- 9-14 Min Read
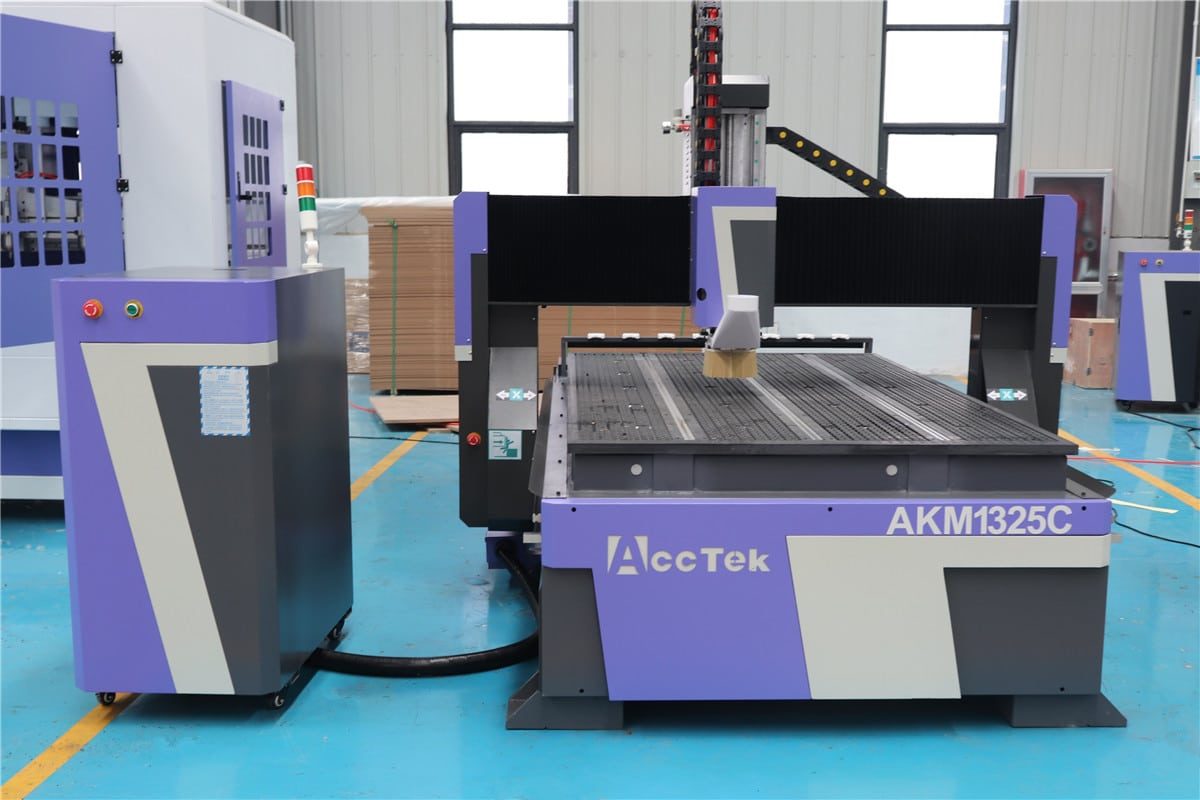
In the realm of modern manufacturing, Computer Numerical Control (CNC) routers have revolutionized the way intricate designs are crafted with precision and efficiency. These automated machines operate with unparalleled accuracy, carving out intricate patterns and shapes from various materials like wood, plastic, metal, and composites. Yet, behind the precision and efficiency lies a fundamental requirement that is often overlooked—the need for a cooling system. While the untrained eye may perceive CNC routers solely as machines of intricate movement and cutting prowess, their reliance on cooling systems unveils a deeper necessity rooted in the very essence of precision engineering. This article delves into the fundamental question: Why does a CNC router need to use a cooling system? Through exploration and analysis, we uncover the indispensable role cooling systems play in preserving precision, enhancing durability, and safeguarding the integrity of both machine and masterpiece. Understanding how these systems contribute not only to the efficiency of the machining process but also to the longevity of tools and the quality of the final product.
