- 11-16 Min Read
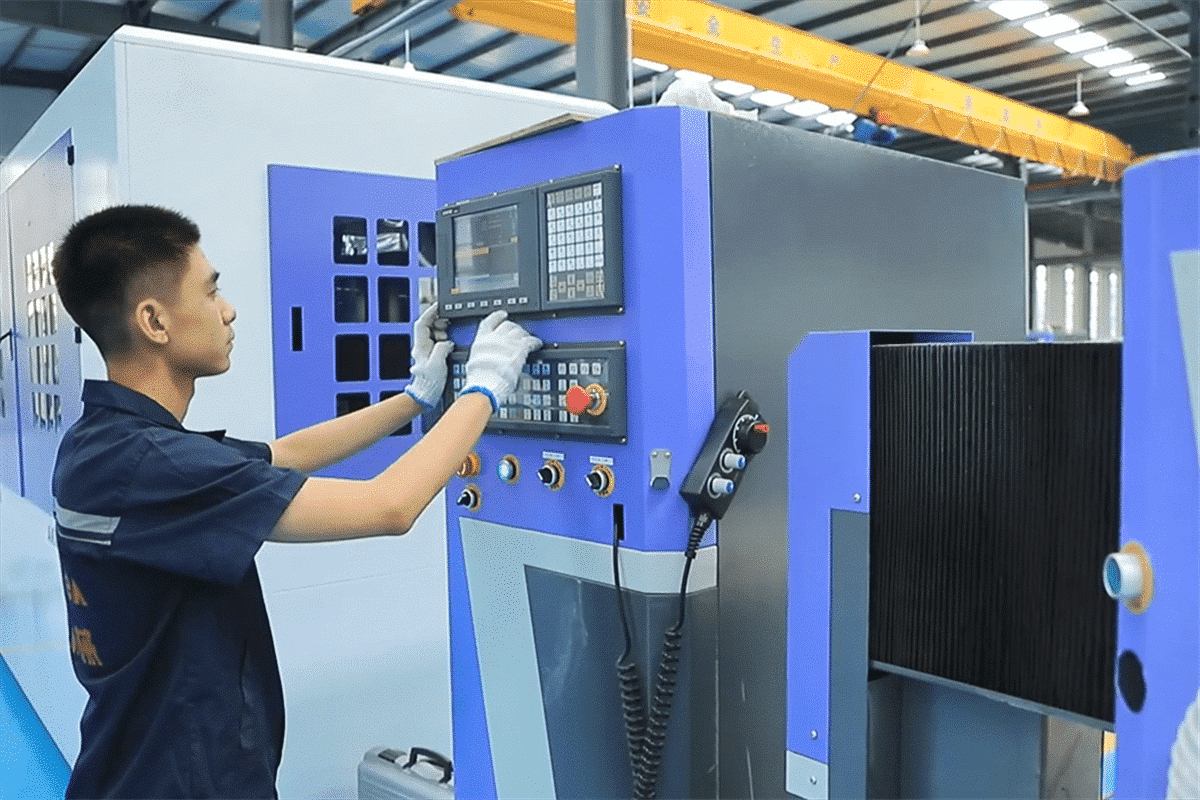
How to Program CNC Router
Understanding CNC Routers
Basic Concepts of CNC Programming
- G-code and M-code: At the heart of CNC programming are G-codes and M-codes. G-codes dictate the tool’s motion, while M-codes control auxiliary functions like tool changes or coolant activation.
- Toolpaths: Think of toolpaths as the route the cutting tool follows to create the desired design. These paths are meticulously planned to achieve precision in the final product.
Software for CNC Programming
- CAD Software: Use Computer-Aided Design software to create detailed 2D or 3D models of your project.
- CAM Software: Transition from design to production by utilizing Computer-Aided Manufacturing software, which translates your design into the G-code necessary for CNC routers.
Creating a CNC Program
- Designing the Part: Begin by creating a detailed design of the part you want to produce using Computer-Aided Design (CAD) software. Ensure that the design is compatible with CNC machining and consider factors such as tool clearance and material constraints.
