- 12-17 Min Read
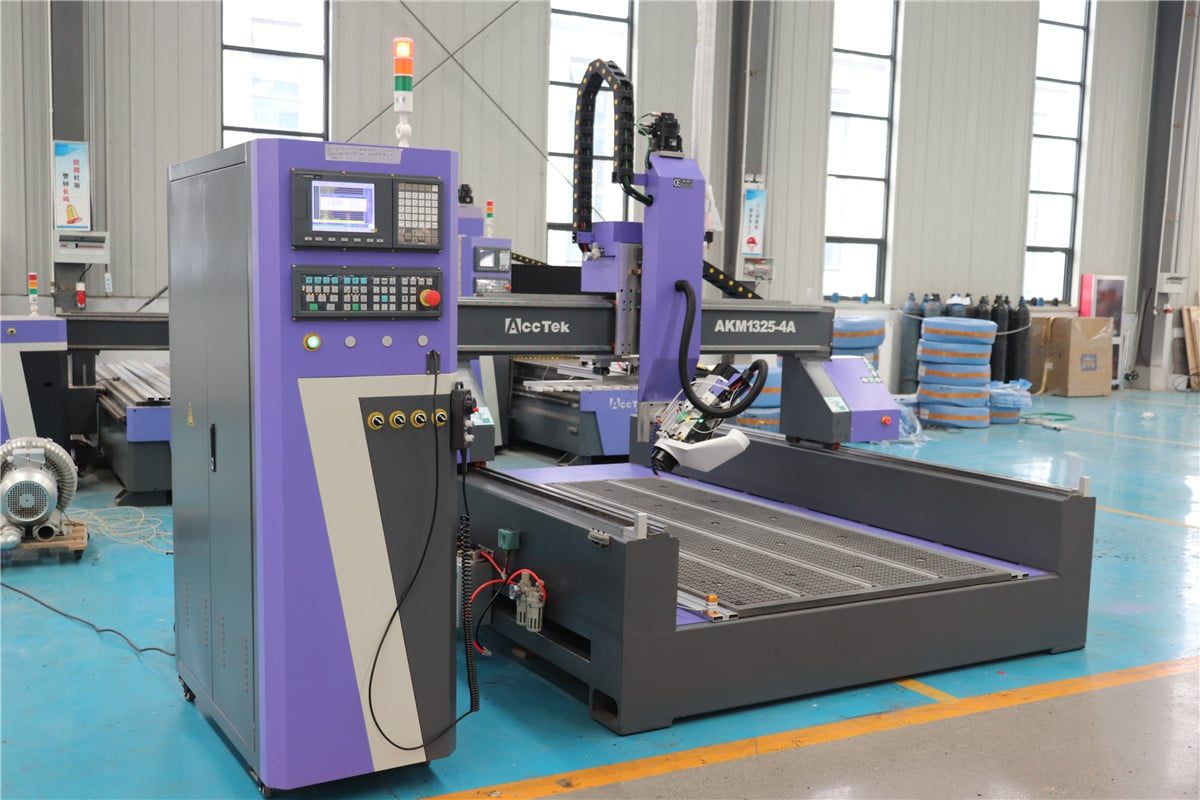
Purchasing a CNC router is a significant investment that can greatly enhance your manufacturing capabilities, whether you’re working in wood, metal, plastics, or composites. However, with the vast range of CNC routers available on the market, it’ s important to know which features and specifications align with your production needs. Understanding factors such as machine size, spindle power, material compatibility, and control systems is beneficial to ensuring that the machine you choose is both efficient and cost-effective. Additionally, evaluating the available support and software integration options can significantly influence your CNC router’s long-term performance.
Before making your purchase, it’ s essential to consider how your CNC router will be used in your production process, as this will determine the level of precision, automation, and scalability you require. The right machine should not only meet your immediate demands but also offer flexibility for future growth. This article will provide an overview of the key considerations that will help you choose the CNC router best suited to your business, from machine configuration and budget planning to manufacturer evaluation and future expandability.
