- 12-17 Min Read
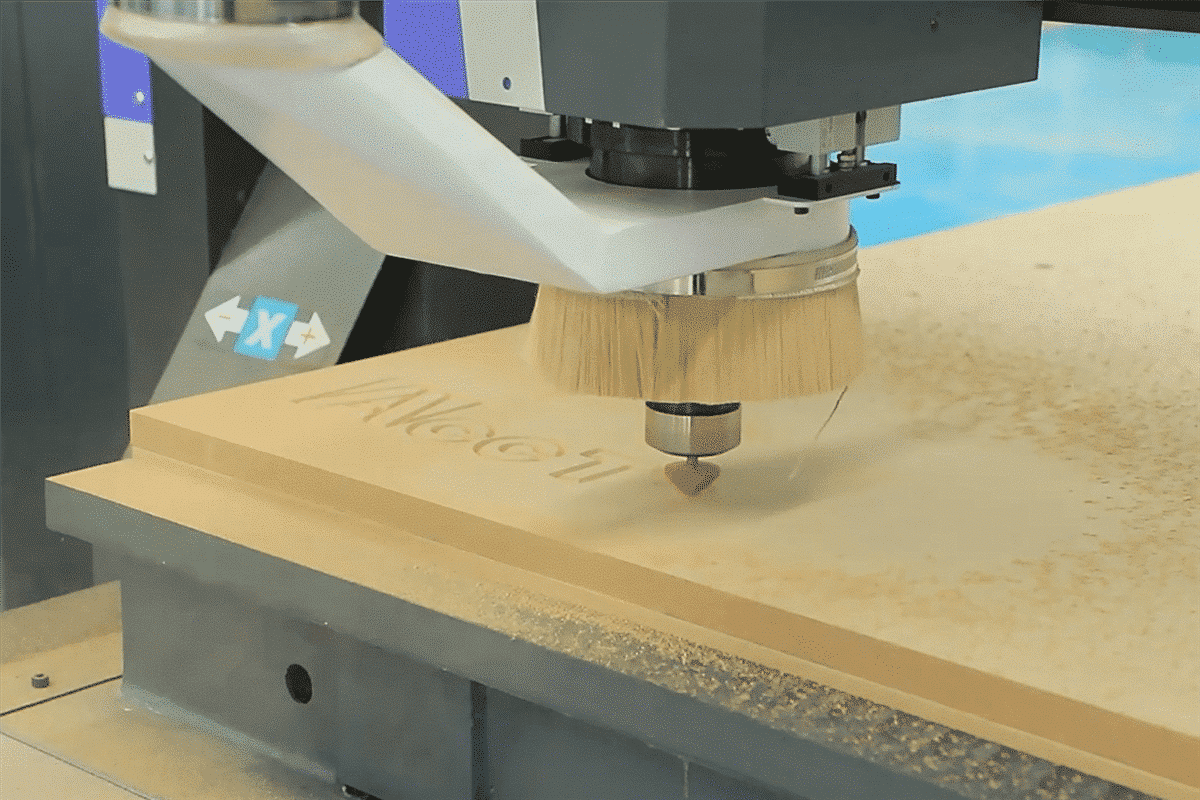
The spindle speed is one of the most critical parameters in CNC router performance, directly influencing the quality, precision, and efficiency of machining tasks. Whether you’re engraving intricate patterns, cutting robust materials, or shaping components, the spindle speed determines how the tool interacts with the material. The ability to adjust spindle speed allows operators to tailor the CNC router’s performance to specific materials, tools, and cutting requirements, ensuring both precision and efficiency.
In this article, we’ll delve into the concept of spindle speed range, explore the factors that influence it, and discuss its effects on cutting quality, materials, and tools. By understanding these aspects, you’ll gain insights into how spindle speed can enhance your machining processes and help you achieve superior results in a variety of applications. Whether you’re working with wood, plastic, or metal, mastering spindle speed settings can help maximize the potential of your CNC router for your manufacturing or fabrication projects.
