Table of Contents
How To Set Up A CNC Router: Step-by-Step Guide
- 10-15 Min Read
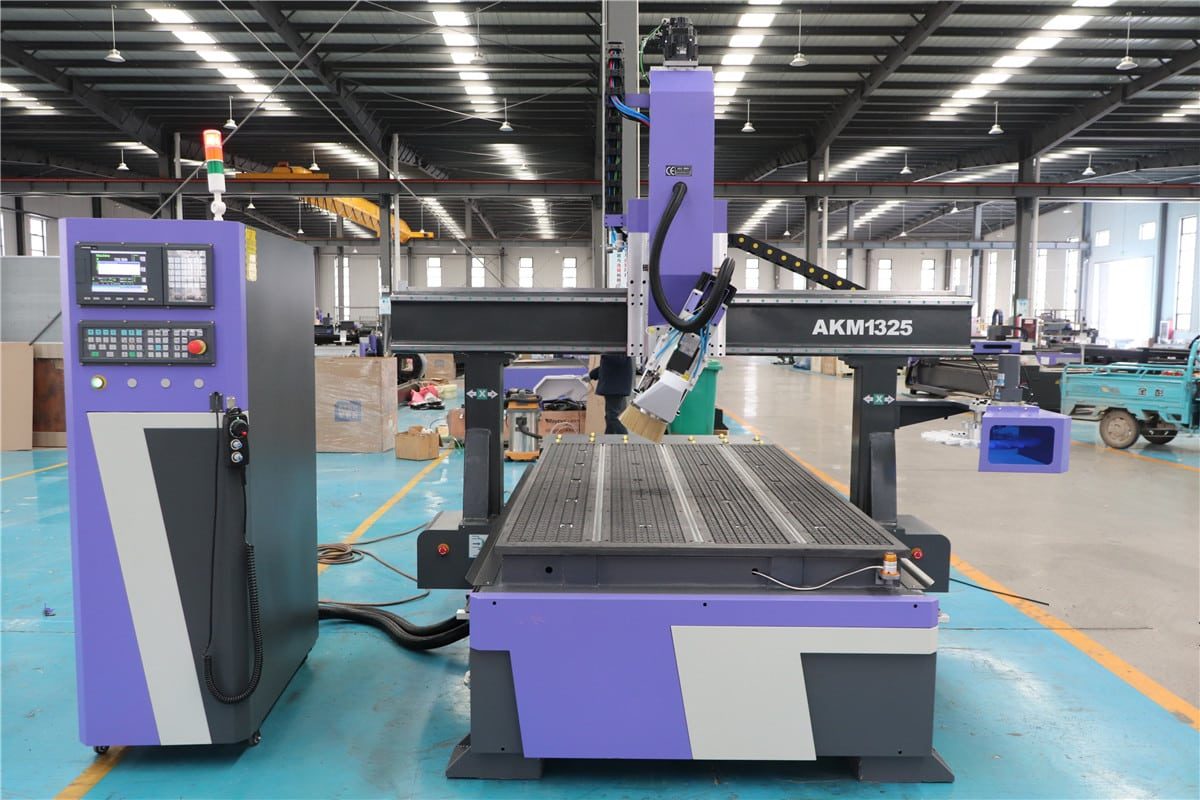
In the realm of modern manufacturing and design, CNC (Computer Numerical Control) routers stand as versatile and indispensable tools. These automated systems offer precision and efficiency in shaping various materials, from wood and plastics to metals. Setting up a CNC router is a meticulous process that involves a series of steps to ensure optimal performance, accuracy, and safety. In this comprehensive guide, we’ll delve into the detailed process of setting up a CNC router, covering each crucial aspect. Whether you are a beginner stepping into the world of CNC machining or an experienced operator looking to enhance your setup procedures, this guide serves as a valuable resource for a successful CNC router installation.
How to set up CNC router
A CNC router operates based on numerical control, where computer programs dictate the movement and actions of the machine. These programs, often in the form of G-code, are generated through CAD (Computer-Aided Design) and CAM (Computer-Aided Manufacturing) software. The CNC router interprets these instructions to execute precise cutting, milling, and carving operations. Here is a general step on how to set up a CNC router.
