Rotary Axis CNC Router
Rotary axis CNC routers are cutting-edge machines designed to bring versatility and precision to your woodworking, metalworking, and engraving projects. Unlike traditional CNC routers, these machines are equipped with a rotary axis, enabling them to carve and engrave intricate details on cylindrical, round, or irregularly shaped objects with unmatched accuracy. Whether you’re crafting custom furniture, designing artistic sculptures, or creating industrial prototypes, rotary-axis CNC routers make complex 3D projects achievable and efficient.
Engineered for precision and ease of use, these CNC routers cater to a wide range of materials, including wood, acrylic, metal, and stone, making them ideal for industries such as manufacturing, design, and artisan craftsmanship. The rotary axis functionality allows for seamless 360-degree rotation, giving users the flexibility to execute detailed designs on objects like columns, balusters, and even curved surfaces.
Rotary axis CNC routers are equipped with user-friendly interfaces and powerful software, enabling professionals and hobbyists alike to create intricate designs with ease. Their robust construction and high-performance components ensure durability, reliability, and long-term value for businesses and creators seeking to elevate their production capabilities. Explore our selection of rotary-axis CNC routers and discover how these versatile machines can transform your creative possibilities.
-
AKM1325-R CNC Router
Rated 5.00 out of 5$5,500.00 Add to cart -
AKM1530-R CNC Router
Rated 5.00 out of 5$6,100.00 Add to cart -
AKM2030-R CNC Router
Rated 5.00 out of 5$6,700.00 Add to cart -
AKM2040-R CNC Router
Rated 5.00 out of 5$7,200.00 Add to cart -
AKM1325-4R CNC Router
Rated 5.00 out of 5$8,500.00 Add to cart -
AKM1530-4R CNC Router
Rated 5.00 out of 5$9,600.00 Add to cart -
AKM2030-4R CNC Router
Rated 5.00 out of 5$10,200.00 Add to cart -
AKM2040-4R CNC Router
Rated 5.00 out of 5$10,600.00 Add to cart
Tips for Choosing the Right Rotary Axis CNC Router
Choosing the perfect rotary axis CNC router is essential to achieving outstanding results in your projects. These machines are investments that need to align with your production needs, material compatibility, and long-term goals. Whether you’re a professional craftsman, a manufacturer, or a hobbyist, evaluating the right features and specifications ensures precision, efficiency, and durability.
Identify Your Application Needs
Before choosing CNC routers, outline your primary applications, whether it’s engraving cylindrical objects, crafting intricate sculptures, or producing industrial components. Your project’s scope and complexity will help you determine the machine’s essential features.
Check Material Compatibility
Ensure the CNC router supports the materials you plan to work with, such as wood, metal, acrylic, or stone. Versatile machines capable of handling multiple materials expand your creative and functional possibilities.
Evaluate Rotary Axis Features
A robust rotary axis system should provide smooth, precise 360-degree rotation. This feature is crucial for engraving detailed designs on cylindrical or irregularly shaped objects, ensuring consistent quality.
Assess Work Area Dimensions
Choose CNC routers with a work area that accommodates your largest projects. A larger bed size increases versatility, allowing you to tackle both small-scale tasks and large-scale designs seamlessly.
Focus on Spindle Power and Speed
Look for CNC routers with high spindle power and adjustable speed settings. These features enable you to handle a variety of materials, from softwood to harder metals, while maintaining precision and efficiency.
Examine Software Usability
User-friendly and versatile software is a must. Ensure the CNC router’s software integrates well with popular design programs and simplifies the transition from design to execution, saving time and reducing errors.
Review Build Quality and Construction
Sturdy construction with high-quality materials like cast iron or steel reduces vibrations and enhances precision. Durable machines also offer better longevity, making them a worthwhile investment for long-term use.
Prioritize Precision Components
High-resolution stepper motors, ball screws, and linear guides are essential for maintaining accuracy in detailed projects. These precision components ensure consistent results, especially in intricate or repetitive tasks.
