- 7-10 Min Read
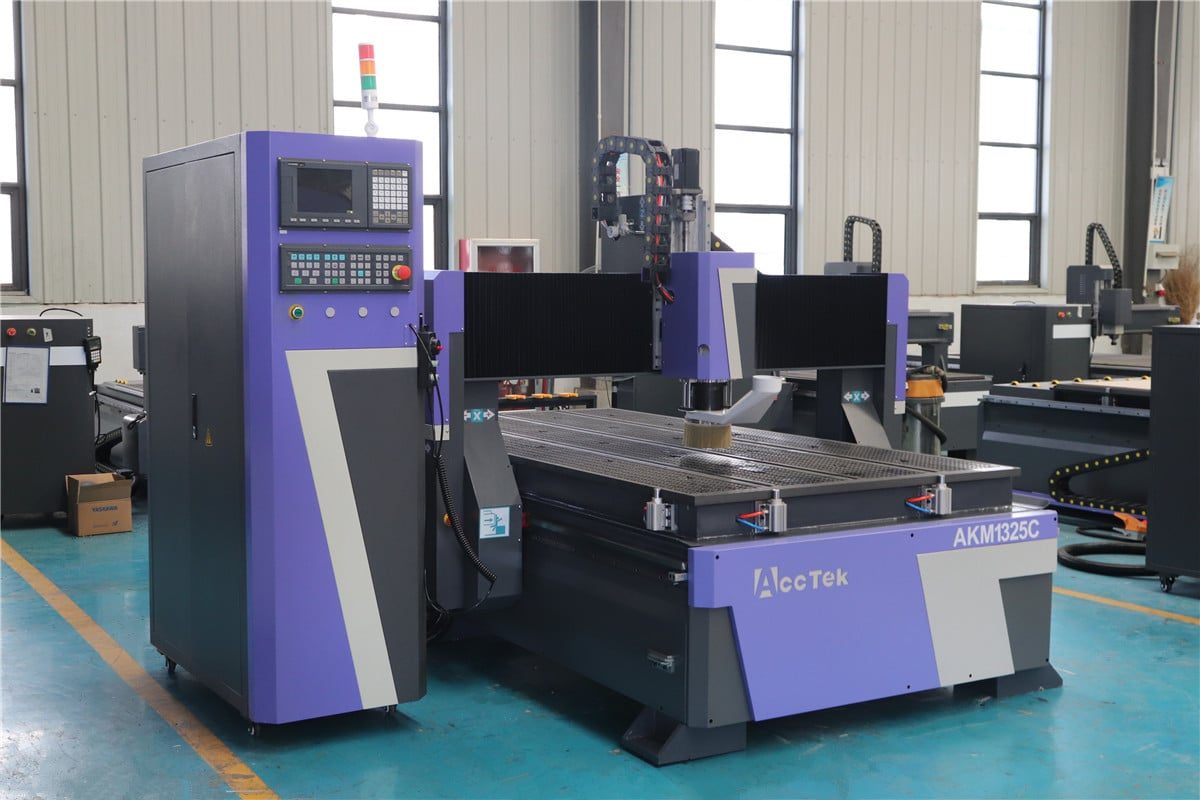
CNC routers are renowned for their precision and versatility in a wide range of applications, and one key factor that plays a big role in achieving these qualities is CNC router clearance. But what exactly is CNC router clearance, and why does it matter? Understanding and managing this clearance is essential for anyone looking to optimize their CNC router’s performance. These small but significant gaps can have a profound impact on the machine’s performance, affecting everything from the accuracy of cuts to the quality of the finished product.
This article delves into the concept of CNC router clearance, exploring its definition, causes, and effects. By comprehensively examining how these gaps arise and the problems they can create, we aim to equip you with the knowledge needed to maintain optimal machine performance and achieve the highest levels of precision in your CNC machining projects. Whether you are a seasoned professional or just starting with CNC routing, gaining a thorough understanding of clearance will undoubtedly enhance your machining capabilities.
Understanding CNC Router Clearance
A CNC router clearance refers to the unintended space or play between interconnected mechanical components of a CNC router. This clearance can exist between various parts such as ball screws and nut assemblies, linear guides and bearings, couplings, joints, and other mechanical interfaces. These clearances can be inherent in the design due to manufacturing tolerances or develop over time due to wear and tear. The importance of understanding and managing clearance is reflected in the following aspects:
Precision and Accuracy
- Impact on Precision: clearances in the mechanical components can lead to inaccuracies in the movement and positioning of the CNC router. Even small clearances can result in significant deviations from the intended path, affecting the quality of the cut or machined part.
- Consistent Output: Minimizing clearances ensures that the CNC router consistently produces parts with the desired dimensions and tolerances.
Machining Quality
- Surface Finish: clearances can cause vibrations and instability during the machining process, leading to poor surface finish and defects in the final product.