Preparing the Workspace
- Workspace Layout: Ensure that the workspace is spacious enough to accommodate the CNC router and provide ample room for the operator to maneuver comfortably. The layout should allow easy access to the machine’s control panel, tool change area, and material loading zone.
- Environmental Considerations: Provide proper ventilation to disperse any dust or fumes generated during machining. Adequate lighting is crucial for visibility, and maintaining a clean, organized environment contributes to both safety and efficiency.
Unboxing and Assembling the CNC Router
- Unpacking Inspection: Upon receiving the CNC router, carefully unbox and inspect its components. Follow the manufacturer’s instructions for assembling the machine.
- Gantry Assembly: Assemble the gantry, ensuring that all components fit securely. Pay attention to alignment and use the provided tools and hardware.
- Motor Installation: Install the motors and ensure they are correctly connected to the corresponding axes. Follow the wiring diagrams provided by the manufacturer.
- Table Setup: Set up the machine bed or table, ensuring it is level and stable. Flat surfaces help ensure the accuracy of CNC machining.
Electrical Connections
- Power Supply: Connect the CNC router to a stable power source, adhering to the specified electrical requirements. Ensure that the power supply is grounded for safety.
- Motor Wiring: Connect the motors according to the wiring diagrams provided by the manufacturer. Pay attention to the correct wiring sequence and ensure a secure connection.
Machine Calibration
- Homing: Initiate the homing process to establish the machine’s starting position. The CNC router will move to predefined reference points for each axis.
- Steps per Unit Calibration: Calibrate the steps per unit for each axis to ensure precise movement. This step involves adjusting the number of motor steps required to move the machine a specific distance.
Tool Setup and Height Calibration
- Tool Selection: Choose the appropriate cutting tools based on the type of material and machining operations. Install the tools securely in the tool holders.
- Workholding Devices: Securely fasten the material to be machined using suitable workholding devices such as clamps, vises, or vacuum tables. Ensure proper alignment and stability.
- Tool Height Calibration: Calibrate the height of the cutting tool to the material surface. This ensures accurate machining depth. Depending on the CNC router model, tool height calibration can be done manually or with automatic tool height sensors.
CNC Software Installation and Configuration
- Software Installation: Install the CNC control software on the designated computer or control panel. Follow the installation instructions provided by the manufacturer.
- Software Configuration: Configure the software settings, including machine parameters, axis limits, and any specific features of your CNC router. Ensure compatibility between the CNC router and the G-code instructions generated by your CAM software.
Toolpath Programming and Verify
- Create or Import CNC Programs (G-code): Use CAD/CAM software to create or import CNC programs (G-code) based on your design. Define toolpaths, cutting parameters, and any additional instructions necessary for your machining operations.
- Verify Toolpaths Through Simulation: Utilize toolpath simulation features in your CAD/CAM software to verify the CNC program before running it on the actual machine. Check for potential collisions or errors in the simulation. Make adjustments as needed to ensure the CNC program aligns with your design.
These are the general steps on how to set up a CNC router. By following these steps and consulting the specific guidelines provided by the CNC router manufacturer, you can ensure a successful setup and optimize the performance of your CNC router for accurate and efficient machining.
Troubleshooting common CNC router setting issues
Solving common CNC router setup issues helps ensure smooth operation and optimal performance of your machine. Problems can be caused by a variety of factors, including incorrect configuration settings, mechanical issues, or CNC program errors. Next, we’ll explore common CNC router setup issues and provide troubleshooting steps to resolve them.
Inaccurate Cutting Dimensions
The CNC router is not cutting to the specified dimensions, resulting in inaccuracies in the finished workpiece. Here are the troubleshooting steps:
- Calibrate Steps per Unit: Check the steps per unit calibration for each axis. Incorrect calibration can lead to discrepancies in movement. Recalibrate as needed to ensure accurate positioning.
- Tool Diameter Compensation: Verify that tool diameter compensation settings are correct. If the CNC program assumes a different tool diameter than the actual tool being used, it can result in inaccuracies.
- Material Thickness: Ensure that the CNC program accounts for the correct material thickness. Adjust the Z-axis zero reference point if necessary.
