- 6-9 Min Read
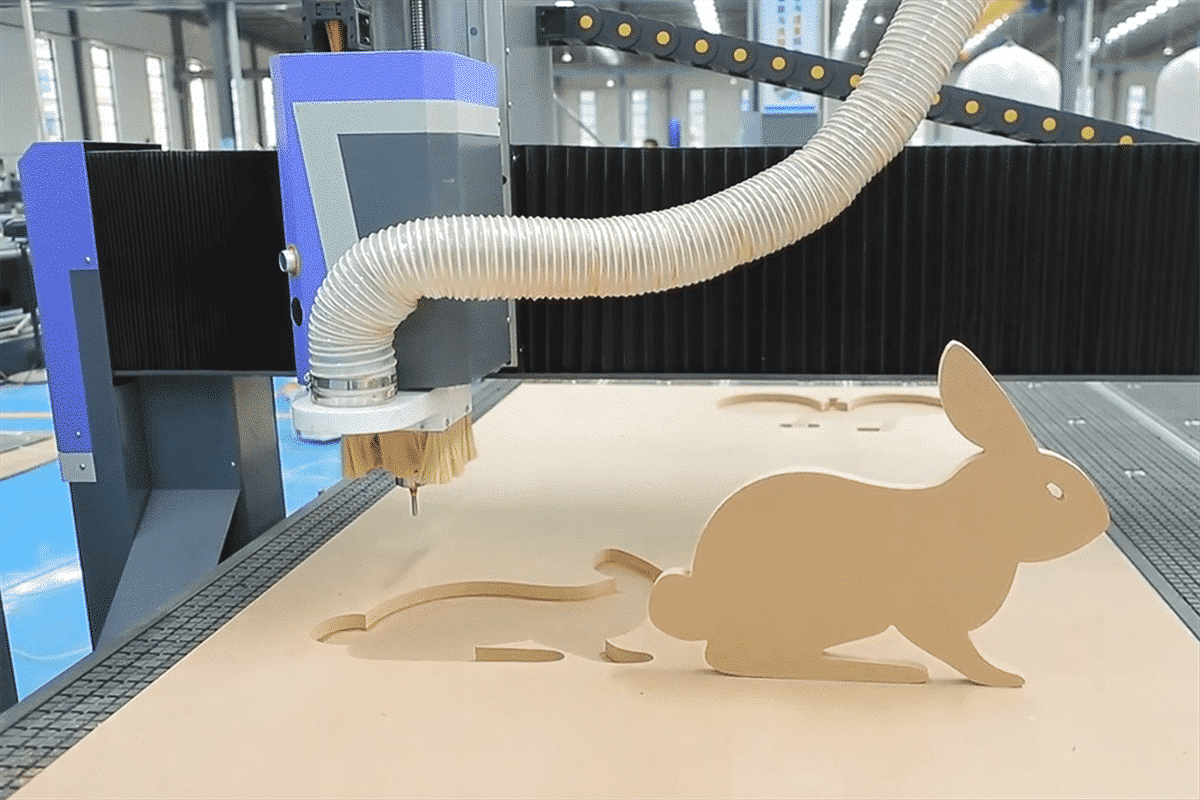
In the realm of modern manufacturing and woodworking, precision has always been a focus. Enter the CNC router, a versatile and indispensable tool that has revolutionized the way we create intricate designs and fabricate complex components. From crafting fine furniture to machining unique crafts, CNC routers offer unparalleled accuracy and efficiency, driving innovation across industries. However, behind the seamless cuts and immaculate finishes lie a myriad of factors influencing the accuracy of these machines. Understanding the nuances of CNC router accuracy is not merely a matter of achieving dimensional perfection but also ensuring optimal performance and reliability.
In this comprehensive exploration, we delve into the multifaceted realm of factors affecting the accuracy of CNC routers and the methods employed to enhance their precision. From mechanical considerations to software intricacies, we dissect the critical components that shape the fidelity of CNC machining processes. Whether you’re a seasoned machinist striving for perfection or a novice enthusiast venturing into the world of CNC machining, this exploration serves as a comprehensive guide to navigating the realm of accuracy in CNC routing.
Understand the accuracy of CNC router
At its core, accuracy in CNC routers refers to the machine’s ability to faithfully translate digital designs into physical objects with minimal deviation from the intended dimensions. The accuracy of a CNC router can vary widely depending on several factors including the quality of the machine, its components, calibration, and operating conditions. Generally, modern CNC routers can achieve high levels of accuracy and repeatability.