Understanding CNC Router
CNC routers are capable of performing a wide variety of tasks, from basic cutting and engraving to more complex processes like 3D carving and milling. Whether used for small-scale projects or large industrial applications, CNC routers help businesses optimize their manufacturing processes by automating intricate and time-consuming tasks. Here is more information about it.
Basic Knowledge of CNC Routing
CNC routing is a method of cutting, carving, or shaping various materials through the use of a computer-controlled machine. CNC, which stands for Computer Numerical Control, allows for precise automation in the manufacturing process. The machine reads digital instructions from a design file, often a CAD (Computer-Aided Design) file, and uses these commands to control the movement of the cutting tool. This level of precision makes CNC routers ideal for producing detailed and consistent cuts, whether for one-off projects or mass production.
CNC routers are highly versatile and can be used to work with a wide range of materials, including wood, metal, plastic, foam, and composites. The key advantage of CNC routing is the ability to perform complex operations with greater accuracy and speed compared to manual methods. This leads to increased productivity, reduced material waste, and higher-quality finishes.
Types of CNC Routers
CNC routers are classified based on the number of axes along which the cutting tool can move. The more axes a machine has, the greater its flexibility in handling complex designs. Here’ s a breakdown of the main types:
- 3-Axis CNC Router: A 3-axis CNC router operates on three basic axes: the X-axis (left and right), Y-axis (forward and backward), and Z-axis (up and down). This configuration allows the machine to move the cutting tool in three directions, which is ideal for working on flat materials and relatively simple designs. Common applications of 3-axis CNC routers include cutting, engraving, and milling on surfaces like wood, plastics, and metal sheets. While versatile, the 3-axis CNC machine is limited in handling more complex shapes or parts that require access from multiple angles.
- 4-Axis CNC Router: The 4-axis CNC router mentioned here is also called a rotary axis CNC router. It adds a rotational axis, typically referred to as the A-axis, to the standard X, Y, and Z movement. This rotational movement allows the material to rotate while being worked on, enabling the machine to perform more intricate operations, such as carving and shaping cylindrical objects like table legs, statues, or complex patterns on curved surfaces. With the additional axis, a 4-axis CNC router offers better flexibility when machining a workpiece compared to a 3-axis CNC router.
- 5-Axis CNC Router: The 5-axis CNC router is the most advanced and versatile machine, providing full rotational control and movement in five directions. It includes all the movements of a 3-axis CNC router, as well as two additional axes, which allow the cutting tool to approach the material from virtually any angle. This enables the machine to work on complex 3D workpieces with high precision. With a 5-axis CNC router, you can cut intricate details on multiple sides of a workpiece without needing to reposition the material, significantly reducing production time.
Defining Your CNC Router Requirements
When choosing a CNC router, it’ s important to clearly define your specific needs to ensure that the machine you select aligns with your production goals. Here are the key factors to consider when defining your CNC router requirements:
Determining Application Requirements
The first step is to determine what type of work you’ll be performing with the CNC router. Understanding the scope of projects you plan to undertake is beneficial in determining the right CNC router. Ask yourself the following:
- What kind of work will you perform? Are you primarily cutting, engraving, milling, or performing more intricate 3D sculpting tasks?
- Production volume: Are you producing one-off custom pieces, small batches, or running continuous production lines?
- Complexity of designs: Do you need a simple CNC router for flat designs, or will you require advanced multi-axis capabilities for 3D work?
- Industry requirements: Specific industries like woodworking, metalworking, or signage and prototyping may have unique demands for precision, speed, or complexity, which impacts the type of machine required.
By identifying the primary application, you can narrow down CNC routers with the necessary features, such as spindle power, axis configuration (3-axis, 4-axis, 5-axis), and automation options.
Material Compatibility
Different CNC routers are optimized for specific materials, so understanding your material needs will help you choose the right machine. Here’ s how to assess material compatibility:
- Wood: Most CNC routers are capable of working with wood, but softer woods may require less spindle power, while hardwoods demand higher power for precision cutting.
- Metal: Metalworking requires a robust CNC router with high spindle power and rigidity, especially if you’ re cutting harder metals like steel or titanium.
