Multi-Head CNC Router
Our multi-head CNC routers are engineered for precision, versatility, and high productivity. These advanced machines combine multiple cutting heads, allowing you to tackle multiple tasks simultaneously, reducing production time and boosting efficiency. Perfect for a wide range of industries, including woodworking, plastics, and composites, these CNC routers deliver exceptional results with minimal downtime.
Each multi-head CNC router is designed to maximize throughput while maintaining high-quality output. Whether you’re working with intricate designs or large-scale projects, the versatility of having multiple heads ensures that complex operations like drilling, milling, and engraving can be completed in a fraction of the time compared to single-head models. The user-friendly interface and robust construction ensure reliability, even in the most demanding production environments.
With customizable configurations, our multi-head CNC routers are tailored to meet the specific needs of your operation, enhancing flexibility and precision. From small businesses to large enterprises, these CNC routers are ideal for companies looking to streamline production, reduce labor costs, and increase overall output.
Tips for Choosing the Right Multi-Head CNC Router
Choosing the right multi-head CNC router is crucial for maximizing your production efficiency, precision, and overall workflow. With various models offering different features, it’s essential to consider your specific requirements such as the materials you work with, the volume of production, and the machine’s flexibility.
Identify Your Primary Material Type
The materials you plan to work with, whether wood, plastic, or composites, greatly influence the choice of CNC routers. Each machine is designed with different cutting capabilities tailored for specific materials. Be sure to choose CNC routers with the necessary power, speed, and tools to handle your material efficiently.
Assess Production Volume and Speed
If your business requires high-volume production, look for multi-head CNC routers with high-speed cutting and minimal downtime. Machines that can handle multiple tasks simultaneously with various heads are perfect for boosting productivity in fast-paced environments. For smaller volumes, you may want a more flexible, compact model.
Consider Cutting Precision and Tolerance
Precision is vital for intricate designs and complex projects. Ensure the CNC routers offer high repeatability and accuracy. Features like advanced linear guides and ball screw drives enhance precision while choosing a machine with low tolerance variation will guarantee consistent output across multiple projects.
Evaluate the Number of Cutting Heads
The number of cutting heads directly affects your machine’s capability to perform multiple operations at once. CNC routers with more heads can simultaneously drill, mill, or engrave, which can significantly reduce production times and improve overall efficiency for complex, multi-step projects.
Match CNC Routers Size to Your Workspace
Make sure the CNC routers fit within your available space while still providing the cutting capacity you need. Larger CNC routers are suitable for larger projects but may take up more floor space. If you’re working in a smaller area, consider a more compact model that offers the same performance in a space-efficient design.
Check for Customizable Features
Different businesses have unique needs, so customizable CNC routers could offer significant advantages. Look for models that allow for tool changes, spindle adjustments, or modular configurations. Customizable machines can evolve with your production needs, offering flexibility as your business grows.
Examine Spindle Power and Speed
The spindle is one of the most critical components of CNC routers. Check for spindles that offer adjustable speeds and sufficient power to cut through your material effectively. High-powered spindles are essential for heavy-duty tasks and tough materials, ensuring smooth, efficient cutting.
Look for Software Compatibility
Ensure that the CNC router’s software is compatible with your existing CAD/CAM systems. Seamless integration with your design software reduces the learning curve and prevents compatibility issues. Many modern CNC routers come with intuitive, user-friendly software that supports advanced design features and enhances overall control.
Evaluate Automation and Tool Changing Features
Automated systems like tool changers or robotic material handling can save time and reduce labor costs. If your production requires frequent tool changes or material handling, an automated multi-head CNC router will enhance workflow, minimize human error, and increase operational efficiency.
Consider Energy Efficiency
Energy costs can add up quickly in high-volume operations. Look for CNC routers designed with energy-efficient motors and systems that minimize power consumption without compromising performance. Energy-saving features will help lower long-term operating costs, benefiting your bottom line over time.
Inspect Maintenance and Durability
Choose a machine that offers easy maintenance and is built to withstand the demands of your production environment. Machines with high-quality components, such as durable bearings, robust spindles, and sturdy frames, will last longer and require less frequent repairs, minimizing downtime.
Review Customer Support and Warranty
Reliable customer support and an extensive warranty are key when selecting CNC routers. Choose a machine from a manufacturer that offers responsive service, technical support, and a warranty that covers major components. This ensures your machine stays operational and any potential issues are addressed quickly.
