A Comprehensive Guide to CNC Router Power Consumption
- 9-13 Min Read
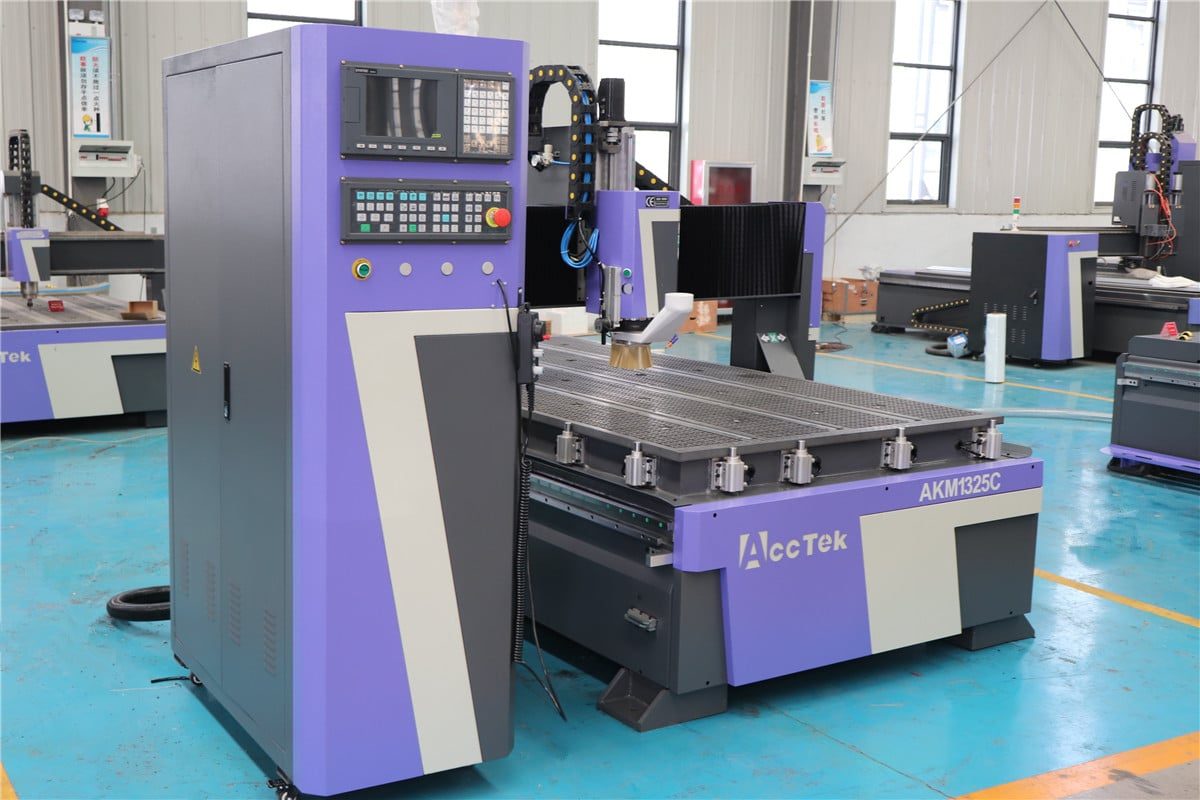
In the ever-evolving landscape of modern manufacturing, Computer Numerical Control (CNC) routers stand as stalwart pillars of precision and productivity. These versatile machines have revolutionized the way industries approach cutting, carving, and shaping various materials. However, like any industrial equipment, CNC routers come with their own set of considerations, one of the most crucial being power consumption. Understanding and optimizing CNC router power consumption can help improve operational efficiency and cost-effectiveness.
This guide seeks to unravel the complexities surrounding CNC router power consumption, offering insights into the factors influencing energy usage, methods for measuring and monitoring consumption, and strategies for optimizing efficiency without compromising productivity or quality. Whether you’re a seasoned industry professional seeking to fine-tune operations or a newcomer navigating the intricacies of CNC machinery, this guide aims to provide you with ways to achieve sustainable and economical manufacturing practices.
Importance of Monitoring Power Consumption
The power consumption of a CNC router refers to the amount of electrical energy it utilizes during its operation. This includes the energy required to drive motors, operate cooling systems, power auxiliary components such as vacuum pumps or dust extraction systems, and run the control electronics. This energy is typically measured in watts (W), kilowatts (kW), or kilowatt-hours (kWh). Understanding and monitoring power consumption is a task that must be performed during the operation of a CNC router. Its importance is specifically reflected in the following aspects:
- Cost Management: Power consumption directly correlates with operational costs. By monitoring power usage, operators can identify inefficiencies and take steps to optimize energy usage, thereby reducing operational expenses.
