Table of Contents
All You Need to Know About CNC Router
- 10-15 Min Read
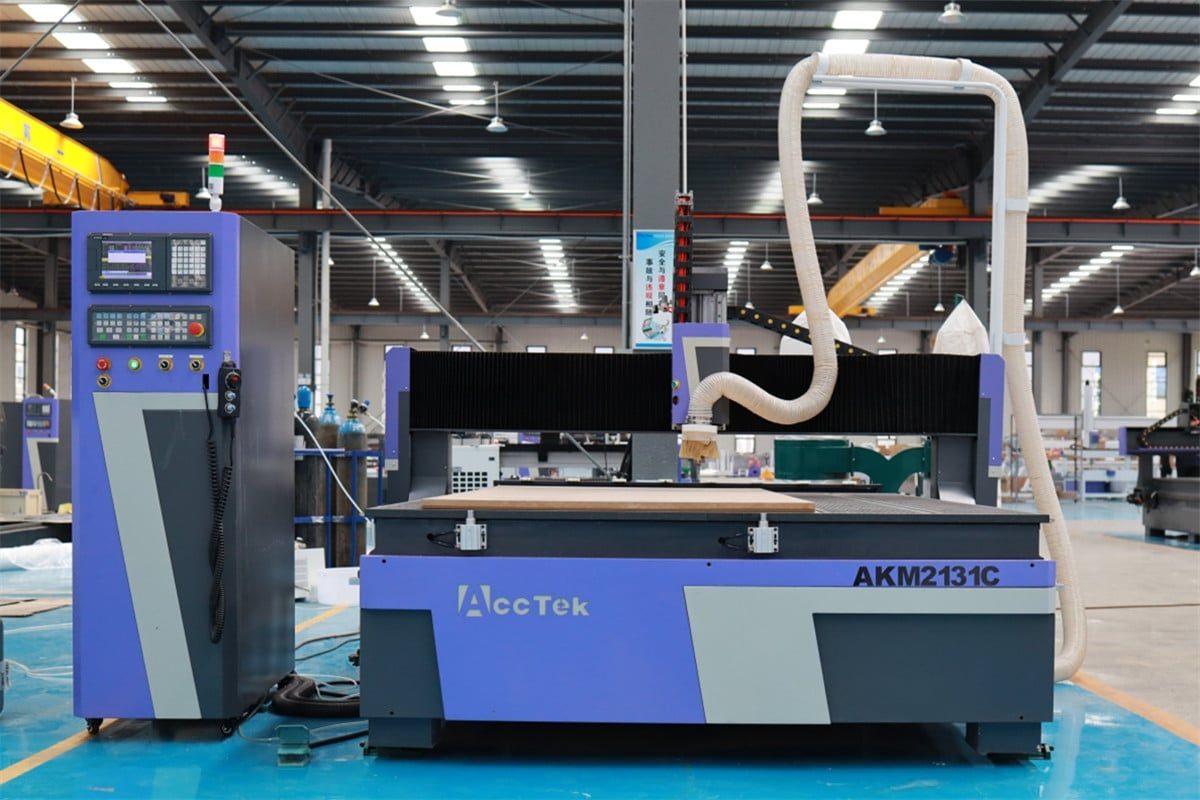
In the ever-evolving landscape of modern manufacturing and design, Computer Numerical Control (CNC) technology has emerged as a cornerstone for precision and efficiency. Among the myriad CNC machines, the CNC router stands out as a versatile tool capable of shaping a diverse range of materials with unparalleled accuracy. They offer precision and repeatability, making them valuable tools for both small-scale workshops and large-scale manufacturing operations. In this comprehensive guide, we delve into the intricate workings of CNC routers, exploring their components, applications, and the transformative impact they have had on industries spanning woodworking, metalworking, and beyond.
What is a CNC Router?
A CNC router is a computer numerical control (CNC) machine that is used for tasks such as cutting out parts, creating intricate designs, and producing prototypes. The term “CNC” refers to the computerized control of the machine, allowing precise and automated movement of the cutting tool or router bit. Here we introduce you to its basic information.
How does CNC Router work?
A CNC router operates based on computer numerical control (CNC) technology, utilizing a combination of hardware and software to precisely cut, carve, or shape various materials. Here is a detailed breakdown of how a CNC router works:
The process begins with the creation of a digital model or design using computer-aided design (CAD) software. Once the design is complete, the CAD software generates a toolpath. This toolpath is translated into a language called G-code, which consists of a series of alphanumeric commands that the CNC router can understand. The G-code is then processed by computer-aided manufacturing (CAM) software. CAM software takes the toolpath information and generates the specific commands needed to control the CNC router’s movements. This includes instructions for the X, Y, and Z axes, spindle speed, and tool changes.
