- 8-12 Min Read
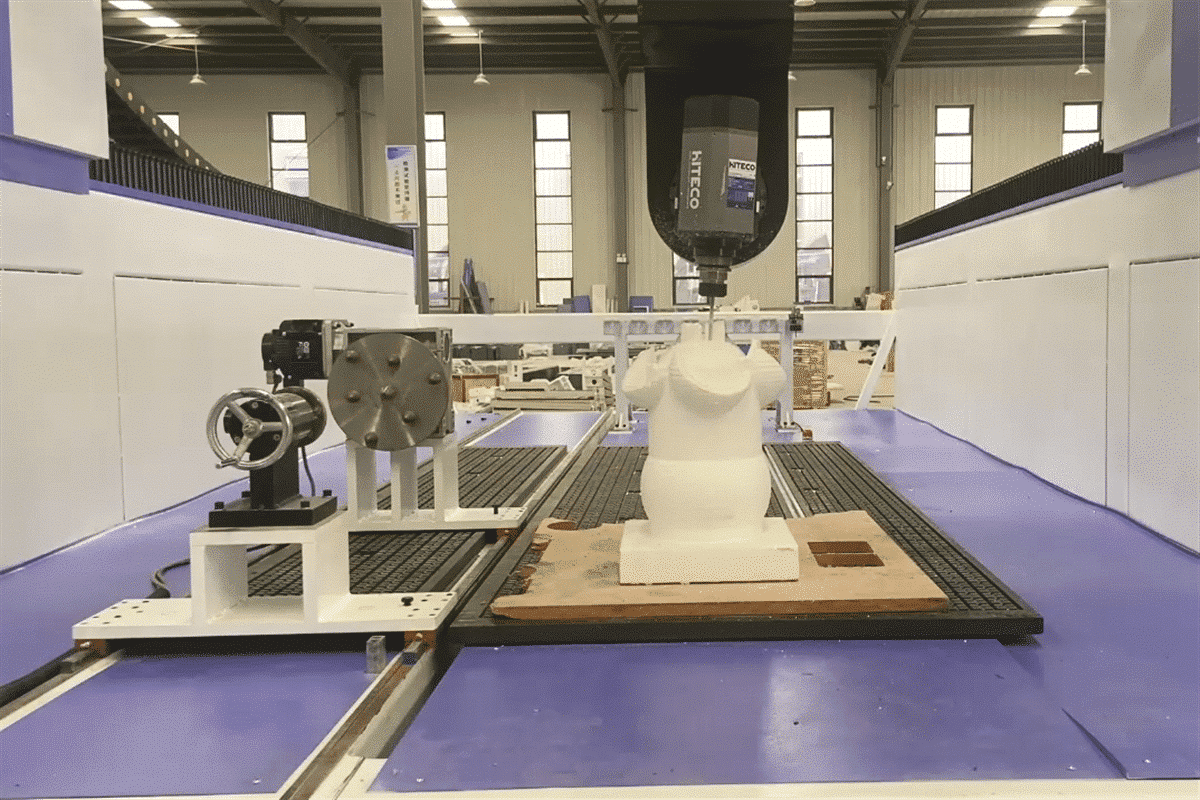
CNC routers are indispensable tools in modern manufacturing, offering precision, versatility, and efficiency in various machining applications. Among the critical parameters that significantly influence machining performance is feed speed—the rate at which the cutting tool moves along the workpiece’s surface. Choosing the optimal feed speed helps achieve the desired results in terms of efficiency, surface finish, and tool longevity. However, choosing the right feed speed involves a nuanced understanding of various factors, including material properties, tool characteristics, surface finish requirements, and machine capabilities. In this comprehensive guide, we’ll delve into the intricacies of feed speed selection for CNC routers, exploring the key factors, methodologies, and best practices to empower machinists to make informed decisions and maximize the potential of their CNC routing operations.
Understanding Feed Speed in CNC Routing
Feed speed in CNC routing is a fundamental parameter that dictates the rate at which the cutting tool moves along the workpiece’s surface during machining. It plays a pivotal role in determining the efficiency, accuracy, and quality of the machining process. Let’s explore feed speed in CNC routing from three key aspects:
What is Feed Speed?