- Toolpath Generation: Use Computer-Aided Manufacturing (CAM) software to generate toolpaths from your design. The CAM software will analyze the geometry of your design and create a series of toolpaths that the CNC router will follow to cut or carve the material.
- G-code Output: Once the toolpaths are generated, export the instructions as G-code. G-code is a set of alphanumeric codes that the CNC router understands. Ensure that the G-code is compatible with your CNC router’s controller.
Setting Up the CNC Router
- Material and Workpiece: Select the appropriate material and secure it on the worktable.
- Right Tool: Select the appropriate cutting tool for your design. Factors to consider include the material being used, the complexity of the design, and the desired finish. Install the chosen tool securely in the CNC router’s tool holder.
- Zero Point Setup: Establish the zero point, a reference for the CNC router, ensuring accuracy in machining.
Running the CNC Program
- Load the Program: Load the G-code program into the CNC router’s control system. This can be done through a USB drive, network connection, or other means depending on the machine. Double-check the program to ensure accuracy and avoid errors.
- Run a Test: Before running the full program, perform a test run to ensure that the tool paths are correct and the machine operates as expected. Use a scrap piece of material for the test to avoid wasting valuable resources.
- Execute the Program: Once satisfied with the test run, initiate the full program. Monitor the CNC router during operation to ensure that everything proceeds smoothly. Be prepared to make adjustments if any issues arise.
Post-Processing and Quality Control
- Inspection and Measurement: After the CNC router completes the machining process, carefully remove the finished part from the work table. Check for any visual defects, irregularities, or inaccuracies.
- Surface Finish Evaluation: Assess the surface finish of the machined part. Depending on your design specifications, you may need to sand, polish, or apply additional treatments to achieve the desired texture.
- Assembly Check: If your design involves multiple components or assemblies, perform a check to ensure proper fit and alignment. Verify that all machined parts fit together seamlessly.
Document and Save
- Documenting Parameters: Document the machining parameters used during the CNC programming phase. This includes spindle speed, feed rates, tool changes, and any other relevant settings.
- Final Documentation and Archiving: Document the results of the quality control process and any changes made during refinement. Archive both the original CNC program and the modified version for future use or reference.
G-code and CNC operation troubleshooting
Incorrect Toolpath
- Issue: The CNC router is not following the intended toolpath.
- Troubleshooting: Check the G-code for errors in the toolpath generation process using CAM software. Verify that the zero point and workpiece setup are accurate. Ensure the correct G-code file is loaded into the CNC router’s control system.
Toolpath Overlapping or Gaps
- Issue: Toolpaths are either overlapping or leaving gaps in the machined part.
- Troubleshooting: Adjust the toolpath parameters in the CAM software. Check for inconsistencies in the original CAD design. Inspect the G-code for any errors or missing commands.
Incorrect Dimensions
- Issue: The machined part does not match the expected dimensions.
- Troubleshooting: Verify the accuracy of the CAD design. Check tool offsets and tool diameter settings in the CAM software. Ensure proper calibration of the CNC router.
Tool Breakage
- Issue: The cutting tool breaks during operation.
- Troubleshooting: Check the tool for signs of wear or damage before starting. Check the tool’s compatibility with the material being machined. Adjust the cutting parameters, such as feed rate and spindle speed, to prevent excessive tool stress. Ensure that the tool is properly secured in the tool holder.
Excessive Tool Wear
- Issue: The cutting tool wears out quickly.
- Troubleshooting: Verify that the tool material is suitable for the material being machined, the appropriate tool coating can be used for the specific material. Adjust cutting parameters to reduce tool wear without sacrificing machining efficiency. Check that tools are properly lubricated and regularly maintain cutting tools.
Machine Jerking or Vibrations
- Issue: The CNC router exhibits jerky movements or vibrations during operation.
- Troubleshooting: Inspect the mechanical components for wear or damage. Check for loose bolts or connections. Ensure proper lubrication of moving parts.
Material Clamping Issues
- Issue: The material shifts or moves during machining.
