- 11-16 Min Read
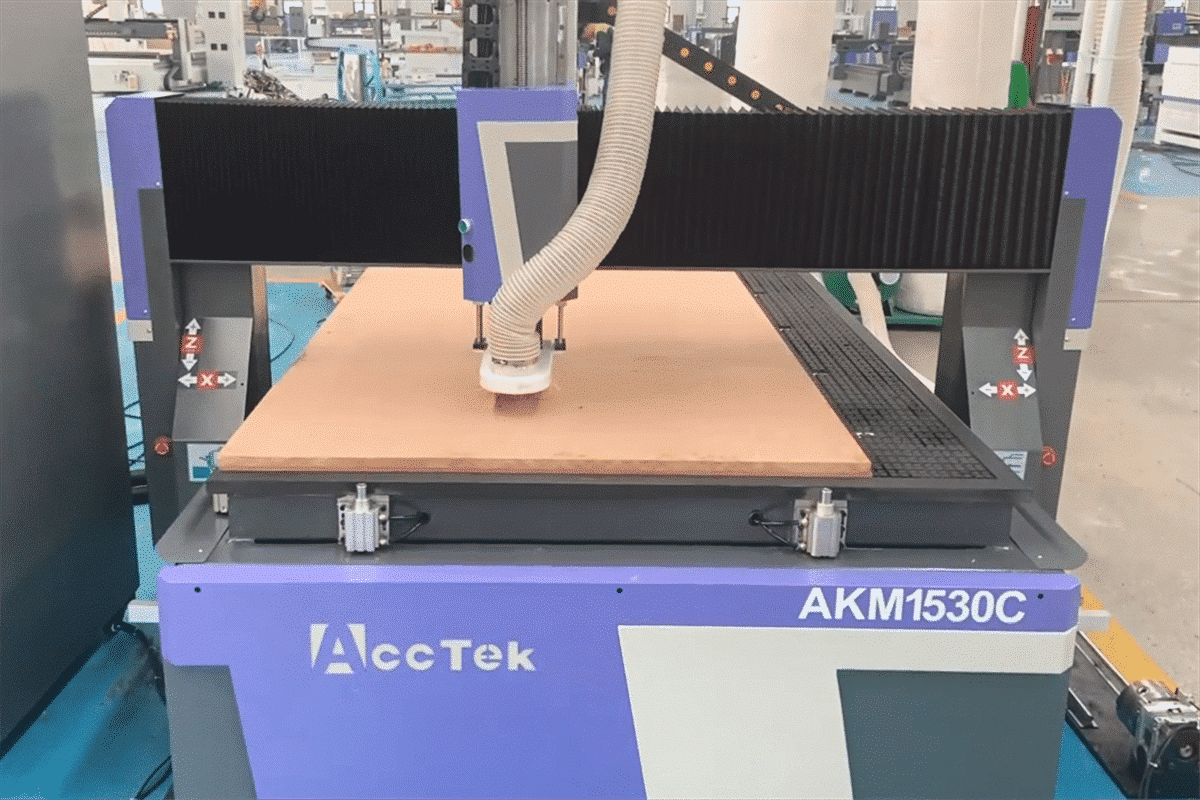
In the world of computer numerical control (CNC) machining, precision and efficiency reign supreme. Whether you’re crafting intricate designs or producing large-scale components, the efficiency of your CNC router’s tool path can make all the difference in the quality and speed of your production process. However, achieving optimal tool paths isn’t always straightforward; it requires a nuanced understanding of machining principles, software capabilities, and material characteristics.
In this comprehensive guide, we delve into the intricacies of optimizing tool paths for CNC routers. We’ll explore the fundamental principles behind tool path optimization, discuss the key factors to consider when designing paths, and introduce advanced techniques to enhance efficiency and precision. Whether you’re a seasoned CNC machinist looking to refine your skills or a newcomer eager to learn the ropes, this article will provide valuable insights and practical tips to help you unlock the full potential of your CNC router.
Understanding Tool Path
The tool path defines the movement of the cutting tools across a workpiece to produce the desired shape or feature. At the beginning of the article, we first have a basic understanding of tool paths.
Definition of Tool Paths
Tool paths are the geometric trajectories or paths that a cutting tool follows during the manufacturing process. These paths are typically specified in terms of coordinates in a numerical control (NC) program or CAM software. The tool paths dictate the movement of the tool along the X, Y, and Z axes relative to the workpiece, controlling factors such as feed rate, cutting depth, and tool orientation.