Importance of spindle speed in CNC routing
Spindle speed refers to the rotational speed of the spindle in a CNC router, typically measured in revolutions per minute (RPM). It indicates how fast the cutting tool or bit attached to the spindle rotates during operation. The spindle speed is a critical parameter that influences the cutting performance, surface finish, and efficiency of the machining process. Adjusting the spindle speed allows operators to optimize the interaction between the tool and the material, ensuring effective material removal while minimizing wear on the cutting tools. Here are the key reasons why spindle speed is important in CNC routing:
- Cutting Quality: The spindle speed determines how the cutting tool interacts with the material. A suitable speed ensures clean cuts, smooth edges, and minimal defects, while improper speeds can lead to rough finishes, chipping, or burn marks.
- Material Compatibility: Different materials, such as wood, plastic, and metals, have varying requirements for spindle speed. Adjusting the speed to suit the material prevents issues like overheating, melting, or cracking, ensuring precise and safe machining.
- Tool Longevity: Running a cutting tool at the correct spindle speed minimizes wear and tear, extending its lifespan. Excessively high or low speeds can cause tool damage, reducing productivity and increasing operational costs.
- Machining Efficiency: Optimized spindle speed improves material removal rates and reduces machining time. This not only enhances productivity but also ensures energy-efficient operations.
- Heat Management: Incorrect spindle speeds can generate excessive heat, leading to material deformation, tool damage, or fire hazards. Proper speed settings help control heat production and maintain a safe working environment.
- Versatility: A wide spindle speed range allows CNC routers to handle diverse applications, from fine engraving to heavy-duty cutting. This adaptability makes the machine suitable for various industries and projects.
Spindle speed is a fundamental aspect of CNC routing that directly affects the efficiency, precision, and overall quality of machining operations. Proper control of spindle speed enables operators to achieve optimal performance for various materials, tools, and cutting processes.
Understanding the spindle speed range
Spindle Speed Range Definition
The spindle speed range refers to the spectrum of rotational speeds that a CNC router’s spindle can achieve. It defines the minimum and maximum speeds at which the spindle can operate, allowing for adaptability to various cutting and machining tasks. A broader spindle speed range enables the CNC router to handle a wide variety of materials, from soft woods to hard metals, and to accommodate different cutting tools and techniques for optimal performance.
Relationship to RPM (Revolutions Per Minute)
The spindle speed range and RPM are interconnected aspects of CNC router operation. Here’s how they relate:
- Definition and Context: Spindle speed range indicates the minimum and maximum speeds the spindle can achieve (e.g., 3,000–24,000 RPM). It defines the operational flexibility of the CNC router. RPM is a specific value within the spindle speed range, chosen for a particular machining task.
- Dependency: RPM is always a subset of the spindle speed range. For example, if the machine’s speed range is 5,000–30,000 RPM, any selected RPM for operation must fall within this range. The spindle speed range sets the boundaries, while RPM is the precise operating speed tailored to the material, tool, and application.
Machines with a broader spindle speed range offer more RPM options, providing better adaptability for diverse applications. Understanding the relationship helps operators fine-tune their CNC router for maximum performance and quality.
Variable Speed Spindle System
A variable speed spindle system is a key feature of modern CNC routers, allowing operators to adjust the spindle’s rotational speed across a defined range to suit specific machining tasks. Here are the key features of variable speed spindle systems:
- Adjustability: Operators can set the RPM to the exact value needed for a task, improving the precision and outcome of the machining process.
- Efficiency: Variable speed systems allow the spindle to operate at optimal speeds, reducing energy consumption and prolonging machine life.
- Material Versatility: They accommodate a wide range of materials, from soft plastics to hard metals, by providing the correct speed for each type.
- Tool Compatibility: Different cutting tools require specific RPMs for effective performance. The variable speed system ensures the correct settings for each tool.
