Can CNC Routers Tackle Any Design Complexity?
- 6-9 Min Read
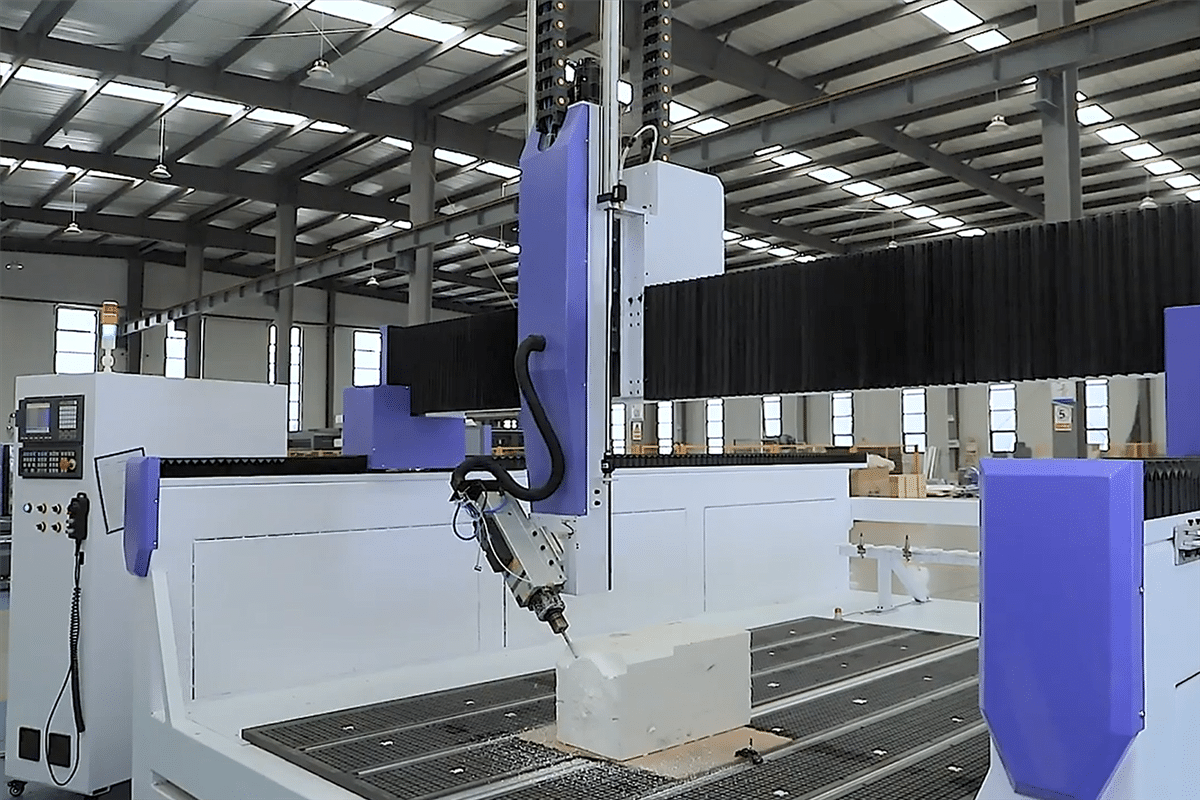
In the ever-evolving landscape of digital fabrication, Computer Numerical Control (CNC) routers stand as pillars of precision and versatility, transforming virtual designs into tangible realities with remarkable accuracy. These machines have become indispensable tools across industries, from architecture and art to manufacturing and prototyping, enabling the realization of intricate and complex designs that were once deemed unattainable. However, the extent to which a CNC router can bring a design to life is intricately intertwined with its performance capabilities. In this exploration, we delve into the profound impact of CNC router performance on the complexity of design, uncovering the symbiotic relationship between technological prowess and creative expression. By understanding the nuances of CNC router performance, we seek to shed light on the limitations and challenges they face in handling design complexity, thereby answering the question of whether CNC routers can address any design complexity.
The Significance of Design Complexity in CNC Routing
Design complexity holds immense significance in CNC routing, catalyzing creativity, innovation, and customization. By embracing complex designs and leveraging the capabilities of CNC routing technology, designers and manufacturers can unlock new possibilities, elevate their craftsmanship, and deliver technically superior products. Design complexity plays a pivotal role in shaping the outcome of CNC routing operations in several key aspects:
- Creative Expression and Innovation: Design complexity catalyzes creative expression and innovation in CNC routing. Intricate designs with fine details, complex geometries, and unique features enable designers to push the boundaries of imagination and explore new realms of artistic expression. CNC routers provide the means to translate these intricate designs into physical objects with precision and fidelity, empowering designers to bring their creative visions to life.