Consider User-Friendliness
Ease of use is critical, especially for beginners. Machines with intuitive controls, clear documentation, and accessible interfaces allow for smoother operation and reduce the learning curve.
Evaluate Maintenance Requirements
Low-maintenance machines save time and reduce operating costs. Look for models with easy-to-replace parts and clear maintenance guidelines to ensure long-term performance and reliability.
Set a Realistic Budget
Establish a budget that balances your needs with cost considerations. Focus on quality and essential features rather than opting for the cheapest option, as this ensures better value over time.
Research Brands and Support
Choose CNC routers from a reputable brand with excellent reviews and strong technical support. Reliable customer service and warranties are invaluable in troubleshooting issues and maintaining long-term satisfaction.
What Materials Can the Rotary Axis CNC Router Cut
Rotary axis CNC routers are incredibly versatile, capable of cutting, carving, and engraving a wide range of materials with precision. These machines are ideal for both soft and hard materials, making them suitable for industries like woodworking, metalworking, and crafting. They handle wood, plastics, metals, foam, and even stone with ease, offering flexibility for various projects.
Whether you’re creating intricate designs on wood, engraving cylindrical metal objects, or carving detailed patterns into acrylic or stone, the rotary axis enables seamless 360-degree operation for complex shapes and surfaces. Its ability to adapt to different material densities ensures consistent quality and accuracy, regardless of the medium. This versatility makes the Rotary axis CNC router a valuable tool for professionals and hobbyists seeking to expand their creative possibilities and production capabilities.
Application Industry
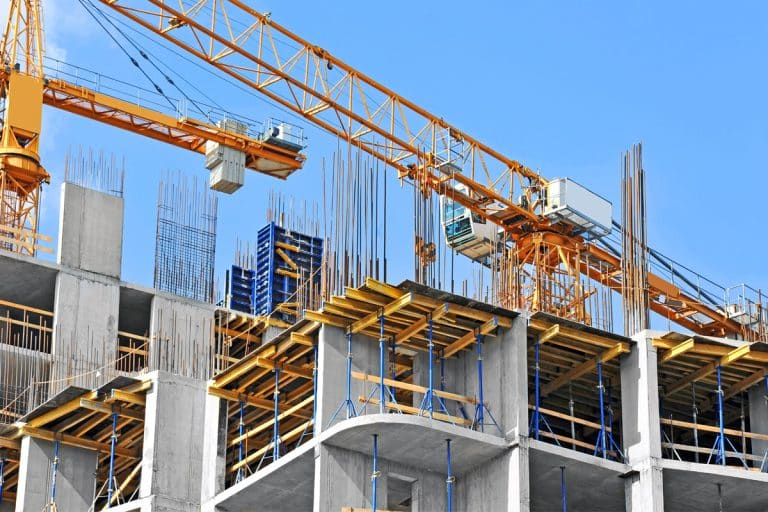
Construction Industry
The integration of CNC routers into construction workflows has ushered in a new era characterized by meticulous detailing, rapid prototyping, and improved material utilization.
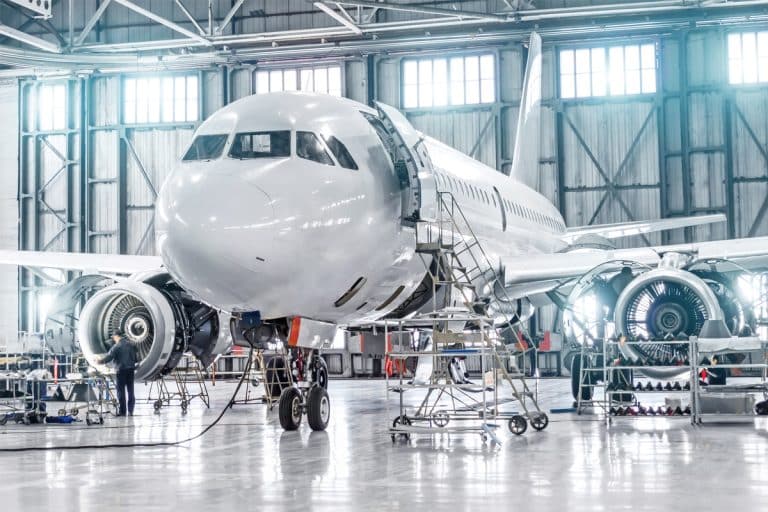
Aerospace Industry
The CNC router is widely used in aerospace engineering due to its unparalleled ability to carve complex designs, manufacture complex parts, and ensure tight tolerances.