Unlike fixed-speed systems, variable speed spindles provide flexibility by enabling precise control over RPM, ensuring compatibility with diverse materials and cutting tools. This adaptability enhances cutting quality, reduces tool wear, and optimizes efficiency.
Factors Affecting Spindle Speed
The spindle speed of a CNC router is affected by a variety of factors. Understanding them can help determine the optimal RPM for a specific task. Here are the main factors that affect spindle speed:
Material Type
The properties of the material being machined are among the most important considerations for determining spindle speed.
- Soft Materials (e.g., Wood, Plastics): These materials typically require higher spindle speeds to achieve clean and efficient cuts. The higher RPM prevents chipping or tearing by enabling the cutting tool to interact smoothly with the material.
- Hard Materials (e.g., Metals): Harder materials like steel or titanium demand lower spindle speeds to reduce heat generation, tool wear, and the risk of damage to the workpiece.
- Heat-Sensitive Materials: Materials like acrylic or certain plastics are prone to melting under excessive heat. Controlling spindle speed is beneficial to minimizing friction and maintaining the material’s integrity.
- Material Density and Grain: Dense materials or those with irregular grain patterns (like hardwood) require slower spindle speeds to prevent tool deflection or poor cutting results.
Cutting Tool Specifications
The design and material of the cutting tool significantly influence the ideal spindle speed.
- Tool Diameter: Larger tools require lower spindle speeds because their greater circumference results in higher linear cutting speeds at the same RPM, which can lead to overheating or excessive wear. Smaller tools can operate at higher spindle speeds for precise cuts.
- Tool Material: Tools made from high-speed steel (HSS) or carbide are more resistant to heat and wear, allowing them to perform effectively at higher spindle speeds. In contrast, less durable materials may require lower speeds to prevent damage.
- Tool Geometry: The shape and cutting edges of the tool affect its ability to interact with the material. Tools with sharper edges may allow higher speeds, whereas those designed for heavy-duty applications require slower RPMs.
- Tool Coatings: Coatings such as titanium nitride enhance heat resistance and reduce friction, enabling the use of higher spindle speeds without compromising tool life.
Machining Operations
The nature of the machining operation also dictates the spindle speed requirements.
- Engraving: Fine and precise operations like engraving require higher spindle speeds to ensure smooth and detailed results.
- Cutting and Profiling: General cutting operations benefit from moderate spindle speeds, balancing cutting efficiency with material-specific considerations.
- Drilling: Drilling often requires slower spindle speeds, particularly for hard or thick materials, to ensure consistent performance and avoid tool breakage.
- Roughing vs. Finishing: Roughing operations, which involve removing large amounts of material, generally use slower speeds to handle higher loads. Finishing tasks, focused on surface quality, often use higher speeds for a polished result.
CNC Router Specifications
The capabilities and design of the CNC router itself play a key role in determining the available spindle speeds.
- Spindle Speed Range: The machine’s speed range (e.g., 5,000–24,000 RPM) sets the boundaries for speed adjustments. Machines with a wider range offer greater flexibility for diverse tasks.
- Spindle Motor Power: Higher power motors can maintain consistent performance at higher spindle speeds, particularly when working with dense or hard materials. Machines with lower power may struggle at higher RPMs, leading to inconsistent results.
- Control Systems: Advanced CNC routers often feature programmable control systems that allow precise adjustments to spindle speed, enabling optimization for specific materials and operations.
- Machine Rigidity and Stability: High spindle speeds can introduce vibrations. Machines with robust frames and stable designs can accommodate higher speeds more effectively without compromising precision.
- Cooling Systems: Machines equipped with efficient cooling systems allow higher spindle speeds by mitigating the heat generated during machining.
Material type, cutting tool specifications, machining operations, and CNC router specifications are interrelated factors that collectively influence the optimal spindle speed for any CNC routing task. By tailoring spindle speed to these factors, CNC routers can be leveraged to their full potential for a wide range of applications.