Relationship with CAD and CAM
- CAD (Computer-Aided Design): CAD software is used to design the part or component that needs to be manufactured. CAD software allows engineers and designers to create precise 3D models of parts, assemblies, or products. These models serve as the foundation for generating tool paths.
- CAM (Computer-Aided Manufacturing): CAM software translates CAD designs into instructions for the manufacturing process. CAM software generates tool paths based on the CAD model, taking into account factors such as material properties, cutting tool specifications, machining operations, and manufacturing constraints.
Types of Tool Paths
- Profile Tool Path: This tool path follows the outline of a 2D or 3D shape, cutting along its perimeter. It’s commonly used for cutting out shapes from a material.
- Pocket Tool Path: Pocketing involves removing material from within closed regions of the part. Pocketing tool paths efficiently clear out material within these enclosed areas. This path is often used for creating slots, holes, or pockets.
- Engraving Tool Path: Engraving tool paths are used for creating decorative or functional designs by cutting into the surface of the material. This can include text, logos, or intricate patterns.
- Drilling Tool Path: Drilling tool paths are used specifically for creating holes in the workpiece at specified locations. These paths specify the coordinates and depths at which the cutting tool should penetrate the material.
- Contour Tool Path: Contouring follows the contours of a 2D or 3D shape, maintaining a consistent distance between the tool and the workpiece surface. This path is often used for finishing operations.
- 3D Machining Tool Paths: This path is used for complex 3D shapes and involves simultaneous movement in multiple axes to accurately carve the desired geometry. 3D machining tool paths utilize sophisticated algorithms to move the cutting tool along the surface of the part, maintaining consistent cutting conditions and surface quality.
- Thread Milling Tool Path: Thread milling is used to create threaded features on the workpiece, such as screws or bolts, by gradually cutting away material in a spiral pattern.
The importance of tool path optimization
- Tool path optimization plays a critical role in maximizing efficiency, quality, and safety in CNC routing operations, ultimately leading to cost savings, improved productivity, and higher-quality finished products. The following illustrates the importance of tool path optimization:
- Efficiency: Optimized tool paths can significantly reduce machining time by minimizing unnecessary movements, tool retractions, and air cuts. This efficiency can result in lower production costs and increased productivity.
- Surface Finish: Proper tool path optimization ensures smoother cutting motions, leading to improved surface finish on the workpiece. This is particularly important for applications requiring high-quality finishes, such as woodworking, signage, and mold making.
- Tool Life: By minimizing tool wear and reducing the occurrence of tool overloading or overheating, optimized tool paths can extend the lifespan of cutting tools. This helps to lower tool replacement costs and reduces downtime for tool changes.
- Material Waste Reduction: Optimized tool paths can minimize material waste by optimizing the cutting process to use the least amount of material possible while still achieving the desired result. This is especially beneficial when working with expensive materials or when trying to maximize material utilization.
- Accuracy and Precision: Well-optimized tool paths ensure accurate and precise machining, reducing the likelihood of errors or inaccuracies in the finished parts. This is particularly important for applications where tight tolerances are required.
- Minimization of Machine Wear: Tool path optimization can help to reduce wear and tear on CNC router components such as ball screws, bearings, and motors by minimizing sudden changes in direction or excessive acceleration and deceleration.
- Safety: Optimized tool paths can also contribute to a safer working environment by reducing the risk of tool breakage, material ejection, and collisions between the tool and the workpiece or machine components.
Factors affecting tool path optimization
- Tool path optimization in CNC routers is influenced by various factors, which are specific to the capabilities and constraints of these machining systems. Here are some key factors that affect tool path optimization in CNC routers:
- Material Type: Different materials (e.g., wood, plastic, foam, composites) have unique characteristics that impact cutting parameters such as feed rates, spindle speeds, and tool selection. The choice of tool path must consider the specific material properties to achieve efficient material removal and the desired surface finish.
- Machine Bed Size and Configuration: The size and configuration of the CNC router’s bed determine the maximum workpiece dimensions and the accessibility of cutting tools to different areas of the workpiece. Tool path optimization should take into account the available workspace and the need for multiple setups if machining large or complex parts.
- Tooling Specifications: The choice of cutting tools, including their geometry, material, coatings, and size, directly impacts the tool path optimization. The selection of appropriate tools ensures optimal cutting performance and tool life.
- Axis Configuration: The number and arrangement of axes on the machine tool (e.g., 3-axis, 4-axis, 5-axis) affect the complexity and feasibility of tool paths. Higher-axis configurations offer more flexibility in tool orientation, enabling complex machining operations and reducing the need for multiple setups.