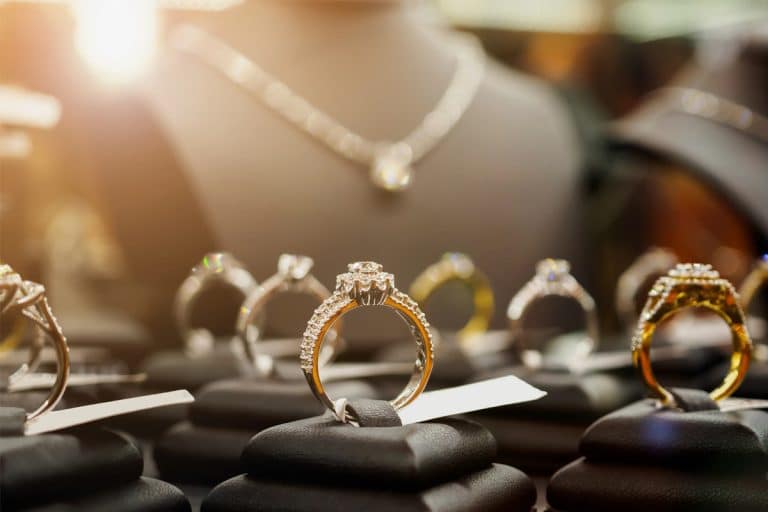
Jewelry Industry
The CNC router revolutionize the way fine jewelry is designed and made by delivering unparalleled precision and efficiency and producing intricate designs with meticulous attention to detail.
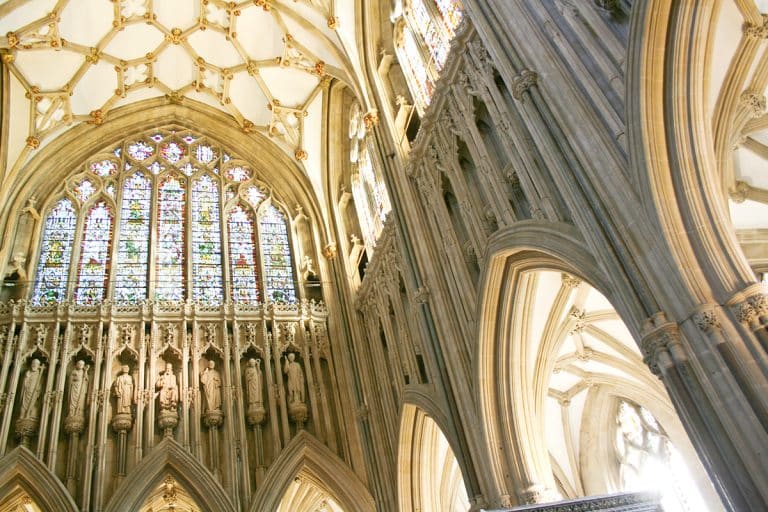
Stone Carving Industry
The integration of CNC routers into the stone carving industry is not only revolutionizing the way craftsmen carve, it is also redefining the boundaries of artistic possibilities in this ancient practice.
Blog
How to Choose the Right Stone CNC Router for Your Workshop?
This guide will walk you through the key factors to consider when choosing a stone CNC router, designed to help you invest wisely in a machine that delivers reliable performance ...
Read More
Best Budget CNC Router for Making Outdoor Signs?
In this guide, we'll break down the key features to look for, explore different models under a variety of price points, and help you choose the best budget CNC router ...
