Table of Contents
Why Do You Need a CNC Router?
- 10-15 Min Read
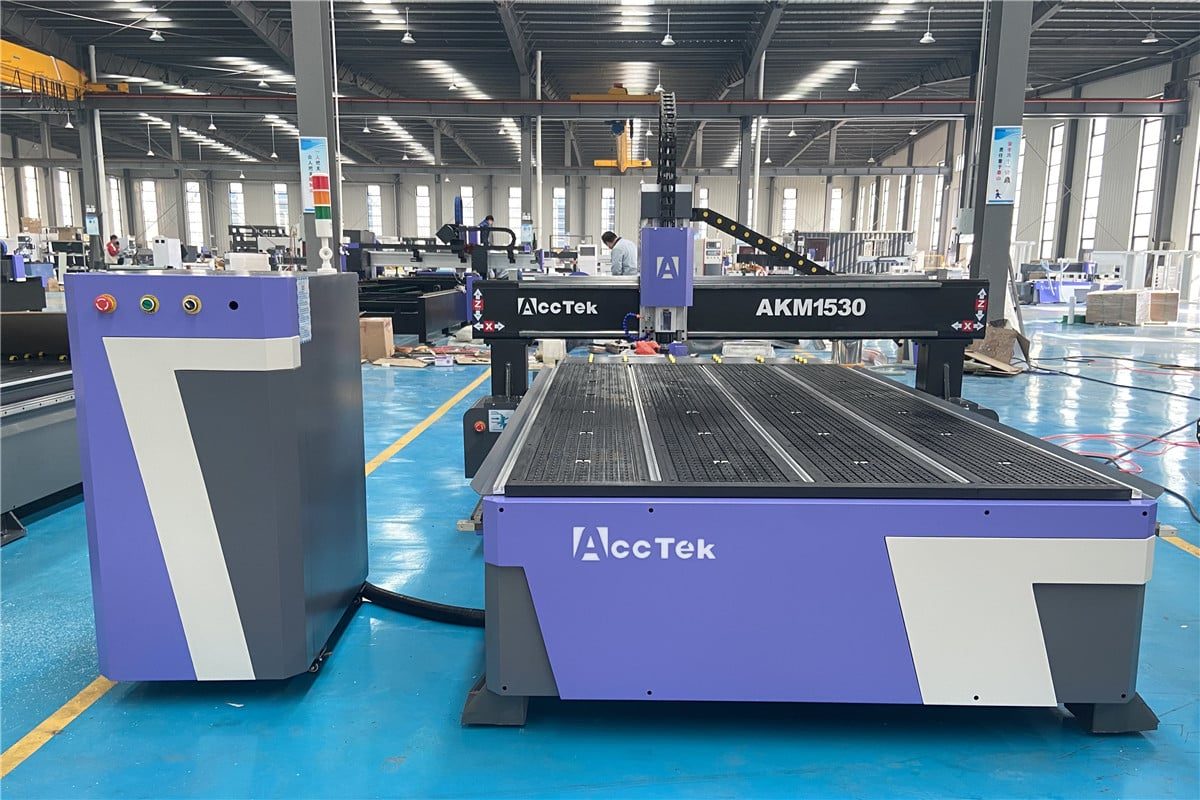
A CNC router, short for Computer Numerical Control router, has become an indispensable tool in various industries, revolutionizing the way we approach precision machining and woodworking. This cutting-edge technology combines computer programming with mechanical precision to execute intricate designs with unmatched accuracy and efficiency. The need for CNC routers arises from the limitations of traditional manual methods, where achieving intricate shapes and complex patterns often proved challenging. The automated nature of CNC routers not only enhances productivity but also minimizes human errors, ensuring a consistent and high-quality output. In this comprehensive article, we delve into the multifaceted reasons why a CNC router has become an indispensable tool in various industries and workshops.
Understanding CNC Router
In today’s rapidly evolving manufacturing landscape, where precision and speed are paramount, CNC routers offer a transformative solution. Before we delve into why the manufacturing industry needs a CNC router, let’s get a basic understanding of this powerful tool.
Working principle of CNC router
The working principle of a CNC router involves a combination of computer programming, motors, and precision cutting tools to carry out automated machining processes. Here is a detailed breakdown of how a CNC router works:
The process begins with the creation of a digital model or design using computer-aided design (CAD) software. Once the design is complete, the CAD software generates a toolpath. This toolpath is translated into a language called G-code, which consists of a series of alphanumeric commands that the CNC router can understand. The G-code is then processed by computer-aided manufacturing (CAM) software. CAM software takes the toolpath information and generates the specific commands needed to control the CNC router’s movements. This includes instructions for the X, Y, and Z axes, spindle speed, and tool changes.
