and accessories, offer even more possibilities in shaping the capabilities and applications of these machines. Understanding the breadth of options available can empower users to harness the full potential of their CNC routers, unleashing creativity and unlocking new possibilities in fabrication and design.
In this article, we delve into the diverse range of options that CNC routers support, exploring their implications for different industries and projects. From the fundamentals to advanced features, we aim to provide insights that will inform and inspire, guiding you toward making informed decisions and achieving remarkable results in your CNC endeavors.
What is a CNC Router?
A CNC router is a computer-controlled cutting machine used for cutting various materials such as wood, plastic, composites, foam, and metals. It operates based on instructions from a computer program to precisely cut, carve, engrave, or mill intricate designs and shapes with high accuracy and repeatability. Through the following introduction, let us learn more about CNC router.
What is the purpose of CNC router?
The primary purpose of a CNC router is to automate the cutting process, providing precise and consistent results while minimizing manual labor. CNC routers are widely used in various industries including woodworking, furniture manufacturing, signage, prototyping, aerospace, automotive, and electronics. They enable the production of intricate designs, prototypes, molds, and custom parts with efficiency and accuracy. CNC routers offer benefits such as increased productivity, reduced material waste, and the ability to create complex shapes that would be challenging or impossible to achieve with traditional manual methods.
What components does the CNC Router consist of?
- Frame and Structure: The frame serves as the foundational structure of the CNC router, providing support and stability to the entire system. It is usually made of heavy-duty materials such as steel or aluminum to minimize vibrations and ensure accuracy during cutting operations. The design of the frame can be in the form of a gantry (bridge), moving gantry, or moving table, depending on the specific configuration of the CNC router.
- Control System: The control system of a CNC router comprises a computer or controller that interprets the instructions from CAD (Computer-Aided Design) or CAM (Computer-Aided Manufacturing) software. It translates these instructions into precise movements of theCNC router’s cutting tool along multiple axes (typically X, Y, and Z axis).
- Spindle: The machinespindle is the motorized component responsible for holding and rotating the cutting tool. It may vary in power and speed depending on the materials being processed and the desired cutting requirements. High-speed spindles are commonly used for cutting materials like wood and plastics, while lower speed and higher torque spindles are preferred for cutting metals.
- Linear Motion System: CNC routers utilize a linear motion system to move the cutting tool along the designated paths with precision. This system typically includes rails, bearings, and lead screws or ball screws to facilitate smooth and accurate movement along the X, Y, and Z axes.
- Cutting Tool: The cutting tool, also known as the router bit, is the component that removes material from the workpiece. Router bits come in various shapes, sizes, and materials to suit different cutting applications such as straight cutting, profiling, engraving, or drilling.
- Worktable: The worktable provides a stable surface for securing the workpiece during the cutting process. It may feature clamps, vacuum systems, or other methods of securing the material in place to prevent movement or vibration, ensuring accurate cutting results.
- CAD/CAM Software: CAD/CAM software is used to create digital designs or models of the desired parts or components, as well as to generate toolpaths and G-code instructions that control the movements of the CNC router. This software allows users to design intricate shapes, specify cutting parameters, and optimize toolpaths for efficient material removal.
Standard Ooptions of CNC Routers
When investing in a CNC router, we need to understand the key components and specifications of the machine to make the right choice for production. Although specific specifications and configurations can vary widely between different CNC router models and manufacturers. However, these machines all have certain basic configurations. In this section, we learn about the standard options of CNC routers.
- Axis Configuration: Most CNC routers come in a 3-axis configuration, offering movement along the X, Y, and Z axes. This setup is suitable for basic routing tasks on flat or slightly curved surfaces. 4-axis and 5-axis configurations are available for more complex machining tasks.
- Spindle Options: Standard configurations include a basic spindle with moderate power and speed capabilities, suitable for general-purpose routing tasks. Spindle power typically ranges from 1 to 15 kW for industrial-grade routers, although smaller hobbyist routers may have lower-powered spindles. Spindle speed can range from a few thousand RPM up to 24,000 RPM.
- Bed Size: CNC routers are available in various bed sizes, ranging from small desktop units to large industrial machines. The bed size is typically fixed in standard configurations. For example, common small desktop units are 6090 and 6012, which are 600×900mm and 600mm× Common large industrial machines are 1325 and 1530, namely 1300×2500 and 1500×3000mm. The choice of bed size depends on the intended application and the size of the workpieces to be machined.
- Material Compatibility: Standard CNC routers are designed to work with common materials such as wood, plastics, and composites. The compatibility may vary based on spindle power, cutting tool selection, and bed design.
- Control System: Basic control systems include digital control units for CNC programming, machining control, and toolpath generation. These systems provide essential functionality for operating the CNC router but may lack advanced features.
