Table of Contents
What is An ATC CNC Router: Comprehensive Guide
- 9-14 Min Read
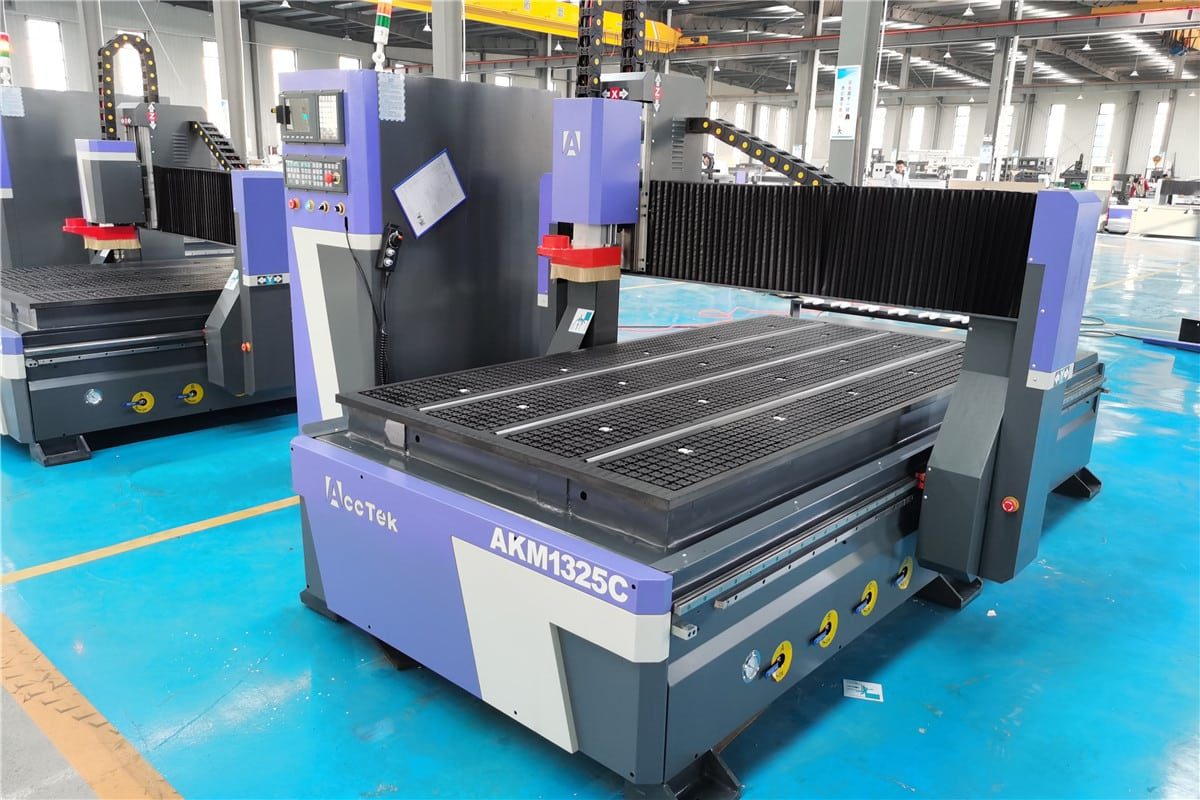
In the ever-evolving landscape of manufacturing and fabrication, technology continues to play a pivotal role in enhancing precision, efficiency, and versatility. The inception of CNC routers marked a significant departure from traditional manual machining methods. With the ability to precisely execute programmed commands, CNC routers brought about a paradigm shift in manufacturing, offering unparalleled accuracy and repeatability. As technology continued to advance, the need for increased automation and efficiency led to the development of the Automatic Tool Changer (ATC) CNC router. The advent of the ATC CNC router has revolutionized the field of machining. In this comprehensive guide, we will delve into the intricacies of ATC CNC routers, exploring their functionality, benefits, applications, and the impact they have on various industries.
Understanding ATC CNC Router
ATC CNC router stands for Automatic Tool Changer Computer Numerical Control router. It is a type of CNC router that is equipped with an automatic tool changer, allowing it to change cutting or milling tools during the machining process without manual intervention. This feature enhances efficiency and productivity in manufacturing and woodworking processes. The CNC router itself is a computer-controlled cutting machine that uses a rotating cutting tool to remove material from a workpiece. The key feature of an ATC CNC router is its ability to automatically change tools based on the programmed instructions. This is particularly useful when a project requires multiple tool types or when different cutting depths and techniques are needed. The automatic tool changer reduces downtime and increases the machine’s overall productivity. The following is the specific information on the ATC CNC router.
