Stone CNC Router
Our stone CNC routers are engineered for precision and efficiency in cutting, carving, and shaping a wide range of stone materials, from marble and granite to quartz and limestone. Designed for both professionals and hobbyists, these advanced CNC routers combine cutting-edge technology with user-friendly interfaces, delivering exceptional results every time.
Whether you’re working on intricate designs for countertops, sculptures, or architectural features, our stone CNC routers offer unmatched accuracy and versatility. Equipped with high-speed spindles and durable components, they can handle even the toughest stone surfaces with ease. The robust construction ensures longevity and minimal maintenance, making these machines a reliable asset for any stoneworking operation.
Ideal for stone fabrication shops, artisans, and large-scale manufacturers, our CNC routers are available in a variety of configurations to suit different project needs. From small-scale engraving to large-format stone cutting, our products deliver top-tier performance, helping you achieve fine detail and high productivity. With customizable features and easy integration into your existing workflow, our stone CNC routers are the perfect solution for anyone looking to elevate their stoneworking capabilities and enhance production efficiency.
Tips for Choosing the Right Stone CNC Router
Selecting the right stone CNC router for your needs can significantly impact the quality, efficiency, and cost-effectiveness of your stoneworking projects. With various models and features available, it’s essential to consider factors such as material compatibility, machine size, power, and ease of use.
Assess Material Compatibility
Ensure the CNC router is designed to handle the specific types of stone you plan to work with, such as granite, marble, or quartz. Different materials require different cutting speeds, spindle power, and tooling configurations. Choose a machine optimized for your material to ensure maximum performance and longevity.
Consider Cutting Area Size
The cutting area determines the size of stone slabs the CNC router can handle. Consider your largest stone pieces and choose CNC routers with an appropriately sized cutting bed. The larger cutting area provides flexibility for bigger projects, while a smaller area may be sufficient for smaller jobs.
Look for High-Speed Spindles
High-speed spindles are critical for the smooth, efficient cutting of stone. The CNC router with a powerful spindle motor will allow for faster operation, reducing production time. Make sure the spindle speed can be adjusted to match the type of stone you are working with.
Evaluate Precision and Accuracy
Precision is key when working with stone, especially for intricate designs. Check for CNC routers with high accuracy, such as a repeatable cutting tolerance of 0.01mm or better. High precision ensures that your designs come out as intended, minimizing waste and rework.
Opt for Durability and Stability
Stone cutting demands durability. Choose a CNC router with a sturdy build, robust frame, and reinforced components to withstand the vibrations and stress that come with stoneworking. A stable machine will ensure consistent performance and prevent wear and tear over time.
Check for Dust Collection Features
Stone cutting generates a significant amount of dust, which can affect both machine performance and operator health. Look for CNC routers with integrated dust collection systems to keep the workspace clean and maintain optimal machine performance. A good dust system will reduce maintenance needs.
Consider Automation and Software Integration
CNC routers with automation capabilities and intuitive software make the stoneworking process more efficient. Look for models that are compatible with popular CAD/CAM software for easy design imports and machine control. Automation reduces manual effort and enhances productivity.
Prioritize User-Friendly Controls
If you’re new to CNC routing, choose CNC routers with an easy-to-use control interface. Look for machines with touch screens, clear menus, and simplified setup processes. A user-friendly control system minimizes the learning curve and improves overall workflow efficiency.
Factor in Machine Power
The power of the motor and spindle plays a critical role in cutting through dense stone materials. Ensure the CNC router has sufficient horsepower to cut through your specific stone types without straining the machine. Higher power is essential for tougher materials like granite.
Examine Tool Compatibility
Tool compatibility is important for achieving desired finishes on stone surfaces. Make sure the CNC router supports a variety of stone-cutting tools, such as diamond-tipped bits, to handle different textures and finishes. Check for tool changers that can automatically switch tools during operation for increased productivity.
Review Maintenance Requirements
Routine maintenance is crucial to keep your CNC router in top working condition. Choose a model that is easy to maintain, with accessible parts for cleaning and regular servicing. Machines with self-lubricating systems or minimal maintenance needs can save you time and effort in the long run.
Consider After-Sales Support
Select a CNC router that comes with solid after-sales support, including customer service and technical assistance. A comprehensive warranty gives you peace of mind knowing that any issues with the machine will be covered. Check the warranty terms and service options before making a purchase.