The Influence of Spindle Speed on Cutting Quality
Spindle speed is a crucial factor that significantly affects cutting quality in CNC routing, particularly in terms of surface finish, edge quality, and precision and accuracy. Below is a detailed analysis of how spindle speed impacts cutting quality:
Surface Finish
The spindle speed determines the tool’s interaction with the material surface, impacting the smoothness and uniformity of the cut.
- Optimal Speed: When the spindle speed is correctly matched to the material and tool, it results in smooth, clean surfaces. The tool engages the material consistently, reducing vibrations and imperfections.
- Too High Speed: Excessive spindle speed can lead to overheating, causing burn marks on wood, melting of plastics, or poor finishes on metals. It may also generate chatter marks or leave rough edges.
- Too Low Speed: Insufficient speed can lead to tearing, dragging, or gouging of the material instead of cleanly cutting it. This is particularly evident in soft materials like foam or plywood, where low speeds create rough, fibrous surfaces.
Edge Quality
Edge quality depends on how cleanly the cutting tool separates the material during machining.
- Optimal Speed: Appropriate spindle speed ensures that the cutting tool cleanly shears the material, producing sharp and accurate edges without distortions or burrs.
- Too High Speed: Excessive speeds can cause excessive vibration or tool instability, leading to imprecise cuts or rounded edges, especially in detailed work.
- Too Low Speed: Under-speeding can result in incomplete material removal, causing edges to appear chipped or uneven.
Precision
Precision refers to the tool’s ability to follow the programmed toolpath without deviations.
- Optimal Speed: A well-calibrated spindle speed reduces vibrations and enhances the machine’s stability. This allows for precise tool movement, maintaining the correct dimensions and tolerances.
- Too High Speed: High speeds can amplify vibrations, especially in less rigid CNC setups, leading to uneven cuts and reduced dimensional accuracy.
- Too Low Speed: Lower speeds might compromise the tool’s cutting ability, causing unstable operations and inferior results.
Accuracy
Accuracy relates to how closely the cut matches the intended design specifications.
- Optimal Speed: The correct spindle speed ensures that the cutting tool operates efficiently and precisely, yielding results that match design specifications.
- Too High Speed: Excessive speed accelerates tool wear, reducing its sharpness and negatively impacting cutting quality.
- Too Low Speed: At low speeds, the cutting process may lack sufficient force to maintain consistent engagement with the material, leading to deviations.
Spindle speed is a critical factor in achieving excellent cutting quality. Properly adjusting the spindle speed based on the material, tool, and operation ensures clean, precise, and high-quality cuts while minimizing tool wear and material defects. An optimized spindle speed not only enhances machining outcomes but also contributes to the overall efficiency and reliability of the CNC router.
Effect of Spindle Speed on Different Materials
Spindle speed has a significant influence on the performance and quality of CNC machining for different materials. Each material type has specific requirements for spindle speed to ensure optimal cutting quality, tool longevity, and efficient machining. Below is a detailed explanation of how spindle speed affects various materials:
Wood
Wood types, categorized by density, grain structure, and hardness, require specific spindle speeds for optimal cutting results. Below are the general guidelines for spindle speed settings based on wood types:
- Softwoods (e.g., Pine, Cedar, Fir): Softwoods are less dense and cut easily. Higher speeds allow for smooth cuts without tearing the fibers or chipping the material. The optimal spindle speed is 18,000–24,000 RPM.
- Medium-Density Hardwoods (e.g., Cherry, Walnut, Birch): Medium-density woods strike a balance between hardness and workability, requiring moderate spindle speeds to maintain control and cut quality. The optimal spindle speed is 14,000–20,000 RPM.
- Hardwoods (e.g., Oak, Maple, Mahogany): Hardwoods are dense and require slower spindle speeds to avoid overheating, tool dulling, and burn marks. The optimal spindle speed is 12,000–18,000 RPM.
- Exotic Woods (e.g., Teak, Ebony, Rosewood): These woods are extremely dense and often contain natural oils, requiring lower speeds to maintain material integrity and prevent smudging or scorching. The optimal spindle speed is 10,000–15,000 RPM.