Before the CNC router begins its work, the material to be machined is securely placed on the worktable. The appropriate cutting tool or router bit is selected based on the material and the design requirements. The chosen tool is then mounted on the CNC router’s spindle. The CNC router needs to establish a reference point on the material, known as the “zero point” or “home position.” With the material secured and the zero point established, the CNC router is ready to start the machining process. The cutting tool rotates at high speed, and the CNC router moves it precisely along the X, Y, and Z axes according to the programmed instructions. Once the CNC router completes the programmed toolpath, the machining process concludes, leaving behind a finished, precisely machined product.
Key components of CNC router
A CNC router consists of several key components, and understanding them can provide insight into how CNC routers operate and how they achieve precise and automated machining processes across various materials. Here are the key components of a CNC router:
- Controller: The controller is the brain of the CNC router. It interprets the programmed instructions (G-code) and sends signals to the motors to move the machine along specified axes.
- Motors: CNC routers have motors for each axis of movement (X, Y, and Z). These motors receive signals from the controller, driving the movement of the machine to specific positions with precision.
- Drive System: The drive system consists of mechanisms like lead screws, ball screws, or racks and pinions that convert the rotational motion of the motors into linear motion along the axes.
- Spindle: The spindle holds the cutting tool (router bit or end mill). It rotates at high speeds and is responsible for removing material from the workpiece.
- Worktable: The worktable provides a stable surface to secure the material being machined. It may have features like T-slots or vacuum systems for material fixation.
- Coolant System: For materials that generate heat during machining, a coolant system may be employed to dissipate heat and prevent damage to the tool or workpiece.
- Control Panel: The control panel allows operators to input commands, set parameters, and monitor the CNC router’s status. It may include a display, keyboard, and buttons for manual control.
- Emergency Stop Button: A safety feature, the emergency stop button allows for the immediate halting of the CNC router in case of emergencies or unexpected issues.
- CAD/CAM Software: Computer-aided design (CAD) software is used for designing the digital model, while Computer-Aided Manufacturing (CAM) software generates the tool paths and G-code instructions for the CNC router based on the design.
- Auto Tool Changer (optional): In some advanced CNC routers, there is a tool changer mechanism that allows the machine to automatically switch between different cutting tools during a job without manual intervention.
Advantages of CNC router in precision machining
CNC routers offer several advantages in precision machining, making them a preferred choice in various industries. These machines are capable of handling a diverse range of materials, from wood and plastic to metals, allowing for versatility in design and production. Whether in the realms of furniture, cabinetry, signage, or prototyping, the demand for precision and repeatability has fueled the widespread adoption of CNC routers. Here are its key advantages:
- Complex Geometries: CNC routers can easily handle complex shapes, contours, and intricate designs that may be challenging or impossible with traditional machining methods. This capability is valuable in industries requiring intricate components.
- Precision Redefined: At the heart of the CNC router’s allure lies its ability to deliver precision and accuracy that surpasses traditional manual methods. They excel at achieving intricate and precise cuts with minimal tolerance. The accuracy is consistently maintained across multiple repetitions, ensuring high-quality results. Real-world examples showcase how CNC routers excel in tasks demanding intricate designs, fine details, and geometric complexities.
- Versatility in Materials: CNC routers are capable of machining a wide range of materials, including wood, plastic, metal, composites, and foam. This versatility makes them suitable for diverse applications across different industries. From woodworking to metal fabrication, signage production to prototyping, CNC routers play an important role in different fields.
- Increased Efficiency and Saved Time: Automation leads to increased machining speed and efficiency, so CNC routers excel in saving time. CNC routers can work continuously without the need for frequent manual interventions, resulting in faster production times. Efficiency gains are evident in various applications, from rapid prototyping to streamlined production processes.
- Automation Unleashed: CNC routers are controlled by computer programs, allowing for automation of the cutting process. This can significantly increase efficiency and reduce the margin of error compared to manual cutting methods. Industries benefit from reduced human error, increased efficiency, and the ability to handle high-volume production seamlessly. In addition, the automation capabilities of the CNC router mean that the actual operation of the machine is relatively straightforward. This reduces the dependence on highly skilled manual machinists for day-to-day operations.
- Reduced Waste: CNC routers can automatically optimize the layout of parts on a sheet or workpiece. This nesting capability ensures that multiple components are arranged in a way that minimizes material waste, leading to more efficient use of the material. The precision of the cuts ensures that each piece is utilized effectively. This is particularly important for expensive materials or projects with tight budget constraints.
- Easy Use and Programmable: The software used to program CNC routers is often intuitive and user-friendly, enabling users to program the machine without extensive coding knowledge. Programmability allows CNC routers to be versatile in handling various applications. This reduces the training time required for individuals to become proficient in CNC machining compared to traditional manual methods.