What Materials Can The Multi-Head CNC Router Cut
Multi-head CNC routers are designed for versatility, capable of cutting a wide range of materials with high precision. These machines are commonly used in industries such as woodworking, metalworking, plastics, and composites. They can efficiently process hardwoods, softwoods, and engineered wood products like MDF and plywood. Additionally, multi-head CNC routers can handle various metals, including aluminum, brass, and steel, as well as non-ferrous materials like copper. The versatility of these CNC routers extends to plastics and composites, including acrylic, PVC, and fiberglass. With customizable tooling and adjustable settings, these CNC routers can tackle complex cuts, engravings, and detailed patterns across different materials, making them an ideal solution for diverse production needs.
Application Industry
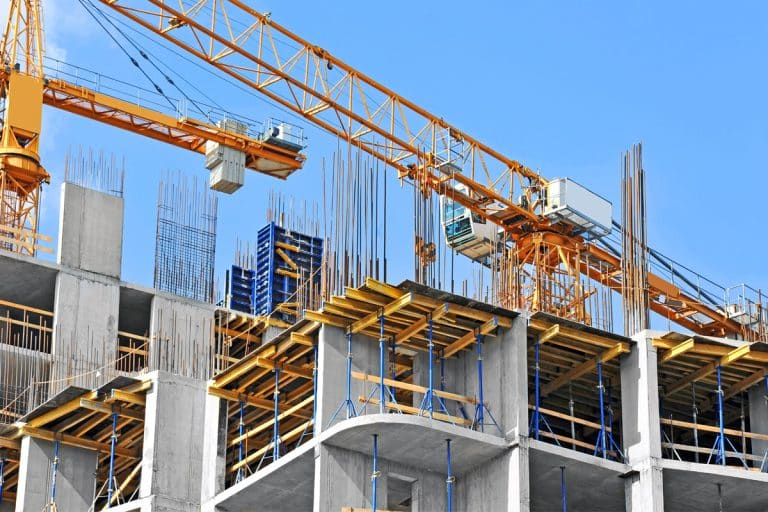
Construction Industry
The integration of CNC routers into construction workflows has ushered in a new era characterized by meticulous detailing, rapid prototyping, and improved material utilization.
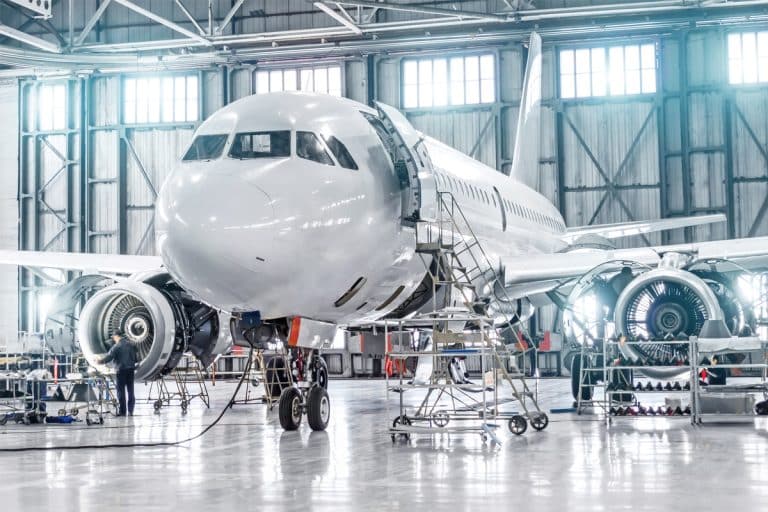
Aerospace Industry
The CNC router is widely used in aerospace engineering due to its unparalleled ability to carve complex designs, manufacture complex parts, and ensure tight tolerances.