Read More
How to Maintain and Troubleshoot the ATC CNC Router?
This article will walk you through a practical maintenance procedure for your ATC CNC router and instruct you on how to diagnose and repair common problems that may arise.
Read More
What Warranties Are Typically Offered on CNC Routers?
In this article, we'll break down the different types of warranties typically offered on CNC routers, what's included, and how to make sure you're getting the support you need long ...
Read More
Frequently Asked Questions
What is the rotary axis on CNC routers?
The rotary axis on CNC routers, often referred to as the “A-axis,” is an additional axis that enables the rotation of the workpiece, enhancing the router’s capabilities. While traditional 3-axis CNC routers operate on X, Y, and Z axes to move in linear directions, the rotary axis adds a fourth rotational dimension, allowing the machine to work on cylindrical, curved, or irregular surfaces.
This functionality is particularly valuable for projects that involve round or cylindrical objects. Instead of moving the cutting tool in a straight line, the A-axis rotates the workpiece, enabling precise engraving, carving, or machining around its circumference. Common applications include crafting table legs, creating intricate designs on sculptures, or producing rotating components for machinery.
By integrating a rotary axis, CNC routers become more versatile, handling a broader range of materials and project types. This is especially beneficial in industries like woodworking, manufacturing, and prototyping, where working on curved or cylindrical surfaces is essential for creative and functional designs.
How to Choose the Installation Position of the CNC Rotary Axis?
Selecting the appropriate installation position for the CNC rotary axis—either on the side of the machine or directly on the work table—requires a thoughtful evaluation of your workshop’s needs, workpiece requirements, and workflow efficiencies. Below is an overview of the pros and cons of each option, along with key considerations to help you make the best decision.
- Rotary Axis on the Side of the Machine
- Advantages: Frees up the workbench for larger workpieces or simultaneous setups. Facilitates easier loading and unloading of materials, improving operator efficiency. Keeps the workbench unobstructed for traditional 3-axis machining tasks.
- Shortcomings: Requires additional floor space on the machine’s side. The fixed position can limit the length of the workpiece that can be accommodated.
- Rotary Axis on the Work Table
- Advantages: Maximizes the use of existing floor space. Allows flexible positioning along the table, accommodating workpieces of varying lengths. Enables machining of longer workpieces by repositioning the rotary axis.
- Shortcomings: Material handling can be more complex, particularly with heavy or bulky items. Careful planning is necessary to prevent interference with linear axes or tools.
- Key Factors to Consider
- Workpiece Length: For long or varied-length workpieces, installing the rotary axis on the workbench offers greater flexibility.
- Space Constraints: If workshop floor space is limited, mounting the rotary axis on the workbench optimizes the available area.
- Workflow Efficiency: Consider how each position impacts material handling, setup times, tool changes, and machining flow.
- Operator Accessibility: Ensure that the selected position allows convenient operator access for programming, setup, and maintenance.
- Interference and Collisions: Verify that the installation location avoids interference with the machine’s other components, linear axes, and tools during operation.
- Material Handling: Evaluate the ease of loading and unloading workpieces based on the rotary axis placement.
- Future Upgrades: Plan for future processing needs or equipment upgrades, choosing a position that remains adaptable to changing requirements.
How Do Rotary Axis CNC Routers Work?
The rotary axis CNC router operates by adding a fourth rotational axis (A-axis) to the traditional three linear axes (X, Y, and Z), enabling precise machining of cylindrical, curved, or irregular workpieces. The integration of rotational motion expands the CNC router’s capabilities, allowing for complex 3D machining. Here’s a step-by-step explanation of how it works:
- Design and Programming: The process begins with creating a 3D design using CAD (Computer-Aided Design) software. This design incorporates the rotational capabilities of the A-axis, ensuring an accurate representation of the desired object.
- CAM Programming: The CAD design is converted into machine-readable code using CAM (Computer-Aided Manufacturing) software. The CAM program calculates the tool path and rotational motion, ensuring synchronization between the linear and rotational axes.
