- 9-13 Min Read
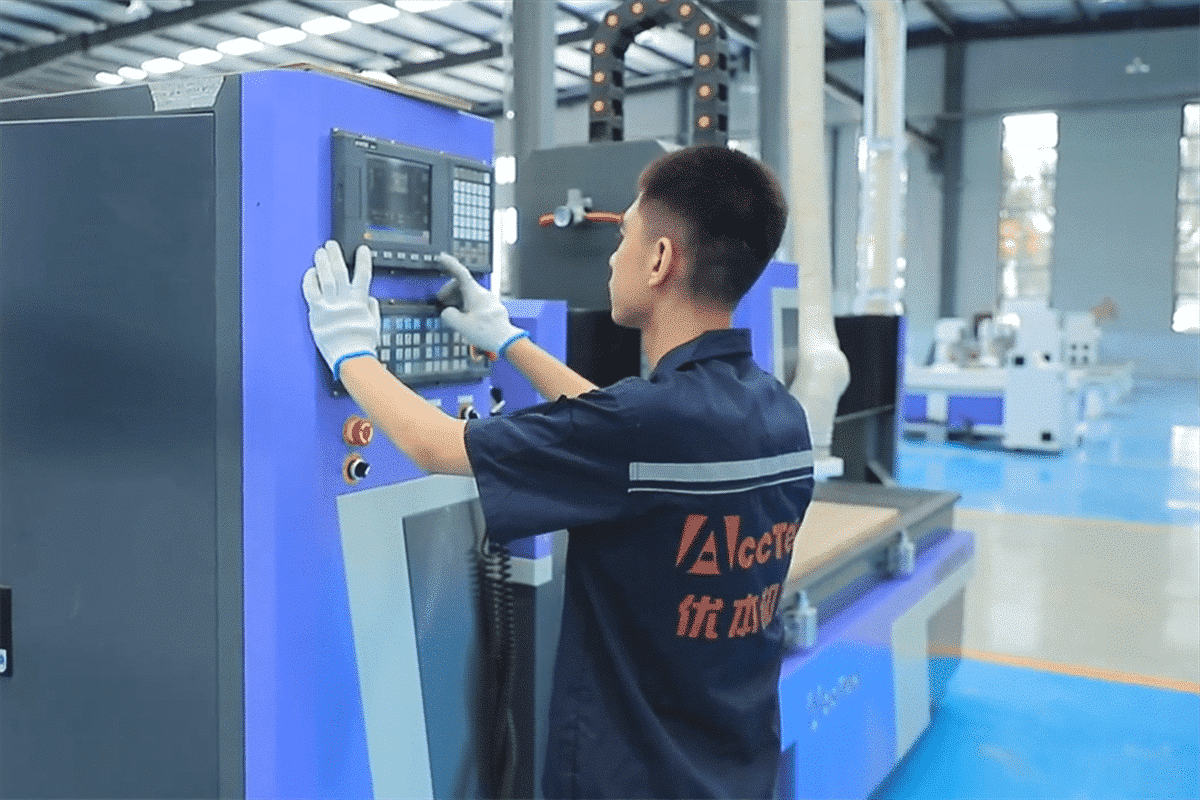
In the ever-evolving landscape of manufacturing and woodworking, Computer Numerical Control (CNC) routers stand as indispensable tools, streamlining production processes and pushing the boundaries of precision. However, alongside their efficiency and versatility, CNC routers present inherent risks that demand meticulous attention to safety protocols and operator proficiency. To ensure safe operation in this complex field, both CNC router operators and experienced professionals must undergo comprehensive training and certification. From foundational safety principles to specialized safety training to CNC router industries, this article delves into the requisite knowledge and skills that empower operators to navigate the intricacies of CNC router operations with confidence and competence. Join us as we delve into the intricacies of safety training in the CNC realm, illuminating pathways toward a safer and more productive future for all involved.
The Importance of Safety Training for CNC Router Operators
From mitigating risks and fostering a culture of safety to enhancing productivity and regulatory compliance, the importance of comprehensive safety training reverberates across every facet of CNC machining. Here are a few key aspects:
- Prevention of Accidents and Injuries: CNC routers involve various moving parts, sharp tools, and high-speed operations, which pose inherent risks to operators. Safety training equips operators with the knowledge and skills to identify potential hazards, assess risks, and implement appropriate safety measures to prevent accidents and injuries.
- Protection of Personnel and Equipment: By understanding safe operating procedures and best practices, operators can protect themselves from harm while also safeguarding the integrity of the machinery. Properly trained operators are less likely to engage in actions that could damage equipment or compromise its performance.