- Spindle Power and Speed: The spindle’s power and rotational speed influence cutting forces, chip formation, and heat generation during machining. Tool path optimization should consider the spindle capabilities to ensure efficient machining while maintaining stability and avoiding tool deflection.
- Workholding and Fixture Design: How the workpiece is secured on the CNC router’s bed influences the accessibility of cutting tools and the stability of machining operations. Effective workholding and fixture design enable optimal tool paths by minimizing vibrations, preventing workpiece movement, and ensuring consistent machining conditions.
- Required Surface Finish: The desired surface finish dictates the selection of machining parameters such as feed rate, cutting speed, and depth of cut. Tool paths must be optimized to achieve the specified surface roughness while balancing productivity and tool life.
- Work Tolerance: The dimensional accuracy required for the finished part influences the tool path optimization process. Tighter tolerances may necessitate finer tool movements and more precise control over machining parameters to meet quality standards.
- Complexity of Geometry: The complexity of the part geometry and features (e.g., pockets, contours, holes) determines the type of tool path strategies that can be employed. Tool path optimization should consider the geometry complexity to minimize machining time and tool movements while maintaining part accuracy and surface finish.
Tool Path Optimization Strategy
CNC router tool path optimization strategies are techniques used to enhance machining efficiency, improve surface finish, reduce cycle times, and extend tool life. Here’s a detailed breakdown of CNC router tool path optimization strategies from various aspects:
Efficient Roughing Strategies
- Adaptive Clearing: Utilize CAM software features like adaptive clearing to dynamically adjust cutting parameters for optimal material removal rates and tool life.
- High-Speed Machining (HSM): Implement high-speed machining techniques to maximize material removal rates while maintaining tool integrity.
- Optimized Stepovers: Adjust stepover values to balance material removal rates with surface finish requirements, optimizing roughing toolpaths for efficiency.
Contour and Finishing Strategies
- Constant Stepover Toolpaths: Utilize constant stepover toolpaths for contouring and finishing operations to achieve consistent surface finishes across the part.
- Z-Level Finishing: Employ Z-level finishing strategies to efficiently remove material layer by layer, resulting in smoother surface finishes.
- Profile Milling: Use profile milling techniques for precise machining of part perimeters and contours, ensuring accuracy and surface quality.
- Rest Machining: Apply rest machining strategies to remove residual material left from previous operations, reducing unnecessary toolpaths and machining time.
- Spiral Toolpaths: Use spiral or continuous toolpaths for finishing operations to minimize tool marks and achieve smoother surface finishes.
Cutting Direction Considerations
- Climb vs. Conventional Milling: Evaluate the benefits of climb milling (reduced tool wear, smoother surface finish) versus conventional milling (higher stability, lower cutting forces) based on the specific material and machining requirements.
- Optimized Toolpath Direction: Analyze part geometry and material characteristics to determine the most efficient toolpath direction, minimizing tool retractions and optimizing chip evacuation.
Intelligent Operation Sequences
- Toolpath Optimization Algorithms: Utilize CAM software algorithms to optimize toolpath sequences, minimizing tool changes, and reducing idle times.
- Batch Processing: Group similar machining operations together in sequential batches to minimize tool changes and setup times, improving overall efficiency and throughput.
- Avoidance of Air Cutting: Optimize toolpaths to minimize air cutting (cutting without material contact), reducing unnecessary tool wear and improving machining efficiency.
Use of High-Performance Toolpaths
- High-Speed Toolpaths: Implement high-speed machining toolpaths to maintain consistent chip loads and maximize cutting speeds, reducing cycle times while maintaining surface finish.
- Toolpath Smoothing: Apply toolpath smoothing algorithms to reduce toolpath jerks and vibrations, resulting in improved surface finishes and reduced tool wear.
- Dynamic Toolpaths: Utilize dynamic toolpaths that adapt to varying cutting conditions, optimizing feeds and speeds for improved performance and tool life.
- Trochoidal Milling: Utilizing trochoidal milling strategies for slotting and pocketing operations to maintain constant tool engagement and prolong tool life.
By incorporating these strategies into CNC router programming and operation, CNC router operators can maximize productivity, achieve higher quality finishes, and extend the life of cutting tools, ultimately reducing manufacturing costs and improving overall efficiency.
Toolpath Optimization Software Tools
There are several software tools specifically designed for tool path optimization in CNC routers. These tools vary in features, capabilities, and complexity, catering to the needs of different users and applications. Some popular tool path optimization software tools for CNC routers include:
- Mastercam: Mastercam is a widely used CAM software that offers powerful tool path generation capabilities for CNC routers. It provides a range of optimization features, including efficient roughing strategies, contouring, finishing, and intelligent toolpath sequencing.