Feed speed, in the context of CNC routing, refers to the velocity at which the cutting tool advances along the workpiece during the machining operation. It represents the linear distance traveled by the cutting tool per unit of time, typically measured in inches per minute (IPM) or millimeters per second (mm/s). Both units provide a quantifiable measure of the feed speed, allowing machinists to precisely control the rate of material removal during CNC routing. Essentially, feed speed determines how quickly material is removed from the workpiece by the cutting tool.
How Feed Speed Affects Processing
The feed speed significantly influences the CNC routing process in several ways. Machinists must carefully adjust feed speeds based on material properties, machining requirements, and tooling considerations to optimize machining performance and achieve desired results.
- Material Removal Rate: Higher feed speeds result in increased material removal rates, leading to faster machining times. Conversely, lower feed speeds reduce material removal rates but may improve surface finish quality by minimizing tool marks and vibrations.
- Surface Finish: Feed speed has a significant impact on determining the surface finish of machined parts. Higher feed speeds may lead to rougher surface finishes due to increased cutting forces and tool wear, while lower feed speeds can produce smoother surfaces with fewer imperfections.
- Tool Life: Feed speed directly impacts tool life and tool wear. Operating at excessively high feed speeds can accelerate tool wear and increase the risk of tool breakage due to higher cutting forces and temperatures. Conversely, using appropriate feed speeds prolongs tool life and reduces the frequency of tool replacement, leading to cost savings and improved efficiency.
Factors affecting feed speed selection
Several factors influence the selection of feed speed in CNC routing, each of which plays a significant role in determining the efficiency, quality, and effectiveness of the machining process. The following are the key factors:
- Material Type and Properties: Different materials have varying hardness, density, thermal conductivity, and other properties that directly impact feed speed selection. For example, softer materials like wood may tolerate higher feed speeds compared to harder materials like metals.
- Tooling and Tool Geometry: The type of cutting tool being used, along with its geometry and specifications, influences feed speed selection. Factors such as tool diameter, number of flutes, cutting-edge geometry, and material composition (e.g., carbide, high-speed steel) affect how the tool interacts with the workpiece and the optimal feed speed required for efficient material removal.
- Surface Finish Requirements: The desired surface finish of the machined part dictates the selection of feed speed.
- Machine Capability and Rigidity: The capabilities of the CNC router itself, including spindle power, acceleration, maximum feed rates, and rigidity, constrain the range of feasible feed speeds.
- Cutting Parameters and Tool Life: Feed speed is closely related to other cutting parameters such as spindle speed, depth of cut, and chip load, which collectively influence tool life and machining efficiency. Machinists must optimize feed speed along with these parameters to maximize tool life while achieving the desired material removal rates and surface finishes.
- Workpiece Geometry and Fixturing: The shape, size, and complexity of the workpiece, as well as the method of fixturing, can affect feed speed selection.
- Operator Experience and Expertise: The experience and expertise of the CNC operator also play a role in feed speed selection.
The correct way to choose feed speed
Choosing the feed speed of CNC routers involves a systematic approach that considers various factors to achieve optimal machining performance. By following these steps and considering the relevant factors, machinists can effectively choose the feed speed of CNC routers to achieve optimal machining performance and produce high-quality parts efficiently. Here is a step-by-step guide on how to choose the feed speed:
- Understand Material Properties: Start by understanding the properties of the material being machined. Consider factors such as hardness, density, thermal conductivity, and machinability. Softer materials generally allow for higher feed speeds, while harder materials may require slower feed rates to maintain machining quality and tool life. Machinists must consider the specific characteristics of the material being machined to determine the appropriate feed speed.
- Review Tooling Specifications: Evaluate the specifications of the cutting tools being used, including their geometry, material composition, and recommended operating parameters. Refer to tool manufacturer guidelines for recommended feed speeds based on tool characteristics and material compatibility.
- Assess Surface Finish Requirements: Determine the desired surface finish of the machined part. Finer surface finishes typically require lower feed speeds to minimize tool marks and achieve smoother surfaces. Machinists must balance the need for surface finish quality with the desired production throughput when selecting feed speeds.
- Consider Machine Capabilities: Take into account the capabilities of the CNC router, including spindle power, acceleration, maximum feed rates, and rigidity. Operate within the machine’s limits to ensure optimal performance and prevent issues such as tool deflection, chatter, or motor overload.
