- 12-17 Min Read
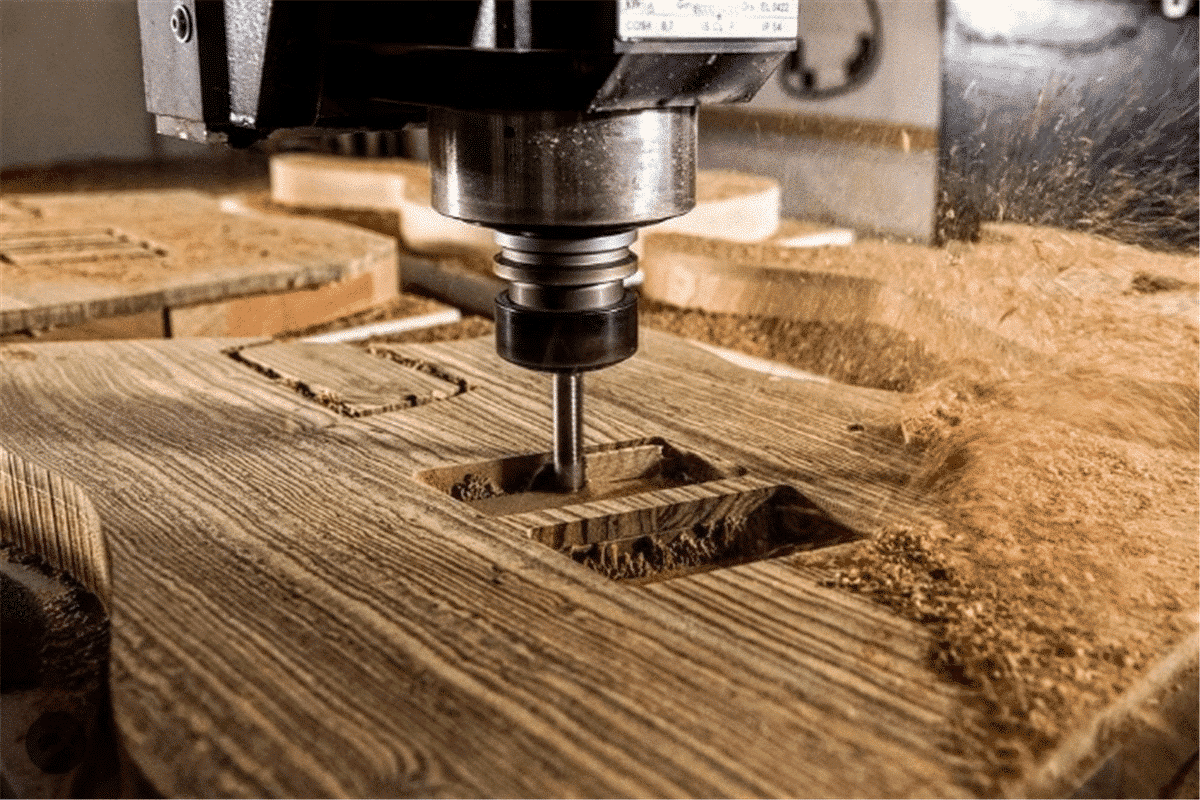
Choosing the right CNC router bit is beneficial for achieving precise and efficient cuts in woodworking projects. Whether you’re a beginner or an experienced craftsman, the variety of router bits available can be overwhelming. Each bit is designed for a specific purpose, from carving intricate details to cutting smooth edges, and selecting the appropriate one can significantly impact the quality and finish of your work. Understanding the types, materials, and cutting characteristics of CNC router bits will not only improve your work’s accuracy but also extend the life of your tools.
In this comprehensive guide, we’ll walk you through the essential factors to consider when choosing the perfect woodworking CNC router bit. We’ll explore the different types of bits, such as straight, chamfer, and roundover bits, and explain their best use cases. You’ll also learn about the importance of bit material, coating, and shank size, helping you make informed decisions based on your project requirements. By the end of this guide, you’ll have a solid understanding of how to select the most suitable CNC router bit for your woodworking needs, ensuring both optimal performance and professional results.