- Maintain Product Consistency: CNC routers can reproduce the same design or cut repeatedly, ensuring consistency in mass production. Once a program is created, CNC routers can repeat the same machining process identically, eliminating variations that might occur in manual machining. This is particularly beneficial for maintaining consistent quality and industries where identical parts are needed.
- Enhance Design Freedom and Creativity: In a world that increasingly values personalization, CNC routers offer a platform for creativity and customization. These machines can transform digital designs into tangible, complex shapes. Whether it’s crafting unique furniture pieces, personalized signage, or bespoke prototypes, CNC routers empower individuals and businesses to bring their visions to life. When customization becomes a competitive advantage for enterprises, this feature of CNC routers can bring greater market space to enterprises.
- Adapting to Industry 4.0 Practices: CNC routers can be equipped with sensors and Internet of Things (IoT) devices to collect real-time data on machine performance, tool condition, and material usage. Analyzing this data can provide insights into production trends, identify areas for improvement, and enhance overall manufacturing processes.
Practical application of CNC router
The adaptability of CNC routers makes them a crucial tool in modern manufacturing and design processes. It has applications in a wide range of industries due to its ability to precisely cut, carve, and shape various materials. Here are some practical applications of CNC routers. These are just a few examples, and the versatility of CNC routers allows them to be applied in numerous other industries where precise cutting and shaping of materials are essential.
Furniture Production
The advent of CNC machines has revolutionized the furniture industry in numerous ways. It is an indispensable tool for the production of various wooden furniture such as cabinets, wardrobes, door panels, tables and chairs. From the largest cuts to the most delicate details, CNC routers are more than capable of handling any cutting operation while processing wood and other materials, which enables the rapid production of simple and complex furniture pieces. With the help of a CNC router, the work speed is faster and more efficient, and the solid wood products produced are often of better quality than other methods.
Advertising Industry
For advertisers, creating signage is often their main job. Commonly used materials for making signs are acrylic, wood, MDF, foam or some metals. CNC routers are a staple in the sign-making industry. They can cut letters, logos, and shapes with high precision, allowing for the production of custom signs for businesses, events, and promotional purposes.
Musical Instrument Industry
About 90% of musical instruments are made of wooden materials and require engraving on their material. Engraving is done to ensure the perfect size and shape of the instrument so that it can be better handled by the user. CNC routers are used in these industries to manufacture these musical instruments perfectly.
Crafts Industry
The range of crafts that can be made with a CNC router is almost unlimited, such as photo frames, holiday decorations, plaques, household items, souvenirs, etc. If you want to engrave 3D crafts, then a 4-axis or 5-axis CNC router may be more suitable for your needs. They have the advantage of high processing accuracy and are specially used for processing complex curved surface workpieces.
Stone Carving Industry
CNC routers have been widely adopted in the stone industry within the last decade to cut marble, granite, limestone, and other similar materials. The stone industry uses large and powerful CNC routers to cut stone, and create patterns on stone designs. CNC routers can also engrave stones, and can be used to create gravestones, stone inlays for home decor, fireplaces, and other architectural projects.
Mold Industry
Injection molding is the best way to mass-produce most things. Rather than having to machine every piece, you can save money and scale production by CNC machining the mold, and then using these molds to make parts. CNC routers are mostly used to mill mold cavities that are to be filled for injection molding, mold cores and inserts, finishing mold surfaces for accurate part production, and drilling holes into mold prototypes for things like injector pins, alignment pins, and cooling channels.
In essence, the applications of CNC routers are boundless, providing a powerful and efficient means for material processing across diverse industries. As technology advances, these machines continue to play a pivotal role in shaping the way we design, manufacture, and bring ideas to life.
Challenges and Mitigation Measures in CNC Router Operation
Operating CNC routers comes with its own set of challenges, and it’s important to implement mitigation measures to ensure efficient and safe operation. By addressing these challenges through proper training, maintenance, and proactive measures, CNC router operators can enhance the reliability, accuracy, and safety of machine operations. Here are some common challenges and corresponding mitigation measures in CNC router operation:
Material Variation
- Challenge: Different materials may have variations in hardness or composition, affecting cutting performance.
- Mitigation: Conduct thorough material testing, and adjust feed rates, spindle speeds, and toolpaths accordingly. Maintain a database of optimal settings for different materials.
Tool Wear and Breakage
- Challenge: Tools can wear out or break during extended use, leading to reduced precision and potential damage.
- Mitigation: Regularly inspect and replace worn tools. Implement tool life monitoring systems. Set up proper toolpaths to reduce tool stress.
Programming Errors
- Challenge: Errors in the CNC program can lead to incorrect cuts, wasting material and time.