- Toolpath Verification: Use CAD/CAM software to simulate and verify toolpaths. Check for any discrepancies between the intended tool paths and the actual cutting paths.
Excessive Vibration or Noise
The CNC router produces excessive vibration or noise during operation. Here are the troubleshooting steps:
- Spindle Speed and Feed Rates: Adjust spindle speed and feed rates based on the material being machined. Running the machine too fast or too slow can lead to vibrations.
- Tool Condition: Inspect the cutting tool for damage or wear. Dull or damaged tools can cause excessive vibration. Replace or sharpen tools as needed.
- Tool Holder and Collet: Ensure that the tool is securely held in the tool holder and collet. Loose tooling can lead to vibrations. Tighten the tool holder properly.
- Machine Rigidity: Check for any loose or damaged components in the machine structure. Tighten bolts and inspect the gantry, rails, and other mechanical parts for stability.
Inconsistent Cutting Depth
The CNC router does not maintain a consistent cutting depth across the workpiece. Here are the troubleshooting steps:
- Z-Axis Calibration: Calibrate the Z-axis to ensure accurate and consistent cutting depths. Check for any mechanical issues affecting the Z-axis movement.
- Tool Runout: Measure tool runout using a dial indicator. Excessive runout can lead to inconsistent cutting depths. Replace or reposition the tool to minimize runout.
- Material Flatness: Ensure that the material is securely fastened and flat on the machine bed. Warped or uneven material can affect cutting depth.
- Check for Mechanical Issues: Inspect the Z-axis components for any mechanical problems, such as loose screws, worn bearings, or misalignment.
CNC Router Stops Mid-Operation
The CNC router unexpectedly stops in the middle of a machining operation. Here are the troubleshooting steps:
- Emergency Stop Button: Check if the emergency stop button has been pressed accidentally. Reset the emergency stop if necessary.
- Power Supply Issues: Ensure a stable power supply. Voltage fluctuations or power interruptions can cause the CNC router to stop. Consider using a UPS (Uninterruptible Power Supply) for protection.
- Overheating: Monitor the temperature of the CNC router components, especially the motor drivers. Overheating can trigger protective measures and cause the machine to stop. Improve ventilation if needed.
- Review G-code: Examine the G-code program for errors. Incorrect or incomplete code can lead to unexpected stops. Validate the G-code and make corrections as needed.
Toolpath Errors or Collisions
The CNC router encounters errors or collisions during the machining process. Here are the troubleshooting steps:
- Simulation: Simulate tool paths using CAD/CAM software before running the CNC program. Identify and rectify any collisions or errors in the simulation.
- Toolpath Optimization: Optimize toolpaths to avoid abrupt changes in direction or tool engagement. Smooth and efficient tool paths reduce the risk of collisions.
- Check Tool Length Offset: Verify that the tool length offset is correctly configured. Incorrect tool length offsets can lead to collisions.
- Material Setup: Ensure that the material is properly secured and positioned. Incorrect material setup can result in toolpath errors and collisions.
Effectively troubleshooting common CNC router setting issues requires a systematic approach, involving careful inspection of hardware, software, and machining parameters. Regular maintenance, calibration, and adherence to best practices can significantly minimize the occurrence of problems. Additionally, staying informed about the specific requirements and recommendations provided by the CNC router manufacturer. By addressing issues promptly and methodically, operators can ensure a reliable and efficient CNC machining process.
How to Optimizing CNC Router Performance
Optimizing CNC router performance involves various considerations to ensure efficiency, accuracy, and reliability. Here are some general tips to enhance CNC router performance. Remember that optimizing CNC router performance is an ongoing process that involves a combination of proper equipment setup, programming, and maintenance practices. Regularly monitoring and fine-tuning these factors will contribute to consistent and efficient machining operations.
Material Selection and Fixing
- Understand the properties of the materials you are cutting.
- Choose materials that are suitable for your CNC router’s specifications.
- Securely fixturing the material reduces vibrations and ensures accurate cuts.
- Use appropriate clamps, jigs, or vacuum systems for effective material holding.
- Explore different workholding methods for various materials and projects.