What are the ATC CNC router components?
The components of an ATC CNC router may vary depending on the specific model and manufacturer, but generally, they include the following key components:
- Base or Frame: The base or frame provides the structural support for the CNC router. It is usually made of heavy-duty materials to ensure stability and rigidity during machining operations.
- Worktable: The worktable is the surface on which the workpiece is placed for machining. It can be a fixed table or a movable one, depending on the design of the CNC router.
- Gantry: The gantry is a bridge-like structure that spans the width of the machine and supports the X-axis motion. It often houses the X-axis drive system and is responsible for moving the cutting tool horizontally.
- ATC Spindle: The spindle is a critical component of the ATC CNC router, responsible for holding and rotating the cutting tools. The ATC system interfaces with the spindle to facilitate the swift exchange of tools.
- Z-Axis Assembly: The Z-axis assembly controls the vertical movement of the cutting tool. It typically consists of a motorized mechanism that raises and lowers the spindle to control the depth of the cut.
- Automatic Tool Changing System: The distinguishing feature of an ATC CNC router is its Automatic Tool Changing system. Unlike conventional CNC routers that require manual intervention for tool changes, an ATC CNC router is equipped with a sophisticated mechanism that enables the automatic swapping of cutting tools during the machining process. It can hold multiple tools in a carousel or magazine, and a robotic arm or similar mechanism is used to retrieve and replace tools as needed.
- Tool Grippers: These are specialized devices within the ATC system that securely grasp and release cutting tools. The design and precision of the tool grippers play a crucial role in ensuring the accuracy of the tool-changing process.
- Control System: The control system includes the CNC controller, which interprets the CNC code and translates it into the movements of the machine axes. It also manages the tool change process in an ATC CNC router.
- Drive Systems: Motors and drive systems control the movement of the machine along the X, Y, and Z axes. These systems are essential for precise and controlled motion.
- Coolant System: A coolant system is often employed to dissipate heat generated during cutting operations. It helps maintain the temperature of the cutting tools and workpiece, preventing overheating.
- Dust Collection System: CNC routers generate a significant amount of dust during machining. A dust collection system is employed to remove debris and maintain a clean working environment.
What is the working principle of ATC CNC router?
The working principles of an ATC (Automatic Tool Changer) CNC router involve a combination of mechanical, electrical, and software systems to automate the process of changing cutting tools during a machining operation. Here’s a general overview of how an ATC CNC router operates:
- Tool Selection: The operator specifies the tool changes in the CNC program. Each tool is assigned a tool number or identifier.
- Tool Carousel or Magazine: The CNC router is equipped with a tool carousel or magazine that holds multiple cutting tools. The tools are stored in designated slots, and each slot corresponds to a specific tool position.
- CNC Controller Programming: The CNC controller interprets the CNC program, which includes instructions for tool changes. The program specifies the tool number and the point in the machining process where the tool change should occur.
- Tool Change Command: When a tool change is commanded in the CNC program, the CNC controller sends signals to the ATC system to initiate the tool change process.
- Tool Change Mechanism: The tool change mechanism, which could be a robotic arm, a spindle with an integrated tool changer, or another automated system, is activated. This mechanism moves to the specified tool position in the carousel.
- Tool Release and Retrieval: The tool change mechanism releases the current tool, either by unclamping it or using a quick-release mechanism. Then, it retrieves the new tool from the tool carousel.
- Tool Installation: The new tool is securely installed in the spindle. This can involve a collet or tool holder that grips the tool tightly to ensure stability during machining.
- Tool Measurement (Optional): Some advanced ATC CNC routers include tool length sensors. After a tool change, the system may measure the length of the new tool to ensure accuracy in the machining process.
- Resuming Machining: With the new tool in place, the CNC controller resumes the machining process from the point where the tool change was commanded. The router continues cutting, carving, or milling based on the updated tool.
- Repeat as Necessary: The CNC router continues to perform tool changes as specified in the program until the machining job is complete.