- Efficiency Optimization: Understanding how much power the CNC router consumes during different operations can help optimize efficiency. By identifying energy-intensive processes or inefficiencies, manufacturers can make adjustments to streamline operations and reduce waste, ultimately improving overall productivity.
- Quality Assurance: Power consumption can sometimes indicate variations in material properties or cutting conditions. Monitoring energy usage alongside other process parameters can help ensure consistent quality in finished products by identifying deviations from optimal operating conditions.
- Equipment Health: Abnormal fluctuations or spikes in power consumption can indicate potential issues with the CNC router’s components. By monitoring power usage patterns, operators can detect potential problems early, allowing for timely maintenance or adjustments to prevent costly downtime and repairs.
- Environmental Impact: Lowering power consumption reduces costs and minimizes manufacturing operations’ environmental footprint. Monitoring energy usage allows businesses to track their carbon footprint and take steps toward sustainability by implementing energy-saving practices.
- Regulatory Compliance: In some regions, there may be regulations or standards governing energy efficiency and emissions. Monitoring power consumption helps ensure compliance with these regulations, avoiding potential fines or penalties.
What are the factors that affect power consumption?
Understanding the intricate dynamics of power consumption in CNC routers involves a comprehensive examination of various operational aspects. Here’s an introduction to the factors affecting power consumption, segmented across critical components and operational phases:
- Spindle Motor: The spindle motor serves as the driving force behind cutting, shaping, and carving operations in CNC routers. Its power rating directly correlates with energy consumption, as higher power motors typically demand more electricity to execute machining tasks efficiently. Factors such as material hardness, cutting depth, and spindle speed influence the workload on the motor, consequently impacting power usage. Additionally, the type of spindle motor (e.g., air-cooled or liquid-cooled) can also impact power usage, as cooling requirements may vary depending on the motor’s design and workload.
- Bed and Axis Motion: Movement along the bed and axes of the CNC router dictates the spatial precision and efficiency of machining operations. Power consumption during motion is influenced by parameters such as acceleration, deceleration, and travel distances. Rapid movements and frequent directional changes can escalate energy demands, particularly if not optimized.
- Cooling System: The cooling system is mainly used to dissipate the heat generated by the spindle motor and other components during operation. Efficient cooling helps maintain component longevity and machining accuracy. However, cooling systems themselves consume power, particularly in environments with elevated ambient temperatures or heavy machining loads.
- Control System: At the heart of every CNC router lies the control system, which governs the execution of machining operations with precision and efficiency. Power consumption associated with the control system arises from various activities, including processing control commands, powering peripherals, and managing communication interfaces. The efficiency of the control system directly affects power usage, with factors such as processor performance, software optimization, and peripheral configurations influencing energy demands.
- Tool Changes: Tool changes represent pivotal moments in CNC machining processes, requiring coordinated movements and operational adjustments. Power consumption during tool changes can vary depending on factors such as tool change speed, tool storage mechanisms, and auxiliary systems involved. Rapid tool changes or inefficient tool management practices can result in spikes in power usage, impacting overall energy efficiency.
- Auxiliary Equipment: The efficient operation of CNC routers often relies on auxiliary equipment like dust collectors and vacuum pumps to maintain cleanliness and workpiece stability. While indispensable, these peripherals contribute to power consumption, particularly during active operation. The energy demands of dust collectors and vacuum pumps can fluctuate based on factors such as duty cycle, airflow requirements, and system efficiency.
- Idle Time and Cutting Time: The idle time, during which the CNC router is powered on but not actively machining, and cutting time, representing the duration of actual machining operations. Excessive idle time without proper energy management can lead to unnecessary power consumption and inflated operational costs.
Quantifying Power Consumption in CNC Routers
In this section, we explore three key aspects of quantifying CNC router power consumption. By examining these dimensions, manufacturers can gain insights to make informed decisions and enhance the overall performance of their CNC machining operations.
Measurement Tools and Techniques
Accurately measuring power consumption is foundational to understanding and optimizing energy usage in CNC routers. Various tools and techniques are available for this purpose, ranging from basic energy meters to advanced monitoring systems. Energy meters, such as watt-hour meters or power loggers, provide real-time or cumulative measurements of energy consumption, allowing operators to track usage patterns and identify inefficiencies. Additionally, integrated monitoring systems offer comprehensive insights into power consumption alongside other operational parameters, enabling proactive energy management and optimization.