- Plastics and Composites: These materials require CNC routers with appropriate feed rates and cutting speeds to prevent melting or rough finishes.
- Foam and Soft Materials: These require lower spindle power but benefit from high-speed movements for quick processing.
Understanding the material type ensures that the CNC router you choose offers the appropriate cutting tools, power, and precision for consistent performance.
Size and Workspace
The size of the CNC router and its workspace depends on the dimensions of the materials you’ ll be using and the available space in your production facility.
- Worktable size: Determine the largest material size you plan to cut or engrave. This will help you choose a CNC router with a worktable that can accommodate the full dimensions of your material without the need for repositioning.
- Machine footprint: Consider the physical space available in your workshop or factory. Larger CNC routers require more floor space, so measure your available area to ensure the machine fits comfortably, with room for the operator to move and access the machine safely.
- Ventilation and Dust Collection: Make sure your workspace has adequate ventilation, especially when cutting wood or materials that generate dust and debris. CNC routers often need dust collection systems, which also require space.
Matching your CNC router’ s size with your material size and available workspace ensures efficient workflow without disrupting production or crowding your work area.
By carefully assessing your application requirements, material compatibility, workpiece size and workspace, you’ ll be well-prepared to choose a CNC router that aligns with your production needs, providing both efficiency and versatility for long-term use.
Understanding the Performance and Configuration of a CNC Router
Choosing the right CNC router requires a clear understanding of both its performance capabilities and optional configuration. These two aspects play a significant role in how well the machine meets your production needs and how efficiently it operates over time.
Technical Specifications
- Machine Stability and Rigidity: The rigidity of the machine’ s frame and components plays a big role in its performance, especially when cutting hard materials. A well-built CNC router with a strong, stable frame minimizes vibrations during operation, leading to smoother cuts and greater precision. Steel and cast iron offer superior rigidity and durability, making them ideal for heavy-duty cutting operations.
- Spindle Power: The spindle is the heart of the CNC router, and its power (measured in kilowatts or horsepower) directly affects the type of materials you can work with and the speed of your cutting processes. For example, working with hardwood, metal, or composite materials typically requires a high-powered spindle, while softer materials like plastics and foam need lower power. A stronger spindle also increases cutting speed, reducing overall production time.
- Cutting Speed and Feed Rate: Cutting speed refers to how fast the cutting tool moves through the material, while feed rate is the speed at which the material is fed into the tool. High-performance CNC routers allow you to adjust both settings to achieve optimal precision and efficiency for different materials and project types.
- Precision and Accuracy: Precision is a key concern when working on intricate designs, as it affects how closely the final product matches the intended design. Factors like cutting tolerance, repeatability, and resolution (the smallest increment of movement) determine how accurate the CNC router is, making it an important consideration in industries requiring fine detail or tight tolerances.
- Resolution and Positioning Accuracy: Resolution and positioning accuracy determine the machine’ s ability to move the cutting tool to precise locations and make detailed, intricate cuts. These specifications impact the level of detail and quality of the final product. A CNC router with high resolution can perform finer, more detailed work, which is useful for projects requiring intricate designs or tight tolerances.
Software Notes
- CAM Software Compatibility: Ensuring that the CNC router is compatible with widely used CAM software is beneficial for smooth workflow integration. Popular CAM software like Fusion 360, VCarve, or Mastercam must seamlessly integrate with your CNC router, allowing it to interpret design files efficiently. Compatibility with industry-standard formats like G-code is a key factor, as it ensures that the CNC router can process a variety of file types and work across different design environments. Choosing a CNC router with robust CAM software compatibility enables greater flexibility in design and production.
- User Interface and Ease of Programming: A user-friendly interface reduces the learning curve and makes it easier to input design files, adjust machine settings, and control operations. For beginners, CNC routers with simplified, intuitive UIs are ideal, while more advanced users may prefer interfaces with customizable options to fine-tune the machine’ s performance. In addition, ease of programming allows users to set up new jobs without extensive coding knowledge, empowering them to quickly modify or update cutting paths as needed, thus improving workflow efficiency.