- Compliance with Regulations and Standards: Occupational health and safety regulations require employers to provide adequate training to employees working with machinery like CNC routers. Compliance with these regulations not only ensures legal adherence but also demonstrates a commitment to creating a safe work environment.
- Reduction of Downtime and Costs: Accidents and injuries can result in downtime, decreased productivity, and increased costs for repairs and medical expenses. Safety training helps minimize the risk of incidents, thereby reducing the likelihood of disruptions to production schedules and avoiding associated financial losses.
- Promotion of a Positive Safety Culture: Safety training fosters a culture of safety consciousness within the workplace, where employees prioritize their well-being and that of their colleagues. A positive safety culture encourages open communication, hazard reporting, and collective responsibility for maintaining a safe work environment.
- Enhancement of Operator Confidence and Efficiency: Well-trained operators feel more confident in their abilities to operate CNC routers safely and effectively. This confidence translates into increased efficiency and productivity, as operators are less likely to hesitate or make mistakes due to uncertainty or lack of knowledge.
- Long-term Sustainability and Reputation: Investing in safety training demonstrates a commitment to the long-term sustainability of the business and the well-being of its employees. Additionally, a strong reputation for safety can enhance the company’s standing within the industry and among potential clients and partners.
Basic Safety Training
Basic safety training for CNC routers is designed to equip operators and technicians with the necessary knowledge and skills to operate machines safely and effectively in a manufacturing environment. Here’s an introduction to general safety training in the CNC router industry from three key aspects:
Basic Machine Operation
Understanding CNC Router Control
- Begin by providing an overview of the CNC router control panel, highlighting key components such as the emergency stop button, power switch, spindle controls, and axis movement controls.
- Demonstrate how to power on the CNC router following the correct sequence, ensuring that all safety checks are performed before initiating any operation.
- Train operators on how to navigate the CNC router interface, including loading and executing pre-programmed cutting paths, adjusting cutting parameters, and monitoring machine status.
Emergency Stop Procedures
- Clearly identify the location of the emergency stop button on the CNC router control panel and ensure that all operators know how to access it quickly and instinctively.
- Explain the circumstances under which the emergency stop should be activated, such as in the event of equipment malfunction, tool breakage, or any situation posing a risk to personnel or property.
- Demonstrate the proper procedure for activating the emergency stop, which typically involves pressing the button firmly to immediately stop all machine movements and spindle rotation.
Personal Protective Equipment (PPE)
Selection and Use of PPE
- Introduce various types of PPE that may be required, including safety glasses, hearing protection, gloves, and closed-toe shoes.
- Explain the specific hazards associated with CNC router operation, such as flying debris, noise, and potential contact with rotating parts, and how PPE can mitigate these risks.
- Provide guidance on selecting the right PPE for the task at hand and ensuring proper fit and comfort to encourage consistent use.
- Demonstrate the correct way to don and doff each piece of PPE, ensuring that operators understand how to wear and adjust it properly for maximum effectiveness.
Importance of Protecting Eyes and Ears
- Highlight the vulnerability of the eyes and ears to common hazards in CNC router operations, such as flying chips, dust, and high noise levels.
- Emphasize the importance of wearing safety glasses with side shields to protect against flying debris and particles generated during cutting and machining processes.
- Stress the importance of wearing hearing protection, such as earplugs or earmuffs, in environments where noise levels exceed safe limits, as prolonged exposure to loud noise can lead to hearing loss and other health issues.
Safe Work Practices
Correct Material Handling
- Provide guidelines on how to safely lift and carry materials, emphasizing the use of proper lifting techniques to avoid strains and injuries to the back and muscles.
- Instruct operators on how to inspect materials for defects, warping, or other irregularities before loading them onto the CNC router bed, ensuring that only suitable materials are used for machining.
- Demonstrate the correct procedure for securely fastening materials to the CNC router bed using clamps, screws, or other appropriate methods to prevent movement or shifting during cutting operations.
Housekeeping and Workspace Organization
- Provide guidance on proper housekeeping practices, including regular sweeping, vacuuming, and dusting to remove debris, chips, and other contaminants from the work area and CNC router equipment.
- Encourage operators to promptly clean up spills, leaks, or other potential hazards to prevent slips, trips, and falls.
- Establish procedures for storing tools, materials, and supplies in designated locations when not in use to reduce clutter and minimize the risk of accidents or injuries caused by misplaced items.
- Conduct regular inspections of the workspace to identify and address any potential safety hazards or areas in need of maintenance or improvement.