Understanding Heat Generation in CNC Routers
CNC routers, like any machinery, generate a significant amount of heat during operation. This heat is primarily produced due to the friction between the cutting tool and the workpiece material, as well as the movement of various mechanical components within the machine itself. Understanding these aspects can guide the implementation of effective cooling solutions. Let’s delve into each aspect to unravel the complexities of heat generation in CNC routers.
Friction and Cutting Force
At the heart of every CNC routing operation lies the interaction between cutting tools and workpiece materials. As the cutting tool traverses through the material, frictional forces are generated at the interface, converting mechanical energy into heat. This phenomenon intensifies during high-speed machining or when cutting hard materials, leading to a significant rise in temperature at the cutting edge. Moreover, the cutting force exerted on the tool further amplifies heat generation, especially in applications involving aggressive material removal or intricate detailing. The cumulative effect of friction and cutting force manifests as localized heating within the machining zone, influencing both tool wear and workpiece quality.
Motor and Driving Components
Within the intricate framework of a CNC router, motors, and driving components serve as the powerhouse, translating electrical energy into mechanical motion. However, this energy conversion process is inherently inefficient, leading to the generation of heat as a byproduct. Stepper motors, servo motors, and associated drivers experience thermal buildup during prolonged operation, particularly when subjected to high loads or rapid acceleration and deceleration. Additionally, friction within ball screws, belts, and gears further contributes to heat generation within the drive system. Left unchecked, elevated temperatures can compromise motor efficiency, degrade lubricants, and ultimately lead to component failure, disrupting machine performance and reliability.
Spindle and Tooling
The spindle, akin to the beating heart of a CNC router, drives the rotation of cutting tools with precision and vigor. However, this dynamic motion is not without its thermal consequences. As the spindle rotates at high speeds, friction between bearings, shafts, and other internal components generates heat, gradually elevating the spindle’s temperature. Furthermore, the cutting tools themselves undergo thermal stress as they engage with the workpiece, experiencing localized heating at the cutting edge. This phenomenon is exacerbated during high-speed machining or when using carbide tools, which have poor thermal conductivity. Prolonged exposure to elevated temperatures can compromise spindle integrity, degrade tool performance, and induce dimensional inaccuracies in machined parts.
In essence, the heating phenomenon in CNC routers is a multifaceted interplay of mechanical interactions, electrical energy conversion, and material properties. From the frictional forces at the cutting edge to the thermal stresses within motor assemblies and spindles, each aspect contributes to the thermal landscape of CNC machining. Recognizing these sources of heat generation is imperative in devising effective cooling strategies to mitigate their detrimental effects on machine performance and longevity. By addressing the root causes of thermal buildup, manufacturers can ensure the sustained precision and reliability of CNC routers, driving forward the boundaries of modern manufacturing.
The Importance of Temperature Control
Armed with an understanding of heat generation, we can now elucidate the indispensable role of temperature control in CNC routers. By carefully managing temperatures throughout the machining process, CNC routers can uphold the highest standards of quality, efficiency, and performance in modern manufacturing operations. Below are key points highlighting the importance of temperature control in a CNC router:
Precision and Accuracy
- Maintaining a stable temperature helps achieve consistent and precise machining results. Temperature fluctuations can cause thermal expansion and contraction in machine components, leading to dimensional inaccuracies in machined parts.
- By controlling temperatures within tight tolerances, CNC routers can uphold the desired geometrical specifications, ensuring that manufactured parts meet exact design requirements without deviations.
Tool Life and Performance
- High temperatures can accelerate tool wear, leading to premature dulling, chipping, or breakage of cutting tools. Consistent temperature control helps mitigate thermal stress on cutting tools, prolonging their lifespan and preserving their cutting edge sharpness.