Application fields of ATC CNC router
With its automatic tool-changing capabilities, the ATC CNC router is an effective tool for many industries to pursue precision and efficiency. From woodworking to metalworking, plastics to stone, these machines have proven their mettle in shaping the future of manufacturing. This part introduces you to the application of ATC CNC routers in different fields so that you can have a better understanding of their functions.
- Furniture Industry: In furniture production, an ATC CNC router plays a key role in making intricate designs and precise cuts. Whether creating a custom table or exquisite cabinetry, these machines achieve maximum productivity without sacrificing quality. The ability to switch tools automatically means that intricate details, such as decorative edges and engraved patterns, can be achieved without manual intervention. This not only saves time but also reduces possible errors caused by manual tool changing.
- Plastics Take Shape: Plastics, with their versatility, have become integral to modern manufacturing. Whether it’s cutting and shaping plastic sheets for packaging or creating intricate 3D carvings for artistic displays, ATC CNC routers offer a level of accuracy that is hard to match. The automatic tool changer ensures that various tools, each specialized for different tasks, seamlessly combine to bring intricate plastic designs to life.
- Sign Making: Sign making is an art that blends creativity with technical precision. From engraving and cutting acrylic sheets to producing dimensional letters and logos, ATC CNC routers bring a level of detail that defines brand identity. The automatic tool changer allows for a dynamic range of tool options, ensuring that sign makers can execute diverse designs without compromising on efficiency.
- Foam Cutting: Foam, often used for packaging and artistic endeavors, requires a delicate touch. ATC CNC routers excel in sculpting foam materials, whether for protective packaging or artistic installations. The ability to switch between tools seamlessly is particularly advantageous in foam cutting, where different tools are needed for roughing and finishing passes. This ensures that the final product is not only precise but also retains the desired texture and form.
- Prototyping and Rapid Manufacturing: In the fast-paced world of prototyping and rapid manufacturing, time means cost. ATC CNC routers, with their automated tool-changing feature, accelerate the innovation cycle. Rapid prototyping of various materials, quick production of small batches of parts, and the ability to adapt to design changes on the fly make these machines indispensable in research and development environments. The flexibility they offer ensures that ideas can be transformed into tangible prototypes with efficiency and precision.
- Stone Engraving and Cutting: The art of stone engraving and cutting requires a delicate touch and unwavering precision. ATC CNC routers bring a modern twist to this ancient craft, allowing for the creation of intricate designs on stone surfaces. From architectural embellishments to artistic sculptures, these routers play a vital role in preserving and evolving the tradition of stone craftsmanship. The automatic tool changer ensures that a variety of tools, suited for different stone types and intricacies, can be seamlessly integrated into the machining process.
- Mold Making: Creating molds for casting metals, plastics, or other materials is a meticulous process that demands precision. ATC CNC milling machines provide the precision required for high-quality mold production. The automatic tool changer facilitates the use of different tools for roughing and finishing passes, ensuring that the final mold meets exact specifications. This precision is invaluable in industries where replication is a key element of the manufacturing process.
- Educational and Research Frontiers: In educational institutions and research facilities, ATC CNC routers are not just tools; they are gateways to learning and innovation. These machines provide hands-on experience in CNC machining, allowing students and researchers to explore the realms of design and manufacturing. The automatic tool changer simplifies the learning process, making CNC technology accessible to a wider audience and fostering a new generation of engineers and designers.
- Custom Manufacturing: The versatility of ATC CNC routers makes them ideal for custom manufacturing. Whether it’s producing one-of-a-kind components or small-scale production runs of unique products, these machines offer the precision and adaptability needed to bring bespoke designs to life. The automatic tool changer ensures that the manufacturing process remains agile and capable of handling diverse requirements without sacrificing efficiency.
Advantages and Disadvantages
The ATC CNC router provides a seamless transition between different tools during the machining process. Its emergence has changed the way materials are formed and carved, marking a major development in efficiency and versatility. As with any technological advancement, however, the adoption of ATC CNC routers comes with its own set of advantages and disadvantages. In this part, we understand its properties from many aspects so that you can consider whether the ATC system is suitable for your workshop based on your specific needs and requirements.
Advantages of ATC CNC Router
- Increased Productivity: The primary advantage of an ATC CNC router lies in its ability to significantly enhance productivity. By automating the tool-changing process, these machines can operate continuously, minimizing downtime associated with manual tool changes. This feature is particularly advantageous in high-volume production environments.