Accuracy in CNC routing is typically measured in terms of tolerance, which denotes the allowable margin of error between the programmed dimensions and the actual output. For example, a CNC router with a tolerance of ±0.005 inches means that the actual dimensions of the cut or carved object may deviate by up to 0.005 inches from the programmed dimensions.
High-quality CNC routers can often achieve tolerances well below ±0.005 inches, sometimes reaching tolerances of ±0.001 inches or even better, especially for industrial-grade machines. However, achieving such high levels of accuracy may require careful calibration, maintenance, and appropriate cutting parameters.
Understand the repeatability accuracy of CNC router
Repetition accuracy, also known as repeatability or positional accuracy, refers to the ability of a CNC router to consistently return to a specific position after multiple movements. In essence, it measures the machine’s ability to reproduce the same positional coordinates with minimal deviation over successive cycles of operation.
Generally, CNC routers are capable of achieving repetition accuracies within a range of a few thousandths of an inch (e.g., ±0.002 inches) to even tighter tolerances, depending on the specific machine and its configuration. For example, a CNC router with a repetition accuracy of ±0.002 inches means that it can consistently return to a given position within a tolerance of 0.002 inches after each movement. Higher-end industrial-grade CNC routers may offer even tighter repetition accuracies, often achieving tolerances in the range of a few tenths or hundredths of a thousandth of an inch.
The importance of precision and repeatability precision
Precision and repeatability are two fundamental pillars upon which the functionality and effectiveness of CNC routers rest. it is the inherent precision and repeatability of CNC routers that elevate them from mere machines to indispensable assets in diverse industries. Let’s explore the profound importance of these characteristics in the realm of CNC routers.
- Quality Assurance: Precision and repeatability ensure that machined parts meet strict dimensional requirements consistently. Maintaining precise dimensions through accurate CNC machining helps guarantee the quality and reliability of end products.
- Cost Efficiency: Achieving precise and repeatable results minimizes material waste, rework, and scrap. CNC routers capable of consistently reproducing identical parts without variation contribute to cost savings by optimizing material usage and reducing production downtime.
- Design Flexibility: Precision in CNC routing enables the realization of intricate and complex designs with fine details and tight tolerances. Whether producing custom furniture or intricate molds, CNC routers provide designers with the flexibility to bring their creative visions to life without compromising accuracy.
- Time Savings: Reliable repetition accuracy reduces the need for manual intervention and fine-tuning between machining cycles. Once a program is set up and validated, the machine can reliably reproduce the same results repeatedly, reducing setup times and minimizing operator intervention. This streamlined workflow not only accelerates production but also improves overall efficiency, allowing manufacturers to meet tight deadlines and respond quickly to changing demands.
- Consistency and Reliability: Customers and end-users expect consistency and uniformity in the products they receive. CNC routers with high precision and repeatability ensure that every part produced adheres to the same standards of quality and accuracy, minimizing variations and defects. Consistent results build trust and confidence in the manufacturer’s brand, enhancing customer satisfaction and loyalty over time.
Precision and repeatability are not mere attributes but essential characteristics that define the capabilities and reliability of CNC routers. As industries continue to demand higher levels of accuracy, efficiency, and quality, the importance of these traits will only grow more pronounced. By leveraging the precision and repeatability inherent in CNC routers, manufacturers can unlock new possibilities, drive innovation, and maintain a competitive edge in today’s dynamic marketplace.
Factors affecting accuracy and ways to improve it
The accuracy of a CNC router, like any machining process, is influenced by several factors. To optimize CNC router operations and improve output quality, machine operators must understand these factors and find solutions. In this section, we not only clarify the factors that affect the accuracy of CNC routers but also bring practical methods to improve accuracy. Read on for actionable advice on pursuing precision craftsmanship.
- Environmental Factors: Environmental conditions such as temperature, humidity, and dust can affect the performance of the CNC router and lead to dimensional variations. It’s important to maintain a stable environment within the machining area. It’s essential to maintain a stable environment within the machining area to minimize these effects.
- Material Properties: Different materials have different properties that can affect machining accuracy. Variations in material thickness can result in uneven cuts and dimensional inaccuracies. Proper fixturing or material leveling techniques may be necessary to address this issue. Additionally, the warping of the material being machined can result in dimensional inaccuracies. Understanding the properties of the material and implementing appropriate fixturing or support strategies can help mitigate this issue.
