- 12-17 Min Read
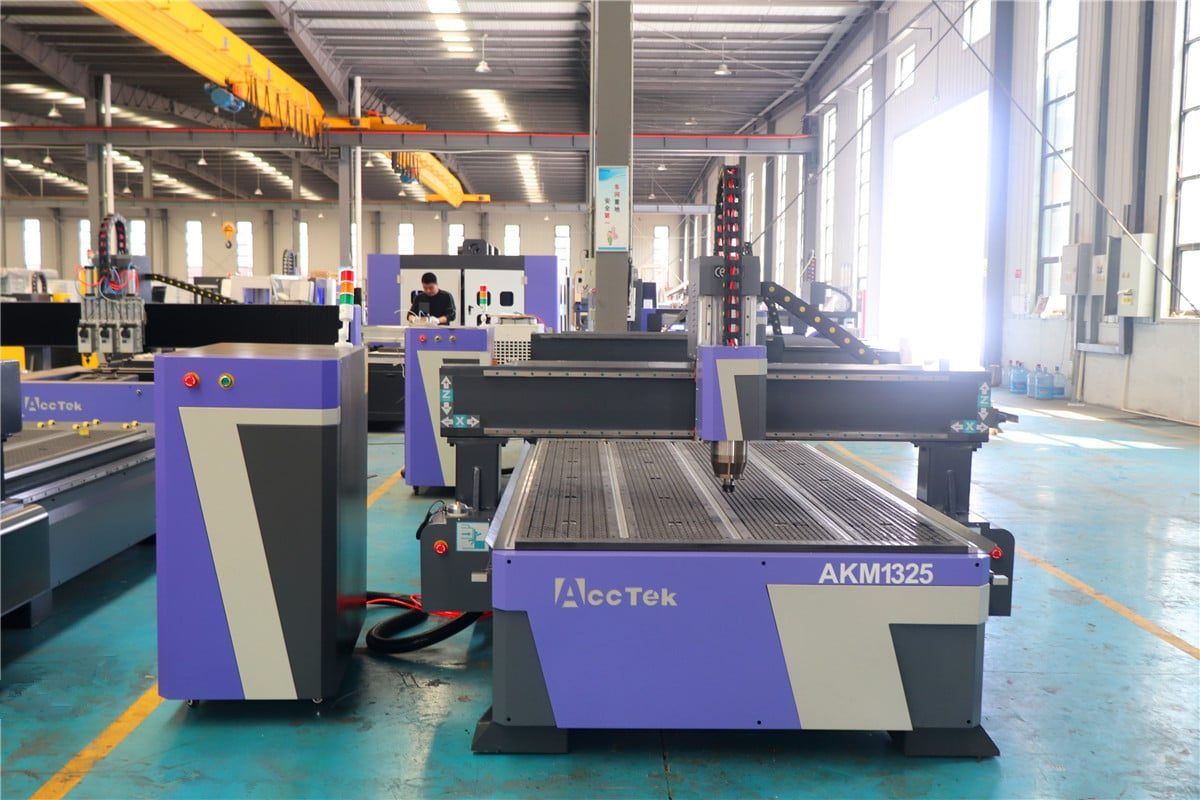
Running a CNC router requires more than just the machine itself. Whether you’re setting up a small shop or scaling up a large manufacturing facility, understanding the essential components and requirements for operating a CNC router is necessary. From the machine’s hardware and software to tools, materials, and maintenance practices, there are several factors that ensure smooth, efficient, and accurate operations.
In this article, we’ll explore the key elements required to run a CNC router, covering everything from the control system and cutting tools to the support infrastructure, safety considerations, and technical skills. By understanding these necessities, you can optimize your workflow, improve product quality, and ensure your CNC router performs at its best.
Understand the basics of CNC router
Before understanding how to run the CNC router, we must first understand its basic information. This involves the definition, working principle and applications of CNC routers. This knowledge forms the foundation for optimizing its use, troubleshooting potential issues, and ensuring the machine can perform to its full potential in various manufacturing and crafting applications.
What is a CNC Router?
A CNC router is a machine used for cutting, carving, drilling, and milling materials based on pre-programmed software instructions. It uses rotating tools, such as routers or spindles, to perform high-precision tasks. The “CNC” part of the name refers to the computer-controlled aspect, meaning the machine can follow specific instructions from a digital design file (usually in formats like G-code) to automate the cutting or shaping process.