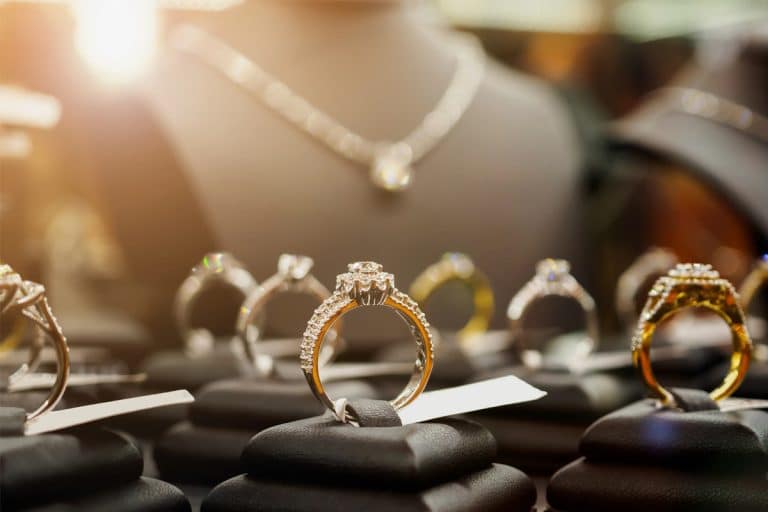
Jewelry Industry
The CNC router revolutionize the way fine jewelry is designed and made by delivering unparalleled precision and efficiency and producing intricate designs with meticulous attention to detail.
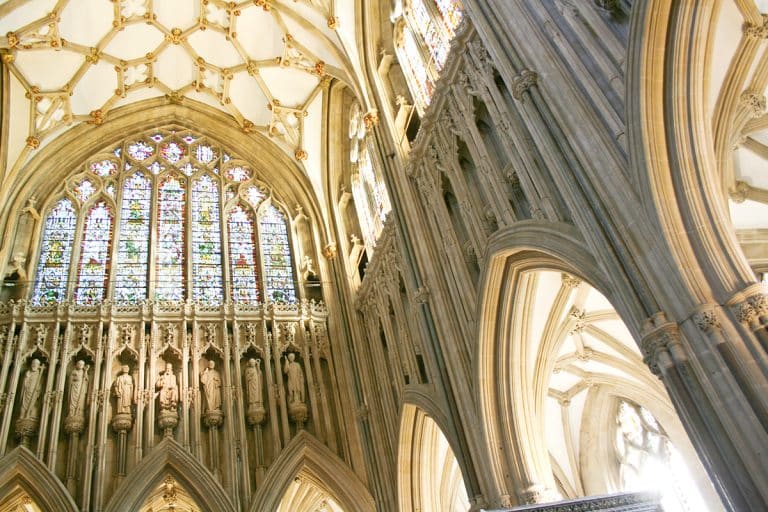
Stone Carving Industry
The integration of CNC routers into the stone carving industry is not only revolutionizing the way craftsmen carve, it is also redefining the boundaries of artistic possibilities in this ancient practice.
Blog
How to Choose the Right Stone CNC Router for Your Workshop?
This guide will walk you through the key factors to consider when choosing a stone CNC router, designed to help you invest wisely in a machine that delivers reliable performance ...
Read More
Best Budget CNC Router for Making Outdoor Signs?
In this guide, we'll break down the key features to look for, explore different models under a variety of price points, and help you choose the best budget CNC router ...
Read More
How to Maintain and Troubleshoot the ATC CNC Router?
This article will walk you through a practical maintenance procedure for your ATC CNC router and instruct you on how to diagnose and repair common problems that may arise.
Read More
What Warranties Are Typically Offered on CNC Routers?
In this article, we'll break down the different types of warranties typically offered on CNC routers, what's included, and how to make sure you're getting the support you need long ...
Read More
Frequently Asked Questions
What Can Multi-Head CNC Routers Do?
The multi-head CNC router is a highly versatile and powerful tool capable of performing a range of tasks across various industries. Its key feature is the ability to operate multiple cutting heads simultaneously, significantly increasing productivity by handling multiple tasks in parallel. This makes it ideal for a variety of applications, from woodworking and signage to manufacturing and prototyping.
- Versatile Cutting: It can cut a wide range of materials including wood, plastic, composites, foam, and metal, offering flexibility for different projects.
- Complex Carving & Engraving: The CNC router can carve intricate patterns and engrave detailed designs, perfect for applications such as custom signage, art, and decorative woodworking.
- Routing & Forming: The machine excels at milling and forming, creating complex 3D shapes with high precision.
- High-Speed Routing: Thanks to its advanced spindle and control system, the CNC router achieves high-speed routing, improving overall production efficiency.
- Automation & Repeatability: Automation ensures consistent, repeatable results, making it ideal for large-scale production with minimal human intervention.