- Tool Path Simulation: Tool path simulation allows operators to preview the cutting process before running the machine. By visualizing how the cutting tool will interact with the material, users can identify potential issues and make adjustments to avoid costly mistakes. This feature improves precision and reduces material waste by providing a clear view of the toolpaths in a virtual environment. Additionally, advanced simulations can show estimated cutting times and predict tool wear, further enhancing production planning and efficiency. A CNC router with tool path simulation capabilities ensures higher-quality outcomes and minimizes errors during operation.
Machine Configuration Options
- Automatic Tool Changer (ATC): An auto tool changer (ATC) allows the CNC router to switch between various tools—such as different drill bits or cutting heads—without manual intervention. This significantly reduces downtime and enables the machine to handle complex, multi-step jobs in one continuous operation. ATC ensures smooth workflow and improves overall efficiency, especially in operations that require multiple tool types.
- Dust Removal System: A dust removal system is a critical accessory for CNC routers, especially when cutting materials like wood or composites that produce a significant amount of dust and debris. These systems help maintain a clean work environment by vacuuming up dust directly from the cutting area, ensuring both the machine and workspace stay free of debris. This not only improves operator safety by reducing airborne particles but also prevents dust from accumulating in the machine’ s components, which can extend the lifespan of the router and ensure more consistent cutting performance.
- Coolant System: Coolant systems play an important role in CNC routers that handle materials such as metals, where high-speed cutting generates significant heat. By circulating coolant over the cutting tool and material, these systems help manage heat build-up, preventing tool wear and material damage. Coolant systems can help in extending tool life while maintaining optimal cutting conditions.
By understanding both the performance factors and configuration options of a CNC router, you can choose the right machine that meets your production requirements and ensures a balance of precision, efficiency, and long-term durability.
Evaluating CNC router manufacturers
When purchasing a CNC router, it’ s equally important to carefully evaluate the manufacturer behind the machine. The right manufacturer will not only deliver a high-quality product but also provide long-term support, training, and access to essential parts. Here are the key factors to consider when evaluating CNC router manufacturers:
Customer Support and After-Sales Service
The level of customer support provided by the manufacturer determines whether your CNC router will keep running smoothly in the long term. A responsive, knowledgeable support team can help troubleshoot issues, provide technical guidance, and offer training for your machine. Look for manufacturers that offer comprehensive after-sales services, including machine setup assistance, ongoing maintenance support, and easy access to replacement parts. Good customer support can help users minimize downtime and keep their production running efficiently.
Training and Resources
In addition to customer support, many manufacturers offer training programs to help customers get the most out of their CNC router. Whether through in-person workshops, online tutorials, or comprehensive manuals, the availability of educational resources can significantly reduce the learning curve and ensure that your operators are fully equipped to run the machine efficiently. Manufacturers that invest in user education demonstrate a commitment to customer success and long-term satisfaction.
Reputation and Experience
A manufacturer’ s reputation within the industry is a key indicator of their reliability and product quality. Look for manufacturers with a proven track record of producing durable, high-performance CNC routers. Established companies with years of experience tend to have more refined designs, better quality control, and a solid customer base that can provide feedback. Online reviews, testimonials, and case studies are valuable resources for understanding how the manufacturer’ s machines perform in real-world applications.
Visiting Machine Demonstrations
Evaluating CNC router manufacturers through machine demonstrations is beneficial to understanding how their machines perform in real-world conditions. A live or recorded demo allows you to observe the machine’ s capabilities, such as cutting precision, speed, and ease of use, in action. Pay attention to how well the machine handles different materials, the quality of the final cut, and how quickly it can be set up and operated. A good demonstration should also showcase the software integration and allow you to ask questions about specific needs or applications.
By considering these factors, you’ ll be better equipped to choose a CNC router manufacturer that not only provides a high-quality machine but also supports your business for the long haul.