- Engineered Woods (e.g., Plywood, MDF, Particleboard): Engineered woods are less prone to grain tearing but may contain adhesives that heat up quickly. Moderate to high speeds ensure clean cuts without burning. The optimal spindle speed is 16,000–22,000 RPM.
Spindle speed significantly influences the surface finish and material integrity of wood during CNC routing. Optimal spindle speeds ensure clean, smooth surfaces by enabling the cutting tool to shear the wood fibers accurately. In terms of material integrity, the correct spindle speed helps preserve the natural structure of the wood, avoiding issues like splitting, cracking, or grain distortion. Balancing spindle speed is beneficial for achieving superior results while maintaining the wood’s structural integrity.
Metal
The optimal spindle speed for machining metals depends on the material’s hardness, thermal conductivity, and machinability. Below are general guidelines for commonly machined metals:
- Aluminum: Aluminum is a relatively soft metal with high thermal conductivity, allowing for moderate to high spindle speeds. Higher speeds facilitate fast material removal and smooth finishes. The optimal spindle speed is 10,000–15,000 RPM.
- Steel: Steel is harder and more heat-resistant than aluminum, requiring slower spindle speeds to maintain tool life and avoid overheating. The optimal spindle speed is 3,000–7,000 RPM.
- Brass/Copper: Brass and copper are soft and highly machinable metals that tolerate higher spindle speeds. These speeds produce smooth finishes with minimal tool wear. The optimal spindle speed is 8,000–12,000 RPM.
- Titanium: Titanium is a hard, heat-resistant metal that requires slow spindle speeds to minimize heat generation and tool wear. The optimal spindle speed is 2,000–4,000 RPM.
Spindle speed significantly affects chip formation and heat generation during metal cutting. At optimal spindle speeds, chips are formed cleanly and efficiently, removing material while maintaining a stable cutting environment. Proper chip formation ensures better cooling and minimizes heat accumulation at the cutting edge. Maintaining the right spindle speed balances effective chip formation and heat management, ensuring a smoother cutting process and extending tool life.
Plastic
Plastics, being heat-sensitive and varying widely in hardness and brittleness, require specific spindle speeds for optimal machining. Below are recommended spindle speeds for common plastic types:
- Acrylic (PMMA): Acrylic is brittle and prone to cracking. Moderate speeds ensure clean edges without causing chips or fractures. The optimal spindle speed is 12,000–18,000 RPM.
- Polycarbonate (PC): Polycarbonate is tough but heat-sensitive, requiring controlled speeds to prevent melting or deformation. The optimal spindle speed is 10,000–15,000 RPM.
- Polyethylene (PE): Polyethylene is soft and highly machinable, tolerating higher speeds for smooth, clean cuts. The optimal spindle speed is 15,000–20,000 RPM
- Polyvinyl Chloride (PVC): PVC is rigid and can handle moderate speeds for clean edges without chipping. The optimal spindle speed is 10,000–16,000 RPM.
When cutting plastics, the spindle speed needs to be controlled to avoid melting and deformation of the material. Optimal spindle speeds allow the cutting tool to interact with the plastic efficiently, removing material without generating excessive friction or heat. Moreover, proper spindle speed must be combined with sharp tools, moderate feed rates, and cooling systems to dissipate heat effectively, ensuring clean, precise cuts and preserving the plastic’s dimensional integrity.
Composites
Composites, which combine fibers and resins, require careful consideration of spindle speed during machining to balance cutting efficiency, tool wear, and material integrity. Here’s a comprehensive guide:
- Carbon Fiber Reinforced Plastics (CFRP): Carbon fibers are abrasive, and the resins are heat-sensitive. Moderate to high speeds ensure clean cuts without delaminating the layers. The optimal spindle speed is 10,000–20,000 RPM.
