- 8-12 Min Read
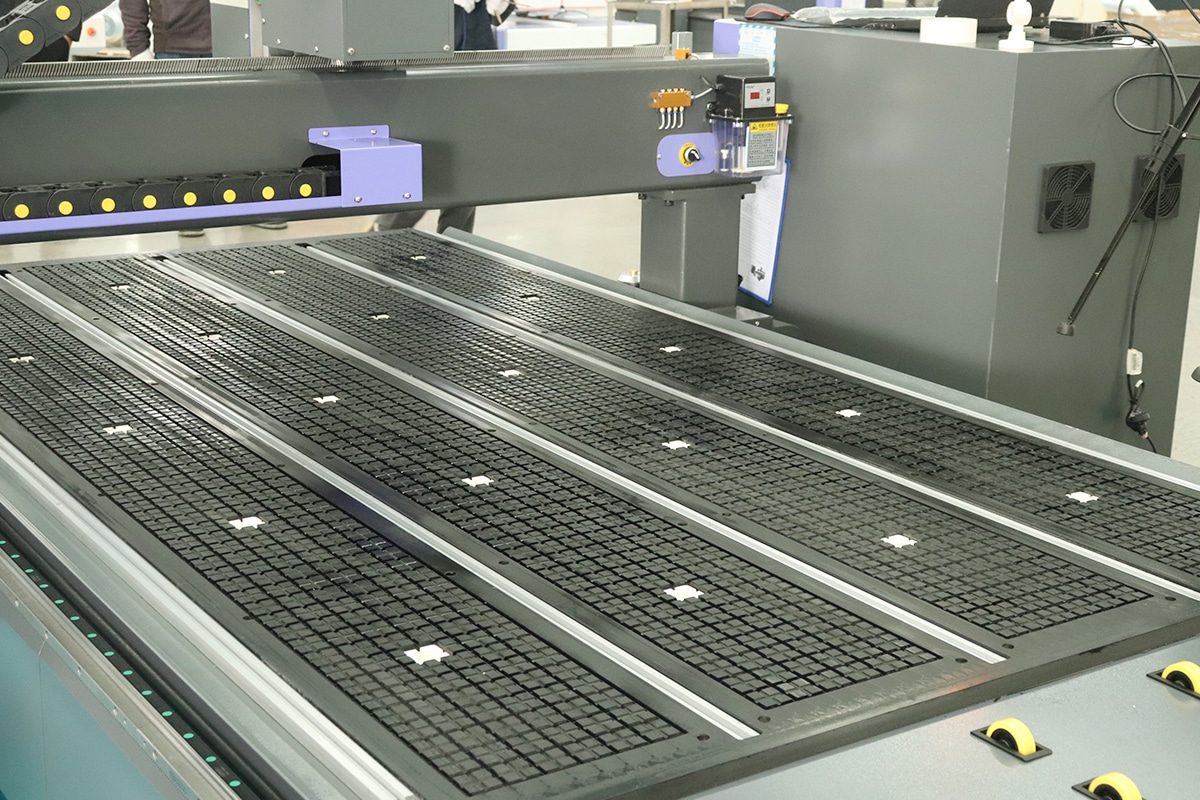
Understand the basic information of vacuum worktable
Composition of vacuum worktable
The composition of a vacuum worktable can vary based on the specific design and intended application. However, there are common components found in most vacuum worktables used in machining processes, particularly with CNC (Computer Numerical Control) router machines. The combination of these components allows the vacuum worktable to securely hold workpieces of various shapes and sizes, contributing to the precision and efficiency of CNC machining processes. Here are the key components that make up a typical vacuum worktable:
- Table Surface: The surface of the vacuum worktable is usually a flat, rigid platform designed to support the workpiece. This surface may be made of materials such as aluminum, steel, or composite materials.
- Perforated Surface: The table surface is perforated with a grid or pattern of small holes. These holes allow the vacuum to create suction, holding the workpiece in place during machining.
- Vacuum Channels or Grid: Beneath the table surface, there is a network of channels or a grid that connects to the vacuum system. This network allows the vacuum force to be distributed evenly across the entire workpiece.
- Vacuum Pump: The vacuum pump is a critical component that creates the negative pressure required for holding the workpiece in place. It generates suction by removing air from the vacuum system.
- Vacuum System Controls: The vacuum system is equipped with controls that allow operators to adjust the level of suction based on the material, size, and shape of the workpiece. This control may include valves, pressure regulators, and vacuum gauges.
- Gasket or Sealing Material: To create an effective seal and prevent air leakage, there is often a gasket or sealing material around the edges of the vacuum worktable. This ensures that the vacuum force is concentrated on the workpiece.
How a vacuum table works?
The working principles of a vacuum worktable involve the creation of a negative pressure, or vacuum, to securely hold a workpiece in place during machining operations. This vacuum-based holding mechanism is especially useful in CNC routing, providing stability, precision, and efficiency during various cutting, milling, and engraving processes. Here’s a step-by-step explanation of the working principles:
- Workpiece Placement: The workpiece is placed on the perforated surface of the table. When the vacuum pump is activated, it creates a negative pressure, causing the air to be evacuated from the vacuum channels and through the perforations.
- Suction Force: As air is removed, the atmospheric pressure on the top side of the workpiece becomes higher than the pressure on the bottom side. This pressure difference generates a suction force that holds the workpiece securely against the table surface.
- Release: To release the workpiece, the vacuum pump is deactivated, equalizing the pressure and allowing the workpiece to be easily lifted off the table.