CNC Router-Specific Safety Training
This section covers safety training matters specifically tailored to the unique characteristics of CNC router machinery. Throughout this training, participants will learn about key safety aspects specific to CNC routers, the specific contents are as follows:
Tooling Safety
Handling Cutting Tools Safely
- Tool inspection: Inspecting cutting tools for damage, wear, and proper sharpness before use to maintain machining quality and operator safety.
- Tool care and maintenance: Cleaning, lubricating, and storing tools properly to extend their lifespan and performance.
Changing and Fixing Tools Safely
- Tool change protocols: Establishing standardized procedures for tool changes, including securing the machine, powering off the spindle, and following manufacturer guidelines for tool change sequences.
- Tool fixture setup: Demonstrating correct methods for fixing tools in collets, toolholders, or automatic tool changers, ensuring secure attachment and proper alignment to minimize runout and tool deflection.
- Verification and testing: Verifying tool changes and performing test runs to ensure tool performance and machining accuracy before resuming production operations.
Workpiece Holding and Fixtures
Safe Clamping Technology
- Clamping methods: Exploring various clamping techniques such as vacuum clamping, mechanical clamps, and fixture plates, and understanding their applications based on material type, size, and geometry.
- Fixture design considerations: Discuss the design principles of effective workholding fixtures, including locating and clamping points, as well as fixture rigidity and stability to withstand cutting forces.
- Clamping force optimization: Providing guidance on determining the appropriate clamping force for different materials and machining operations to prevent over-clamping or under-clamping, which can lead to workpiece distortion or tool breakage.
Reducing the Risk of Material Movement
- Workpiece preparation: Properly preparing workpieces by ensuring flatness, squareness, and uniformity to facilitate secure clamping and reduce the likelihood of material shifting during machining.
- Fixturing techniques: Implementing effective fixturing strategies, such as specialized jigs or fixtures, to immobilize workpieces and prevent unintended movement during cutting operations.
- Machining strategies: Optimizing machining parameters such as cutting speeds, feed rates, and toolpath strategies to minimize vibration, chatter, and material deflection, which can contribute to workpiece movement and machining inaccuracies.
Understanding CNC Programs
Program Verification and Simulation
- Program validation procedures: Demonstrating techniques for verifying CNC programs through careful review of toolpaths, cutting parameters, and machine movements to detect errors or inconsistencies.
- Simulation software utilization: Introducing simulation software tools that allow operators to visualize and simulate CNC toolpaths in a virtual environment, enabling them to identify potential collision points and optimize machining sequences before actual production runs.
- Collision detection and avoidance: Using simulation software to detect and address potential collisions between cutting tools, workpieces, and machine components, thereby minimizing the risk of equipment damage and operator injury.
Interpretation of G Code and M Code
- Basics of G code and M code: Providing an overview of common G code and M code commands used in CNC programming, including their meanings, syntax, and functions.
- Program debugging techniques: Equipping participants with the skills to interpret G code and M code instructions to identify and troubleshoot programming errors or anomalies that may affect machine operation or machining accuracy.
- Safety-related codes: Highlighting specific G code and M code commands related to machine safety functions, such as rapid traverse, feed rate overrides, and spindle control, and their implications for operator safety and equipment integrity.
Emergency Response Training
Comprehensive emergency response training is designed to equip operators and technicians with the knowledge, skills, and protocols necessary to effectively respond to various emergencies that may arise during CNC router operation. The following are specific training projects:
Fire Safety
- Understanding fire hazards: Identifying potential fire hazards in the CNC router environment, such as flammable materials, electrical components, and heat sources.
- Implementing preventive measures: Learning fire prevention techniques, including proper storage of flammable materials, regular equipment maintenance, and adherence to safe operating procedures to minimize fire risks.
- Proper Use of Fire Extinguishers: Familiarize participants with different types of fire extinguishers and their appropriate uses, such as water, CO2, or dry chemical extinguishers. Providing practical training on how to operate fire extinguishers effectively, including the PASS technique (Pull, Aim, Squeeze, Sweep), to extinguish small fires safely.
First Aid and Medical Emergency Response
- Basic First Aid Training: Introducing basic first aid principles and techniques for treating common injuries and medical emergencies that may occur in the workplace, such as cuts, burns, and sprains.
- Emergency Communication Procedures: Establishing clear procedures for reporting emergencies, including designated emergency contact numbers, communication channels, and chain of command. Training participants on how to convey critical information accurately and calmly during emergencies to facilitate prompt response and coordination.
Evacuation Procedures
- Emergency Exit Routes Identification: Identifying primary and secondary emergency exit routes from the CNC router workspace and ensuring they are clearly marked and unobstructed.