- Fiberglass Reinforced Plastics (FRP): Fiberglass is highly abrasive and requires slower speeds to reduce tool wear and avoid fiber pull-out. The optimal spindle speed is 8,000–15,000 RPM.
- Thermoplastic Composites: These composites combine fibers with thermoplastic resins, which are prone to melting. Controlled speeds avoid heat buildup while providing clean edges. The optimal spindle speed is 10,000–18,000 RPM.
- Metal Matrix Composites (MMC): MMCs are highly abrasive due to the metal content, requiring slower speeds to minimize tool wear and maintain machining precision. The optimal spindle speed is 4,000–8,000 RPM.
Spindle speed is key in balancing cutting efficiency and fine processing when machining composite materials, as it directly affects material removal, surface quality, and structural integrity. Achieving the optimal spindle speed ensures precise cuts with minimal defects while maintaining productivity. This balance is further optimized by using sharp tools, appropriate feed rates, and effective cooling systems, allowing for both efficient machining and superior surface quality in composite materials.
Different materials require tailored spindle speeds to achieve optimal cutting quality and efficiency. By understanding the unique requirements of each material, operators can select the right spindle speed to ensure precise and effective machining.
The Influence of Spindle Speed on Cutting Tools
Spindle speed significantly affects the performance, lifespan, and effectiveness of cutting tools during machining operations. Proper spindle speed ensures efficient cutting, minimal tool wear, and high-quality results, while incorrect settings can lead to tool damage and reduced productivity.
Tool Wear and Lifespan
- High Spindle Speeds: Excessively high speeds generate more friction and heat at the cutting edge, accelerating wear, dulling the tool, and potentially causing thermal damage.
- Low Spindle Speeds: Speeds that are too low can increase the cutting force required, causing mechanical stress on the tool and contributing to uneven wear or chipping.
Cutting Edge Performance
- Optimal Speed: Allows the cutting edge to engage the material smoothly, reducing impact forces and ensuring clean, precise cuts. This maintains the sharpness of the tool and minimizes regrinding needs.
- Improper Speed: Too high or too low speeds can lead to edge deformation or micro-fractures, especially in brittle tool materials like ceramics or carbide.
Heat Generation and Thermal Effects
- High Spindle Speeds: Generate significant heat at the tool-material interface, potentially causing tool coatings to degrade, leading to increased friction and further wear. Prolonged overheating may also cause plastic deformation in the cutting tool.
- Low Spindle Speeds: While reducing heat, excessively low speeds can lead to prolonged contact time between the tool and material, resulting in heat accumulation and uneven tool wear.
Tool Breakage
- High Spindle Speeds: Combined with aggressive feed rates, high speeds can cause rapid tool breakage, especially in hard or brittle materials like metals or composites.
- Low Spindle Speeds: Higher forces required to cut materials at low speeds can result in tool deflection or breakage, particularly in thin or fragile tools.
Spindle speed directly influences cutting tool wear, performance, and lifespan. Properly matching the speed to the material, tool type, and machining operation minimizes wear and heat buildup, ensuring efficient, precise cuts and prolonging tool life.
Summarize
The spindle speed range of a CNC router is a critical factor that defines its versatility and performance across a variety of materials and machining tasks. By understanding the spindle speed range and its influence on cutting quality, tool life, and material compatibility, operators can optimize their CNC router to achieve precise, efficient, and high-quality results. Factors such as material type, tool specifications, and the nature of machining operations must all be considered to select the ideal spindle speed. To learn more about spindles, you can read “Exploring Cooling Mechanisms in Spindles: Impact on Performance” and “The Impact of Spindle Power on CNC Router Functionality”.
AccTek CNC, a well-known CNC router manufacturer in China, is an ideal choice for businesses and professionals seeking high-quality and versatile CNC routers. Whether you’re cutting wood, plastics, metals, or composites, AccTek CNC routers deliver precise, efficient, and consistent performance by allowing operators to optimize spindle speed for superior cutting quality and tool longevity. Consult online and get your own exclusive CNC router customization solution.