- Production Optimization & Customization: By reducing material waste and offering customizable tool configurations, it optimizes the manufacturing process and enhances product quality.
- Prototyping & Material Finishing: The CNC router also allows for rapid prototyping and precise material finishing, ensuring a smooth, functional, or decorative surface for your projects.
What Are The Types of Multi-Head CNC Routers?
Multi-head CNC routers come in different configurations to cater to various manufacturing needs. Each type offers unique advantages, making them suitable for specific tasks. Here’s an overview of the most common types:
- Multi-Process (Sequential) CNC Router
- Operation: This type utilizes multiple spindles, each dedicated to a specific machining step. The machine switches between spindles to perform different operations in sequence.
- Advantages: Sequential processing optimizes precision and flexibility, allowing multiple tasks to be performed without compromising on efficiency. This setup is ideal when precision and multi-step processes are essential.
- Multi-Head (Synchronous) CNC Router
- Operation: This router features multiple spindles that operate simultaneously, with each head performing independent operations on different parts of the workpiece.
- Advantages: The ability to process multiple areas of the material at the same time significantly increases production speed without sacrificing accuracy. This type is ideal for high-volume manufacturing where efficiency is key.
- Hybrid Multi-Function CNC Router
- Operation: A hybrid multi-function CNC router combines traditional router capabilities with additional functionalities, such as plasma cutting, drilling units, vibrating knives, and more.
- Advantages: This versatile configuration offers a wide range of applications in a single machine, reducing the need for multiple machines and increasing overall system flexibility. It’s perfect for manufacturers looking to handle diverse tasks without additional equipment.
What is the Price of Multi-Head CNC Routers?
The price of a multi-head CNC router can vary significantly depending on several factors, such as the machine’s configuration, features, and capabilities. Similar to other CNC routers, the cost is influenced by elements like spindle power, working dimensions, motor type, control systems, and overall configuration. Higher-end features, such as automatic tool changers, advanced control systems, and enhanced precision, will naturally increase the cost.
On average, multi-head CNC routers typically range from $5,000 to $20,000. However, it’s important to note that these price ranges are approximate, and the actual cost will depend on the specific requirements of your project. Customizations, such as specialized tool configurations, enhanced functionality, and additional features, can further affect the final price.
For the most accurate pricing based on your needs, it’s best to reach out to our sales team. They can provide a customized quote based on the exact specifications and features you require for your operations.
Why Choose Multi-Head CNC Routers?
Multi-head CNC routers offer a range of advantages that can significantly enhance productivity, efficiency, and versatility in manufacturing. Here are several compelling reasons to choose a multi-head CNC router for your business:
- Increased Productivity: With the ability to perform simultaneous or sequential operations, multi-head CNC routers boost production speed without sacrificing accuracy. This leads to optimized workflow and higher output.
- Versatility and Flexibility: Multi-head CNC routers are capable of handling a wide variety of tasks—such as cutting, engraving, drilling, and forming—on a diverse range of materials. This flexibility enhances manufacturing capabilities within a single setup.
- Reduced Production Costs: By minimizing production time and reducing manual labor, these machines help cut costs. Faster processing and optimized material usage lead to less waste and lower overall operational expenses.
- Precision and Consistency: Whether operating sequentially or simultaneously, the high precision of each cutting head ensures consistent results across every part of the workpiece. This reliability is essential for high-quality output.
- Parallel Processing: Multiple heads working in parallel enable the production of multiple identical or similar parts simultaneously, which is especially advantageous for large-scale runs.
- Adaptability to Various Materials: These CNC routers can process various materials, including wood, plastics, and composites, making them suitable for diverse industries with varying material requirements.
- Optimized Workflow: The ability to perform multiple operations within a single setup streamlines the production process, reducing bottlenecks and enhancing throughput.
- Simplified Prototyping: Multi-head CNC routers accelerate prototyping, allowing for faster iterative design, testing, and production of prototypes, which is especially useful in industries like aerospace and automotive.
- Competitive Advantages: By investing in advanced technology, manufacturers gain faster turnaround times, improved precision, and stronger production capabilities compared to traditional single-head CNC routers, giving them a competitive edge.
- Scalability and Customization: Multi-head CNC routers offer customizable configurations, allowing businesses to adapt the machine to meet evolving production demands, supporting growth and diversification.
How to Maintain Multi-Head CNC Routers?