What Materials Can the Stone CNC Router Cut
Stone CNC routers are versatile machines capable of cutting, engraving, and shaping a wide variety of stone materials. These CNC routers are ideal for working with natural stones like marble, granite, and limestone, as well as engineered stones such as quartz and composite materials. Whether you’re crafting intricate designs for countertops, tiles, sculptures, or architectural features, the CNC router provides the precision and power required to handle both soft and hard stones with ease. With the right tooling and settings, these CNC routers can tackle materials of varying densities, ensuring high-quality results across a broad range of stone types.
- Marble
- Granite
- Limestone
- Travertine
- Sandstone
- Slate
- Basalt
- Quartzite
- Travertine
- Onyx
- Soapstone
- Talc
Application Industry
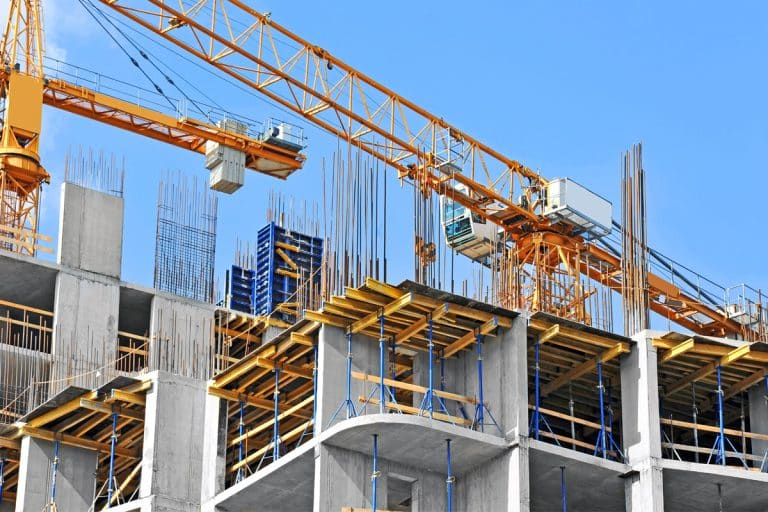
Construction Industry
The integration of CNC routers into construction workflows has ushered in a new era characterized by meticulous detailing, rapid prototyping, and improved material utilization.
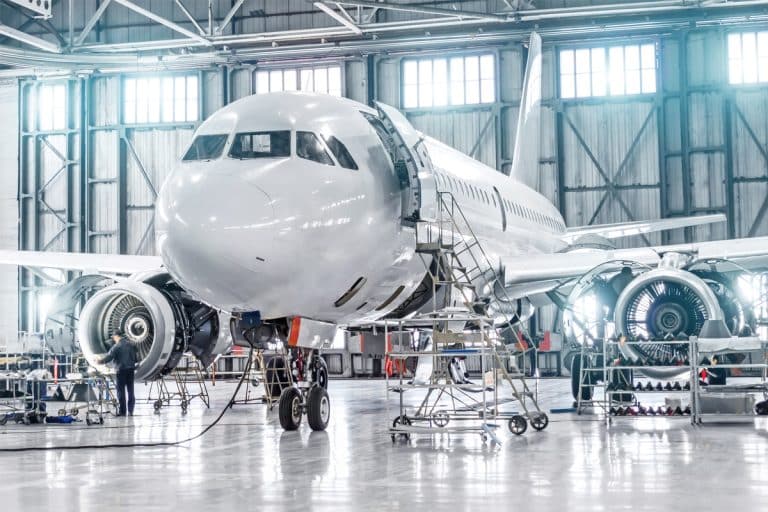
Aerospace Industry
The CNC router is widely used in aerospace engineering due to its unparalleled ability to carve complex designs, manufacture complex parts, and ensure tight tolerances.
