Table of Contents
Use a CNC Router: Comprehensive Guide
- 11-16 Min Read
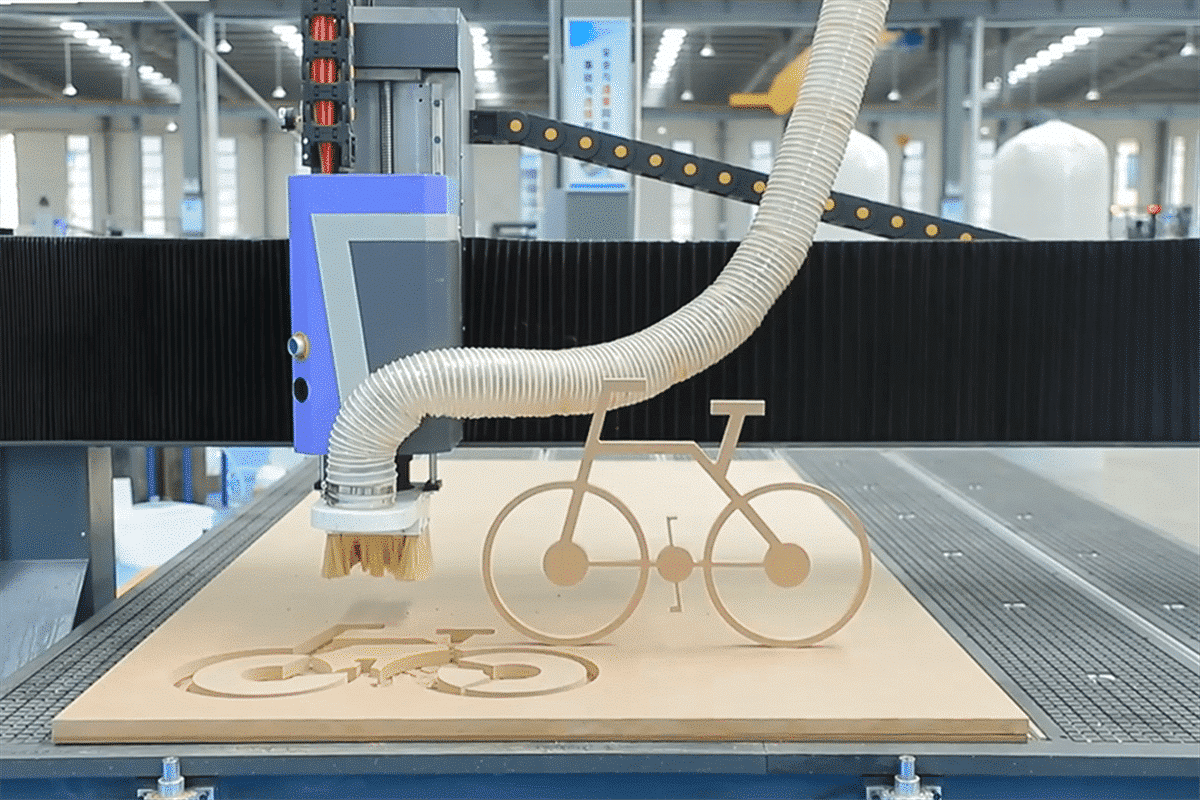
In the realm of modern manufacturing and craftsmanship, the CNC (Computer Numerical Control) router stands as a powerful tool, offering precision and versatility in shaping various materials. From intricate designs in aerospace components to the crafting of artistic sculptures, the CNC router empowers makers, engineers, and artists alike to transform raw materials into refined masterpieces with unparalleled accuracy. Whether you’re a seasoned professional seeking to refine your skills or a novice eager to explore the possibilities, this comprehensive guide will walk you through the intricate process of using a CNC router effectively. From mastering intricate tool paths to common machine troubleshooting, we’ll delve into each step to ensure a successful CNC router experience.
Understand the basic information of CNC routing and CNC router
CNC routing is the broad process or technique that involves using a CNC router to perform the cutting, shaping, and engraving tasks. It encompasses the entire workflow, from designing the digital model (using CAD software) to programming the tool paths (using CAM software) and, finally, executing the cutting process on the CNC router. In the realm of modern craftsmanship and manufacturing, CNC routing emerges as a transformative force, reshaping the way materials are sculpted and creations come to life. At the heart of this technological marvel is the CNC router, a powerful machine that seamlessly blends precision with creativity.
The CNC router is a type of CNC machine used for routing tasks. It typically consists of a worktable, a cutting tool (router bit or spindle), and a system of motors and actuators. It is a computer-controlled cutting machine that precisely moves a spindle in multiple directions (usually front and back, left and right sides, and up and down) to carve out desired shapes and designs. Whether you are an aspiring artisan, an industrial professional, or a hobbyist with a penchant for precision, understanding the fundamentals of CNC routing is the key to unlocking a world of limitless possibilities.
In summary, “CNC routing” refers to the overall process of using computer numerical control to automate the cutting of materials, and a “CNC router” is a specific type of CNC machine optimized for routing tasks. In the upcoming sections, we will give you a more comprehensive explanation from the basics of safety precautions and material selection to the intricacies of CNC software and the hands-on operation of the CNC router. Through the fusion of technology and craftsmanship, CNC routers have become an effective tool for turning innovative and complex designs into reality.