Before the CNC router begins its work, the material to be machined is securely placed on the work table. The appropriate cutting tool or router bit is selected based on the material and the design requirements. The chosen tool is then mounted on the CNC router’s spindle. The CNC router needs to establish a reference point on the material, known as the “zero point” or “home position.” With the material secured and the zero point established, the CNC router is ready to start the machining process. The cutting tool rotates at high speed, and the CNC router moves it precisely along the X, Y, and Z axes according to the programmed instructions. Once the CNC router completes the programmed toolpath, the machining process concludes, leaving behind a finished, precisely machined product.
What components does the CNC Router consist of?
A CNC router consists of several key components that work together to execute precise cutting, carving, or shaping of materials. While the specific components can vary based on the manufacturer and model, the following are common components that constitute a typical CNC router:
- Control System: CNC routers are controlled by computer programs that translate designs into specific tool movements. These programs are typically created using computer-aided design (CAD) and computer-aided manufacturing (CAM) software.
- Control Panel: The control panel provides an interface for the operator to start, stop, and monitor the CNC router. It may include features for adjusting spindle speed, feed rates, and other parameters.
- Router Bit or Cutting Tool: The router bit is the tool that physically cuts or shapes the material. There are various types and sizes of router bits designed for different applications, such as cutting, engraving, or carving.
- Worktable: The worktable is the surface on which the material to be cut is placed. It can be an aluminum flatbed or a vacuum table that holds the material securely in place during the cutting process.
- Spindle: The spindle is the motorized component that rotates the router bit. It is responsible for the actual cutting or carving of the material. Spindles can have different power ratings depending on the materials they are intended to cut.
- Drive System: CNC routers use various drive systems to move the cutting tool precisely along the X, Y, and Z axes. Common drive systems include ball screws, lead screws, or rack and pinion systems. Ball screws offer high accuracy and repeatability. Lead screws are often used in applications where slightly lower precision is acceptable. Rack and pinion systems are known for their speed and are commonly used in larger CNC routers.
- Stepper or Servo Motors: Motors drive the movement of the CNC router along each axis. Stepper motors are commonly used due to their cost-effectiveness and simplicity, but servo motors offer higher precision and performance. Servo motors are often used in high-end CNC routers and applications where precision is paramount.
- Guide Rails: They are precision components that guide the motion of the CNC router’s moving parts along the X, Y, and Z axes. These rails are typically made of hardened steel or other materials with low friction to allow smooth and precise linear movement.
- Frame: The frame serves as the foundational structure of the CNC router, providing support and stability to the entire system. It is usually made of heavy-duty materials such as steel or aluminum to minimize vibrations and ensure accuracy during cutting operations. The design of the frame can be in the form of a gantry (bridge), moving gantry, or moving table, depending on the specific configuration of the CNC router.
- Cooling and Dust Collection Systems: CNC routers generate heat and produce dust during the machining process. Cooling systems help dissipate heat, while dust collection systems remove debris to maintain a clean working environment and prevent damage to the machine.
- Auto Tool Changer (Optional): In advanced CNC routers, an automatic tool changer may be included. This component allows the machine to change cutting tools automatically during a job, enabling a seamless transition between different tools and cutting operations.
What industries can CNC routers be used for?
The adaptability of CNC routers makes them a crucial tool in modern manufacturing and design processes. It has applications in a wide range of industries due to its ability to precisely cut, carve, and shape various materials. Here are some of the industries where CNC router machines are commonly used. These are just a few examples, and the versatility of CNC routers allows them to be applied in numerous other industries where precise cutting and shaping of materials are essential.
Furniture Production
The advent of CNC routers has revolutionized the furniture industry in numerous ways. It is an indispensable tool for the production of various wooden furniture such as cabinets, wardrobes, door panels, tables and chairs. From the largest cuts to the most delicate details, CNC routers are more than capable of handling any cutting operation while processing wood and other materials, which enables the rapid production of simple and complex furniture pieces. With the help of a CNC router, the work speed is faster and more efficient, and the solid wood products produced are often of better quality than other methods.
Advertising Industry
For advertisers, creating signage is often their main job. Commonly used materials for making signs are acrylic, wood, MDF, foam or some metals. CNC routers are a staple in the sign-making industry. They can cut letters, logos, and shapes with high precision, allowing for the production of custom signs for businesses, events, and promotional purposes.
Musical Instrument Industry
About 90% of musical instruments are made of wooden materials and require engraving on their material. Engraving is done to ensure the perfect size and shape of the instrument so that it can be better handled by the user. CNC routers are used in these industries to manufacture these musical instruments perfectly.
Crafts Industry
The range of crafts that can be made with a CNC router is almost unlimited, such as photo frames, holiday decorations, plaques, household items, souvenirs, etc. If you want to engrave 3D crafts, then a 4-axis or 5-axis CNC router may be more suitable for your needs. They have the advantage of high processing accuracy and are specially used for processing complex curved surface workpieces.