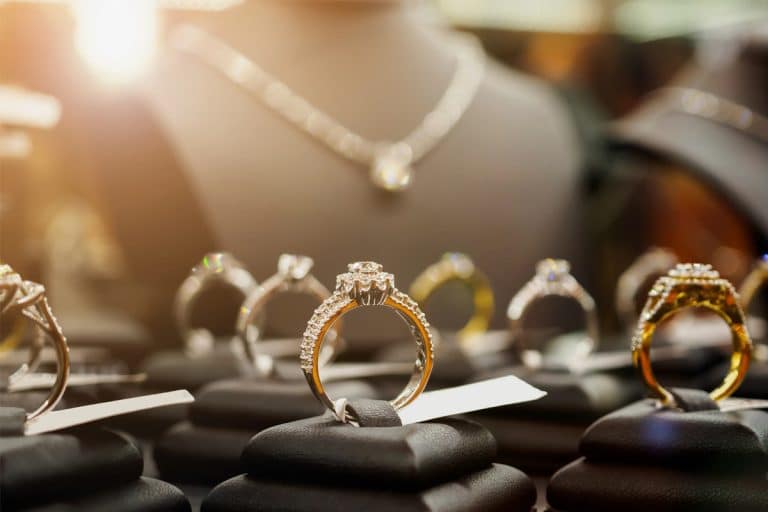
Jewelry Industry
The CNC router revolutionize the way fine jewelry is designed and made by delivering unparalleled precision and efficiency and producing intricate designs with meticulous attention to detail.
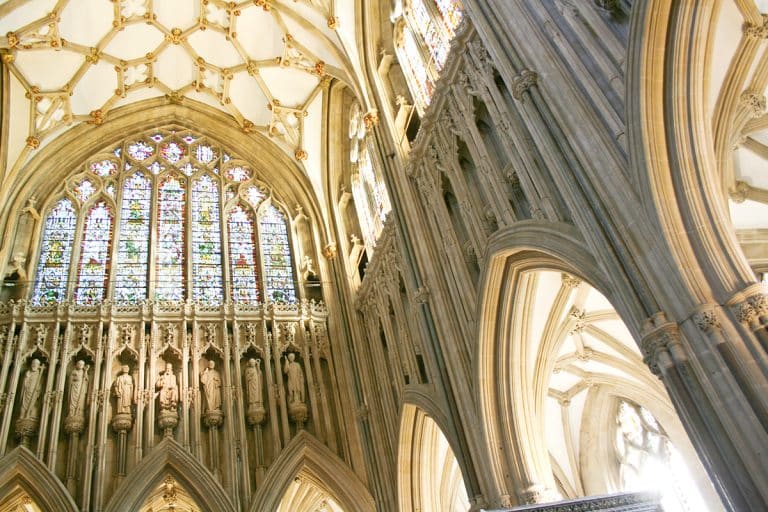
Stone Carving Industry
The integration of CNC routers into the stone carving industry is not only revolutionizing the way craftsmen carve, it is also redefining the boundaries of artistic possibilities in this ancient practice.
Blog
How to Choose the Right Stone CNC Router for Your Workshop?
This guide will walk you through the key factors to consider when choosing a stone CNC router, designed to help you invest wisely in a machine that delivers reliable performance ...
Read More
Best Budget CNC Router for Making Outdoor Signs?
In this guide, we'll break down the key features to look for, explore different models under a variety of price points, and help you choose the best budget CNC router ...
Read More
How to Maintain and Troubleshoot the ATC CNC Router?
This article will walk you through a practical maintenance procedure for your ATC CNC router and instruct you on how to diagnose and repair common problems that may arise.
Read More
What Warranties Are Typically Offered on CNC Routers?
In this article, we'll break down the different types of warranties typically offered on CNC routers, what's included, and how to make sure you're getting the support you need long ...
Read More
Frequently Asked Questions
Can CNC Routers Cut Stone?
Yes, CNC routers can cut stone. Stone CNC routers are specifically designed to handle various types of stone, including granite, marble, limestone, and more. These machines utilize specialized cutting tools, such as diamond or carbide router bits, to tackle the hardness and density of stone materials.
Operating with advanced computer numerical control (CNC) technology, these routers precisely carve intricate designs into the stone surface. The machine moves the cutting tool along multiple axes, following a programmed design to ensure accurate and consistent results.
Unlike traditional woodworking or metalworking CNC routers, which aren’t suited for stone, dedicated stone CNC routers are built with the necessary features and tools for effective stone cutting, shaping, and engraving. This makes them ideal for applications in architecture, art, interior design, and other industries requiring detailed stonework.
How Do Stone CNC Routers Work?
Stone CNC routers operate using advanced computer numerical control (CNC) technology to precisely control the movement of the cutting tool. Here’s a step-by-step overview of how they work:
- Design Input: The process begins with a digital design created in computer-aided design (CAD) or computer-aided manufacturing (CAM) software. This design outlines the pattern, shape, or carving that will be made on the stone surface.