Basics of Router Bit
Router bits are vital components in woodworking and CNC machining, designed for cutting, shaping, and engraving materials. To choose the right router bit, it is important to understand its structure and the types available. Here are their basic information:
Router Bit Structure
The structure of a router bit is composed of several key elements that work together to deliver precise cutting performance.
- The Shank: The shank is the cylindrical part of the router bit that is inserted into the router or CNC machine’s collet. It comes in two standard sizes, typically 1/4-inch or 1/2-inch in diameter. A thicker shank, such as a 1/2-inch, offers greater stability and less vibration during operation, which is an advantage in heavy-duty applications or deep cuts. The shank must be securely fastened to prevent wobbling and ensure a clean cut.
- The Body: The body is the central part of the router bit that holds the cutting edges and other features like bearings. It determines the overall shape and function of the bit. For instance, some bits have bearings attached to the body that guide the bit along the edge of the material. The design of the body varies significantly depending on the type of bit—whether it’s a straight bit, a V-bit, or a flush-trim bit—since the body’s contour influences how the bit interacts with the material.
- The Groove: The groove refers to the fluted or hollowed-out sections along the body of some router bits, which aid in the removal of chips and debris during cutting. Spiral bits, for example, have grooves that run helically along the body, helping to pull chips away from the cutting area, which results in smoother cuts and reduced material buildup. The design and number of grooves influence the efficiency of chip evacuation and the finish quality.
- The Cutting Edge: The cutting edge is the part of the router bit that makes direct contact with the material to remove it. It is crafted from either high-speed steel (HSS) or carbide, with carbide being more durable and suited for tougher materials. The cutting edge’s sharpness, angle, and length determine the precision and smoothness of the cut. Bits can have one or more cutting edges, and their sharpness and alignment determine whether a clean and accurate cut can be achieved.
These four structural components of a router bit work together to ensure precision, stability, and efficiency in cutting, shaping, and engraving materials. Understanding each part helps in selecting the right bit for specific tasks and achieving optimal results.
Router Bit Types
Router bits come in various types, each designed for specific cutting, shaping, and trimming tasks in woodworking. Here are five common types of router bits:
- Straight Bits: These are among the most versatile and widely used router bits. Straight bits are designed to cut straight, clean lines in materials, making them ideal for tasks like creating grooves, dados, and rabbets. They come in various sizes, allowing woodworkers to make cuts of different depths and widths. Straight bits are excellent for hollowing out an area in the wood or for cutting through material, making them essential for cabinet and furniture making.
- Flush Trim Bits: Flush trim bits are primarily used for trimming the edges of materials to match the template or a guiding surface. These bits have a bearing at the top or bottom that follows the template, while the cutting edge trims the material flush with it. They are especially useful for finishing the edges of veneered surfaces, trimming laminates, or duplicating shapes in workpieces. The bearing ensures precision, making it easy to achieve a smooth, consistent finish.
- Chamfer Bits: Chamfer bits are used to create angled edges, known as chamfers, on workpieces. These bits are cut at various angles, typically 45 degrees, to add beveled edges for decorative purposes or to prepare edges for joints. Chamfered edges give a finished look to furniture, cabinetry, and frames, and they also serve a practical function by softening sharp corners. Adjustable chamfer bits can be set to different angles, making them versatile for a range of applications.
- Roundover Bits: Roundover bits are designed to soften the sharp edges of a workpiece by rounding them off. These bits come in various radius sizes, allowing you to choose how pronounced the rounded edge will be. Roundover bits are commonly used for adding smooth, decorative edges to tabletops, shelves, and other furniture pieces. The rounded edge not only improves the appearance but also reduces the risk of splinters or sharp edges in the finished product.
- Cove Bits: Cove bits are the inverse of roundover bits, used to create concave, rounded grooves along the edges of a workpiece. This produces a decorative, inward curve that is often used in moldings, cabinetry, and furniture designs. Cove bits are frequently combined with other router bits, like roundover bits, to create complementary edge profiles. The smooth, curved cut from a cove bit adds an elegant, finished look to any woodworking project.
These five types of router bits each offer unique functionality for a wide range of woodworking applications, helping craftsmen achieve both practical and decorative finishes. Understanding their specific uses will allow for better selection and improved project results.