CNC routers are versatile machines that can handle a wide range of materials, including wood, plastic, aluminum, composites, and sometimes stone and metal. They are widely used in various industries for producing intricate shapes, designs, and precise cuts.
How CNC Router Works
A CNC router works by following a series of steps that begin with a digital design file, typically created in a CAD (Computer-Aided Design) program, which is then converted into a CNC-compatible file (usually G-code). The process can be broken down into the following steps:
- Design and Programming: The user designs the part or product using CAD software. Once the design is complete, it is converted into machine-readable code (G-code) through CAM (Computer-Aided Manufacturing) software.
- Machine Setup: The material to be cut is placed onto the router’s worktable. The router’s cutting tools (such as end mills, bits, or drills) are set, and the machine is calibrated to the workpiece.
- Toolpath Execution: The CNC router follows the G-code instructions, which dictate how the cutting tool should move across the workpiece. The machine typically has multiple axes (usually X, Y, Z), which allow for movement in three dimensions.
- Cutting Process: As the router’s spindle or motor moves, it removes material from the workpiece in precise increments. The cutting tool’s speed, depth of cut, and feed rate are adjusted based on the material and desired outcome.
- Finishing and Quality Control: After the cutting process is completed, the piece is checked for accuracy and quality. Sometimes additional finishing operations, such as sanding or polishing, are required.
Applications of CNC Router
CNC routers are used in a wide variety of industries due to their ability to automate complex cutting tasks with high precision. Common applications include:
- Woodworking: In woodworking, CNC routers are used for cabinet making, furniture manufacturing, moldings, and custom wood carvings. They can produce intricate designs with fine details that would be difficult or impossible to achieve by hand.
- Sign Making: CNC routers are ideal for creating signs, logos, and decorative elements, often made from wood, plastic, or metal. They can cut complex patterns and intricate details for both commercial and artistic signage.
- Prototyping: CNC routers are widely used in prototyping industries to create rapid prototypes of parts or products from various materials, helping to accelerate product development.
- Plastic and Metal Cutting: In addition to wood and composites, CNC routers are sometimes used for cutting plastics and non-ferrous metals like aluminum. They can also be used for engraving or marking metal surfaces.
- Custom Carpentry and Furniture: High-end furniture makers and custom carpenters use CNC routers to produce one-of-a-kind, precision-crafted wood pieces, ensuring that parts are consistently accurate and meet exact specifications.
CNC routers provide efficiency, consistency, and the ability to handle both small-scale, detailed projects as well as large, production-level jobs. They are indispensable tools in many industries that require intricate, high-quality craftsmanship.
Basic components of CNC router operation
A CNC router operates through a combination of key components that work together to accurately cut, carve, and mill materials based on programmed instructions. The basic components involved in CNC router operation include:
- Computer and Software: The computer is the heart of the CNC router system, where the machine’s operations are controlled through specialized software. CAD software is used to design the part, while CAM software generates the toolpath that guides the router. It interprets the design into machine-readable code (G-code), which tells the CNC router exactly how to move.
- CNC Controller: The controller interprets the G-code and sends signals to the machine’s motors to perform the desired operations. It acts as the interface between the computer and the mechanical parts of the CNC router, ensuring the movement of the machine aligns with the design specifications.
- Motors and Drives: Motors are used to drive the movement of the CNC router in different axes (X, Y, Z). These motors are usually stepper or servo motors, with the latter offering more precision and speed. They control the movement of the cutting head, spindle, and table, enabling accurate and automated operations.
- Spindle: The spindle holds and drives the cutting tool and is responsible for the CNC router’s cutting action, removing material from the workpiece. It may have variable speeds, depending on the material and tool being used.
- Cutting Tools: The cutting tools, such as end mills, ball mills, or specialized routers, are attached to the spindle and perform the actual cutting, shaping, or carving of the material. They come in various shapes and sizes, depending on the task at hand, such as routing, engraving, drilling, or carving.
- Machine Worktable: The table supports the workpiece and provides a stable base for the CNC router to operate. The table may have clamps, vacuum systems, or other fixtures to secure the material. It ensures the workpiece remains steady and aligned during the cutting process.
- Linear Guides and Rails: Linear guides and rails allow precise, smooth movement of the CNC router’s spindle or table in the X, Y, and Z axes. These components minimize friction and improve the precision and stability of the machine’s movements.
- Framework Structure: The frame serves as the foundational structure of the CNC router, providing support and stability to the entire system. It is usually made of heavy-duty materials such as steel or aluminum to minimize vibrations and ensure accuracy during cutting operations.