- Calculate Chip Load: Calculate the appropriate chip load based on the selected feed speed, spindle speed, and number of cutting edges on the tool. Chip load refers to the thickness of material removed by each cutting edge during machining and helps ensure efficient material removal and prolonged tool life.
- Perform Test Cuts: Conduct test cuts at various feed speeds to evaluate the results and fine-tune the parameters for the specific machining task. Monitor the surface finish, chip evacuation, tool wear, and overall machining performance to determine the optimal feed speed.
- Consider Workpiece Geometry: Take into account the shape, size, and complexity of the workpiece, as well as the method of fixturing. Adjust feed speed as needed to maintain consistent cutting forces and prevent excessive tool wear or tool breakage, especially for irregular or intricate geometries.
- Factor in Operator Experience: Leverage the experience and expertise of the CNC operator to make informed decisions on feed speed selection. Experienced machinists can rely on their knowledge and intuition to adjust feed speeds based on real-time observations of tool performance, material behavior, and machining conditions.
- Iterate and Optimize: Continuously monitor and adjust feed speeds based on feedback from machining operations. Fine-tune the parameters to optimize material removal rates, surface finish quality, and tool life, ultimately enhancing productivity and profitability in manufacturing operations.
Common challenges and troubleshooting for CNC router feed speeds
When dealing with CNC router feed speeds, several common challenges may arise, requiring troubleshooting to address. Here are some of the typical issues and ways to troubleshoot them:
Chatter or Vibration
- Challenge: The CNC router produces excessive chatter or vibration during cutting, leading to poor surface finish and dimensional accuracy.
- Troubleshooting: Increase the feed speed gradually to find the optimal balance between cutting forces and tool engagement. Ensure that the workpiece is securely clamped and supported to minimize vibration. Consider using vibration-damping tool holders or reducing the spindle speed to minimize chatter.
Inconsistent Material Removal
- Challenge: Material removal rates vary across the workpiece, resulting in dimensional inaccuracies or uneven surfaces.
- Troubleshooting: Check for uneven workpiece fixturing or irregularities in material thickness that may affect cutting consistency. Adjust the feed speed and cutting parameters to maintain uniform chip formation and material removal rates. Ensure that the CNC router’s acceleration and deceleration settings are optimized to minimize variations in cutting forces.
Excessive Heat Generation
- Challenge: Excessive heat buildup occurs during machining, leading to thermal deformation of the workpiece or tool.
- Troubleshooting: Decrease the feed speed to reduce cutting temperatures and frictional heat generation. Use coolant or lubrication to dissipate heat and improve chip evacuation. Consider reducing the depth of the cut or increasing the cutting tool’s radial engagement to distribute heat more evenly across the cutting edge.
Machine Overload or Motor Stalling
- Challenge: The CNC router’s motors experience overload or stall during high-speed cutting operations.
- Troubleshooting: Reduce the feed speed to alleviate the load on the motors and prevent overload conditions. Check for any mechanical issues, such as worn bearings or improperly tensioned belts, that may contribute to motor stalling. Consider upgrading the CNC router’s motor or spindle to handle higher feed rates and cutting forces if necessary.
Advanced technology for feed speed optimization
Advanced technology for feed speed optimization in CNC routers involves the integration of various sensors, algorithms, and software solutions to dynamically adjust feed rates based on real-time feedback and optimization criteria. By leveraging these advanced technologies, CNC routers can achieve higher levels of efficiency, precision, and reliability in machining operations while adapting to a wide range of materials and cutting conditions. Here are some advanced techniques used for feed speed optimization in CNC routers:
- Tool Wear Monitoring: Integrated sensors can monitor tool wear during the machining process. By continuously assessing tool condition, the CNC router can dynamically adjust feed rates to compensate for wear, maintaining consistent cutting performance and extending tool life.
- Force Sensors: Force sensors can be integrated into the machining setup to measure cutting forces experienced during the process. By analyzing these forces in real time, the CNC router can adjust feed rates to optimize cutting efficiency while avoiding excessive tool loads that could lead to tool breakage or poor surface finish.
- Vibration Analysis: Advanced CNC routers may incorporate vibration analysis systems to detect and analyze vibrations during machining. By monitoring vibration patterns, the machine can adjust feed rates to minimize chatter and vibration-induced tool deflection, resulting in improved surface finish and dimensional accuracy.