- Functional and Aesthetic Appeal: Complex designs often blend functional requirements with aesthetic appeal, resulting in products that are both visually striking and highly functional. Whether creating architectural ornamentation, intricate sculptures, or custom furniture pieces, CNC routing allows designers to integrate intricate details, sculptural elements, and ornamental features into their designs with unparalleled precision and consistency. The ability to achieve intricate designs adds value to the final product and enhances its aesthetic appeal.
- Customization and Personalization: Design complexity enables customization and personalization in CNC routing, allowing designers to tailor products to individual preferences and specifications. Whether producing personalized signage, bespoke furniture, or custom prototypes, CNC routers offer the flexibility to accommodate unique design requirements and variations. Intricate details, intricate textures, and personalized embellishments enhance the uniqueness and exclusivity of the final product, catering to diverse customer needs and preferences.
- Versatility and Adaptability: CNC routing’s ability to handle complex designs extends its versatility and adaptability across a wide range of industries and applications. From furniture and signage to molding and architecture, CNC routers are utilized in diverse fields to fabricate complex components, intricate assemblies, and artistic creations. The versatility of CNC routing technology enables designers and manufacturers to tackle a myriad of design challenges and explore innovative solutions across various domains.
- Precision and Accuracy: While complexity poses challenges in CNC routing operations, it also drives advancements in precision and accuracy. Complex designs demand meticulous attention to detail, precise toolpath generation, and optimized machining strategies to ensure dimensional accuracy and surface finish quality. CNC routers equipped with advanced CAM software tools, high-performance spindle systems, and multi-axis machining capabilities are capable of achieving exceptional levels of precision, even in the most intricate designs.
Factors Affecting CNC Router Performance
CNC routers operate by interpreting digital instructions to carve, cut, and shape materials such as wood, plastic, and metal with unparalleled accuracy. The performance of a CNC router is influenced by several key factors:
Machine Specifications
- Axis Configuration: The axis configuration significantly impacts the types of shapes and geometries that can be machined. While three-axis systems are suitable for basic flat shapes, four-axis and five-axis systems offer greater flexibility for machining complex contours, curved surfaces, and undercut features. Moreover, multi-axis systems reduce the need for repositioning the workpiece, streamlining production processes and enhancing overall efficiency.
- Work Area Size: The size of the CNC router’s work area dictates the maximum dimensions of the designs it can accommodate. Larger work areas allow for machining larger workpieces or multiple smaller parts in a single setup, minimizing material handling and setup times.
- Spindle Power: The spindle is one of the most critical components of a CNC router. Spindle power, typically measured in horsepower (HP) or kilowatts (kW), determines the machine’s ability to cut through different materials and handle varying loads. Higher spindle power allows for faster cutting speeds, deeper cuts, and the ability to machine tougher materials.
Cutting Tools
- Tool Types: CNC routers utilize a diverse range of cutting tools, each tailored to specific materials, geometries, and machining operations. Common tool types include end mills, ball mills, engraving bits, and V-bits. A diverse range of tooling options expands the design possibilities by offering varying levels of detail and surface finish.
- Tool Diameter and Length: Tool diameter determines the width of the cut and influences machining accuracy and surface finish. Smaller-diameter tools are suitable for fine detail work and intricate geometries, while larger-diameter tools are more efficient for roughing and material removal. Tool length, on the other hand, affects the reach and stability of the cutting tool. Longer tools may exhibit increased deflection and vibration, particularly when machining deep pockets or thin-walled structures.
- Tool Changes: The frequency of tool changes depends on factors such as the complexity of the part, the material being machined, and the desired machining strategy. Efficient tool change systems, such as automatic tool changers (ATCs), minimize downtime and maximize productivity by enabling rapid tool swaps without manual intervention.
Programming and Software
- CAM Software Functionality: Advanced CAM software offers a wide range of features and functionalities, including adaptive toolpath generation, collision detection, and material optimization. These capabilities enable operators to streamline machining processes, minimize material waste, and achieve optimal surface finishes.
- G-code Complexity: Complex G-code programs may include intricate toolpath trajectories, variable feed rates, and tool changes at specific intervals. Managing and executing such G-code programs requires a CNC router with advanced motion control capabilities, high processing power, and robust toolpath interpolation algorithms.
Material Properties
- Material Hardness and Density: Different materials present varying challenges for CNC routing. Hardwoods, metals, and composites may require more robust cutting tools and slower cutting speeds to achieve intricate details without compromising quality. Moreover, the material’s density, grain direction, and structural integrity can impact certain designs’ feasibility.