- Dust Collection System: A dust collection system removes debris and dust created by the cutting process. It keeps the work area clean, improves safety, and prevents material buildup that can affect the quality of the cut.
These components work together in a coordinated fashion to produce high-precision, automated cuts on a variety of materials.
Setting Up and Operating a CNC Router
Operating a CNC router involves a series of well-defined steps to ensure accurate results, efficiency, and safety. Below is a comprehensive guide covering everything from setup to monitoring.
Machine Setup and Calibration
- Position the CNC Router: Place the machine on a stable, level surface to minimize vibrations and ensure precision.
- Connect Power and Components: Securely connect the CNC controller, spindle, and drive motors to the power source. Check all cables and connections for proper installation.
- Calibrate the Machine: Home the machine to establish its reference point. Set the tool’s zero point on the workpiece by manually positioning the spindle and saving the coordinates in the software.
- Check Mechanical Components: Inspect the linear guides, screws, and motors for smooth operation and adjust as needed.
Material Preparation
- Select Material: Choose the appropriate material (e.g., wood, plastic, or metal) for your project.
- Secure the Workpiece: Position the material on the worktable and secure it using clamps, vacuum systems, or fixtures. Ensure the workpiece is flat and aligned with the machine’s axes.
- Clean the Material: Remove any debris, oils, or surface imperfections that might affect cutting quality.
Toolpath Generation and Programming
- Design the Project: Use CAD software to create the design, then convert the design into a CNC-compatible format using CAM software.
- Generate the Toolpath: Set parameters like feed rate, cutting speed, and depth of cut based on the material and tool specifications. Simulate the toolpath in the software to verify accuracy and avoid collisions.
- Load the Program: Transfer the G-code to the CNC router via USB, network, or directly from the control computer.
Safety Protocols and Best Practices
- Personal Protective Equipment (PPE): Wear safety goggles, ear protection, and gloves as needed.
- Check the Machine: Ensure all guards, enclosures, and emergency stop buttons are functional.
- Area Safety: Keep the workspace clean and clear of unnecessary objects or personnel.
- Test Runs: Perform a dry run (air cut) to check the toolpath without engaging the cutting tool with the material.
Machine Operation and Monitoring
- Start the Spindle: Adjust the spindle speed according to the material and cutting tool requirements.
- Begin Cutting: Start the cutting process by following the programmed toolpath.
- Monitor Performance: Observe the machine for irregular sounds, vibrations, or deviations. Ensure the cutting tool remains sharp and the material is being processed as planned.
- Adjust as Necessary: Pause the operation if corrections to speed, depth, or alignment are required.
Finishing the Job
- Stop the Machine: Once the cutting is complete, turn off the spindle and disconnect the power.
- Remove the Workpiece: Carefully release the material from the clamps or vacuum table.
- Inspect the Output: Check the finished piece for accuracy, quality, and any required finishing.
Post-Operation Maintenance
- Clean the Machine: Use a dust extraction system or vacuum to clear debris and dust from the machine and work area.
- Inspect Components: Check for wear on the spindle, cutting tool, and mechanical parts. Replace or lubricate as needed.
- Update Records: Log the machine’s operation time and maintenance tasks for future reference.
By mastering these steps, operators can ensure efficient and safe CNC router operations while achieving precise and consistent results.
Advanced technologies and techniques for successful CNC routing
CNC routing has evolved significantly with the advent of advanced technologies and techniques that improve accuracy, speed, and versatility in manufacturing processes. These innovations enable manufacturers to meet the growing demands for precision and complexity in product design. Here are some of the most advanced technologies and techniques for successful CNC routing:
Tool Path Optimization
Tool path optimization is beneficial for improving the efficiency and accuracy of CNC routing. Here are advanced techniques:
- Optimizing Feed Rates and Speeds: Adjusting feed rates and spindle speeds to match the material and cutting tool can significantly reduce cycle time and improve surface finishes. Using optimal values helps prevent tool wear and overheating.
- Tool Path Strategies: Advanced routing strategies such as Climb Milling (for better chip removal) and Raster Milling (to achieve smoother finishes) can be selected based on the material and part design. Spiral or Zigzag paths often offer better results for certain shapes.
- Tool Path Smoothing: Path smoothing algorithms help in reducing unnecessary movements, minimizing tool engagement time, and increasing throughput. Tools like curvature-based smoothing or segmentation reduce the number of sharp turns, leading to faster processing.
