Unveiling Material Waste in CNC Routing: Strategies for Minimization
- 6-10 Min Read
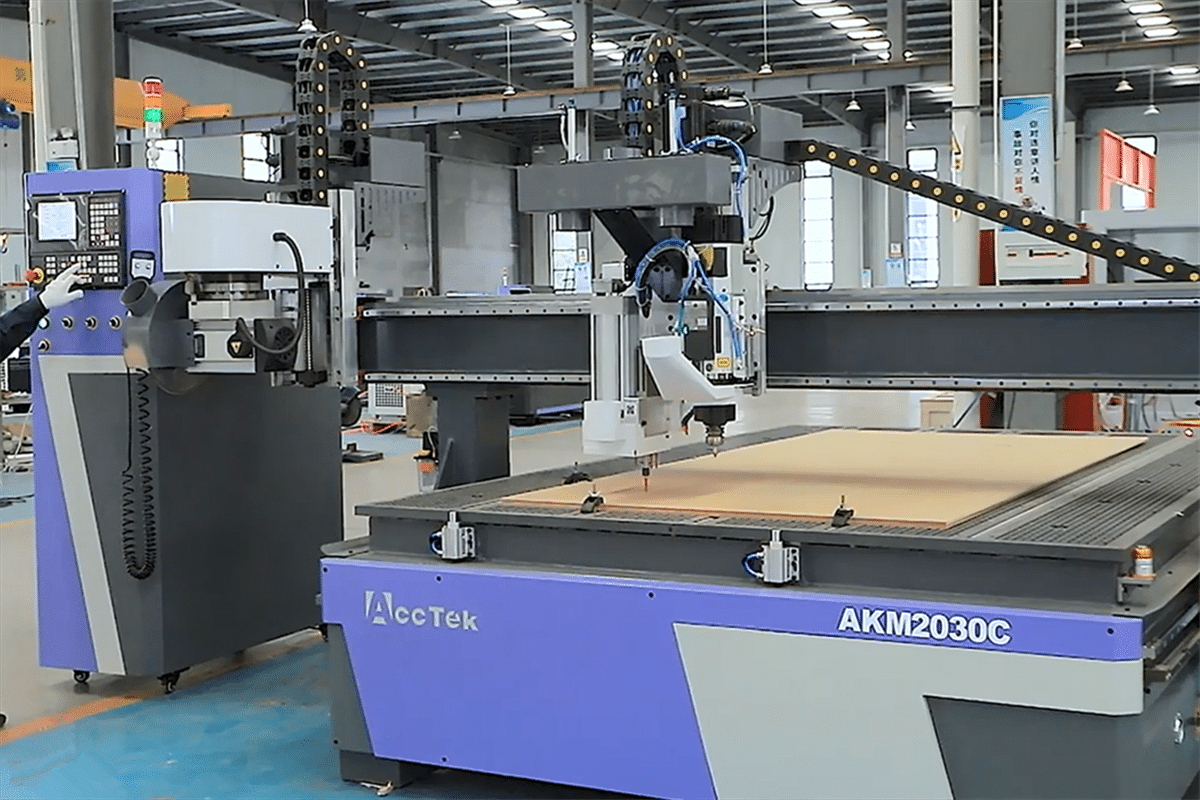
In the world of manufacturing and fabrication, CNC (Computer Numerical Control) routing stands out as a versatile and precise method for cutting, shaping, and engraving a wide range of materials. From woodwork to metal fabrication, CNC routers have revolutionized the way intricate designs are brought to life with efficiency and accuracy. However, amidst the CNC routing lies a significant challenge: material waste. Every cut, every carve, and every meticulous maneuver of the CNC router produces remnants of the raw material, contributing to the growing issue of waste generation.
CNC routing inevitably produces waste material, a byproduct of the cutting and shaping process. Understanding the nature of this waste is beneficial for optimizing production processes, reducing environmental impact, and ultimately cutting costs for businesses. In this article, we delve into the kinds of material waste generated during CNC routing and explore effective strategies for minimizing it. Read on to discover more sustainable and resource-efficient CNC routing methods with us.
The Importance of Reducing Material Waste
The importance of reducing material waste in CNC routing is reflected in its environmental, economic, and operational implications. By addressing waste generation at its source and implementing effective waste reduction strategies, manufacturers can achieve significant benefits in terms of sustainability, cost savings, efficiency, and competitive positioning. Here are several key aspects in which the importance of reducing material waste in CNC routing is demonstrated:
- Environmental Impact: Material waste generated during CNC routing contributes to environmental degradation through resource depletion and pollution. By reducing waste, manufacturers can minimize their ecological footprint, preserve natural resources, and mitigate environmental harm.