Typical Power Requirements of Different CNC Router Types
The power requirements of CNC routers vary across different types and configurations, influenced by factors such as spindle motor power, bed size, and auxiliary equipment. Understanding these variations can help select the appropriate machine for a specific application and accurately estimate energy usage. Generally, smaller desktop or hobbyist CNC routers may have lower power requirements, typically ranging from a few hundred watts to a few kilowatts. In contrast, industrial-grade CNC routers designed for heavy-duty machining operations may consume several kilowatts or more, depending on their size and capabilities. By benchmarking typical power requirements across different machine types, manufacturers can make informed decisions during equipment selection and capacity planning.
What challenges does CNC router face?
Beyond understanding power consumption, calculating energy costs is an essential step in effectively managing operating expenses and budgets. Energy costs are determined by factors such as electricity rates, operating hours, and the efficiency of CNC router operations. By multiplying the measured power consumption (in kilowatt-hours) by the applicable electricity rate, operators can estimate the energy cost associated with running the CNC router over a specific period. Incorporating this information into cost analyses and production planning facilitates informed decision-making and enables businesses to optimize energy usage while minimizing expenses.
Quantifying power consumption in CNC routers encompasses a multifaceted approach. By leveraging insights from these dimensions, manufacturers can implement targeted strategies to enhance energy efficiency, reduce operational costs, and promote sustainable manufacturing practices. Embracing a holistic approach to power management empowers businesses to navigate the complexities of CNC machining operations and drive continual improvements in performance and profitability.
Strategies to reduce power consumption
Efficient power management provides opportunities for CNC routers to save costs, achieve sustainable development, and achieve operational excellence. This section presents a comprehensive array of strategies to reduce power consumption, spanning various aspects of CNC machining processes. The specific implementation steps are as follows:
- Optimizing Tool Path Efficiency: Maximizing tool path efficiency helps reduce unnecessary movement and reduce power consumption during CNC router operation. Strategies such as optimizing tool paths to minimize travel distance, reducing air cutting (cutting without material contact), and employing high-efficiency cutting techniques (e.g., climb milling) can significantly reduce energy usage while maintaining machining accuracy and quality.
- Using Energy-Saving Components: Leveraging energy-saving components, such as high-efficiency motors, spindle drives, and cooling systems, contributes to overall power consumption reduction in CNC routers. Investing in energy-efficient components not only lowers electricity usage but also enhances operational reliability and longevity, yielding long-term cost savings and sustainability benefits.
- Implementing Software-Based Energy-Saving Functions: Modern CNC control software offers a range of energy-saving functions and features that can be utilized to optimize power consumption. Implementing features such as idle mode activation, dynamic spindle speed adjustment, and adaptive feed rate control enables CNC routers to operate more efficiently, minimizing power usage during idle periods and adjusting performance parameters based on workload requirements.
- Maintenance and Calibration: Regular maintenance and calibration of CNC router components is beneficial to ensure optimal performance and energy efficiency. Proper lubrication, alignment, and calibration of machine components reduce friction, improve accuracy, and minimize energy losses, thereby optimizing power consumption and extending equipment lifespan.
- Intelligently Scheduling: Intelligently scheduling to minimize idle time and maximize cutting time enhances energy efficiency in CNC router operations. Batch processing similar jobs, optimizing job sequences to minimize tool changes and setup times, and utilizing machine downtime for maintenance or energy-saving standby modes contribute to overall power consumption reduction.
- Using Energy-Saving Tools and Workpiece Fixtures: Selecting energy-saving tools and workpiece fixtures, such as high-efficiency cutting tools and vacuum fixtures with optimized airflow designs, can further reduce power consumption in CNC router operations. These tools and fixtures minimize material waste, improve cutting efficiency, and enhance workpiece stability, resulting in lower energy usage and increased productivity.
By implementing a comprehensive array of strategies, manufacturers can achieve significant reductions in power consumption in CNC router operations. Embracing these strategies not only lowers operational costs but also promotes sustainability and competitiveness in today’s manufacturing landscape. As CNC machining continues to evolve, prioritizing energy efficiency remains a cornerstone for driving continual improvements in performance and profitability.
Benefits of reduced power consumption
Reducing CNC router power consumption offers a myriad of benefits across various aspects of operation. By adopting energy-efficient practices, businesses can not only enhance their bottom line but also contribute to sustainability efforts and improve the overall reliability of their operations.
- Cost Savings: One of the most immediate benefits is cost savings on energy bills. By reducing power consumption, businesses can significantly lower their electricity bills. CNC routers often consume substantial amounts of power during operation, so optimizing energy usage can lead to considerable cost savings over time.
- Environmental Impact: Decreasing power consumption contributes to a smaller carbon footprint and helps in environmental conservation efforts. By consuming less energy, you reduce the demand on power plants, which often rely on fossil fuels, thereby lowering greenhouse gas emissions.