- Adaptive Tool Paths: Adaptive machining dynamically adjusts the tool path during the routing process based on feedback (e.g., tool wear or material inconsistency), leading to improved material removal rates and reduced risk of errors.
Material Selection and Processing Parameters
Selecting the right material and setting the proper processing parameters are beneficial for achieving desired results in CNC routing.
- Material Characteristics: Understanding the mechanical properties (hardness, density, thermal conductivity) and machining characteristics (cutting behavior, chip formation) of materials like wood, plastics, metals, and composites. For example, harder materials like aluminum require slower feed rates and higher spindle speeds.
- Cutting Tools and Material Compatibility: Selecting appropriate tools (e.g., carbide tools for hard materials or HSS for softer ones) based on the material type helps in improving tool life and cut quality.
- Optimization of Cutting Depth and Passes: For tougher materials, multiple shallow passes are often preferred over one deep pass to reduce tool stress and improve finish quality. Fine-tuning cutting depth and step-over distance will also ensure smoother cuts.
- Coolant and Lubrication: The use of proper cooling methods (e.g., air blast or mist cooling) prevents tool overheating, prolongs tool life, and improves the cut quality. For metals, using liquid coolants can also help with chip evacuation.
Maintenance and Troubleshooting
Regular maintenance and proactive troubleshooting are beneficial for minimizing downtime and ensuring that the CNC router operates at peak performance.
- Regular Tool Checks and Replacements: Routinely inspect cutting tools for wear and tear. Tools that show signs of dullness or chip build-up should be replaced or sharpened immediately to maintain cut quality and avoid damaging the workpiece.
- Spindle Maintenance: The spindle is a crucial component for routing. Ensure it is kept clean, and lubricate bearings to prevent overheating. Over time, the spindle’s accuracy may degrade due to wear or misalignment, requiring realignment or replacement.
- Machine Calibration: Ensure that the CNC router is properly calibrated by checking the X, Y, and Z axes alignment regularly. Calibration tools can assist in verifying and adjusting the machine’s accuracy. Misalignment may cause issues like incorrect cuts or poor finishes.
- Electrical and Mechanical Checks: Check wiring, motors, and controllers to ensure everything is functioning correctly. Troubleshoot errors like overheating, vibration, or unexpected tool movements, which can cause misalignment or inaccuracies in parts.
- Error Codes and Diagnostics: Modern CNC routers provide diagnostic tools or error codes that help in troubleshooting. Understanding the meaning of these error codes and how to resolve them can quickly address machine malfunctions or operational issues.
Workflow Optimization
Optimizing the workflow from design to final part production improves efficiency and throughput in CNC routing operations.
- Advanced CAD/CAM Integration: Integrating CAD and CAM systems optimizes part design for machining. Advanced CAD/CAM software features like parametric modeling and 3D simulation help identify potential design or toolpath issues before production begins, saving time and reducing errors.
- Automated Tool Change Systems: Auto tool changers allow CNC routers to switch tools without manual intervention, ensuring faster and more efficient production, especially for jobs that require multiple tool types.
- Batch Processing and Nesting: Use nesting software to maximize material usage and reduce waste. Nesting software arranges multiple parts on a sheet of material in a way that minimizes leftover material.
- Real-time Monitoring and Adjustment: Implement systems for real-time performance monitoring and feedback to ensure everything is operating as expected. Machines that can adjust cutting parameters dynamically during operation based on feedback data can maintain higher precision and optimize machine usage.
Advanced technologies and techniques are continually transforming the CNC routing industry, improving production efficiency, precision, and the ability to handle complex materials and shapes. By continuously refining these advanced techniques, CNC operators can achieve higher precision, reduce errors, extend tool life, and enhance productivity across their operations.
Safety and Precautions for CNC Routing
CNC routers are powerful machines that can offer precision and efficiency, but they also pose safety risks due to the high speeds, rotating tools, and other moving parts. To ensure the safe operation of CNC routers, several safety measures must be observed. Here are the key safety measures and operating guidelines:
Safety Measures
- Personal Protective Equipment (PPE): Operators should always wear appropriate PPE, such as safety glasses, hearing protection, and gloves, to safeguard against flying debris, high noise levels, and potential contact with sharp objects. Depending on the material being cut, respiratory protection may also be necessary to avoid inhaling harmful dust or fumes.
- Emergency Stop System: Familiarize yourself with the location of the emergency stop button, which immediately halts the machine in case of malfunction or dangerous situations. Emergency procedures should be clearly outlined, and operators should be prepared to stop the machine quickly if needed.