- Programming: The digital design is converted into a CNC program containing a series of instructions. These instructions determine the cutting tool’s path, depth, speed, and other crucial parameters for executing the design accurately.
- Material Setting: The stone slab is securely mounted on the CNC router bed. Proper fixation is essential to ensure stability and minimize movement during the cutting process.
- Tool Selection and Setup: The appropriate cutting tool, such as a diamond or carbide bit, is chosen based on the type of stone and the design requirements. The tool is then installed on the CNC router’s spindle.
- Machine Calibration: The CNC router is calibrated to ensure it moves with precision. This step accounts for any adjustments needed based on machine structure or material placement.
- Execution of CNC Program: The CNC operator starts the machine, which then follows the programmed instructions to move the cutting tool along the specified path, carving or cutting the design into the stone.
- Dust Collection and Cooling: As the CNC router cuts, a dust collection system removes debris, ensuring a clean work environment. Cooling systems may also be used to prevent the cutting tools from overheating during extended operations.
- Completion and Quality Inspection: After the routing is complete, the finished stone piece is inspected for quality. The precision of CNC routing ensures that the design is executed consistently and accurately, resulting in high-quality products.
What Router Bit Do Stone CNC Routers Use?
Stone CNC routers require specialized router bits designed to handle the hardness and abrasiveness of stone materials. These bits differ significantly from those used in woodworking or metalworking due to the unique challenges posed by stone. The most commonly used router bits for stone CNC routers include:
- Diamond Router Bits: Diamond router bits are the most popular choice for stone CNC routing. Due to the diamond’s exceptional hardness, these bits can effectively cut through tough stones like granite and marble. They come in various forms, such as straight bits, ball-end bits, V-bits, and engraving bits, each suited for different applications.
- Carbide Router Bits: Carbide bits are an alternative for cutting softer stones like limestone and sandstone. While not as hard as diamonds, carbide bits are durable and available in shapes like straight, ball-end, and V-bits, offering versatility for carving and cutting.
- Polycrystalline Diamond (PCD) Bits: PCD bits use polycrystalline diamonds, providing superior durability and cutting performance. These bits excel in cutting abrasive materials like quartzite and are ideal for high-precision work on hard stones.
- Engraving Bits: Engraving bits are designed for fine, detailed work, such as carving intricate patterns or designs. Typically, they feature a V-shaped or conical profile, enabling the creation of sharp, detailed lines on stone surfaces.
- Polishing Bits: In addition to cutting, stone CNC routers can also use polishing bits to achieve smooth, glossy finishes on stone surfaces. These bits, often embedded with diamond particles, are essential for post-cutting polishing to enhance the stone’s appearance.
How to Maintain Stone CNC Routers?
Proper maintenance of your stone CNC router is essential for ensuring its longevity, reliability, and optimal performance. Here are some key maintenance practices:
- Regular Cleaning: Keep the machine clean by removing dust, debris, and stone particles from the work area, guide rails, and spindles. Use a brush and air compressor to effectively clean these areas, preventing buildup that could affect performance.
- Lubrication: Lubricate moving parts, including bearings, ball screws, and linear guides, according to the manufacturer’s guidelines. Regular lubrication reduces friction and ensures smooth and efficient operation.
- Check Alignment and Calibration: Regularly verify and recalibrate the machine to maintain cutting accuracy. Ensure that the axis alignment, tool calibration, and the machine’s level and plumpness are correct to prevent errors during operation.
- Inspect and Replace Worn Parts: Examine cutting tools, chucks, belts, and other parts for wear and tear. Replace damaged or worn parts promptly to maintain consistent performance.
- Spindle Maintenance: Monitor the spindle for abnormal noise, vibration, or overheating. Ensure proper cooling and ventilation to prevent spindle failure during extended operations.
- Inspect Tool Holders and Chucks: Regularly check and clean tool holders and chucks to remove debris. Ensure that tools are securely fastened to prevent vibrations or inaccuracies during cutting.
- Dust Removal System: Clean and maintain the dust removal system to ensure efficient operation. Replace filters and empty the dust collection container as necessary.
- Electrical Components: Inspect electrical wiring, components, and connections for any signs of wear or damage. Address any issues promptly to avoid electrical failures.
- Software Updates: Ensure that your CNC control software is up to date by installing any available updates or patches. Keeping the software current ensures compatibility with new features and improvements.