- Accuracy and Precision Specifications: Standard CNC routers offer moderate levels of accuracy and precision suitable for typical routing tasks. Accuracy may range from ±005 inches to ±0.001 inches, depending on the specific machine and application.
Upgrade Options of CNC Router
To keep pace with evolving machining requirements and industry standards, CNC router owners have various upgrade options at their disposal. Upgrading the individual components of the CNC router is an essential step to enhance machine performance, efficiency, and versatility. By investing in these upgrade options, CNC router owners can stay competitive, adapt to evolving manufacturing requirements, and unlock new opportunities for innovation and growth in their operations. Let’s delve into each aspect:
Spindle
- Spindle Power: Increasing the spindle power is one of the most common upgrade options for CNC routers. Higher spindle power enables the machineto handle tougher materials and achieve faster cutting speeds, resulting in improved efficiency and productivity.
- Spindle Number: Multiple spindles can be configured to accommodate different types of cutting tools, allowing for diverse machining processes to be performed simultaneously. Adding extra spindles to a CNC router expands its capabilities and enables simultaneous machining of multiple parts or operations. This upgrade option is particularly beneficial for increasing throughput and reducing production time.
Additional Cutting Tools
- Rotary Axis: Introducing a rotary axis as an additional component enables the CNC router to perform machining tasks of cylindrical materials. Rotating shafts add flexibility to the CNC router’s capabilities, allowing for a wider range of applications and creative possibilities in machining.
- Cutting Saws: Integrating cutting saws into the CNC router setup expands its functionality to include cutting and trimming operations on various materials such as wood, plastic, and acrylic. Saw blades with different specifications can achieve precise cuts, angles, and profiles.
- Drill Packages: Adding drill packages to the CNC router allows for accurate hole drilling and boring operations on workpieces. These packages typically include drill bits of different sizes and configurations to accommodate various hole diameters and depths.
- Vibrating Knives: Vibrating knives, also known as oscillating knives, are useful for cutting soft and flexible materials such as foam, rubber, and textiles. Adding vibrating knife capabilities to the CNC router enables precise and clean cutting of these materials without fraying or tearing.
- Plasma Cutting Heads: Incorporating plasma cutting heads into the CNC router setup allows for high-speed cutting of metals such as steel, aluminum, and brass. Plasma cutting is ideal for producing intricate shapes and contours in metal sheets and plates.
Machine Bed and Frame
- Improving Bed and Frame Materials: Upgrading the materials used for the bed and frame of the CNC router can enhance rigidity, stability, and durability, resulting in improved machining precision and reliability. Common upgrade options include utilizing high-quality aluminum or steel for the frame and bed construction.
- Improving Bed and Frame Form: Altering the form of the bed and frame of the CNC router can optimize workspace utilization and accessibility, catering to diverse machining needs and spatial constraints. Implementing a sunken workbench design involves recessing the bed into the frame, allowing for easier loading and unloading of workpieces, as well as providing better access to the machining area. Alternatively, adopting a desktop workbench configuration raises the bed above the frame, providing convenient access to the workpiece from all sides and facilitating ergonomic operation and material handling.
Automatic Loading and Unloading Device
Integrating an automatic loading and unloading device streamlines the workflow of the CNC router, minimizing manual intervention and maximizing productivity. This upgrade option typically involves the installation of a robotic arm or conveyor system that can automatically feed raw material to the machine, remove finished parts, and transport them to subsequent processing stations or storage areas. Automatic loading and unloading devices reduce cycle times, optimize material usage, and enhance overall efficiency, making them ideal for high-volume production environments.
Drive System
Upgrading the drive system of the CNC router can improve speed, accuracy, and responsiveness, resulting in smoother motion control and better machining performance. Options for drive system upgrades include replacing conventional stepper motors with more precise servo motors, upgrading to high-precision ball screw or rack and pinion drive mechanisms, or implementing advanced linear motor technology.
ATC (Automatic Tool Changer) Tool Changer
- Fixed Linear Tool Changer: This type of ATC features a linear tool magazine with fixed tool positions. When a tool change is required, the spindle moves to the designated tool position for retrieval or replacement. While simple and reliable, fixed linear tool changers may have limited capacity.
- Follow-Up Linear Tool Changer: A follow-up linear tool changer improves on the fixed linear design by allowing the spindle to move along the tool magazine during tool changes. This enables faster tool selection and reduces idle time between machining operations.
- Disc Tool Changer: Disc tool changers utilize a rotating disc or carousel to store and retrieve cutting tools. With a larger tool capacity compared to linear tool changers, disc changers offer greater flexibility and enable quick tool changes without interrupting the machining process.
Upgrading the ATC system of a CNC router significantly enhances efficiency by reducing tool change times and enabling uninterrupted machining operations.