Stone Carving Industry
CNC routers have been widely adopted in the stone industry within the last decade to cut marble, granite, limestone, and other similar materials. The stone industry uses large and powerful CNC routers to cut stone, and create patterns on stone designs. CNC routers can also engrave stones, and can be used to create gravestones, stone inlays for home decor, fireplaces, and other architectural projects.
Mold Industry
Injection molding is the best way to mass-produce most things. Rather than having to machine every piece, you can save money and scale production by CNC machining the mold, and then using these molds to make parts. CNC routers are mostly used to mill mold cavities that are to be filled for injection molding, mold cores and inserts, finishing mold surfaces for accurate part production, and drilling holes into mold prototypes for things like injector pins, alignment pins, and cooling channels.
CNC routers are versatile tools that can be adapted to different applications within these industries, making them valuable for both prototyping and production purposes. The specific capabilities and features of a CNC router may vary, so choosing the right machine for a particular application is important.
Why choose a CNC router?
CNC routers have various advantages that make them widely used in various industries. Choosing a CNC router machine for industrial processing is a beneficial decision, and its introduction and widespread use have had a significant impact on the manufacturing industry. The following are the advantages that CNC router brings to the manufacturing industry.
- Precision and Accuracy: CNC routers operate with high precision and accuracy, ensuring that the desired design specifications are consistently met. This level of precision is difficult to achieve consistently with manual methods.
- Repeatability: CNC routers can reproduce identical products or components repeatedly, ensuring consistency in manufacturing. This is crucial for industries that require mass production of precise and uniform parts.
- Complex Designs: CNC routers can create intricate and complex designs that may be challenging or impossible to achieve manually. This capability is particularly valuable in industries such as woodworking, metalworking, and prototyping.
- Efficiency and Speed: CNC routers can work quickly and efficiently, reducing production times compared to traditional methods. This increased speed can lead to higher productivity and faster turnaround times.
- Automation: CNC routers automate the cutting and shaping processes, reducing the need for manual labor and minimizing the risk of errors caused by human factors. This leads to increased efficiency, higher production speeds, and reduced production costs in the long run.
- Versatility: CNC routers can work with a wide range of materials, including wood, plastic, metal, foam, and composites. This versatility makes them suitable for a wide range of applications across different industries.
- Programming Capabilities: CNC routers can be programmed to execute complex tasks and sequences of movements, allowing for the production of customized and intricate designs. This flexibility allows for the production of diverse and customized products with relative ease.
- Reduced Material Waste: CNC routers optimize material usage by minimizing waste. The computer-controlled precision ensures efficient cutting, reducing the amount of scrap material generated during the production process.
- Improved Safety: CNC routers contribute to improved safety in the workplace. Operators can control the machine from a distance, reducing the risk of accidents associated with manual machining processes.
- Cost-Effective in the Long Run: While the initial investment in a CNC router can be substantial, the long-term cost savings in terms of increased efficiency, reduced waste, and minimized labor costs often make it a cost-effective solution over time.
- Prototyping and Small Production Runs: CNC routers are well-suited for prototyping and small-scale production runs. They allow for quick adjustments to designs and easy production of small batches without the need for extensive tooling changes.
- Technology Integration: CNC routers can be integrated with computer-aided design (CAD) and computer-aided manufacturing (CAM) software, allowing for seamless design-to-production workflows. This integration streamlines the manufacturing process and facilitates design changes.
What is the future development of CNC routers?
The future development of CNC routers is likely to involve advancements in technology, addressing current challenges, and expanding capabilities to meet the evolving needs of industries. In this section, by understanding the challenges faced by CNC routers, we explore some of its potential development areas in the future. As these technologies continue to advance, CNC routers are likely to play a crucial role in shaping the future of manufacturing.
What challenges does CNC router face?
While CNC routers offer numerous advantages, they also face some challenges. These challenges can vary depending on the specific application and industry. Here are some common challenges associated with CNC routers:
- Initial Cost: The upfront investment in CNC router equipment, including the machine itself and associated software, can be substantial. This cost may pose a barrier for smaller businesses or those with limited budgets.
- Skilled Labor Requirements: Operating a CNC router requires skilled personnel who can program and set up the machine correctly. Finding and retaining qualified operators can be a challenge, and the skills gap in the workforce for CNC machining is a concern in some regions.
- Maintenance and Downtime: CNC routers require regular maintenance to ensure optimal performance. Unexpected breakdowns or downtime can occur, impacting production schedules. Preventive maintenance and prompt troubleshooting are crucial to minimize disruptions.
- Complex Programming: Programming CNC routers for specific tasks can be complex, especially for intricate or custom designs. Skilled programmers are needed to create efficient toolpaths and optimize the cutting process.