- Sustainability: Waste reduction aligns with sustainability goals by promoting responsible resource management and minimizing the carbon footprint of manufacturing operations. Embracing sustainable practices in CNC routing supports long-term viability by ensuring that materials are used efficiently and sustainably.
- Cost Savings: Material waste represents lost resources and money. By optimizing cutting processes, minimizing scrap, and maximizing material utilization, manufacturers can significantly reduce production costs. Waste reduction also leads to enhanced efficiency, streamlined operations, and decreased expenses associated with waste disposal.
- Operational Efficiency: Minimizing material waste improves overall operational efficiency in CNC routing. It reduces downtime associated with material handling, setup, and cleanup, allowing for smoother production processes and increased throughput. Additionally, efficient waste management practices contribute to a safer and more organized work environment.
- Competitive Advantage: Embracing waste reduction practices in CNC routing can provide a competitive edge in the marketplace. Companies that prioritize sustainability and environmental stewardship appeal to environmentally conscious consumers and business partners. Moreover, demonstrating a commitment to reducing waste can enhance brand reputation and attract customers who prioritize sustainability in their purchasing decisions.
Types of Material Waste in CNC Routing
In CNC routing, several types of material waste are generated throughout the machining process. Understanding the various types of material waste in CNC routing is beneficial for implementing effective waste minimization strategies and optimizing production processes. These waste types include:
- Offcuts or Scrap: Offcuts are the leftover pieces of material that are not used in the final product. They result from the initial cutting and shaping of the raw material to create the desired workpiece. Offcuts can vary in size and shape depending on the complexity of the design.
- Dust and Chips: During the cutting and machining process, fine particles of material, as well as larger chips, are produced as a byproduct. This dust and debris accumulate around the work area and on the machine itself. Dust extraction systems are often employed to remove these particles from the air and maintain a clean working environment.
- Edge Trimming: Edge trimming waste occurs when excess material needs to be removed from the edges of the workpiece to achieve the desired dimensions or finish. This waste is generated when the CNC router cuts away material along the edges of the workpiece, resulting in trimmings that are typically discarded.
- Tool Wear Debris: As the cutting tools (such as end mills, router bits, and drills) engage with the material, they gradually wear down over time. This wear produces small metal or composite debris that can mix with the dust and chips generated during machining.
- Water or Coolant Contaminants: In certain CNC routing applications, water or coolant is used to lubricate and cool the cutting tools and workpiece. This coolant can become contaminated with material particles and debris during machining, leading to waste that must be properly disposed of or recycled.
- Fixture and Jig Waste: Fixtures and jigs are often used to hold the workpiece securely in place during CNC routing. Waste may be generated from the fabrication or modification of these fixtures and jigs, particularly when custom fixtures are required for specific machining operations.
Factors Affecting Material Waste
In this section, we will explore the key factors that affect material waste in the CNC routing process. By understanding these factors, manufacturers can implement strategies to minimize waste, improve efficiency, and enhance overall productivity. The following are factors that influence material waste:
- Incorrect Tooling: Using the wrong cutting tools or bits can lead to excessive material removal or poor-quality cuts, resulting in waste. Additionally, the type of cutting tool, such as end mills, ball mills, or specialty tools for specific materials, can affect material removal efficiency and waste generation.
- Tool Wear: Worn-out cutting tools can produce rough cuts or inaccurate dimensions, necessitating the reworking or scrapping of parts, thus contributing to material waste.
- Material Quality: Inconsistent material quality, such as variations in density or hardness, can affect the cutting process, leading to uneven cuts and material waste.
- Material Properties: Different materials have varying characteristics that affect their machinability and the amount of waste produced. For example, brittle materials like ceramics may produce more dust and chipping, while soft materials like plastics may result in stringy chips.
- Nesting Efficiency: How efficiently parts are nested on the material sheet affects waste. Inefficient nesting of parts on the material sheet can lead to unused or unusable material remnants, increasing waste.
- Tool Path Optimization: Inefficient tool paths may result in unnecessary retractions, tool collisions, and increased machining time, leading to higher material waste.
- Design Complexity: The complexity of the design can significantly impact material waste. Intricate designs with numerous cuts, curves, and fine details may result in more offcuts and scrap material compared to simpler designs.
- Improper Feeds and Speeds: Inappropriate feed rates and spindle speeds can cause burning, tearing, or chipping of the material, leading to unusable parts and waste.
- Fixturing and Clamping: Inadequate or improper fixturing and clamping can cause material movement during cutting, resulting in inaccurate cuts or damage to the workpiece, leading to waste.