- Detail Accuracy: For intricate designs and fine details, any clearancecan result in loss of sharpness and precision in the machined features.
Tool Life and Wear
- Reduced Wear: Properly managing clearances helps in reducing the wear and tear on both the machine components and the cutting tools, extending their service life.
- Tool Breakage: Excessive clearances can lead to uneven load distribution on the cutting tool, increasing the risk of tool breakage.
Machine Longevity
- Maintenance and Repairs: Regular monitoring and adjustment of clearances can prevent excessive wear and damage to the CNC router, reducing the frequency and cost of maintenance and repairs.
- Operational Stability: A machine with well-managed clearances operates more smoothly and reliably, reducing downtime and increasing productivity.
Safety
- Operational Safety: clearances can lead to unexpected movements or failures during operation, posing safety risks to the operator and the work environment.
- Component Failure: Preventing clearances helps in avoiding sudden component failures that could lead to accidents or damage to the machine and workpiece.
Understanding and managing CNC router clearances is essential for anyone doing fine work. It ensures that every cut is precise, every detail is sharp, and the overall quality of the work is maintained. By mastering CNC router clearance, operators can achieve optimal performance from their machines, extending their lifespan and enhancing the quality of their outputs.
Causes of CNC Router Clearance
Understanding the causes of CNC router clearance is beneficial for optimizing their performance and ensuring precise, high-quality results. Various factors can contribute to the need for clearance in CNC routing, and recognizing these can help in managing and maintaining the appropriate clearances. Here are some of the primary causes:
Clearance of Mechanical Parts
The clearance in CNC routers can often be attributed to clearances in the mechanical parts. These clearances can be inherent in the design or develop over time due to use. Key areas where mechanical clearances may occur include:
- Ball Screws and Nut Assembly: Even with precision manufacturing, there can be small clearances between the ball screws and nuts.
- Linear Guides and Bearings: These components are designed to have minimal clearance, but slight clearances are inevitable.
- Couplings and Joints: The connections between various parts of the machine may have slight clearances, contributing to overall clearance.
Wear
Wear is a significant factor in the development of clearance in CNC routers. Over time, repeated use of the machine can lead to:
- Abrasive Wear: Caused by friction between moving parts, leading to material loss and increased clearance.
- Fatigue Wear: Repeated stress can cause cracks and material failure, contributing to clearance
- Corrosive Wear: Exposure to harsh environments can lead to chemical reactions that degrade mechanical parts.
Elastic Deformation
Elastic deformation refers to the temporary shape change of mechanical parts under load, which can lead to clearance issues. Factors influencing elastic deformation include:
- Load Distribution: Uneven or excessive loads can cause parts to bend or stretch, creating temporary clearance
- Material Properties: Different materials have varying degrees of elasticity, which can impact how much they deform under load.
- Structural Design: The design and rigidity of the machine’s structure can affect its susceptibility to elastic deformation.
Temperature Influence
Temperature changes can cause expansion or contraction of mechanical parts, leading to clearance variations. Key aspects of temperature influence include:
- Thermal Expansion: Different materials expand or contract at different rates with temperature changes, affecting clearances.
- Heat Generation: CNC routers generate heat during operation, which can cause parts to expand and create clearance
- Environmental Conditions: External temperature fluctuations can also impact the clearance in CNC routers.
Understanding the causes of CNC router clearance from these four aspects—mechanical part clearances, wear, elastic deformation, and temperature influence—can help in diagnosing and mitigating clearance issues. Regular maintenance, proper material selection, and robust design can minimize these effects and ensure precision in CNC router operations.
The Influence of CNC Router Clearance
The presence of a clearance in a CNC router’s mechanical components can significantly impact the machine’s performance and the quality of the machined parts. Here, we explore the influence of CNC router clearance from three critical aspects: accuracy, surface finish, and size.
Accuracy
- Impact on Precision: clearances between the mechanical parts of a CNC router can lead to inaccuracies in the movement and positioning of the router. This deviation occurs because the machine’s movements may not precisely follow the programmed path due to the play in the components. Even small clearances can accumulate over multiple movements, leading to larger errors in the final product.
- Repetition Accuracy:In addition to affecting single-instance accuracy, clearances can also compromise the repeatability of the CNC router. This means that the machine may not consistently produce identical parts, leading to variability and reducing the overall reliability of the production process.
Surface Finish
- Vibrations and Oscillations: clearances in the CNC router’s components can cause vibrations and oscillations during operation. These unwanted movements can create irregularities on the surface of the machined parts, resulting in a poor surface finish.
- Quality of Cut: Many applications require smooth and precise cuts, and clearances can result in jagged or rough edges on the material. This not only affects the visual appeal of the part but can also impact its functionality, especially in applications where a smooth surface is required for further processing or assembly.
- Tool Marks: Excessive clearance can cause the cutting tool to move unpredictably, leaving tool marks on the material. These marks can be difficult to remove and may necessitate additional finishing processes, increasing production time and costs.