- Extended Equipment Lifespan: Running machinery at lower power levels can lead to less wear and tear on components. Over time, this can translate to reduced maintenance costs and longer equipment lifespan, as lower power consumption typically results in less stress on the router’s motors, electronics, and other components.
- Improved Stability and Accuracy: In some cases, reducing power consumption can lead to more stable operation of the CNC router. Fluctuations in power supply or excessive power draw can affect the precision and accuracy of the router’s movements. By optimizing power consumption, you may achieve more consistent and accurate results in your machining operations.
Challenges and Considerations
Balancing Power Consumption Reduction and Performance
- Optimizing Efficiency: CNC routers need to strike a delicate balance between reducing power consumption and maintaining optimal performance. While reducing energy usage is desirable for cost savings and environmental sustainability, it must not compromise the speed, precision, or quality of machining operations. Achieving this balance often involves employing advanced motor control algorithms, optimizing toolpath generation software, and implementing energy-saving features without sacrificing productivity.
- Dynamic Power Management: CNC routers operate across a wide range of speeds and loads, leading to fluctuating power requirements. Dynamic power management systems are necessary to adapt power consumption in real-time based on the current operational demands. This involves intelligently adjusting motor speeds, spindle power, and auxiliary systems to minimize energy wastage during idle or low-load periods while ensuring sufficient power during high-demand tasks.
- Material and Tool Considerations: Different materials and cutting tools require varying levels of power to achieve optimal machining results. CNC router operators must consider the specific requirements of the material being processed and the tools being used when optimizing power consumption. This may involve adjusting cutting parameters, feed rates, and spindle speeds to minimize energy usage while maintaining desired machining outcomes.
Compatibility with Specific CNC Router Models
- Diverse Hardware and Software: CNC routers come in a wide variety of models from different manufacturers, each with its own hardware configurations and software interfaces. Compatibility challenges arise when implementing power-saving features across different CNC router models, as the underlying hardware architecture and control systems may vary significantly. Ensuring seamless integration and compatibility across diverse platforms requires thorough testing, standardized communication protocols, and firmware updates tailored to specific models.
- Interoperability with Accessories: CNC routers often interface with various accessories and peripherals such as vacuum pumps, coolant systems, and robotic arms. Ensuring compatibility and efficient power management across these interconnected devices helps optimize overall energy usage. Standardized interfaces and communication protocols facilitate interoperability and enable centralized control and monitoring of power consumption across the entire CNC system.
User Training and Awareness
- Efficient Operation Practices: User training also plays a key role in optimizing the power consumption of CNC router operations. Operators need to be educated about efficient operation practices, including proper machine setup, tool selection, and cutting parameters adjustment to minimize energy waste. Training programs should emphasize the importance of monitoring power usage metrics, identifying energy-intensive processes, and implementing strategies for improvement.
- Awareness of Energy-Saving Features: Users must be familiar with the energy-saving features and capabilities of CNC routers to leverage them effectively. Training programs should cover topics such as idle shutdown modes, energy-efficient toolpath optimization algorithms, and motor power management techniques. By raising awareness and providing practical guidance, users can actively contribute to reducing power consumption and optimizing the overall energy efficiency of CNC router operations.
- Maintenance and Calibration: Regular maintenance and calibration of CNC routers is beneficial to ensure optimal performance and energy efficiency. User training should include instructions on performing routine maintenance tasks, such as lubrication, alignment checks, and system calibration, to minimize energy losses due to mechanical inefficiencies. Additionally, users should be trained to identify and address energy-related issues promptly, such as worn-out components or improper machine settings, to prevent unnecessary energy consumption and prolong the lifespan of CNC router systems.
Summarize
Understanding the power consumption of CNC routers is an important link for efficient operation and cost management. In this article, we provide comprehensive insights into managing energy usage effectively in CNC routing operations. By implementing energy-saving practices and investing in modern, efficient equipment, businesses can not only reduce their environmental footprint but also enhance their bottom line by minimizing electricity costs. As technology continues to advance, staying informed about the latest developments in CNC router efficiency can help stay competitive in the manufacturing industry while maintaining sustainability goals.
AccTek CNC is a well-known CNC router manufacturer in China. We value the quality, efficiency, and precision of our machines. From our versatile 3-axis CNC routers, ideal for precise plane machining, to our rotary-axis CNC routers, optimized for cylindrical machining tasks, we offer solutions that deliver exceptional results. Moreover, our comprehensive lineup includes advanced 4-axis and 5-axis CNC routers, specifically engineered for intricate 3D engraving projects, providing unparalleled versatility and performance. At AccTek CNC, we take pride in our ability to deliver innovative solutions that empower businesses to achieve their manufacturing goals with utmost precision and efficiency. Contact us to start your CNC router plan.