- Dust Removal System: CNC routers can generate a significant amount of dust and fumes, particularly when cutting materials like wood or plastics. It’s necessary to ensure that a proper dust extraction system is in place and functioning to minimize airborne particles and maintain a clean work environment. Adequate ventilation systems should be used to ensure a safe atmosphere for operators.
Operational Best Practices
- Machine Calibration: Before starting any project, ensure that the machine is calibrated, including the alignment of the axis, spindle, and tool holder. Regular calibration ensures that the machine operates within the desired tolerances, reducing errors and wear. Calibration should be performed periodically and after any significant movement or maintenance.
- Tool Path Optimization: A well-planned tool path minimizes unnecessary movements, reduces cutting time, and prevents excessive wear on the tools. Using software to simulate the tool path before cutting can help identify potential collisions, excessive tool forces, or inefficient movements, ensuring that the machine operates smoothly and without risk to both the machine and the material.
- Operator Training: Only trained operators should run CNC routers. Proper training ensures that the operator understands the machine’s capabilities and limitations and can recognize and address potential issues. Operators should be familiar with the control software, machine functions, and emergency procedures to avoid accidents.
By following these safety precautions, operators can reduce the risk of accidents and ensure the efficient operation of CNC routers.
Maintenance and Troubleshooting of CNC Routers
Proper maintenance and troubleshooting of CNC routers are beneficial to ensure their longevity and optimal performance. Here’s an essential maintenance area:
Routine Maintenance
- Lubrication: Proper lubrication is beneficial for maintaining the moving parts of a CNC router, such as rails, spindles, and bearings. Regular lubrication ensures smooth movement, reduces friction, and prevents premature wear and tear. It is important to use the recommended lubricant for each component and apply it at regular intervals as specified in the manufacturer’s maintenance schedule. Failing to keep parts adequately lubricated can lead to system malfunctions, decreased performance, and costly repairs.
- Cleaning: Routine cleaning of the CNC router is beneficial to prevent dust, debris, and metal shavings from accumulating and affecting machine performance. Cleaning the work area, especially around the spindle, rails, and dust collection system, will help maintain optimal operation and reduce the risk of tool damage. It’s recommended to use compressed air or soft brushes for cleaning and to check that the dust collection system is functioning properly. Keeping the machine clean also improves safety by reducing the chances of overheating or electrical issues caused by blocked components.
Troubleshooting
- Error Log: Regularly checking the CNC router’s error log is an important part of troubleshooting and maintenance. The log stores valuable information about any system malfunctions, software glitches, or hardware failures. By analyzing the error log, operators can identify recurring issues and take proactive measures before they result in significant downtime or more expensive repairs. Ensuring that error logs are regularly reviewed and properly addressed will help maintain the machine’s reliability and longevity.
- Tool Inspection: Routine tool inspection is beneficial to ensure that cutting tools, such as end mills, drills, and other accessories, are in good condition. Worn-out or damaged tools can cause poor-quality cuts, excessive vibrations, and unnecessary stress on the CNC router. Regularly inspecting the tools for wear, corrosion, and breakage will help avoid unexpected tool failure during operation. Replacing tools as needed, and ensuring they are correctly calibrated, ensures optimal cutting performance and prolongs the life of both tools and the CNC router.
By maintaining a consistent schedule for lubrication, cleaning, error logging, and tool inspection, you can significantly reduce downtime, improve machining precision, and extend the life of your CNC router. Additionally, addressing issues as soon as they arise through troubleshooting will ensure that your machine operates efficiently for years to come.
Summarize
Running a CNC router requires a combination of the right equipment, software, and skills to ensure optimal performance and efficiency. Understanding your machine’s components and investing in the right setup can help you realize your CNC routing’s full potential. With the guidance provided in this article, you can effectively run your CNC router and take your projects to the next level. To learn more about CNC router operation, you can read “Beginner’s Guide to CNC Router Programming” and “How To Set Up A CNC Router: Step-By-Step Guide.”
AccTek CNC, a leading CNC router manufacturer in China, offers high-quality and reliable CNC routers designed to meet the needs of various industries. Whether you’re looking for a versatile machine for woodworking, metalworking, or other materials, AccTek’s range of CNC routers ensures efficient and precise performance. Our expert customer support and tailored solutions further enhance the value of their products, making AccTek CNC a trusted choice for businesses seeking to optimize their production processes.