- Moreover, proper temperature management minimizes thermal deformation in workpiece materials, resulting in improved surface finish and dimensional accuracy of machined parts.
Component Longevity
- Excessive heat can degrade the performance and lifespan of critical components within the CNC router, such as spindles, motors, bearings, and electronics. Overheating may lead to premature component failure, increased maintenance requirements, and costly downtime.
- Temperature control ensures that components operate within their specified temperature ranges, reducing the risk of thermal fatigue, material degradation, and mechanical failures.
Material Stability
- Temperature fluctuations can affect the stability and mechanical properties of workpiece materials, particularly thermally sensitive materials like plastics, composites, and certain metals.
- By controlling temperatures during machining processes, CNC routers can minimize the risk of material distortion, warping, or internal stresses, ensuring consistent material behavior and dimensional stability in finished parts.
Process Reliability and Consistency
- Consistent temperature control enhances the reliability and repeatability of machining processes, reducing the likelihood of errors, scrap, or rework.
- By eliminating temperature-related variations, CNC routers can achieve consistent machining results across different batches or production runs, fostering process reliability and quality assurance.
Types of Cooling Systems in CNC Routers
Air Cooling
Air cooling systems are a common cooling method utilized in CNC routers to dissipate heat generated during machining operations. Operating on the principle of convective heat transfer, air cooling systems utilize fans or blowers to circulate ambient air around heat-generating components, such as the spindle, motors, and electronics. The following is its detailed introduction:
Working Principle
Air cooling systems rely on the natural convection of air to carry heat away from machine components. Fans or blowers draw ambient air into the system, directing it over heat sinks or fins attached to heat-generating components. As the air passes over these surfaces, heat is transferred from the components to the air, which is then expelled from the system, carrying away the absorbed heat. This continuous airflow helps maintain optimal operating temperatures and prevents overheating of critical machine components.
Heat Dissipation Efficiency
The efficiency of air cooling systems in dissipating heat depends on several factors, including the airflow rate, heat sink design, and ambient temperature. Higher airflow rates and larger heat sink surfaces generally result in better heat dissipation efficiency. However, air cooling systems may struggle to dissipate heat effectively in high-temperature environments or during heavy-duty machining operations with prolonged or intense heat generation.
Temperature Adjustment
Temperature adjustment in air cooling systems is typically achieved by controlling the speed of fans or blowers. By varying the airflow rate, operators can regulate the cooling effect and maintain desired operating temperatures. Some air cooling systems may also incorporate temperature sensors and automatic control mechanisms to adjust fan speeds dynamically based on real-time temperature feedback.
Advantages of air cooling Systems
- Cost-Effective: air coolingsystems are generally more affordable to implement compared to water or oil cooling methods, as they require fewer additional components and infrastructure.
- Simple Installation: air coolingsystems are relatively simple to install and do not require complex plumbing or coolant circulation systems.
- Low Maintenance: With fewer moving parts and no coolant to manage, air coolingsystems typically have lower maintenance requirements and reduced risk of system failure.
- Suitable for Light to Moderate Machining: air coolingsystems are well-suited for light to moderate machining applications where heat generation is moderate and continuous airflow is sufficient for heat dissipation.
Disadvantages of air cooling Systems
- Limited Cooling Capacity: air coolingsystems may struggle to dissipate heat effectively in high-temperature environments or during heavy-duty machining operations with intense heat generation.
- Temperature Control Challenges: Maintaining precise temperature control can be challenging with air coolingsystems, especially in fluctuating ambient conditions.
- Noise and Airborne Contaminants: The operation of fans or blowers in air coolingsystems can generate noise, and airflow may carry airborne contaminants or debris, potentially affecting machining quality.
- Reduced Efficiency in Enclosed Spaces: air coolingsystems may exhibit reduced efficiency in enclosed or confined spaces where airflow is restricted, leading to elevated temperatures and diminished cooling performance.