- Material Setup: The workpiece, typically cylindrical or curved, is securely fixed in the machine’s rotary axis. Proper alignment and tight fixation are essential to ensure machining precision.
- Origin Positioning: The cutting tool (spindle) is positioned at the origin point, aligning with the programmed coordinates for both the linear and rotational axes.
- Tool Changes (If Necessary): If the design requires multiple tools, the CNC router can perform automatic tool changes to adapt to different machining stages, such as cutting, engraving, or shaping.
- Machining Process: The CNC router executes the programmed tool path, combining movements along the X, Y, and Z axes with the A-axis rotation. This coordination allows the cutting tool to machine different angles, sides, or contours of the workpiece.
- Rotary Motion: The A-axis rotates the workpiece, enabling the CNC router to process intricate designs on the circumference or other curved surfaces. The rotational and linear movements work in harmony to achieve detailed 3D results.
- Finishing and Completion: As the CNC router completes the programmed tool path, it carves, engraves, or shapes the workpiece into the desired form with high precision and detail.
- Tool Retraction and Workpiece Removal: Once the machining process is complete, the tool retracts, and the finished workpiece is carefully removed from the rotary axis.
- Cleaning and Maintenance: Finally, the machine is cleaned and inspected for wear. Routine maintenance ensures ongoing accuracy and reliability.
What Can a Rotary-Axis CNC Router Machine Do?
The rotary-axis CNC routers significantly enhance the capabilities of traditional CNC routers, enabling precise machining on cylindrical or curved workpieces. Here’s an overview of the key applications and tasks it can perform:
- 3D Carving and Engraving: Create intricate 3D carvings and engravings on cylindrical objects like decorative columns, table legs, and sculptures. The rotary motion allows for seamless design continuity around curved surfaces.
- Rotary Sign Making: Craft cylindrical or curved signs with detailed lettering and graphics, perfect for unique branding, outdoor signage, and display applications.
- Woodturning and Lathe Work: Simulate traditional lathe work to carve patterns, grooves, and intricate details on turned wood pieces such as chair legs, balusters, and spindles.
- Cylindrical Parts Production: Machine cylindrical parts with exceptional precision, catering to industries like aerospace, automotive, and manufacturing that require components with curved or rounded features.
- Rotary Indexing: Perform indexing operations to machine multiple sides of a cylindrical workpiece without manual repositioning, improving efficiency and accuracy.
- Rotary Fluting and Twisting: Produce fluted or twisted patterns on cylindrical surfaces, adding decorative features to furniture components, architectural details, or artistic designs.
- Rotary Nesting: Optimize material usage by nesting and cutting multiple parts from cylindrical stock, reducing waste and maximizing productivity.
- Custom Woodworking: Create unique and custom woodworking projects involving curved or cylindrical elements, enabling artisans to produce bespoke designs with precision.
- Artistic and Decorative Items: Fabricate artistic and decorative items featuring intricate patterns, textures, or reliefs on curved surfaces, expanding possibilities for creative projects.
- CNC Lathe Operations: Simulate lathe operations for producing turned components on a CNC router, eliminating the need for a dedicated lathe machine.
- Multi-Axis Machining: Combine the rotary axis with linear axes for complex multi-axis machining, allowing for highly detailed geometries and advanced component designs.
- Specialized Industrial Applications: Handle specialized tasks such as machining cylindrical molds, rollers, or other industry-specific parts with precise rotational control.
How Much Do Rotary-Axis CNC Routers Cost?
The cost of rotary-axis CNC routers varies widely, ranging from $3,500 to $25,000, depending on machine specifications, features, and configurations. To provide an accurate quote, it’s essential to assess your specific processing needs, as factors like workpiece size, material type, and accuracy requirements significantly influence the machine choice and cost.
- Factors Affecting Cost
- Worktable Size and Spindle Power: Larger worktables and high-power spindles cost more, as they offer greater versatility for machining larger or harder materials.