- Operator Training: Ensure that operators are well-trained in machine operation, maintenance procedures, and safety protocols. Well-trained staff can identify and address issues early, preventing costly repairs.
- Emergency Stop and Safety Check: Regularly test emergency stop buttons and other safety features to ensure they function correctly. Routine safety inspections are vital to preventing accidents and ensuring safe operation.
- Regular Professional Maintenance: Schedule periodic professional inspections by qualified technicians. Expert maintenance can identify potential issues before they become major problems, extending the life of your CNC router.
What Is the Expected Lifespan of Stone CNC Routers?
The expected lifespan of stone CNC routers can vary significantly depending on factors such as the quality of the machine, frequency of use, maintenance practices, and operating conditions. On average, a well-maintained stone CNC router can last between 10 to 15 years or more. Key factors influencing the lifespan include:
- Quality of Components: High-quality CNC routers with durable components like precision spindles, motors, and frame structures tend to have a longer lifespan.
- Maintenance: Regular and proper maintenance, including cleaning, lubrication, and calibration, can extend the lifespan of the machine by preventing premature wear and tear.
- Usage Intensity: CNC routers used for heavy, continuous operations may experience more wear and may require parts replacement sooner than those used less frequently.
- Operating Conditions: Machines used in optimal conditions with proper dust extraction, cooling, and stable power supply tend to last longer.
- Upgrades and Software Support: Regular software updates and hardware upgrades (when needed) can keep the CNC router functioning at its best and prolong its life.
What Are the Disadvantages of Stone CNC Routers?
While stone CNC routers offer exceptional precision and versatility, there are several disadvantages to consider when deciding if this technology is right for your business or project:
- High Initial Cost: Stone CNC routers can be expensive to purchase and install. The cost of the machine, along with any necessary accessories, tools, and setup, can be a significant investment, making it challenging for small businesses or hobbyists to afford.
- Maintenance Costs: CNC routers require regular maintenance to ensure optimal performance. Routine tasks such as lubrication, part replacement, and calibration can lead to ongoing costs. Additionally, replacing worn or damaged parts like spindles or cutting tools can add up over time.
- Complexity and Learning Curve: Operating stone CNC routers require specialized knowledge and expertise. For businesses without experienced operators, the learning curve can be steep. The programming, setup, and operation of the machine may also require ongoing training and troubleshooting.
- Space Requirements: Stone CNC routers are large, heavy machines that require a substantial amount of space in the workshop or production facility. This can be a challenge for smaller workshops with limited room for large machinery.
- Material Waste: Although CNC routers are precise, improper settings or operator errors can result in material waste. Mistakes in design, programming, or machine setup may lead to scrap, which could be costly when working with expensive stone materials.
- Limited to Certain Materials: Stone CNC routers are designed specifically for cutting and engraving stone. While they can handle various types of stone, they may not be suitable for cutting other materials such as wood, plastic, or metal, requiring additional machines for a diversified range of projects.
- Maintenance of Dust and Noise: Stone cutting produces significant dust and noise. Even with dust collection systems in place, the work environment can be challenging. Ensuring that workers have appropriate protective gear and that the dust is properly managed is crucial to maintaining a safe and clean workspace.
- Energy Consumption: Stone CNC routers are power-intensive machines that consume a lot of electricity, especially when running continuously. The energy costs can add up, particularly for businesses operating multiple machines.
What Customer Support Do Stone CNC Routers Provide?
Stone CNC routers come with reliable customer support options to ensure smooth operation and user satisfaction:
- Free Online Technical Support: Customers can access complimentary technical assistance through online platforms, including email, chat, or video support. This service is ideal for troubleshooting, software setup, or resolving operational issues remotely.
- Paid On-Site Training: For users requiring hands-on guidance, on-site training sessions are available at an additional cost. These sessions cover installation, operation, and maintenance to ensure optimal use of the machine.
What Is The Warranty Period of Stone CNC Routers?
Our CNC router is backed by a comprehensive warranty designed to give you peace of mind and protect your investment:
- 3-Year Warranty for the Entire Machine: This full warranty covers any defects or malfunctions in the machine as a whole, ensuring reliable performance and longevity over time.
- 5-Year Warranty for Core Components: Key components essential for optimal machine operation are covered for 1.5 years. This includes parts that may experience wear and tear with regular use, ensuring you have support for the most vital parts of the machine.