- Evacuation Protocols: Providing guidance on evacuating the premises safely during emergencies, including procedures for assisting individuals with disabilities and conducting headcounts at assembly points.
- Evacuation drills: Conducting regular evacuation drills to familiarize personnel with emergency exit routes, assembly points, and evacuation procedures, and to assess the effectiveness of emergency response plans.
Machine-Specific Safety Features
Be Familiar with Safety Devices
- Emergency Stop Buttons: Emergency stop buttons are critical safety devices that allow operators to halt machine operation immediately in case of emergencies or imminent hazards.
- Safety Interlocks Devices: Safety interlocks are designed to prevent access to hazardous areas of the CNC router, such as the cutting area or moving parts, when the machine is in operation.
- Safety Guarding Devices: Physical guards and barriers are installed to shield operators from potential hazards, such as rotating spindles or flying debris, and to prevent accidental contact with moving machine components.
Understand the Limitations of Machine
- Safe Operating Speeds: CNC routers have designated maximum operating speeds for different machining operations and materials, which should be adhered to at all times to prevent overloading the machine and ensure safe operation.
- Load Capacities and Ratings: CNC router tables and tooling systems have specified weight capacities and ratings that dictate the maximum load they can safely support during machining operations. Careful consideration of workpiece weight and placement is required for correct load distribution.
By understanding and implementing these CNC router-specific safety features, operators and technicians can create a safer working environment, reduce the risk of accidents and injuries, and ensure the reliable and efficient operation of CNC routers.
CNC Router Operator Certification
The CNC Router Operator Certification program, designed in alignment with the OSHA 10-hour General Industry Certification, offers a comprehensive training package that combines industry-standard safety practices with specialized CNC router operation skills. This certification equips individuals with the knowledge and expertise necessary to operate CNC routers safely and effectively in compliance with Occupational Safety and Health Administration (OSHA) standards. Key Components of the Certification Program:
OSHA 10-Hour General Industry Certification
- Safety Awareness: Participants learn about workplace hazards, including those specific to the general industry, and how to identify, prevent, and mitigate them to ensure a safe working environment.
- Hazard Recognition: Training covers hazard recognition, assessment, and control methods, empowering participants to recognize potential dangers and take appropriate measures to address them.
- Emergency Response: Essential emergency response procedures are taught, including first aid, fire safety, and evacuation protocols, ensuring individuals are prepared to respond effectively to emergencies in the workplace.
- OSHA Standards: An overview of OSHA standards and regulations relevant to the general industry is provided, ensuring compliance with legal requirements and fostering a culture of safety.
CNC Operator Certification Program
- CNC Router Fundamentals: Participants gain an understanding of CNC router technology, including machine components, controls, and operation principles, setting a foundation for safe and efficient operation.
- Machine Setup and Operation: Hands-on training covers machine setup, tooling selection, material loading, and execution of machining operations, ensuring proficiency in operating CNC routers to produce accurate and high-quality workpieces.
- Toolpath Programming: Training in CNC programming software enables participants to create, edit, and simulate toolpaths for various machining tasks, enhancing productivity and efficiency.
- Safety in CNC Router Operation: Specialized safety training addresses hazards specific to CNC router operation, such as tooling hazards, material handling risks, and emergency stop procedures, ensuring safe working practices are upheld.
- Practical Assessment: Practical evaluations assess participants’ proficiency in CNC router setup, operation, troubleshooting, and adherence to safety protocols, ensuring they meet industry standards and requirements.
By completing the CNC Router Operator Certification program, individuals gain a comprehensive understanding of both general industry safety practices and specialized skills in CNC router operation. This dual certification prepares them to operate CNC routers confidently, efficiently, and safely, contributing to a culture of safety and excellence in the workplace.
Summarize
In a rapidly evolving manufacturing landscape, where CNC routers continue to play a pivotal role in production processes, the importance of safety training for CNC router operators cannot be overstated. These safety pieces of training should encompass a broad range of knowledge and skills essential for ensuring a safe and productive work environment. By investing in robust safety training programs and ensuring adherence to best practices and regulatory standards, organizations can create a work environment where operators can thrive, machinery operates efficiently, and safety remains paramount.
AccTek is a trusted name in the CNC machining industry, renowned for its pursuit of high quality and comprehensive technical support. We believe that success in CNC machining requires more than just the right tools—it requires expertise, guidance, and support every step of the way. Whether you’re a seasoned professional or new to CNC machining, our team is here to provide the knowledge, training, and assistance you need to achieve your goals. Thank you for considering AccTek for your CNC machining needs. We look forward to serving you and helping you unlock the full potential of CNC milling technology.