Water Cooling
Water cooling systems offer efficient heat dissipation and precise temperature control to ensure optimal machine performance. Employing a closed-loop circulation of coolant, water cooling systems play a pivotal role in maintaining stable operating temperatures and preserving the longevity of critical components. The following is its detailed introduction:
Working Principle
Water cooling systems in CNC routers operate on the principle of heat exchange, where coolant, typically water or water-based solutions, absorbs heat from heat-generating components such as the spindle, motors, and electronics. The heated coolant is then circulated through a closed-loop system, where it passes through a heat exchanger or radiator to dissipate heat before being recirculated back into the system. This continuous circulation ensures effective cooling and temperature regulation throughout the machining process.
Heat Dissipation Efficiency
Water cooling systems offer high heat dissipation efficiency, thanks to the excellent thermal conductivity and specific heat capacity of water. By absorbing heat from machine components and carrying it away from the machining area, water cooling systems effectively prevent overheating and thermal stress on critical components. Additionally, the closed-loop circulation ensures consistent cooling performance, even in demanding machining applications and high-temperature environments.
Temperature Adjustment
Water cooling systems provide precise temperature control, allowing users to adjust coolant temperatures to meet specific machining requirements. Temperature adjustments can be made by regulating the flow rate of coolant, adjusting the temperature setpoints on the cooling system controller, or incorporating additional cooling capacity as needed. This flexibility enables operators to optimize cooling performance based on varying machining conditions and material properties.
Advantages
- High Heat Dissipation Efficiency: Water cooling systems offer superior heat dissipation capabilities compared to air cooling, making them suitable for heavy-duty machining tasks and high-temperature environments.
- Precise Temperature Control: Water cooling systems provide accurate temperature regulation, ensuring stable operating temperatures for critical machine components.
- Consistent Cooling Performance: The closed-loop circulation of coolant ensures consistent cooling performance, minimizing the risk of overheating and thermal-related issues.
- Compatibility with Various Materials: Water cooling systems are compatible with a wide range of materials and machining applications, making them versatile and adaptable to different manufacturing needs.
Disadvantages
- Complexity and Maintenance: Water cooling systems require additional infrastructure for coolant circulation, including pumps, hoses, and radiators. Regular maintenance is necessary to ensure proper functioning and prevent issues such as coolant contamination or corrosion.
- Initial Investment: The initial cost of installing a water cooling system may be higher compared to air cooling systems, particularly for custom or high-capacity setups.
- Potential Leakage Risks: Water cooling systems carry a risk of leaks or spills, which can lead to equipment damage or safety hazards if not properly addressed.
Cooling System Operation Precautions
Operating the cooling system in a CNC router requires careful attention to ensure optimal performance, safety, and longevity of machine components. Here are several precautions to consider when operating the cooling system. By following these precautions, CNC router operators can ensure the safe, efficient, and reliable operation of the cooling system, minimizing the risk of overheating, component damage, and downtime.
- Monitor Coolant Levels: Regularly check coolant levels in the reservoir and top up as needed to maintain proper coolant circulation and heat dissipation. Low coolant levels can lead to inadequate cooling and an increased risk of overheating.
- Use Recommended Coolant: Use the coolant recommended by the CNC router manufacturer to ensure compatibility with system components and optimal cooling performance. Avoid mixing different types of coolant unless explicitly specified by the manufacturer.
- Dilution Ratios: Dilute coolant with water according to manufacturer recommendations to achieve the desired coolant concentration. Using coolant at the correct dilution ratio ensures effective heat transfer and corrosion protection without compromising cooling performance.
- Proper Ventilation: Ensure adequate ventilation in the CNC router workspace to prevent heat buildup and maintain a comfortable working environment for operators. Proper ventilation also helps dissipate coolant vapors and fumes generated during machining processes.