- Versatility: The ability to automatically switch between different tools allows for greater versatility in machining. With the capability to house and utilize various cutting tools, including end mills, drills, and routers, these machines can tackle a wide range of machining operations. This makes them suitable for industries with diverse manufacturing needs.
- Complex Machining: ATC CNC routers are well-suited for projects that involve intricate designs and multiple machining operations. They can handle tasks such as carving, engraving, and cutting with different tools in a single setup.
- Time Savings: By eliminating the need for manual tool changes, ATC CNC routers can significantly reduce the total machining time, contributing to faster job completion.
- Reduction of Human Error: Automation not only improves efficiency but also reduces the likelihood of human error. ATC CNC routers eliminate the need for manual tool changes, minimizing the risk of mistakes that can arise from operator intervention.
- Precision and Accuracy: Precision is the hallmark of CNC machining, and ATC CNC routers take this to the next level. The automatic tool-changing system ensures that the correct tool is used for each specific operation, contributing to the overall precision and accuracy of the finished product.
Disadvantages of ATC CNC Router
- Initial Cost: ATC CNC routers tend to have a higher upfront cost compared to their manual tool change counterparts. This can be a significant factor for small businesses or individuals with budget constraints.
- Maintenance Complexity: To ensure the smooth operation of the auto tool changer, regular maintenance is required. ATC systems involve more complex machinery and additional components, which may require more maintenance.
- Limited Tool Storage: The number of tools that can be stored in an ATC system is limited by its design and capacity. This limitation may affect the suitability of the router for certain projects with a large number of tool changes.
- Programming Complexity: Programming an ATC CNC router can be more complex than programming a manual tool change machine. Proper toolpath planning and tool change sequencing help maximize the benefits of an ATC system.
What factors should be considered when choosing ATC CNC router?
For any workshop or manufacturing facility, the process of choosing an automatic tool changer (ATC) CNC router requires a careful evaluation of a variety factors to ensure that chosen machine aligns specific operational needs and long-term goals. Here are key considerations to keep in mind when choosing an ATC CNC router:
- Tool Capacity: Determine the number of tools required for your typical projects. Different ATC CNC routers come with varying tool capacities. The tool carousel can accommodate a specific number of tools, and the choice of machine depends on the complexity of the machining tasks at hand.
- Tool Selection: The range of tools that an ATC CNC router can accommodate is a crucial consideration. Manufacturers must assess the compatibility of the machine with the cutting tools required for their specific applications.
- Speed and Performance: Evaluate the speed at which the ATC system can change tools. The speed at which an ATC CNC router can change tools directly impacts its overall performance. High-speed tool-changing systems contribute to reduced cycle times and increased throughput.
- Material Compatibility: Consider the types of materials you will be working with (wood, metal, plastic, etc.) and ensure that the ATC CNC router is suitable for the desired applications.
- Precision and Repeatability: Consider the rigidity and stability of the machine’s construction. A rigid structure contributes to better accuracy and precision in machining. Evaluate ATC CNC machine repeatability to ensure consistent and high-quality results in production.
- Future Trends and Upgrades: As technology continues to advance, the landscape of CNC machining, including ATC CNC routers, is poised for further innovation. Check if the machine is compatible with future upgrades or accessories, allowing for scalability as your business grows.
Summarize
ATC CNC routers stand at the forefront of modern manufacturing, embodying precision, efficiency, and versatility. From automating tool changes to handling complex machining tasks, these machines have become indispensable in industries ranging from woodworking to metalworking and beyond. While ATC CNC routers offer enhanced efficiency and capabilities for certain applications, users need to weigh the advantages against the higher upfront costs and potential complexities associated with maintenance and programming. The choice between an ATC and a manual tool change CNC router depends on the specific requirements of the machining tasks and the available budget.
At AccTek CNC, we produce heavy-duty 3-axis CNC routers, 3D 4-axis, and 5-axis CNC routers, all of which can be equipped with auto tool changers for 4-12 tools according to user needs. The specific number of tools is determined based on the complexity of your processing project. Contact us to find out which type of CNC router is right for your workshop.
Want To get a good machine?
Click the button, our CNC Experts will contact you and send you a solution.