Tool Selection and Maintenance
- Choose high-quality cutting tools suitable for the material you’re working with.
- Regularly inspect and maintain tools to ensure sharpness and proper functioning.
Feeds and Speeds
- Optimize feed rates and spindle speeds based on the material being cut.
- Avoid excessive spindle speeds that can lead to tool wear or material burning.
- Consider the material’s hardness and the type of cut you’re performing.
- Refer to tool manufacturers’ recommendations and make adjustments based on real-world performance.
Toolpath Optimization
- Simulate tool paths before actual machining to identify and correct any potential issues.
- Verify that the tool paths are collision-free and optimized for the CNC router.
- Use efficient tool paths to minimize tool travel and reduce cycle times.
- Implement toolpath strategies that minimize sudden direction changes to enhance cutting efficiency.
Dust Collection
- Excessive dust can affect the CNC router’s performance and longevity. Implement effective dust collection systems to keep the workspace clean.
Machine Calibration
- Regularly calibrate the CNC router to maintain accuracy.
- Check and adjust axis alignments, machine squareness, and tool length offsets.
Proper Programming
- Use CAM (Computer-Aided Manufacturing) software to generate efficient toolpaths.
- Optimize toolpath strategies to minimize tool changes and reduce machining time.
- Consider adaptive clearing techniques for efficient material removal.
Training and Skill Development
- Ensure operators are well-trained in programming and operating the CNC router.
- Educate them on proper loading, unloading, and maintenance procedures.
- Stay updated with the latest technology and techniques to improve performance continually.
- Keep CNC control software and firmware up to date to benefit from performance improvements and bug fixes.
Regular Maintenance
- Follow the manufacturer’s maintenance schedule.
- Keep the machine clean and inspect components regularly for wear and tear.
- Regularly calibrate the machine to maintain accuracy.
Coolant and Lubrication
- Use coolant or lubrication systems to prevent overheating of tools and improve cutting efficiency.
- Monitor coolant levels and replace them regularly, and ensure proper maintenance of coolant systems.
Quality Control
- Implement a quality control process to check finished parts for accuracy and adherence to specifications.
- Use probing systems for in-process measurement and tool offset adjustments.
Security Guide and Best Practices
When setting up a CNC router, security should be a priority to ensure safe and efficient operation. Here are some general security guidelines and best practices for setting up a CNC router. Always consult the specific documentation provided by the CNC router manufacturer for detailed security instructions tailored to your equipment.
Physical Security
- Secure Location: Place the CNC router in a secure area to prevent unauthorized access.
- Restricted Access: Limit access to authorized personnel only.
Network Security
- Independent Network Settings: If possible, place the CNC router on a separate network to reduce the risk of unauthorized access to sensitive data.
- Firewall Protection: Implement firewalls to control incoming and outgoing network traffic.
- Regular Updates: Keep all networking equipment, including controllers and switches, updated with the latest security patches.
Authentication and Access Control
- Strong Passwords: Use strong and unique passwords for all user accounts on the CNC router.
- Multi-Factor Authentication (MFA): Enable MFA to add an extra layer of security.
- Role-Based Access Control (RBAC): Implement RBAC to restrict access based on job responsibilities.
Software Security
- Firmware Updates: Regularly update the CNC router’s firmware to patch vulnerabilities and improve performance.
- Secure Software Sources: Only install software and applications from reputable sources.
- Regular Audits: Conduct regular security audits to identify and address potential vulnerabilities.
Emergency Stop (E-Stop) System
- Install E-Stop Button: Place emergency stop buttons within easy reach of operators to quickly halt machine operations in case of emergencies.
Monitoring and Logging
- Activity Logging: Enable logging to keep track of user activities, system events, and potential security incidents.
- Monitoring System: Implement a monitoring system to detect unusual patterns or activities that may indicate a security breach.
- Data Backups: Regularly back up critical data and configurations to prevent data loss in case of system failures or security incidents.
Training and Awareness
- User Training: Provide comprehensive training for operators on security best practices and safe operation of the CNC router.
- Security Awareness: Foster a security-aware culture among all personnel involved in CNC operations.