- Vectric VCarve Pro and Aspire: Vectric’s VCarve Pro and Aspire are user-friendly CAM software solutions tailored for CNC routing. They offer a variety of tool path optimization tools for 2D and 3D machining, including efficient roughing, precise contouring, and detailed finishing strategies.
- ArtCAM: ArtCAM is a specialized CAM software designed for artistic and decorative CNC routing applications. It provides advanced tool path optimization features for carving, engraving, and sculpting operations, allowing users to create intricate designs with high precision.
- Fusion 360: Fusion 360 is a comprehensive CAD/CAM software developed by Autodesk. It offers powerful tool path optimization capabilities for CNC routing, including adaptive clearing, high-speed machining, and multi-axis tool paths, along with intelligent operation sequencing.
- CAMWorks: CAMWorks is a feature-based CAM software that integrates seamlessly with SolidWorks CAD software. It provides advanced tool path optimization tools for CNC machining, including automated feature recognition, adaptive roughing, and high-performance machining strategies.
- RhinoCAM: RhinoCAM is a CAM plugin for Rhino 3D modeling software. It offers a wide range of tool path optimization features for CNC routing, including efficient roughing, precise finishing, and multi-axis machining capabilities.
- BobCAD-CAM: BobCAD-CAM is a versatile CAM software solution with dedicated modules for CNC routing. It offers a variety of tool path optimization tools, including adaptive roughing, advanced finishing strategies, and intelligent toolpath sequencing.
These are just a few examples of the many software tools available for tool path optimization in CNC routers. When choosing a tool path optimization software, it’s essential to consider factors such as compatibility with your CNC router, ease of use, features required for your specific applications, and overall cost-effectiveness.
Simulation and Testing of Tool Path Optimization
The simulation and testing of CNC router tool path optimization are integral processes for enhancing machining efficiency and quality. Manufacturers can achieve superior performance, reduced cycle times, and enhanced productivity in CNC machining operations by simulating tool paths, identifying and addressing potential issues, and iteratively refining optimization strategies through testing.
Simulating Tool Paths
Simulating tool paths before actual machining execution serves as a pivotal step in the optimization process. It offers several key benefits:
- Error Identification: Simulation reveals potential errors, such as tool collisions or excessive tool deflection, enabling preemptive mitigation.
- Material Visualization: By visualizing tool movements, operators gain insights into material removal rates and surface finishes, aiding in performance prediction.
- Cycle Time Estimation: Accurate simulation facilitates the estimation of cycle times, facilitating production planning and scheduling.
Identifying and Solving Problems
Upon simulation, identifying and resolving problems within tool paths becomes imperative. Common issues include:
- Tool Collisions: Simulation highlights instances of tool collisions with the workpiece, fixtures, or clamps, necessitating adjustments in tool paths or fixture placement.
- Tool Deflection: Excessive tool deflection can lead to inaccuracies in machining. Simulation helps identify areas of high tool deflection, prompting adjustments in cutting parameters or tool selection.
- Poor Surface Finish: Simulation aids in detecting areas with suboptimal surface finishes, prompting modifications in cutting strategies or toolpath optimization.
Optimizing Iterative Testing
Iterative testing forms the backbone of tool path optimization, enabling continuous refinement and enhancement. Key aspects include:
- Parameter Variation: Through iterative testing, operators can systematically vary cutting parameters such as feed rates, spindle speeds, and stepover values to determine optimal settings.
- Toolpath Modification: Operators iteratively modify tool paths based on simulation results and machining performance, aiming to minimize cycle times and improve surface finishes.
- Performance Evaluation: Iterative testing involves a comprehensive evaluation of machining performance, including dimensional accuracy, surface finish quality, and tool longevity, driving continuous improvement efforts.
Application-Specific Considerations
Optimizing tool paths for CNC routers involves considering specific material applications to ensure efficient machining and high-quality results. Here are some considerations for common materials. By considering these material-specific factors and optimizing tool paths accordingly, CNC router operators can achieve optimal machining performance and produce high-quality parts across a wide range of materials.
Woodworking
- Grain Orientation: Optimize tool paths to account for the direction of the wood grain to minimize tear-out and achieve smoother surface finishes.
- Cutting Speed: Wood tends to burn at high cutting speeds, so optimize tool paths to maintain appropriate cutting speeds and feed rates to prevent overheating.