- Material Size and Thickness: Larger workpieces or components may require machines with larger working envelopes and higher load-bearing capacities to accommodate their size and weight. Moreover, machining thick materials may necessitate longer cutting tool lengths and deeper cutting depths to achieve complete material penetration and desired part geometries.
- Material Fixtures: Effective fixture design and implementation ensure proper material support, minimize vibration, and prevent workpiece movement during machining operations. The choice of fixture depends on factors such as material type, size, and geometry, as well as machining requirements and accessibility.
Design Complexity
- 2D and 3D Design: CNC routers are capable of machining both 2D profiles and 3D geometries, offering designers unparalleled flexibility in realizing their creative visions. In 2D design, flat shapes and contours are defined by lines, arcs, and curves in a two-dimensional space. On the other hand, 3D design involves creating three-dimensional models with depth, volume, and complex surface features. 3D designs enable designers to push the boundaries of creativity, exploring sculptural elements, architectural ornamentation, and product prototypes with unprecedented realism and fidelity.
- Details and Exquisite Features: Designs with intricate features, sharp corners, and fine textures may require specialized tooling, smaller-diameter cutting tools, and meticulous attention to cutting parameters to achieve desired results. Moreover, the presence of intricate details and complex geometries introduces challenges related to toolpath generation, collision avoidance, and surface finish quality.
Dealing with the challenges of complex designs
While CNC routers offer remarkable capabilities in translating digital designs into physical objects, they also have limitations and face challenges when it comes to handling complex designs. Some of the key limitations and challenges include:
Processing Time and Efficiency
As design complexity increases, so does the time required for CNC routers to execute machining operations. Intricate designs with fine details, complex contours, and high-density features may necessitate longer machining times due to the sheer volume of tool movements and material removal required. Additionally, the presence of tight corners, sharp angles, or narrow passages may require slower cutting speeds and more cautious machining approaches to ensure accuracy and prevent tool breakage.
Balancing design intricacy with machining efficiency helps optimize overall production workflow and minimize lead times. However, achieving this balance requires careful consideration of cutting parameters, tooling strategies, and material properties. Advanced CAM software tools, such as high-speed machining algorithms and adaptive toolpath optimization, can help streamline toolpath generation and maximize machining efficiency without sacrificing quality.
Toolpath Optimization
Optimizing toolpaths for complex designs poses a significant challenge for CNC routing operations. As designs become more intricate, generating optimized toolpaths that minimize machining time, reduce tool wear, and maintain dimensional accuracy becomes increasingly complex. Toolpath optimization involves balancing factors such as cutting forces, tool engagement, and chip evacuation to achieve optimal machining performance while preserving intricate design details.
Certain design features, such as sharp corners, tight radii, or intricate surface textures, may pose challenges for standard toolpath optimization algorithms. In such cases, manual intervention or custom toolpath adjustments may be necessary to overcome limitations and achieve desired machining results. Additionally, optimizing toolpaths for multi-axis machining operations, where the cutting tool can move along multiple axes simultaneously, requires advanced CAM software capabilities and expertise in machine programming.
Machine Rigidity
CNC routers rely on rigid structures and stable foundations to maintain accuracy and precision during machining operations. However, as design complexity increases, so does the risk of machine deflection, vibration, or backlash, which can compromise dimensional accuracy and surface finish quality. Ensuring adequate machine rigidity and stability can maintain precision and consistency in machining operations.
Machining complex designs may exert higher cutting forces and induce greater stress on the CNC router’s components, particularly during aggressive cutting maneuvers or deep material removal. Therefore, selecting a CNC router with a robust frame, high-quality linear guides, and rigid spindle mounting can minimize machine deflection and ensure reliable performance. Additionally, optimizing cutting parameters and tooling strategies to reduce cutting forces and mitigate vibrations can help preserve machine rigidity and enhance machining accuracy.
Summarize
While CNC routers possess remarkable capabilities in handling a wide range of design complexities, they are not without limitations. Whether CNC routers can solve any design complexity is nuanced and multifaceted. While these machines excel at translating intricate digital designs into physical reality with precision and efficiency, they face challenges in certain areas. However, it’s essential to recognize that CNC routing technology continues to evolve rapidly, driven by advancements in machine design, software development, and material science. With ongoing innovation and improvements in CNC router capabilities, the boundaries of design complexity that can be achieved continually expand.
At AccTek CNC, we have always pursued technological progress. From 3-axis CNC routers that can only perform plane processing to 4-axis and 5-axis CNC routers that can perform 3D processing, we continue to promote design complexity into reality. We can offer personalized machining solutions tailored to each customer’s specific needs and preferences. Whether it’s automating repetitive tasks or optimizing complex machining processes, AccTek CNC can deliver bespoke solutions that maximize efficiency and productivity. Choose AccTek to turn your design vision into life.