Understanding Router Bit Materials
Router bits are made from different materials, each suited for specific tasks and designed to deliver varying levels of performance and durability. When choosing a router bit, it is essential to understand the advantages of High-Speed Steel (HSS), Carbide-Tipped Bits, Solid Carbide, and Coated Bits. These materials offer distinct benefits depending on the application and material being cut.
High-Speed Steel (HSS)
HSS router bits are the most common and affordable option, often used for general-purpose woodworking. Made from an alloy that resists heat and wear, HSS bits are designed for high-speed cutting without losing their sharpness quickly. They perform well with softer woods and light-duty applications. However, HSS bits dull faster when used on harder materials like hardwoods or composite materials, and they have a shorter lifespan compared to carbide alternatives. HSS bits are ideal for beginners and for projects that don’t require heavy or prolonged cutting.
Carbide
Carbide-tipped bits feature a steel body with a carbide cutting edge, offering a blend of durability and cost-effectiveness. The carbide tip is much harder than HSS, allowing these bits to maintain their sharpness for a longer period, especially when working with tough materials like hardwoods, MDF, or plastics. Carbide-tipped bits are more heat-resistant and wear slower, making them suitable for both light and heavy-duty projects. While more expensive than HSS, carbide-tipped bits offer a good balance of cost and longevity, making them a popular choice for both professionals and hobbyists.
Solid Carbide
Solid carbide bits are made entirely from carbide, making them the most durable and heat-resistant of all router bit materials. These bits are ideal for precision work and are capable of handling the toughest materials, such as hardwood, aluminum, and abrasive composites. Solid carbide bits maintain their edge longer than both HSS and carbide-tipped bits, even under continuous use. However, they are the most expensive option, and their hardness can make them more brittle and prone to breakage if mishandled or subjected to excessive force. Solid carbide bits are typically used by professionals who require precision and longevity in their cutting tools.
Coated
Some router bits come with specialized coatings that enhance their performance and durability. Common coatings include titanium nitride (TiN), diamond coating, or aluminum titanium nitride (AlTiN). These coatings provide a layer of protection against wear and heat, reducing friction and extending the lifespan of the bit. Coated bits are especially useful in high-speed applications or when cutting abrasive materials like plywood or particleboard. The coating helps the bit maintain its sharpness and resist corrosion, making it an excellent choice for demanding projects that involve prolonged use.
By considering the properties of HSS, carbide-tipped, solid carbide, and coated router bits, users can select the best option for their woodworking or CNC machining needs. HSS is suitable for light-duty tasks, while carbide-tipped and solid carbide bits offer greater durability for heavy-duty applications. Coated bits provide an additional layer of performance, extending the life of the bit in high-wear environments.
Router Bit Outline and Shape
When selecting router bits, the outline and shape determine how they cut and handle material. These characteristics can be understood from three important aspects: straight groove and spiral groove, single edge and double edge, and point style. Each influences how efficiently the bit cuts and the type of finish it produces.
Straight Groove and Spiral Groove
- Straight Groove: Bits with straight grooves feature flat, parallel cutting edges running vertically down the length of the bit. They are typically used for making straight cuts, grooves, or dados in wood and other materials. Straight groove bits excel at removing material quickly but may cause tear-out in certain woods, especially when cutting against the grain.
- Spiral Groove: Spiral groove bits have helically wound flutes that wrap around the body of the bit, resembling a drill bit. They are designed to provide a smoother cut by pulling material away from the cutting area as they work, reducing chip buildup and leaving cleaner edges. Spiral bits are excellent for plunging cuts, and their design helps to minimize tear-out in delicate or high-speed applications, making them ideal for hard or softwoods, plastics, and composites. They come in up-cut and down-cut variations, with up-cut bits pulling chips up and out of the cut, and down-cut bits pushing chips down for cleaner surface finishes.
Single Edge and Double Edge
- Single Edge: Single-edge router bits have just one cutting edge. They are simpler in design and are generally used for lighter-duty tasks. These bits are often employed for softer woods or for situations where precision is more important than speed. The single-edge design removes material at a slower rate, but it can offer more control over the cut, especially for fine detailing or engraving tasks.
- Double Edge: Double-edge bits feature two cutting edges, which work in tandem to remove material more quickly and evenly. These bits are more efficient and can handle heavier workloads, making them ideal for high-speed cutting or when working with harder materials like hardwoods. Double-edge bits also tend to produce smoother finishes due to their balanced cutting action, as both edges cut simultaneously and evenly distribute the load on the bit.