- Operator Error: Mistakes made by operators, such as incorrect setup, programming errors, or improper machine operation, can result in wasted material.
Strategies to Reduce Material Waste
In this section, we delve into the strategies aimed at reducing material waste in CNC routing operations. From meticulous design considerations to advanced toolpath optimization techniques and sustainable material choices, we explore the multifaceted approaches that manufacturers can adopt to enhance productivity, minimize waste, and embrace sustainability in CNC routing. The following is a detailed introduction to specific plans:
Efficient Design and Programming
- CAD/CAM Optimization: The utilization of advanced CAD/CAM software empowers manufacturers to streamline the CNC routing process. CAD software enables designers to craft intricate designs while optimizing material usage. By prioritizing designs that minimize scrap and offcuts, manufacturers can significantly reduce waste from the outset.
- Consider Material Characteristics: Understand the characteristics of the material being used, including its grain structure and directional properties. Certain materials exhibit directional properties due to their grain structure or composition. By aligning cutting paths with the material’s grain direction, operators can achieve cleaner cuts with reduced resistance, resulting in less waste. Factor these considerations into the design process to maximize material efficiency.
Use of Nested Software
- Automatic Nesting Algorithms: Leverage automatic nesting algorithms to optimize the arrangement of parts on material sheets automatically. These algorithms analyze part geometries and material constraints to maximize material utilization, minimizing scrap and offcuts.
- Manual Nesting Techniques: In situations where automatic nesting algorithms may not produce the desired results due to complex part geometries or material constraints, utilize manual nesting techniques to manually adjust the nesting layout. This allows for optimization of material utilization and waste reduction in special cases. Employ manual nesting techniques to have greater flexibility and control over the arrangement of parts on material sheets.
Material Selection
- Maximizing Sheet Utilization: Selecting plate sizes that align closely with part dimensions minimizes waste by reducing the need for extensive trimming or cutting. By optimizing sheet sizes, manufacturers can effectively utilize material and minimize scrap.
- Inventory Management: Implementing inventory optimization techniques ensures that material stocks are maintained at optimal levels. By accurately forecasting material requirements and strategically managing inventory, manufacturers can reduce excess material and minimize waste associated with overstocking.
- Integration of Recycled Materials: Embracing recycled materials in CNC routing operations offers a sustainable solution to reduce waste and minimize environmental impact. Incorporating recycled materials into the manufacturing process not only conserves natural resources but also reduces energy consumption and greenhouse gas emissions.
- Promoting Recyclability: Selecting materials that are recyclable or have a high potential for reuse promotes circularity in the manufacturing process. By prioritizing recyclable materials, manufacturers contribute to the creation of a closed-loop system where materials are continuously repurposed, minimizing waste generation.
Tool Path Optimization
- Contour Optimization: Contouring strategies focus on minimizing tool retractions and rapid movements between cutting paths. This ensures smooth, uninterrupted cutting motion, minimizing unnecessary stops and starts that contribute to material waste.
- Cavity Strategies: When creating cavities or pockets in CNC routing, efficient pocketing techniques are employed to minimize non-cutting motion. This involves strategic toolpath planning to reduce dwell time and optimize chip evacuation, maximizing material utilization and minimizing waste.
- Adaptive Clearing Algorithms: Adaptive clearing algorithms dynamically adjust toolpath parameters based on part geometry and material properties. By intelligently removing material in successive layers, adaptive clearing minimizes non-cutting motion and optimizes cutting efficiency, reducing waste and enhancing productivity.
Summarize
The exploration of material waste in CNC routing has shed light on significant inefficiencies within manufacturing processes. By identifying various sources of waste, from design flaws to machining errors, manufacturers can implement targeted strategies to minimize waste and optimize resource utilization. By integrating technological advancements, adopting sustainable practices, and fostering a culture of waste minimization, manufacturers can mitigate the environmental impact and enhance the efficiency and cost-effectiveness of the CNC routing process.
If you are planning to improve your production efficiency through CNC router, AccTek CNC is a very good choice. We specialize in manufacturing 3-axis, 4-axis, and 5-axis CNC routers to meet different production needs. With a commitment to high precision and efficiency, AccTek CNC offers a comprehensive range of production solutions tailored to elevate your manufacturing capabilities. Whether you’re in the woodworking industry, sign-making, or model processing, our CNC routers are designed to deliver exceptional performance and reliability, empowering you to achieve your production goals with ease. Join the ranks of satisfied customers who have revolutionized their workflow with AccTek CNC’s advanced machining solutions.