Advantages of Vacuum Worktable
Unobstructed Access
Enhance Workpiece Stability
Increase Productivity
Enhanced Precision
Reduced Setup Time
Material Compatibility Versatility
Customization through Controls
Reduced Material Waste
Integration with CNC Systems
Applications of Vacuum Worktable
Woodworking
- Precision Cutting and Milling: In woodworking, vacuum worktables are utilized for precision cutting and milling of wooden components. The vacuum system secures wooden sheets or workpieces in place, allowing CNC routers to execute intricate designs with accuracy.
- Craftsmanship in Furniture Making: Furniture manufacturers leverage vacuum worktables to craft intricate furniture components. The stability provided by the vacuum system ensures precise shaping and detailing, contributing to the overall quality of the finished furniture pieces.
- Panel Processing: In the production of wooden panels used in cabinetry and construction, vacuum worktables facilitate the accurate processing of large wooden sheets. This is particularly valuable for tasks such as panel sizing and edge banding.
Metalworking
- Precision Machining of Metal Components: Metalworking industries benefit from vacuum worktables for the machining of metal components. Whether cutting, milling, or shaping metallic materials, the vacuum system securely holds the workpiece, ensuring the precision required in aerospace, automotive, and general metal fabrication.
- Aerospace Component Manufacturing: In aerospace manufacturing, where precision is paramount, vacuum worktables play a crucial role. They are employed for the machining of intricate components used in aircraft, spacecraft, and other aerospace applications.
- Sheet Metal Fabrication: Vacuum worktables contribute to the efficiency of sheet metal fabrication processes. The secure fixation of thin and delicate metal sheets during cutting and shaping operations ensures accurate results in applications ranging from electronics enclosures to automotive components.
Plastic Fabrication
- Molding and Shaping Plastic Materials: In plastic fabrication, vacuum worktables are utilized for molding and shaping plastic materials. Whether creating prototypes, packaging, or intricate plastic components, the vacuum system ensures a stable hold during CNC routing and shaping processes.
- Signage Production: The production of detailed and precise signage often involves the use of vacuum worktables. The vacuum system secures various materials, including plastics, allowing CNC machines to engrave detailed designs and lettering with finesse.
Prototyping and Rapid Manufacturing
- Rapid Prototyping: In industries focused on rapid prototyping and product development, vacuum worktables expedite the process. The ability to securely hold diverse materials enables the creation of prototypes with intricate features, allowing for rapid iteration and design refinement.
- Custom Manufacturing: For manufacturers involved in custom and small-scale production runs, vacuum worktables offer a flexible solution. The adaptability to different workpiece sizes and shapes makes them suitable for the varied demands of custom manufacturing.
Precautions for using vacuum worktable
Inspection and maintenance
- Regular Inspections: Conduct regular visual inspections of the worktable, vacuum hoses, and fittings for signs of wear, damage, or degradation. Address any issues promptly to maintain optimal performance.
- Check and Maintain Vacuum System: Regularly inspect and maintain the vacuum pump and system to ensure proper functioning. Monitor vacuum levels to prevent unexpected loss of holding force.
- Seal Integrity: Inspect and maintain the seals on the worktable to prevent air leaks. Verify that the seals are in good condition and replace them if necessary.
Material Availability
- Material Compatibility: Ensure that the material being processed is compatible with the vacuum system. Consider the porosity and surface characteristics of the material to ensure effective suction.
- Material Flatness: Ensure that the material being processed is flat and free of warps or irregularities that may affect the vacuum seal.
Safety Measures
- Proper Workpiece Placement: Ensure that the workpiece is placed evenly on the worktable to promote uniform clamping force. Avoid overhanging workpieces beyond the table edges, as this may compromise stability.
- Secure Fixturing: For irregularly shaped or small workpieces, use additional fixturing methods (e.g., jigs or supports) to enhance stability. Avoid relying solely on the vacuum for workpieces that may be prone to tipping or shifting.
- Consider Workpiece Weight: Be mindful of the weight capacity of the vacuum worktable and avoid exceeding it. Distribute heavier workpieces evenly across the table to prevent uneven stress on the system.
- Emergency Stop Procedures: Familiarize operators with emergency stop procedures in case of a sudden loss of vacuum or other unexpected events. Ensure that emergency stop controls are easily accessible.
- Operator Training: Provide thorough training to operators on the proper use and maintenance of the vacuum worktable. Emphasize the importance of following safety protocols and procedures.
- Noise and Vibration Monitoring: Monitor and address excessive noise or vibration during operation, as these may indicate issues with the vacuum system or the machining process.
Vacuum Pump Selection
- Pump Type: There are different types of vacuum pumps, including rotary vane pumps, diaphragm pumps, and scroll pumps. Choose a pump type that is suitable for your specific application and provides the required performance characteristics.
- Oil-Lubricated vs. Oil-Free: Decide whether an oil-lubricated or oil-free vacuum pump is more suitable for your application. Oil-free pumps are often preferred in situations where oil contamination is a concern, such as in cleanroom environments.
- Noise Level: Consider the noise level of the vacuum pump, especially if the work environment has noise restrictions. Some applications, particularly in the laboratory or quiet workspaces, may require low-noise vacuum pumps.
Integrate with CNC Equipment
- Compatibility: Ensure that the vacuum worktable is compatible with the CNC machine or other equipment. Check for matching sizes, connection interfaces, and overall design compatibility.
- CNC Machine Specifications: Review the specifications of the CNC machine, including its weight capacity, size constraints, and vacuum requirements. The vacuum worktable should align with these specifications to ensure seamless integration.
- Control System Integration: Ensure that the control systems of the vacuum worktable and CNC machine can communicate seamlessly. This may involve integrating the control interfaces, such as PLCs (Programmable Logic Controllers) or other communication protocols.