How to operate CNC router?
Using a CNC router involves several steps, and it’s a meticulous process encompassing safety measures, material preparation, software proficiency, machine setup, and post-processing. The operating procedures of the CNC router are organized here for you. By following these steps, you can effectively use a machine for various projects. Also, always refer to the specific manual and guidelines provided by the CNC router manufacturer for detailed and accurate instructions.
Safety Precautions
- Read the Manual: Before embarking on your CNC journey, it’s imperative to acquaint yourself with the intricacies of your CNC router. Refer to the manufacturer’s manual and documentation for specific instructions, safety guidelines, and maintenance protocols.
- Safety Gear: Protecting yourself is paramount. Wear safety glasses, ear protection, and, if necessary, a dust mask. These precautions safeguard against potential hazards, ensuring a secure working environment.
- Workspace Setup: Ensure the workspace is clean and well-lit. Keep the emergency stop button accessible, providing a quick means to halt operations in case of unforeseen circumstances.
Material Preparation
- Material Selection: Choose the appropriate material for your project, considering factors like hardness, density, and compatibility with your CNC router. Wood, plastic, and metal are common choices. Ensure the material is cut to size and free from defects.
- Workpiece Securing: Stability is key. Utilize clamps or other secure fastening methods to anchor the material firmly to the CNC router This prevents unintended movement during the machining process.
CNC Software
- Design Your Project: Begin by creating or obtaining a digital design for your project using CAD (Computer-Aided Design) software.
- CAM Software: Convert your design into G-code using CAM (Computer-Aided Manufacturing) software. This code dictates the toolpath the CNC router will follow during the cutting process.
- Toolpath Simulation: Prior to initiating the CNC router, simulate the toolpaths using the CAM software. This virtual run-through allows you to identify and rectify any errors or anomalies, preventing potential issues during actual machining.
CNC Router Setup
- Tool Selection: Selecting the appropriate cutting tool helps achieve good workpiece quality. Different materials and projects require specific tools. Install the chosen tool securely, following manufacturer guidelines.
- Zero Point Setup: Establish the workpiece zero point, also known as the origin, on the CNC router bed. This point serves as the reference for the machine to execute the programmed toolpath accurately.
- Tool Height Calibration: Calibrate the tool height to ensure accurate cutting. Calibrate the tool height using the CNC router’s calibration feature or manually adjust the tool to the correct height.
CNC Router Operation
- Load G-code: Load the G-code generated by the CAM software into the CNC router. This step ensures that the machine understands the programmed instructions for your specific project.
- Machine Homing: Initiate the homing process to establish the reference position for the CNC router. This step is crucial for ensuring the machine starts from a consistent and known position.
- Tool Change (if necessary): Follow the manufacturer’s instructions for changing tools for projects requiring multiple tools. Ensure proper calibration and verification of each tool before proceeding.
- Run a Test: Before running to the full job, perform a test run to ensure everything is set up correctly. This allows you to identify any potential issues, such as tool interference or programming errors before the actual machining begins.
- Start CNC Router: With all preparations in place, initiate the CNC router to begin the cutting process. Monitor its operation closely during the initial stages to ensure everything is running smoothly.
Post-Processing
- Remove Finished Workpiece: Once the CNC router completes the job, carefully remove the finished workpiece. Exercise caution to avoid damage or injury.
- Inspect and Sand: Thoroughly inspect the workpiece for imperfections. Sand or finish the material as needed to achieve the desired final product.
Maintenance and upkeep of CNC router
Routine maintenance is also part of the CNC router operation. Regular and proactive maintenance can help avoid downtime, extend the life of the machine, and ensure consistent, high-quality performance. It’s important to note that because different CNC routers may have unique requirements, always refer to the manufacturer’s guidelines and the specific maintenance manual for your CNC router when performing machine maintenance. Here are some general guidelines for the routine maintenance and upkeep of a CNC router:
Daily Maintenance
- Clean the Workspace: Remove debris, dust, and chips from the work area, especially around the spindle and guide rails. This prevents contamination and ensures accurate cnc router machine movements.
- Check Emergency Stop Function: Verify that the emergency stop button is functioning correctly. This is a safety feature that should be regularly tested.
- Inspect Tooling: Check the condition of the cutting tool or router bit. Replace or sharpen tools as needed.
Weekly Maintenance
- Lubrication: Lubricate the moving parts, such as guide rails and ball screws, according to the manufacturer’s recommendations. Proper lubrication prevents wear and ensures smooth operation.
- Check Belt Tension: Inspect and adjust the tension of the belts that drive the CNC router. Loose or overly tight belts can affect accuracy.
- Inspect Vacuum System: If your CNC router has a vacuum system for dust collection, check and empty the collection bins. Ensure that the vacuum system is functioning properly.
Monthly Maintenance
- Check Electrical Connections: Inspect electrical connections for signs of wear or loose connections. Tighten any loose terminals and replace damaged wiring.