- Adaptive Control Algorithms: Advanced control algorithms can dynamically adjust feed rates based on various inputs such as cutting conditions, material properties, and tool characteristics. These algorithms may utilize machine learning techniques to continuously optimize feed speeds for specific machining tasks, resulting in improved efficiency and quality over time.
- Real-time Simulation and Optimization: Some CNC routers are equipped with real-time simulation and optimization capabilities. These systems use digital twin technology to simulate machining processes and predict optimal feed rates based on current conditions. By continuously updating the simulation with real-time data, the CNC router can adaptively adjust feed speeds to achieve the best possible outcomes.
- Integration with CAD/CAM Systems: Advanced CNC routers often integrate seamlessly with CAD/CAM software solutions. This integration allows for direct translation of design specifications into optimized toolpaths, including feed speed adjustments based on material properties, tooling, and machining constraints.
- Energy Efficiency Optimization: In addition to optimizing cutting performance, advanced CNC routers may also focus on energy efficiency. By dynamically adjusting feed rates based on power consumption and machine load, these systems can minimize energy usage while maintaining productivity.
Safety precautions and best practices
Safety precautions and best practices that focus on CNC router feed speeds can help ensure operator health, prevent accidents, and optimize machining performance. Here are some key considerations. By following these safety precautions and best practices, operators can effectively manage feed speeds on CNC routers to achieve optimal machining results while prioritizing safety and minimizing risks.
- Operator Training: Before operating a CNC router, operators should receive thorough training on machine operation, including understanding feed speed settings and safety protocols. Training should cover topics such as proper programming, tool selection, and emergency procedures.
- Manufacturer Guidelines: Follow manufacturer recommendations and specifications regarding feed speeds for specific materials, tooling, and machining processes. These guidelines are based on extensive testing and assure safe and efficient operation.
- Start with Conservative Settings: When starting a new machining operation or working with unfamiliar materials, begin with conservative feed speed settings. Gradually increase feed rates while monitoring performance and quality to find the optimal balance between productivity and safety.
- Tooling Condition: Ensure that cutting tools are in good condition before starting a machining operation. Dull or damaged tools can lead to increased cutting forces, poor surface finish, and potential safety hazards. Regularly inspect and replace worn-out tools as needed.
- Workpiece Fixturing: Securely fixturing the workpiece can effectively prevent movement or vibration during machining, especially at high feed rates. Use clamps, vises, or other appropriate methods to securely hold the workpiece in place and minimize the risk of accidents.
- Chip and Dust Management: Proper chip and dust management helps maintain a safe and clean work environment. Use chip guards, dust extraction systems, and other safety measures to control debris generated during machining operations.
- Monitoring and Supervision: Operators should continuously monitor machining operations, especially when using high feed speeds or working with challenging materials. Be alert for any signs of tool wear, excessive vibration, or other abnormalities that may indicate a safety issue.
- Emergency Stop Procedures: Ensure that all operators are familiar with emergency stop procedures and know how to quickly halt machine operations in case of an emergency or unexpected event.
- Personal Protective Equipment (PPE): Operators should wear appropriate PPE, including safety glasses, hearing protection, and, if necessary, gloves and protective clothing, to minimize the risk of injury from flying debris or other hazards.
- Regular Maintenance: Perform regular maintenance on the CNC router, including lubrication, calibration, and inspection of critical components. A well-maintained machine is safer and more reliable, reducing the likelihood of accidents related to feed speed issues or other mechanical failures.
Summarize
Choosing the right feed speed for your CNC router is a key aspect of achieving optimal machining results. It requires careful consideration of various factors such as material type, tooling, machine capabilities, and desired results. By understanding the factors that affect feed rates, utilizing selection methods, and implementing best practices, machinists can increase efficiency, improve surface finish quality, and extend tool life in CNC routing operations. By continuously learning, experimenting, and adapting, machinists can realize CNC routers’ full potential and meet modern manufacturing demands with precision and excellence.
AccTek CNC prioritizes the user’s operating experience with CNC routers to ensure customer satisfaction from purchase to operation. In addition to providing a comprehensive machine instruction manual, AccTek CNC provides customers with additional support and resources. Whether fine-tuning cutting parameters or resolving technical issues, customers can rely on AccTek CNC for prompt and effective solutions. A dedicated support team is always available to resolve issues and provide expert guidance, ensuring customers can maximize their CNC router’s performance and efficiency. Contact us for more information about CNC routers.