- Mitigation: Use simulation software to verify programs before running them on the machine. Implement a rigorous testing and validation process for CNC programs.
Dust and Chip Management
- Challenge: Accumulation of dust and chips can affect machine components and compromise precision.
- Mitigation: Use effective dust collection systems to minimize airborne particles. Clean the machine and surrounding area regularly to prevent buildup. Use compressed air to clear chips during operation.
Operator Training and Skill Level
- Challenge: Inadequate operator training can result in suboptimal machine performance and increased risk of accidents.
- Mitigation: Provide comprehensive training for operators on machine operation, programming, and troubleshooting. Regularly update training programs to incorporate new technologies and best practices.
Machine Calibration
- Challenge: Inaccurate machine calibration can lead to dimensional inaccuracies in the finished parts.
- Mitigation: Perform regular machine calibration and maintenance. Use calibration tools to ensure accurate positioning and motion control.
Security and Access Control
- Challenge: Unauthorized access to the CNC machine can lead to safety hazards and potential misuse.
- Mitigation: Implement strict access control measures. Restrict machine access to trained and authorized personnel. Secure the CNC control system with passwords.
Software Updates and Compatibility
- Challenge: Outdated or incompatible software can lead to programming and communication issues.
- Mitigation: Regularly update CNC control software. Ensure compatibility between CAD/CAM software and CNC controllers. Test software updates in a controlled environment before implementation.
Addressing these challenges with appropriate mitigation measures ensures smoother CNC router operations, minimizes downtime, and enhances overall productivity and safety in the manufacturing environment. Regular monitoring and continuous improvement efforts contribute to the efficiency and reliability of CNC router operations.
CNC router safety guide and operator training
In the section on challenges during CNC router operation, we have learned the importance of safety and training. Here, we have compiled general guidelines for CNC router safety and operator training for users. By following the steps below, machine operators can contribute to a safer working environment, reduce the risk of accidents, and increase the overall efficiency of the machining process.
- Read the Manual: Always start by thoroughly reading the manufacturer’s manual for the specific CNC router model you are using. Follow the recommended operating procedures and safety guidelines outlined in the manual.
- Personal Protective Equipment (PPE): Wear appropriate PPE, including safety glasses, hearing protection, dust masks, and any other equipment recommended by the manufacturer, to protect against potential hazards.
- Training: Provide comprehensive training for operators before they use the CNC router. Training should cover machine operation, emergency procedures, and safety protocols. Ensure that only trained and authorized personnel operate the CNC router.
- Work Area Safety: Keep the work area clean and well-organized to avoid tripping hazards. Ensure proper lighting for clear visibility. Mark and secure the boundaries of the machine area.
- Tool Handling and Changing: Train operators on safe tool-handling practices. Regularly inspect and maintain cutting tools to ensure they are sharp and in good condition. Replace worn-out or damaged tools promptly.
- Material Handling: Follow proper procedures for loading and unloading materials onto the CNC router. Secure materials firmly to prevent movement during operation. Use lifting equipment whenever possible when moving heavy or bulky materials.
- Emergency Procedures: Lack of well-defined emergency procedures can lead to delays in addressing issues and potential safety risks. Operators therefore need to be able to identify emergency stop buttons and become familiar with emergency shutdown procedures. Test the emergency stop function regularly. Also, post emergency contact information in a prominent location.
- Machine Calibration and Maintenance: Neglecting regular maintenance can lead to unexpected breakdowns and downtime. Therefore machine calibration is performed regularly to ensure accuracy. Follow a proactive maintenance schedule that regular inspections, lubricating components, and replacing worn parts as needed. Address any issues promptly and, if necessary, consult with the manufacturer for repairs.
- Fire Safety: Prohibit smoking in the machine area. Implement fire safety measures, including the presence of fire extinguishers in the vicinity. Train operators in the proper use of fire extinguishers. Have a clear evacuation plan in case of fire.
Summarize
The indispensability of a CNC router in modern manufacturing is evident, shaping industries with precision, efficiency, and versatility. As we navigate the intricate landscape of manufacturing, the CNC router emerges as a cornerstone, streamlining processes and elevating the quality of end products. From the evolution of CNC technology to the diverse applications in various industries, the CNC router has firmly established itself as an indispensable asset.
AccTek CNC produces CNC routers for different industries, including woodworking CNC routers, stone CNC routers, mold CNC routers, and advertising CNC routers. Different industry applications require different machine configurations. Whether you are purchasing a CNC router for the first time or upgrading an existing machine, you can contact us. Our professional sales team will provide you with complete purchase plans and price information.
Want To get a good machine?
Click the button, our CNC Experts will contact you and send you a solution.