- Inspect Coolant Systems: If your CNC router uses a coolant system, check coolant levels and ensure that the system is working correctly. Clean or replace filters as needed.
- Calibration: Verify the machine’s calibration by running test programs. This helps ensure accuracy in the cutting and machining processes.
Quarterly Maintenance
- Inspect Spindle: Check the spindle for any signs of wear, unusual noises, or vibrations. If necessary, replace bearings or other worn components.
- Check Ball Screws and Lead Nuts: Inspect ball screws and lead nuts for wear and backlash. Adjust or replace components as needed.
Yearly Maintenance
- Review Software and Firmware Updates: Check for updates to the CNC router’s control software and firmware. Keeping software up-to-date can provide performance improvements and additional features.
- Replace Worn Parts: Replace any worn-out components, such as limit switches, sensors, or belts, to maintain the overall reliability of the CNC router.
- Perform Preventive Maintenance: Consider a comprehensive preventive maintenance check, which may include more in-depth inspections and adjustments. Consult the machine’s manual for specific recommendations.
Common troubleshooting of CNC router
Maintaining a CNC router in optimal condition requires a proactive approach to troubleshooting. By understanding the common issues and implementing the suggested troubleshooting techniques, operators can ensure the longevity and consistent performance of CNC routers. Here we introduce to you some common troubleshooting methods and solution processes for CNC routers.
Incorrect Cutting or Engraving
- Check Tooling: Ensure that the cutting tool or router bit is sharp, properly secured, and appropriate for the material. Dull or inappropriate tools can lead to imprecise cuts.
- Toolpath Issues: Verify the toolpaths in the CAM software. Incorrectly programmed toolpaths can lead to cutting errors.
Inaccurate Cuts
- Calibration: Check the machine’s calibration. Run calibration tests and adjust settings if necessary.
- Loose Components: Inspect the machine for loose bolts, screws, or belts that could affect its precision. Tightening any loose components may resolve accuracy issues.
Excessive Vibration or Noise
- Spindle Issues: Inspect the spindle for wear or damage. Unusual noise or vibrations may indicate a problem with the spindle.
- Tool Holder: Check the tool holder and make sure it is properly secured. Vibrations can result from improperly secured tools, impacting cut quality.
Material Shift or Slippage
- Workholding: Ensure that the material is securely held in place. Use appropriate clamps or fixtures to prevent slippage.
- Feeds and Speeds: Adjust cutting speeds and feeds based on the material being used. Incorrect settings can contribute to material shift or slippage.
Error Messages on the CNC Control Panel
- Check Alarms: Review the error messages or alarms displayed on the CNC control panel. Consult the machine’s manual to interpret and address specific alarms.
- Electrical Issues: Inspect electrical connections for loose or damaged components. Electrical problems can trigger error messages and affect machine performance.
Z-Axis Drifting or Inconsistency
- Ball Screw and Lead Nut: Inspect the Z-axis ball screw and lead nut for wear. Replace or adjust components as needed.
- Lubrication: Ensure proper lubrication of the Z-axis components to prevent friction-related issues.
Tool Breakage
- Feeds and Speeds: Check if the cutting parameters (feeds and speeds) are appropriate for the material and tool. Adjust as necessary.
- Tool Quality: Use high-quality tools suitable for the job to minimize the risk of tool breakage during machining.
Dust Collection Issues
- Clean Dust Collection System: A clogged system can impact machine performance and result in poor dust extraction. Regularly clean or replace filters in the dust collection system, and ensure proper dust extraction.
Spindle Overheating
- Cooling System: Check the spindle cooling system, check coolant levels and functionality, and ensure that it is functioning properly. Overheating can be caused by a lack of coolant or issues with the cooling system.
Electrical Issue
- Power Supply: Verify the stability of the power supply. Fluctuations or interruptions in power can lead to erratic machine behavior.
- Wiring Inspection: Inspect the electrical wiring for signs of wear, damage, or loose connections. Faulty wiring can contribute to electrical issues.
Software Issues
- Update Software: Ensure that the CNC control software is up-to-date. Check for software updates or patches provided by the manufacturer.
For specific troubleshooting procedures, always refer to the CNC router’s user manual and documentation provided by the manufacturer. If issues persist, it may be necessary to contact the manufacturer’s technical support or consult with a qualified technician for further assistance.
Summarize
The versatility of CNC routers empowers creators to bring their designs to life with precision and efficiency. Whether you’re crafting intricate woodworking pieces, personalized signage, or complex prototypes, the CNC router is a powerful tool. By following the machine operating steps and troubleshooting methods in this guide, you have gained the basic knowledge to successfully operate a complex CNC router.
At AccTek CNC, we not only provide users with high-quality machines, but also provide complete after-sales services. We provide comprehensive technical guidance to every user who purchases a machine, including machine installation, parameter setting and troubleshooting. With the help of AccTek engineers, you can become an experienced CNC router operator faster. Want to add a high-performance CNC router to your workshop to help you complete projects faster? Contact us and AccTek CNC’s professional sales team will provide you with a complete solution based on your specific application and provide you with detailed pricing information.
Want To get a good machine?
Click the button, our CNC Experts will contact you and send you a solution.