Point Style
- Flat Point: Router bits with a flat point have a blunt or squared-off tip, making them ideal for cutting grooves, dados, or straight edges. They do not plunge well but excel in operations where the bit is moved horizontally along the material. Flat point bits are commonly used for applications like routing along the surface of a workpiece or in combination with templates.
- V-Point: V-point bits feature a sharply angled tip, typically used for engraving, veining, or decorative groove cutting. The V-shape allows for precision cutting and is perfect for fine detailing work. These bits are often used for tasks that require clean, crisp lines, such as sign-making or decorative inlay work. V-point bits can also be used for chamfering edges at specific angles.
- Ball Point: Ball point router bits have rounded tips and are typically used for cutting concave shapes or rounded grooves. These bits are excellent for creating flutes, rounded edges, or even decorative moldings. Ball point bits are also known as “core box bits” and are commonly used in applications where smooth, rounded cuts are needed.
The outline and shape of a router bit directly influence its cutting performance and the type of finish it creates. Straight and spiral grooves determine the efficiency of material removal and chip clearance, while single and double edges impact cutting speed and smoothness. Finally, the point style defines how the bit interacts with the material, whether it’s for straight cuts, engraving, or creating rounded profiles. Understanding these aspects will help in selecting the right router bit for your specific woodworking or CNC project.
Router Bit Application
Each router bit serves a specific purpose, enabling the user to achieve a variety of cuts, shapes, and finishes. Understanding the specific applications of each type of router bit ensures both efficiency and precision in woodworking or CNC machining tasks. Here’s an overview of common router bit applications, focusing on some of the most widely used types:
Edge Molding
Edge molding refers to shaping the edges of a workpiece to create decorative or functional profiles. Router bits can add an aesthetic element to furniture, cabinetry, or molding. Edge molding is widely used to create smooth transitions, rounded edges, or complex profiles that enhance the visual appeal of wood projects. Common Bit Types:
- Roundover bits: For creating soft, rounded edges.
- Cove bits: To create concave curves on edges.
- Ogee bits: These are used to produce intricate S-shaped or double curves.
- Chamfer bits: To cut angled edges for beveled looks.
Joinery
Router bits can cut joints that provide structural strength to furniture, cabinetry, and other woodworking projects. Precision is key when making joinery, as strong, well-fitting joints help create a durable construction. Router bits can create a variety of interlocking and strong joints. Common Bit Types:
- Dovetail bits: To create dovetail joints, commonly used in drawer construction and cabinetry.
- Rabbeting bits: To cut a stepped edge (rabbet) along the workpiece for joinery.
- Box joint bits: For producing interlocking box joints.
- Finger joint bits: To make strong finger or comb joints.
Surface Decoration
Surface decoration involves adding decorative details, patterns, or grooves to the flat surfaces of a workpiece. Router bits are perfect for engraving, fluting, or veining, which can enhance the visual appeal of wood projects. Decorative routing is often used in sign-making, furniture design, or artistic woodworking. Common Bit Types:
- V-groove bits: For creating V-shaped grooves, commonly used for engraving letters and designs.
- Core box bits: To cut rounded, concave grooves.
- Fluting bits: For creating decorative fluted grooves along a workpiece.
- Veining bits: For fine, intricate surface engraving.
Flush Trim and Template Routing
Flush trimming and template routing is the process of trimming excess material along the edge of a workpiece so it is perfectly flush with a template or another material. Flush trim bits have bearings that guide the bit along a template or surface, ensuring precise trimming and smooth edges. They are commonly used for veneering, laminates, and pattern routing, where precision in following a template is required. Common Bit Types:
- Flush trim bits: Equipped with a top or bottom-mounted bearing that follows the template while trimming the material, for trimming material flush with the edge of a template.
- Pattern bits: Similar to flush trim bits, used for cutting along a template or pattern, with bearings that guide the bit precisely along the shape.
Router bits enable precision and creativity in woodworking by allowing users to perform various applications. Each application has specialized router bits that help achieve professional-quality results, from decorative edges to strong joints and detailed surface engravings. By selecting the right bit for each task, woodworkers can efficiently accomplish their project goals with both precision and aesthetic appeal.