- Material Limitations: While CNC routers can handle a wide range of materials, certain materials may pose challenges due to their hardness, abrasiveness, or heat generation during machining. Specialized tooling and techniques may be required for such materials.
- Tool Wear and Replacement: Cutting tools used in CNC routers experience wear over time, affecting the quality of cuts. Regular tool replacement is necessary, and the cost of tooling can add to the overall operating expenses.
- Size Limitations: The size of the CNC router’s work area may limit the production of larger components. Industries requiring the machining of oversized parts may need to invest in larger, more expensive machines.
- Technological Advancements: Rapid technological advancements in CNC technology can make older machines obsolete. Keeping up with the latest software updates and hardware improvements may be necessary to stay competitive and maintain efficiency.
- Dust and Chip Management: CNC routers generate dust and chips during the cutting process. Effective dust and chip management systems are required to maintain a clean working environment and prevent damage to the machine.
- Complexity in 3D Machining: Three-dimensional machining can be more complex than 2D machining. Programming and executing intricate 3D designs may require specialized expertise and tools.
- Energy Consumption: CNC routers, especially larger and more powerful models, can consume a significant amount of energy. Energy-efficient practices and equipment may be needed to mitigate this challenge.
The future development direction of CNC router
These challenges currently faced by CNC routers largely dictate its future development direction. To meet these challenges, CNC routers need to continue to improve in design and functionality to adapt to future needs. Here are some potential areas of development for CNC routers in the future:
- Integration with Industry 4.0: Future CNC routers are expected to be more seamlessly integrated into the broader concept of Industry 4.0, which involves the interconnectedness of machines, data exchange, and automation. This integration could lead to smarter, more efficient, and interconnected manufacturing processes.
- Improved Automation: Automation in CNC routers is likely to advance further, reducing the need for manual intervention in setup, tool changes, and other processes. This can enhance overall efficiency and reduce the demand for highly skilled operators.
- Artificial Intelligence (AI) and Machine Learning: Incorporating AI and machine learning technologies can enable CNC routers to adapt and optimize their processes based on real-time data. This could improve predictive maintenance, toolpath optimization, and the overall performance of the machine.
- Enhanced Precision and Accuracy: Continuous improvements in drive systems, control algorithms, and sensor technologies could lead to even higher levels of precision and accuracy in CNC routers. This would enable manufacturers to produce increasingly complex and intricate designs with greater confidence.
- Multi-Functionality: Future CNC routers may evolve to offer more multi-functionality, allowing them to perform a broader range of tasks within a single machine. This could include combining milling, cutting, 3D printing, and other processes in a unified system.
- Augmented Reality (AR) and Virtual Reality (VR) Integration: AR and VR technologies could be integrated into CNC machining processes to enhance operator training, simplify machine setup, and provide real-time visualization of machining operations. This could improve the overall user experience and reduce the learning curve for operators.
- Energy Efficiency: Future CNC routers are likely to incorporate more energy-efficient components and systems to reduce overall energy consumption. This could involve advancements in spindle and motor technology, as well as improvements in system optimization.
- Advanced Material Handling: Improved material handling capabilities could become a focus of future CNC router development. This may include automated loading and unloading systems, as well as advancements in workholding solutions to accommodate a wider range of materials.
- Customization and Ease of Use: Future CNC routers may be designed to be more user-friendly, with intuitive interfaces and simplified programming. This could open up CNC technology to a broader range of users, including those with less technical expertise.
- Nanotechnology Applications: Advancements in nanotechnology could influence CNC router development, allowing for the machining of smaller and more intricate components with extreme precision. This could be particularly relevant in industries such as electronics and medical devices.
- Environmental Sustainability: As environmental concerns become more prominent, future CNC routers may incorporate eco-friendly features, such as improved dust and waste management systems, as well as the use of sustainable materials in construction.
Summarize
The CNC router, with its intricate dance of motors, spindle, and precision tooling, empowers creators to bring digital designs to life with unparalleled accuracy. As the boundaries of innovation are pushed, multi-axis machining, automatic tool changers, and smart interfaces usher in an era of heightened productivity and user-friendly operation. Moreover, the integration of CNC routers with additive manufacturing technologies and the versatility to work with an expanding array of materials further solidify their indispensable role in the manufacturing landscape. Achieving a comprehensive understanding of CNC routers opens the gateway to a world of precision and efficiency in manufacturing. As these technologies continue to evolve, their impact reverberates across diverse industries, from woodworking and metal fabrication to aerospace and beyond.
At AccTek CNC, we provide various types of CNC routers according to the needs of users, including heavy-duty 3-axis CNC router, 3D 4-axis CNC router, 5-axis CNC router, ATC CNC router, and customized CNC router. For CNC router operators looking for reliability, versatility and high efficiency, AccTck is a wise choice.
Want To get a good machine?
Click the button, our CNC Experts will contact you and send you a solution.