- Troubleshooting: Use secure clamping methods, such as clamps or vacuum systems. Check for inconsistent material thickness and ensure the workpiece is flat on the worktable.
G-code Syntax Errors
- Issue: G-code file fails to execute due to syntax errors.
- Solution: Use CAM software to validate the G-code for errors. Manually review the G-code file for any anomalies or typos. Correct the errors and regenerate the G-code.
Incorrect Spindle Speed or Feed Rates
- Issue: Inconsistent machining results due to incorrect spindle speed or feed rates.
- Troubleshooting: Verify the spindle speed and feed rate settings in the CAM software. Adjust parameters based on material specifications. Check for any inconsistencies in the G-code related to speeds and feeds.
Program Execution Stops Midway
- Issue: The CNC router stops abruptly during operation.
- Solution: Check the G-code file for syntax errors or corruption. Inspect the control system for loose connections or faults. Restart the CNC router and reload the G-code.
How to Optimize CNC Router Program
- Tool Selection: Choose the right tool for the job. Consider factors such as material type, cutting depth, and desired finish. Opt for high-quality tools with appropriate coatings for extended tool life. Group similar operations to use the same tool for consecutive tasks. Minimize the number of tool changes, as each change adds to the overall machining time.
- Optimize Feeds and Speeds: Adjust feed rates and spindle speeds based on the material and tool being used. Use the recommended cutting parameters from the tool manufacturer or conduct tests to find optimal settings. Some CAM software provides adaptive feed rate control for optimal performance.
- Efficient Toolpath Planning: Minimize unnecessary tool movements by optimizing contour toolpaths. Use CAM software with efficient algorithms to generate smooth and efficient paths. Utilize high-efficiency pocketing strategies, such as adaptive clearing or high-speed machining, to remove material more rapidly.
- Trochoidal Milling: Implement trochoidal milling strategies, especially in pockets and slots. This technique involves using circular toolpaths to minimize tool engagement and increase tool life.
- Cut Depth and Stepover: Balance the depth of the cut with the stepover to ensure efficient material removal without overloading the tool. Adjust these parameters based on the material and tool being used.
- Consideration of Cutting Direction: Experiment with both climb and conventional cutting to determine the most efficient method for your specific application. Climb cutting can reduce tool deflection and produce a better finish.
- Toolpath Smoothing: Use CAM software with advanced toolpath smoothing algorithms to minimize sharp changes in direction, improving surface finish and reducing tool wear.
- Use High-Quality CAM Software: Invest in advanced CAM software that provides optimization features and efficient toolpath generation. Utilize simulation features to visualize and optimize the toolpaths before machining.
- Nesting Optimization: If you’re machining multiple parts from a single sheet, optimize the layout (nesting) to minimize material waste and improve overall efficiency. Efficient nesting can significantly reduce material costs.
- Ramp Entry Strategies: Use ramp entry strategies instead of plunging directly into the material. Ramps reduce stress on the tool and improve surface finish.
- Reducing Air Moves: Minimize non-cutting moves (air moves) between machining operations to reduce cycle time. Optimize the toolpath to eliminate unnecessary retractions and rapid movements.
- Maintain CNC Machine: Regularly maintain the CNC router by lubricating components, checking for loose parts, and ensuring proper calibration. Keep the machine in optimal condition to avoid unexpected issues during operation. A well-maintained machine operates more efficiently.
Advanced CNC Programming Technology
Advanced CNC programming technology involves a combination of software, hardware, and innovative techniques to optimize the machining process, improve efficiency, and enable the production of complex and high-precision components. It is a complex method and technique of programming CNC machines for manufacturing purposes. Advanced CNC programming technology encompasses several key aspects:
- CAD/CAM Integration: Computer-Aided Design (CAD) and Computer-Aided Manufacturing (CAM) software are integrated to create a seamless workflow. CAD is used for designing the part, while CAM generates the CNC code necessary for machining based on the CAD model.
- High-Speed Machining (HSM): Advanced CNC programming involves optimizing cutting parameters for high-speed machining. This includes adjusting spindle speeds, feed rates, and tool paths to achieve faster and more efficient machining without compromising accuracy.