Selecting a Router Bit for a Specific Wood Type
Selecting the right router bit for a specific type of wood is beneficial for achieving clean cuts, prolonging tool life, and ensuring a smooth finish. The hardness, grain structure, and density of the wood determine which router bit material and shape will perform best. Here’s how to choose router bits based on the type of wood you are working with:
Softwood (Pine, Cedar, Fir)
Softwoods are lightweight, less dense, and easier to cut than hardwoods. However, they are prone to tear-out and splintering, especially when cut across the grain. For softwood, High-Speed Steel (HSS) or carbide-tipped bits are suitable. HSS is affordable and works well with softer woods, while carbide-tipped bits offer longer life and cleaner cuts. Recommended Bit Types:
- Straight bits: Ideal for making clean grooves and dados.
- Roundover bits: For creating smooth, rounded edges that prevent splintering.
- Down-cut spiral bits: Minimize tear-out, especially when cutting across the grain or making plunge cuts.
Application Tips: Use bits with sharp edges to prevent tearing or splintering. Slower feed rates will help maintain a smooth finish, especially on the softer grain of pine and fir.
Hardwood (Oak, Maple, Cherry, Walnut)
Hardwoods are dense, tough, and more challenging to cut. They can cause router bits to dull quickly due to their hardness and grain complexity. Carbide-tipped or solid carbide bits must be used for hardwoods. They retain their sharpness longer and can withstand the rigors of cutting dense, heavy wood. Recommended Bit Types:
- Spiral up-cut bits: Efficient at removing material and producing clean cuts, especially for deep grooves and mortises.
- Dovetail bits: Perfect for creating strong dovetail joints in hardwoods.
- Chamfer bits: Provide clean, beveled edges without burning the wood.
Application Tips: Maintain a consistent feed rate to avoid burning the wood, and use multiple shallow passes rather than a single deep cut.
Plywood and Medium-Density Fiberboard (MDF)
Plywood and MDF are engineered woods that contain layers of wood or compressed fibers bonded with adhesives. These materials are abrasive and tend to wear down router bits quickly. Carbide-tipped or solid carbide bits are recommended for plywood and MDF due to their durability and resistance to wear from the glue and resin used in these materials. Recommended Bit Types:
- Flush trim bits: For trimming plywood or MDF to match templates or other surfaces.
- Down-cut spiral bits: Ensure clean cuts on the top surface, reducing chipping and fraying.
- Compression bits: Excellent for cutting plywood, as they reduce tear-out on both sides of the material by combining up-cut and down-cut flutes.
Application Tip: Use dust extraction when routing MDF to avoid inhaling harmful dust particles, and opt for down-cut or compression bits to prevent edge fraying.
When selecting a router bit for specific wood types, the key factors to consider are wood hardness, grain structure, and the material of the bit. Softwoods benefit from sharp, single-edged bits to avoid tear-out, while hardwoods require durable carbide bits to handle the dense material. Engineered woods like plywood and MDF demand carbide or solid carbide bits due to their abrasive nature. Choosing the right bit ensures clean, efficient cuts and prolongs the life of both your router bit and your project’s finish.
Summarize
Choosing the perfect CNC router bit for woodworking is all about understanding the specific needs of your project and the material you are working with. Always consider the characteristics of the wood, the complexity of the cut, and the durability of the bit to ensure precision and efficiency. By investing in the right router bits, you can enhance both the performance of your CNC machine and the overall finish of your woodworking projects. With the right bit in hand, you’ll be ready to tackle any task, from detailed engraving to robust joinery, achieving professional results every time. Continue reading “CNC Router Bits: Complete Buyer’s Guide” and “What Are The Factors That Affect The Life of CNC Router Bit?” for more information.
If you’re looking for a reliable and high-quality CNC router for your woodworking projects, AccTek CNC is an excellent choice. As a professional CNC router manufacturer based in China, AccTek CNC offers a wide range of machines that are designed to meet the diverse needs of users, from beginners to advanced craftsmen. Our CNC routers are built with precision and durability in mind, making them ideal for working with different types of wood, including softwoods, hardwoods, plywood, and MDF. With AccTek CNC, you can count on professional results, backed by both innovative equipment and comprehensive support.