Size
- Dimensional Accuracy: The clearancein a CNC router can lead to dimensional inaccuracies in the machined parts. As the router experiences variations in clearance, it can lead to fluctuations in the cutting path and depth, resulting in workpieces that do not conform to the specified dimensions.
- Tolerance Issues: In manufacturing, tolerances are key to ensure that parts can be assembled correctly and function as designed. clearances can cause deviations from specified tolerances, leading to workpieces that are out of spec.
CNC router clearance affects the machine’s performance in several critical ways, impacting accuracy, surface finish, and the consistency of part sizes. By understanding and addressing these influences, operators can enhance the precision, quality, and reliability of their machining processes, leading to better overall outcomes in their manufacturing operations.
Solutions to CNC Router Clearance
We’ve learned that CNC router clearances can lead to inaccuracies, poor surface finishes, and inconsistent part sizes, posing challenges to achieving high-performance standards. To address these issues, a comprehensive approach is necessary. Here, we delve into various solutions for minimizing CNC router clearance.
Precision Manufacturing and Assembly
One of the fundamental solutions to minimizing CNC router clearance is to ensure that the machine is built with high precision:
- High-Quality Components: Use high-quality, precision-engineered components such as ball screws, linear guides, and bearings to reduce inherent clearance
- Tight Tolerances: Manufacture parts with tight tolerances to minimize the clearance between mating components.
Careful Assembly: Assemble the machine components with great care, ensuring that parts fit together as intended without unnecessary clearances.
Regular Maintenance and Inspections
Regular maintenance and inspections are beneficial for identifying and addressing clearance issues before they impact machine performance:
- Scheduled Maintenance: Implement a regular maintenance schedule to check for wear and tear on critical components such as ball screws, linear guides, and couplings.
- Lubrication: Ensure that all moving parts are adequately lubricated to reduce friction and wear, which can lead to increased clearance over time.
- Component Replacement: Replace worn or damaged components promptly to maintain the machine’s precision and minimize clearance.
Adjustment and Calibration
Periodic adjustments and calibration of the CNC router can help maintain optimal clearance settings:
- Backlash Compensation: Use software settings to compensate for backlash (the play between mechanical components) and reduce its impact on accuracy.
- Alignment Checks: Regularly check and adjust the alignment of key components such as the spindle, linear guides, and ball screws to ensure they are correctly positioned.
- Tension Adjustments: Adjust the tension in belts and other drive mechanisms to minimize play and maintain tight control over movements.
Upgrading Components
Upgrading certain components can significantly reduce CNC router clearance:
- Advanced Ball Screws and Linear Guides: Consider upgrading to more advanced ball screws and linear guides that offer tighter tolerances and less play.
- Improved Bearings and Couplings: Use bearings and couplings designed for high precision and low clearance applications.
- Servo Motors: Upgrade to servo motors with higher precision and better control over movements to reduce the impact of clearance.
Temperature Control
Managing the operating temperature of the CNC router can help minimize the effects of thermal expansion and contraction on clearance:
- Cooling Systems: Install efficient cooling systems to maintain a stable temperature during operation and prevent thermal-induced clearance variations.
- Temperature Monitoring: Use temperature sensors to monitor the machine’s operating temperature and adjust processes accordingly to maintain consistent conditions.
Software Solutions
Leverage software solutions to detect and compensate for clearance issues:
- Advanced Control Software: Use CNC control software that offers advanced features for backlash compensation and real-time error correction.
- Predictive Maintenance Software: Implement predictive maintenance software that analyzes machine performance data to predict and address potential clearance issues before they become problematic.
Addressing CNC router clearance requires a multifaceted approach that includes precision manufacturing, regular maintenance, careful adjustments, component upgrades, temperature control, and advanced software solutions. By implementing these strategies, operators can significantly reduce clearance, enhance machine accuracy, improve surface finish, and ensure consistent part dimensions, ultimately leading to higher quality and more reliable CNC machining operations.
Summarize
CNC router clearance is a critical factor that influences the overall performance, precision, and quality of machined parts. By understanding the nature of these gaps and their potential impacts on accuracy, surface finish, and size, operators and technicians can take proactive steps to manage and minimize clearance issues. Regular maintenance, precise calibration, and proper material selection are essential practices that ensure the optimal functioning of CNC routers. By prioritizing these aspects, manufacturers can enhance productivity, reduce waste, and produce high-quality parts that meet specifications.
If you’re in the market for a reliable and high-quality CNC router, look no further than AccTek CNC. As a professional CNC router manufacturer, AccTek CNC is committed to providing users with top-notch machines and exceptional service. With a strong focus on precision, durability, and customer satisfaction, we ensure that our machines meet your manufacturing needs. Whether you are a seasoned professional or new to CNC routing, AccTek CNC’s products and support services will help you achieve outstanding results in your projects.