- Advanced Configurations: Features like an ATC (Automatic Tool Changer) spindle, vacuum table, and automatic lubrication systems can increase the price but enhance efficiency and ease of use.
- Software and Tools: Software for design and CAM programming, along with cutting tools, are additional costs to consider.
- Accessories and Upgrades: Accessories like dust collection systems, rotary fixtures, or specialized cutting tools add to the total investment.
- Training and Support: Training for machine operation and maintenance may involve additional fees, though it ensures optimal use and efficiency.
- Considerations Before Purchase
- Processing Needs: Match the machine’s specifications to your workpiece size, material type, and accuracy requirements.
- Future Scalability: Choose features that accommodate potential future projects or production needs.
- Budgeting: Account for supplementary costs, such as software, training, and maintenance.
How to Lubricate Rotary Axis CNC Routers?
Proper lubrication is essential for maintaining the performance and extending the service life of your rotary-axis CNC router. Follow these general guidelines to ensure optimal care and operation:
- Refer to the Manufacturer’s Guide: Consult the machine’s manual for specific lubrication instructions. Different CNC routers may have unique requirements based on their design and components.
- Identify Lubrication Points: Locate designated lubrication points on the rotary axis, including Bearings, Sliders, Gears, and Other moving parts. These points are typically marked or described in the manual.
- Use the Correct Lubricant: Choose the lubricant recommended by the manufacturer, often a lightweight oil or grease suitable for machine components. Avoid using products that may attract dirt or debris, which can reduce efficiency.
- Clean Components Before Lubricating: Ensure that all parts are clean and free of dirt, debris, or old lubricant. Use a clean cloth or an appropriate cleaning solution to prepare the surfaces.
- Apply Lubricant Sparingly: Use a grease gun or applicator to apply the lubricant to the designated points. Avoid over-lubrication, as excess lubricant can attract dirt and cause potential issues.
- Rotate the Axis Manually: After applying the lubricant, manually rotate the rotary axis to distribute the lubricant evenly across the moving parts. This ensures smooth operation and proper coverage.
- Schedule Periodic Inspections: Set up a routine maintenance schedule to inspect and lubricate the rotary axis. The frequency depends on machine usage, operating conditions, and the type of lubricant used.
- Remove Excess Lubricant: Wipe off any excess lubricant from the surface after operation to prevent dirt and debris from sticking to the components.
- Monitor and Reapply as Needed: Regularly monitor the condition of lubricated parts. Reapply lubricant if you notice signs of dryness, increased friction, or wear.
- Utilize Automatic Lubrication Systems: If your machine is equipped with an automatic lubrication system, ensure it is functioning properly and the lubricant reservoir is filled as needed.
- Maintain Records: Keep detailed records of lubrication schedules and maintenance activities. This helps track maintenance history and ensures timely inspections and repairs.
- Consult the Manufacturer: If you encounter issues or have specific questions, consult the manufacturer or dealer for tailored advice based on your CNC router model.
What Customer Support Do Rotary Axis CNC Routers Provide?
Rotary Axis CNC routers come with reliable customer support options to ensure smooth operation and user satisfaction:
- Free Online Technical Support: Customers can access complimentary technical assistance through online platforms, including email, chat, or video support. This service is ideal for troubleshooting, software setup, or resolving operational issues remotely.
- Paid On-Site Training: For users requiring hands-on guidance, on-site training sessions are available at an additional cost. These sessions cover installation, operation, and maintenance to ensure optimal use of the machine.
What Is The Warranty Period of Rotary Axis CNC Routers?
Our CNC router is backed by a comprehensive warranty designed to give you peace of mind and protect your investment:
- 3-Year Warranty for the Entire Machine: This full warranty covers any defects or malfunctions in the machine as a whole, ensuring reliable performance and longevity over time.
- 5-Year Warranty for Core Components: Key components essential for optimal machine operation are covered for 1.5 years. This includes parts that may experience wear and tear with regular use, ensuring you have support for the most vital parts of the machine.