Firmware Update
Regular firmware updates help maintain the machine’s optimal performance, reliability, and compatibility with new features and technologies. Firmware updates often address bug fixes, performance optimizations, and security enhancements to ensure the smooth and stable operation of the CNC router.
Control Software Enhancement
Enhancing the control software of a CNC router can unlock advanced features, streamline workflow, and improve user productivity. Control software enhancements may include improvements to CAD/CAM integration, toolpath generation algorithms, simulation capabilities, and user interface design. Advanced control software enables users to optimize machining parameters, visualize toolpaths in real-time, and simulate machining processes to detect potential errors or collisions before execution.
Compatibility with Industry Standards
Ensuring compatibility with industry standards facilitates seamless integration with other manufacturing systems, software and peripherals. Upgrading a CNC router to support industry-standard communication protocols such as OPC UA, MTConnect, or EtherCAT facilitates interoperability with other equipment and manufacturing software. Compatibility with industry standards also extends to file formats, ensuring seamless exchange of design files, machining programs, and tooling data between different software applications and CNC machines.
These upgrade options empower users to tackle a wider range of materials and applications, increase productivity, and achieve superior machining results. By carefully considering these upgrade options and selecting the most suitable enhancements for their specific needs, users can unlock the full potential of their CNC routing systems and achieve superior machining results.
How to determine the configuration required for a specific project
Determining the CNC router configuration required for a specific project involves a comprehensive approach. Here’s a detailed guide on how to approach each step:
Understanding Project Requirements
- Begin by thoroughly understanding the specific requirements of the project, including the type of material to be machined, the size and complexity of the workpieces, and any special features or tolerances needed.
- Consider factors such as production volume, machining speed, accuracy requirements, and budget constraints.
Collaborating with CNC Manufacturers
- Work closely with CNC router manufacturers or suppliers to discuss the project requirements and explore available configuration options.
- Seek guidance from manufacturers on selecting the appropriate CNC router model, spindle configuration, axis configuration, and additional features based on the project specifications.
Customizing Tooling and Fixtures
- Customize cutting tools, fixtures, and workholding solutions to match the specific requirements of the project.
- Select cutting tools based on the material properties, machining processes, and desired outcomes. Consider factors such as tool geometry, coating, and material compatibility.
- Design and fabricate custom fixtures or jigs to securely hold and position the workpieces during machining operations, ensuring accuracy and repeatability.
Implementing Project-Specific Software Modules
- Evaluate the need for project-specific software modules or enhancements to optimize CNC router performance and functionality.
- Customize or develop software modules for CAD/CAM integration, toolpath generation, simulation, optimization, and process monitoring tailored to the project requirements.
- Integrate specialized software solutions for complex machining processes, multi-axis machining, or advanced automation features as needed.
Ensuring Customized Safety Compliance
- Prioritize safety compliance by implementing customized safety measures and protocols tailored to the project environment and workflow.
- Conduct a thorough risk assessment to identify potential hazards associated with CNC router operation and develop safety strategies to mitigate risks.
- Install safety features such as interlocks, emergency stop buttons, protective enclosures, and machine guarding to ensure operator safety and compliance with regulatory standards.
Testing and Validation
- Conduct comprehensive testing and validation of the CNC router configuration in real-world operating conditions.
- Perform machining trials using representative workpieces to verify the performance, accuracy, and quality of the machined parts.
- Iterate and make adjustments to the configuration, tooling, software settings, and safety measures based on testing results and feedback.
By following this systematic approach and leveraging the expertise of CNC manufacturers, engineers, and software developers, you can determine the most suitable CNC router configuration for your specific project. Customizing tooling, fixtures, software modules, and safety compliance measures ensures that the CNC router meets the unique requirements and delivers optimal performance and results.
Summarize
As we’ve explored, CNC routers offer a plethora of options to suit various needs and preferences. From different spindle types to diverse cutting tools and configuration upgrades, the flexibility of CNC routers empowers users to unleash their creativity and accomplish intricate designs with precision. However, it’s crucial to remember that the options available may vary depending on the specific make and model of the CNC router. Therefore, it’s advisable to thoroughly research and consult with experts to select the best options for your particular project requirements.
The versatility and capabilities of CNC routers continue to expand, offering endless possibilities for the industrial field. At AccTek CNC, we not only provide users with standard models of CNC routers but also provide customized services. Tell me your needs and AccTek’s professional sales team will provide you with configuration upgrade suggestions. By customizing some options for your machine, you can achieve results that improve accuracy, efficiency, or develop new features. Whether you’re a hobbyist, a professional craftsman, or a manufacturing industry veteran, there’s an AccTek CNC router configuration out there to help bring your ideas to life with efficiency and accuracy. So, contact us to get a customized solution.