- Temperature Monitoring: Monitor coolant temperature regularly using temperature sensors or gauges to ensure that it remains within the specified operating range. Sudden temperature fluctuations may indicate cooling system issues that require immediate attention.
- Inspect Hoses and Connections: Inspect coolant hoses, fittings, and connections regularly for signs of leaks, cracks, or deterioration. Replace damaged or worn hoses promptly to prevent coolant leaks and ensure consistent coolant flow.
- Regular Maintenance: Follow the manufacturer’s recommended maintenance schedule for the cooling system, including coolant replacement, filter cleaning or replacement, and lubrication of moving components. Regular maintenance helps prevent system failures and ensures optimal cooling performance.
- Emergency Procedures: Establish emergency procedures for handling coolant leaks, spills, or system malfunctions. Train operators on how to respond to coolant-related emergencies, including shutting down the machine, containing spills, and contacting maintenance personnel.
Cooling System Maintenance
Maintaining the cooling system of a CNC router helps ensure optimal performance, longevity of machine components, and high-quality machining results. Here are several steps to effectively maintain the cooling system. By following these maintenance practices, CNC router operators can ensure the reliability and efficiency of the cooling system.
- Regular Inspection: Conduct routine visual inspections of the cooling system components, including coolant reservoirs, pumps, hoses, filters, and radiators. Look for signs of leaks, corrosion, blockages, or damage that may affect the system’s performance.
- Cleanliness: Keep the cooling system clean and free from debris, contaminants, and buildup. Regularly clean coolant reservoirs, filters, and cooling lines to prevent clogging and ensure proper coolant flow.
- Coolant Quality: Monitor the quality of coolant regularly, checking for contamination, degradation, or dilution. Replace coolant as needed according to manufacturer recommendations or based on coolant condition testing results.
- Lubrication: If the cooling system utilizes oil-based lubricants, ensure proper lubrication of moving components such as pumps, bearings, and fans. Lubricate as recommended by the manufacturer to prevent premature wear and ensure smooth operation.
- Pump Maintenance: Inspect coolant pumps regularly for signs of wear, damage, or malfunction. Check pump seals, impellers, and motor bearings for leaks, corrosion, or excessive wear. Replace worn or damaged components and lubricate pump bearings as needed.
- Radiator Cleaning: Clean radiator fins and cooling fins regularly to remove dust, dirt, and debris that may impede airflow and reduce heat dissipation efficiency. Use compressed air or a soft brush to clean radiator surfaces gently.
- Filter Replacement: Replace coolant filters or strainers at recommended intervals to ensure proper filtration of coolant and prevent contamination of machine components. Clean or replace clogged filters promptly to maintain optimal coolant flow and cooling system efficiency.
- Professional Maintenance: Schedule periodic professional maintenance and servicing of the cooling system by qualified technicians. This may include thorough cleaning, inspection, lubrication, and testing of system components to identify and address any potential issues.
Summarize
The necessity of a cooling system for CNC routers cannot be overstated. These systems play a key role in maintaining optimal operating conditions, prolonging the lifespan of the machinery, and ensuring consistent and high-quality output. By effectively dissipating heat generated during the machining process, cooling systems prevent overheating, reduce the risk of thermal expansion, and minimize the potential for tool wear and material deformation. Investing in a reliable cooling system for CNC routers is not just a matter of convenience but a strategic decision to optimize productivity, minimize downtime, and safeguard the long-term performance of the equipment.
The CNC routers produced by AccTek have air-cooling systems and water-cooling systems. We usually recommend suitable machines for users based on their processing requirements, workshop temperature, and other factors. By leveraging our extensive industry experience and technical expertise, we ensure that you receive professional purchasing advice that aligns perfectly with your goals and objectives. Whether you prioritize precision, speed, or versatility, we’re committed to maximizing the value of your investment in CNC router technology. Contact us today to explore how we can elevate your CNC machining capabilities to new heights.