Additional Considerations
When purchasing a CNC router, several additional considerations can impact your overall experience and the long-term success of your investment. Here are some key factors to keep in mind:
Budget Planning
- Initial Investment: The initial investment for a CNC router varies widely depending on the machine’s size, capabilities, and brand. Basic 3-axis CNC routers designed for smaller projects or hobbyists are more affordable, while industrial CNC routers with multi-axis capabilities and advanced features come with a significantly higher price tag. In addition to the machine cost, consider the expenses for software, installation, tooling, and training.
- Operating Costs: Beyond the initial purchase, operating costs include electricity consumption, maintenance, replacement parts, tooling, and operator wages. Routine maintenance, such as lubrication, tool replacements, and machine calibration, will also add to your ongoing costs. It’s important to calculate these expenses to ensure your production stays cost-efficient over the CNC router’s lifetime.
- Return on Investment (ROI): Return on investment (ROI) is a key metric to assess before purchasing a CNC router. To calculate ROI, factor in the machine’ s production capacity, the cost savings it generates from improved efficiency, and the reduction in labor-intensive processes. High-quality CNC routers typically offer significant productivity gains, reducing material waste and speeding up production cycles.
Environmental Considerations
- Workshop Requirements: Your workshop must meet certain conditions to accommodate a CNC router effectively. Workshop requirements include sufficient space for the machine’s footprint, material handling, and operator access. You’ ll also need to ensure the workspace has adequate power supply capacity for the CNC router, as some machines require high-voltage connections.
- Noise and Dust Management: CNC routers can generate significant noise and dust, especially when working with materials like wood or metal. Proper noise and dust management systems are beneficial for a safe and efficient workspace. Dust extraction systems help keep the machine clean and prevent debris from interfering with precision cutting. In addition, soundproofing measures or operating the machine in a separate area may be necessary to reduce noise pollution.
Regulatory Compliance
- Safety Standards: CNC routers come with inherent risks due to their high-speed cutting and rotating tools. Look for CNC routers that include features like emergency stop buttons, interlock systems, protective shields, and overload protection. Additionally, check whether the machine complies with national and international safety certifications such as CE or UL, ensuring that it meets the necessary safety regulations for operation in your region.
- Environmental Regulations: CNC routers, particularly those used in industrial settings, may require dust collection systems and proper ventilation to manage waste material and ensure environmental safety. Machines that comply with RoHS (Restriction of Hazardous Substances) and other environmental standards demonstrate a commitment to minimizing hazardous materials and pollution.
Future-Proof Your Investment
- Scalability: When purchasing a CNC router, consider its scalability for future growth. As your business expands, you may need to handle larger production volumes or more complex projects. Selecting a machine that allows for growth prevents the need for early upgrades and ensures that it continues to meet your production demands as your business evolves.
- Upgradeability: Opt for machines from manufacturers that offer ongoing software updates and the ability to add new features, such as more advanced control systems, faster spindles, or enhanced cutting tools. This ensures that your machine remains competitive and can take advantage of new technologies without requiring a complete replacement. A CNC router that can adapt to new tools or processes also provides flexibility as your production requirements change.
By considering these additional aspects, you’ ll be better equipped to make a well-rounded decision when purchasing a CNC router. Balancing these factors will help ensure that the machine not only meets your current production needs but also provides long-term value and adaptability for future growth.
Summarize
Buying a CNC router is a significant investment that requires careful planning and consideration of multiple factors. This article discusses the information you need to know before buying a CNC router from multiple aspects, and each aspect plays a role in making the right choice. By taking the time to assess these factors and doing thorough research, you’ll be well-equipped to choose a CNC router that enhances your production efficiency and provides a strong return on investment. If you want to learn more about this, you can check out “Comprehensive CNC Router Buying Guide” and “Reviewing a CNC Router: Key Questions to Ask the Manufacturer”, which will give you more help.
For those seeking a reliable and high-quality CNC router, AccTek CNC is a good choice. As a professional CNC router manufacturer, AccTek offers a range of machines tailored to various needs, from budget-conscious options to advanced CNC routers equipped with powerful features. Additionally, our commitment to customer support and comprehensive training resources ensures that users are fully equipped to operate their machines efficiently. With options for upgradeability and customization, AccTek CNC routers are ideal for businesses looking to invest in long-term production solutions.