- 5-Axis Machining: Traditional CNC machines operate in three axes (X, Y, Z). Advanced CNC programming extends this capability to include 5-axis machining, allowing for more complex and intricate part geometries to be produced in a single setup.
- Toolpath Optimization: Utilizing algorithms to optimize tool paths can significantly reduce cycle times and improve overall machining efficiency. This involves finding the most efficient route for the cutting tool to traverse the material.
- Simulation and Verification: Advanced CNC programming includes the use of simulation software to validate and verify the machining process before it is executed on the actual CNC machine. This helps in detecting errors, collisions, or toolpath issues in a virtual environment, reducing the risk of mistakes during actual production.
- Adaptive Machining: This technology involves adjusting machining parameters in real time based on feedback from sensors or measurements during the machining process. It ensures consistent quality and adapts to variations in material properties.
- IoT Integration: Internet of Things (IoT) technologies can be integrated into CNC machines for real-time monitoring and data collection. This allows for predictive maintenance, performance optimization, and overall equipment efficiency improvements.
- Additive Manufacturing Integration: Some advanced CNC systems can integrate with additive manufacturing processes, allowing for hybrid manufacturing where both subtractive and additive processes are combined in a single setup.
- Cloud-Based Programming: Storing and accessing CNC programs in the cloud enables easier collaboration, version control, and remote monitoring of machining processes.
- Artificial Intelligence (AI) in CNC: The use of AI algorithms can optimize tool selection, cutting parameters, and toolpath generation based on historical data and real-time feedback, further enhancing efficiency and quality.
Safety precautions in CNC programming
Safety is a critical aspect of CNC programming and machining processes. By incorporating safety precautions into CNC programming and machining practices, manufacturers can create a safer working environment and reduce the risk of accidents or injuries. It’s essential to prioritize safety at every stage of the CNC machining process. Here are some key safety precautions to consider in CNC programming:
- Training and Education: Ensure that CNC programmers and operators are adequately trained and have a thorough understanding of the CNC machine, its software, and safety protocols.
- Machine Familiarity: Operators should be familiar with the specific CNC router they are working with, including its control panel, emergency stop procedures, and any unique features.
- Protective Equipment: Wear appropriate personal protective equipment (PPE), including safety glasses, hearing protection, and any additional equipment required for specific machining tasks.
- Emergency Stop Procedures: Communicate and understand the emergency stop procedures. Ensure that operators can quickly and effectively stop the machine in case of an emergency.
- Tool Inspection: Regularly inspect and maintain cutting tools. Ensure that tools are in good condition, properly secured, and meet safety standards. Replace dull or damaged tools promptly.
- Secure Workholding: Properly secure workpieces in the machine to prevent movement or shifting during machining. Use clamps, vises, or other appropriate work-holding devices.
- Machine Enclosures: If the CNC machine has an enclosure, keep it closed during operation. This helps contain debris and provides an additional layer of protection.
- Spindle Speed and Feed Rates: Set appropriate spindle speeds and feed rates to prevent tool breakage or excessive wear. Avoid pushing the machine beyond its recommended capabilities.
- Toolpath Simulation: Before executing the CNC program on the actual machine, use toolpath simulation software to check for collisions, errors, or any potential safety issues.
- Material Handling: Follow proper procedures for loading and unloading materials. Use lifting equipment or assistance as needed to prevent injuries.
- Ventilation and Dust Collection: Ensure proper ventilation and dust collection systems are in place to control airborne particles and maintain a safe working environment.
- Regular Maintenance: Conduct regular maintenance on the CNC router to ensure all components are in good working condition. This includes lubrication, inspections, and addressing any issues promptly.
- Fire Safety: Be aware of potential fire hazards, especially when working with materials that may generate heat or sparks. Have fire extinguishers readily available and conduct fire safety training.
- Secure Programming Practices: Verify CNC programs thoroughly before running them on the machine to prevent errors or unexpected movements that could pose safety risks.
- Communication: Establish clear communication protocols between CNC programmers, operators, and other personnel involved in the machining process.