- Develop a Plan: Have an emergency response plan in place to address security incidents promptly and effectively.
Future Trends in CNC Router Setup and Automation
The field of CNC router setup and automation is continually evolving, driven by advancements in technology and industry demands. Here are some future trends that may shape the landscape of CNC router setup and automation. These trends reflect the ongoing efforts to enhance efficiency, flexibility, and precision in CNC router setups while addressing the evolving needs of modern manufacturing processes. As technology continues to advance, understanding these trends can help companies maintain a competitive advantage in the CNC machining industry.
Integration of AI and Machine Learning
- Smart Decision-Making: AI algorithms can optimize tool paths, predict tool wear, and enhance overall efficiency.
- Adaptive Machining: Machine learning can enable CNC routers to adapt to variations in material properties, improving precision.
IoT Connectivity
- Remote Monitoring: Integration with the Internet of Things (IoT) allows for real-time monitoring of CNC routers, enabling operators to track performance and receive alerts remotely.
- Predictive Maintenance: IoT sensors can facilitate predictive maintenance by monitoring equipment health and identifying potential issues before they cause downtime.
Digital Twin Technology
- Simulation and Visualization: Digital twins create virtual replicas of physical CNC routers, allowing for simulation and visualization of machining processes before actual production.
- Performance Optimization: Analyzing data from digital twins can lead to continuous improvements and optimization of CNC router performance.
Augmented Reality (AR) in Training and Operation
- Training Simulations: AR can be used for training operators by providing immersive simulations of CNC router setup and operation.
- Real-time Assistance: AR overlays can offer real-time information and guidance to operators during the machining process, improving accuracy and efficiency.
Collaborative Robotics (Cobots)
- Human-Robot Collaboration: The integration of collaborative robots with CNC routers allows for safer and more efficient collaboration between human operators and machines.
- Flexibility in Automation: Cobots can adapt to changing production requirements, offering flexibility in automation setups.
Additive Manufacturing Integration
- Hybrid Systems: Integration of CNC routers with additive manufacturing processes, enabling the production of complex components with both subtractive and additive techniques.
- Material Variety: CNC routers may be used in conjunction with 3D printing for processing a broader range of materials.
Advanced Material Handling Systems
- Automated Loading/Unloading: Integration of robotic systems for automated loading and unloading of materials, reducing manual labor and increasing efficiency.
- Material Tracking: RFID and barcode systems for tracking material throughout the production process, improving traceability.
Energy Efficiency and Sustainability
- Green Machining Practices: Future CNC routers may incorporate energy-efficient features and sustainable machining practices to minimize environmental impact.
- Recycling and Waste Reduction: Improved waste management systems and recycling processes integrated into CNC router setups.
Customization and Small Batch Production
- Agile Manufacturing: CNC router setups that enable quick changeovers and efficient production of customized or small-batch components.
- Digitalization of Workflows: Digital tools for design and programming that facilitate rapid customization.
Cybersecurity Measures
- Enhanced Security Protocols: With increased connectivity, future CNC routers will likely incorporate advanced cybersecurity measures to protect against cyber threats and unauthorized access.
Summarize
Setting up a CNC router is a meticulous process that requires prioritizing efficiency and adhering to safety protocols. From physical considerations to network and software security, a well-established setup ensures smooth operations and minimizes potential risks. As technology evolves, embracing trends such as AI integration, IoT connectivity, and collaborative robotics can enhance the capabilities of CNC routers, paving the way for increased automation and precision. By staying informed about these advancements and adhering to best practices, manufacturers can not only optimize their CNC router setups for current demands but also position themselves for success in the dynamic landscape of advanced manufacturing.
At AccTek CNC, we provide users with high-quality CNC routers and complete technical support. From the initial setup and configuration of your CNC router to ongoing troubleshooting and optimization, our team of highly skilled and experienced technicians is committed to providing comprehensive assistance. Specializing in the provision of CNC routers, AccTek empowers users with versatile and high-performance equipment tailored for various purposes. Whether you are adding a high-end industrial CNC router for mass production or a small hobbyist CNC router for your personal studio, you will find the answer here.
Want To get a good machine?
Click the button, our CNC Experts will contact you and send you a solution.