- Machine Rigidity: The rigidity of the machine affects its ability to maintain precise positioning and prevent vibrations during cutting. Insufficient rigidity can lead to vibrations and poor surface finish, affecting accuracy. A CNC router must possess a sturdy frame and high-quality components to minimize vibrations and deflections during cutting operations, resulting in more precise cuts. Rigidity ensures that the machine maintains its intended position and orientation throughout the machining process, resulting in more precise cuts and consistent dimensional accuracy.
- Machine Calibration: Ensuring that the machine is properly calibrated and that all components are in optimal condition is key to consistent performance. This includes ensuring that the axes are perpendicular and parallel to each other, alignment of auto tool changers, as well as verifying the accuracy of the spindle and tooling.
- Feed Rates and Speeds: Optimizing the feed rates and spindle speeds according to the material being machined is important for achieving accurate results. Incorrect settings can lead to tool deflection, poor surface finish, and dimensional inaccuracies.
- Tool Runout: Tool runout, or the deviation from true rotation, can lead to inaccuracies in the machined part. Proper tool inspection and maintenance are necessary to minimize runout.
- Tool Deflection: Tool deflection occurs when cutting forces cause the tool to bend, resulting in dimensional inaccuracies. Using proper tooling and cutting techniques can help minimize deflection.
- Tool Length Changes: Changes in tool length during machining can affect tool positioning and lead to inaccuracies. Implementing tool-length probing or compensation techniques can help mitigate this issue.
- Gantry Verticality: Misalignment of the gantry can lead to skewed cuts and dimensional inaccuracies. Regular alignment checks and adjustments are necessary to ensure gantry verticality.
- Drive system: CNC routers may use various drive systems such as lead screws, ball screws, or rack and pinion systems, each affecting accuracy differently. Systems with low backlash and minimal friction contribute to higher precision by minimizing errors introduced during motion. Additionally, wear and clearance in lead screws can introduce backlash and positional errors. Regular maintenance and inspection of lead screw assemblies are necessary to maintain accuracy.
- Control Systems: The precision of the CNC controller and the interpolation algorithms it uses can impact accuracy. Sophisticated control algorithms, coupled with feedback mechanisms such as encoders, enable precise positioning and motion control, even in dynamic machining environments.
- Programming and Toolpath Optimization: The CNC program and toolpaths generated by CAM software should be optimized for accuracy. This includes minimizing sharp direction changes, optimizing tool entry and exit points, and selecting appropriate cutting strategies.
- Accumulation of Dust or Residue: Dust and residue buildup on machine components can affect movement and accuracy. Regular cleaning and maintenance are necessary to prevent this issue.
- Multi-axis Synchronization Issues: Inaccuracies in multi-axis synchronization can result in misaligned cuts and dimensional errors. Properly calibrating and adjusting multi-axis systems helps maintain accuracy.
- Machine Warm-up Time: Allowing sufficient warm-up time for the machine components to reach stable operating temperatures can help ensure consistent accuracy during machining operations.
- Operator Skill and Experience: The skill and experience of the operator also play a significant role in achieving accuracy. Operators should be trained in machine operation, tooling selection, and troubleshooting to minimize errors and optimize performance.
Regular maintenance, calibration, and process optimization are key to maintaining consistent accuracy over time. By acknowledging and addressing the diverse array of factors influencing CNC router accuracy, manufacturers can consistently produce accurate, high-quality parts and products. Through a commitment to excellence and continuous improvement, CNC routers can fulfill their potential as indispensable tools in the realm of modern manufacturing.
Summarize
Precision and repeatability precision are indispensable attributes that define the performance and reliability of CNC routers. From ensuring quality assurance and cost efficiency to enabling design flexibility and accelerating production, these qualities underpin the success of modern manufacturing operations. As industries continue to evolve and demand ever-higher standards of performance, the importance of precision and repeatability precision in CNC routers remains steadfast, driving innovation and excellence in machining processes. By understanding the factors that affect the accuracy of CNC routers and optimizing them, manufacturers can achieve high levels of precision and consistency in their machining operations.
At AccTek CNC, we understand the pivotal role that precision plays in the world of machining. Our commitment to excellence drives us to provide users with high-precision machines equipped with accessories sourced from world-renowned brands. We not only provide products, but comprehensive solutions tailored to meet the diverse needs of our customers. Beyond the initial purchase, we always provide technical support to our customers. Should you encounter technical challenges, our team of experienced engineers stands ready to provide timely assistance, ensuring minimal downtime and optimal performance of your CNC router. Contact us to get more information about CNC routers.