Proper maintenance is essential for ensuring the longevity, accuracy, and efficiency of your multi-head CNC router. Here are key maintenance tips to keep your machine in optimal condition:
- Regular Cleaning: Clean the CNC router regularly to remove dust, debris, and residue. Use compressed air, brushes, or a vacuum system to clean the work area, spindle, guide rails, and ball screws.
- Lubrication: Follow the manufacturer’s lubrication schedule and apply the correct lubricants to moving parts such as rails, bearings, and ball screws. This reduces friction and minimizes wear.
- Monitor the Cooling System: Regularly check coolant levels and ensure the cooling system is functioning well, especially for high-speed spindles. Clean or replace filters to prevent overheating and maintain spindle performance.
- Collet and Tool Holder Maintenance: Inspect and clean the collet and tool holder periodically. Replace worn components to ensure precise machining and improve tool holder life.
- Check Runout: Measure spindle runout regularly to ensure concentricity. Address any discrepancies promptly to maintain machining accuracy and prevent tool wear.
- Check Alignment and Calibration: Periodically check the alignment and calibration of the machine, ensuring accurate positioning and squareness of the spindle, axes, and overall machine geometry.
- Electrical Component Inspection: Inspect electrical connections, cables, and wiring regularly. Tighten loose connections and replace damaged cables to avoid electrical issues that may impact performance.
- Dust Removal System: If equipped with a dust collection system, clean or replace the filters regularly to maintain effective dust and chip removal, improving air quality and machine efficiency.
- Software Updates and Backups: Ensure the control software is up to date with the latest version. Regularly back up machine settings and programs to avoid data loss.
- Operator Training and Education: Train operators on proper machine operation, routine maintenance, and safety protocols. A well-trained operator is essential for preventing mistakes and maintaining machine health.
- Axis Movement Inspection: Regularly inspect the movement of all axes to ensure smooth operation. Address any irregularities immediately to prevent mechanical failures.
- Safety Measures: Test and ensure all safety features such as emergency stops, interlocks, and guards are in proper working condition. Regular safety checks are essential to protect operators and prevent accidents.
What Is the Expected Lifespan of Multi-Head CNC Routers?
The lifespan of a multi-head CNC router largely depends on factors such as machine quality, maintenance, operating conditions, and frequency of use. On average, with proper care and regular maintenance, a multi-head CNC router can last between 10 to 20 years. However, several factors can influence this:
- Maintenance Practices: Regular maintenance, including cleaning, lubrication, and calibration, plays a significant role in extending the lifespan of a CNC router. Well-maintained machines are less prone to wear and tear, ensuring longer operational life.
- Machine Usage: The intensity of machine use directly impacts its longevity. A CNC router used continuously in high-volume production will likely have a shorter lifespan compared to one used for less frequent, lighter tasks.
- Quality of Components: Higher-quality components such as motors, spindles, and rails can extend the lifespan of the machine. Investing in a well-built CNC router can pay off in terms of durability and overall performance.
- Environmental Conditions: Machines operating in environments with high humidity, extreme temperatures, or excessive dust may experience more wear and require more frequent servicing, which could affect their overall lifespan.
- Upgrades and Parts Replacement: Periodic upgrades to the software, tool changers, or spindles can enhance the performance and extend the useful life of a multi-head CNC router.
What Customer Support Do Multi-Head CNC Routers Provide?
Multi-Head CNC routers come with reliable customer support options to ensure smooth operation and user satisfaction:
- Free Online Technical Support: Customers can access complimentary technical assistance through online platforms, including email, chat, or video support. This service is ideal for troubleshooting, software setup, or resolving operational issues remotely.
- Paid On-Site Training: For users requiring hands-on guidance, on-site training sessions are available at an additional cost. These sessions cover installation, operation, and maintenance to ensure optimal use of the machine.
What Is The Warranty Period of Multi-Head CNC Routers?
Our CNC router is backed by a comprehensive warranty designed to give you peace of mind and protect your investment:
- 3-Year Warranty for the Entire Machine: This full warranty covers any defects or malfunctions in the machine as a whole, ensuring reliable performance and longevity over time.
- 5-Year Warranty for Core Components: Key components essential for optimal machine operation are covered for 1.5 years. This includes parts that may experience wear and tear with regular use, ensuring you have support for the most vital parts of the machine.