- Chip Evacuation: Wood chips can accumulate quickly, leading to poor cutting performance. Optimize tool paths to ensure effective chip evacuation, especially when machining deep cuts or intricate designs.
Plastics
- Heat Sensitivity: Some plastics are prone to melting or warping when subjected to high temperatures. Optimize tool paths to minimize heat buildup by adjusting cutting speeds and feed rates accordingly.
- Chip Control: Plastics can produce stringy or sticky chips that may interfere with machining. Optimize tool paths to ensure proper chip control and evacuation to prevent chip buildup and tool damage.
Metals
- Material Hardness: Metals vary in hardness, affecting tool selection and cutting parameters. Optimize tool paths to accommodate the hardness of the metal being machined by selecting appropriate cutting tools and cutting speeds.
- Lubrication: Metals often require lubrication or coolant during machining to reduce heat generation and tool wear. Optimize tool paths to incorporate lubrication or coolant application points for efficient machining.
- Work hardening: Certain metals, such as stainless steel and titanium, can work hard during machining, leading to increased tool wear and decreased cutting performance. Optimize tool paths to minimize the number of tool engagements and reduce the risk of work hardening.
Composites
- Fiber Orientation: Composites typically contain reinforcing fibers that can affect cutting performance. Optimize tool paths to account for fiber orientation and minimize delamination or fraying.
- Abrasive Properties: Some composite materials contain abrasive particles that can accelerate tool wear. Optimize tool paths to reduce tool engagement and prolong tool life when machining abrasive composites.
Foam and Soft Materials
- Material Stability: Soft materials like foam may deform or compress under cutting forces. Optimize tool paths to minimize material distortion and achieve accurate part dimensions.
- Dust Control: Soft materials can produce a significant amount of dust during machining, which may affect cutting performance and operator safety. Optimize tool paths to control dust generation and ensure effective chip evacuation.
Training and Skills Development
Becoming proficient in tool path optimization for CNC routers requires a combination of theoretical knowledge, practical skills, and hands-on experience gained through training, practice, and experimentation. Here are three key aspects of training and skill development in tool path optimization for CNC routers:
CNC Operator Training for Tool Path Optimization
CNC operators need to undergo specialized training to understand the intricacies of tool path optimization. This training involves learning how to operate CNC machines effectively, interpret CAD/CAM software-generated tool paths, and make adjustments as necessary to optimize machining processes. They learn how to input cutting parameters, select appropriate tool paths, and monitor machining operations for efficiency and accuracy.
Staying Informed About Software Updates and New Technologies
In the field of CNC machining, software updates, and new technologies are continually being developed to enhance efficiency, precision, and capabilities. CNC operators involved in tool path optimization must stay informed about these updates and advancements. This may involve attending training sessions, workshops, or webinars offered by software vendors or industry organizations. Additionally, operators may need to self-educate by reading technical publications, participating in online forums, or watching tutorial videos to stay up-to-date with the latest software features and techniques for tool path optimization.
Continuous Improvement Culture
Tool path optimization is not a one-time task but rather an ongoing process of refinement and improvement. CNC operators should be encouraged to adopt a culture of continuous improvement, where they actively seek opportunities to enhance tool path efficiency, reduce machining time, and improve surface finish quality. This involves analyzing past machining projects for areas of improvement, experimenting with different tool paths and cutting parameters, and implementing changes based on lessons learned.
Summarize
Optimizing the tool path of a CNC router is an important process for achieving efficient and precise machining operations. By considering factors such as cutting tool selection, feed rates, spindle speed, and cutting strategies, manufacturers can minimize production time and costs while maximizing the quality of finished products. Additionally, leveraging advanced software tools and simulation techniques can aid in visualizing and fine-tuning the tool path before actual machining begins, reducing the risk of errors and material wastage. Continuous experimentation and refinement of tool path optimization techniques will enable manufacturers to stay competitive in today’s fast-paced manufacturing environment, meeting the demands for accuracy, speed, and cost-effectiveness.
As a leading CNC router manufacturer in China, AccTek CNC is dedicated to providing users with top-quality machines and comprehensive after-sales support. Our range of CNC routers caters to various industries and applications, from woodworking and metalworking to signage and prototyping. Whether you’re a small workshop or a large-scale manufacturing facility, our machines are engineered to meet your specific requirements and deliver exceptional results every time. But our commitment doesn’t end with the sale of a machine. From installation and training to maintenance and troubleshooting, our team of experienced technicians is here to ensure that your machine operates at peak performance, maximizing productivity and minimizing downtime. With AccTek CNC take your CNC machining capabilities to new heights.