- 11-16 Min Read
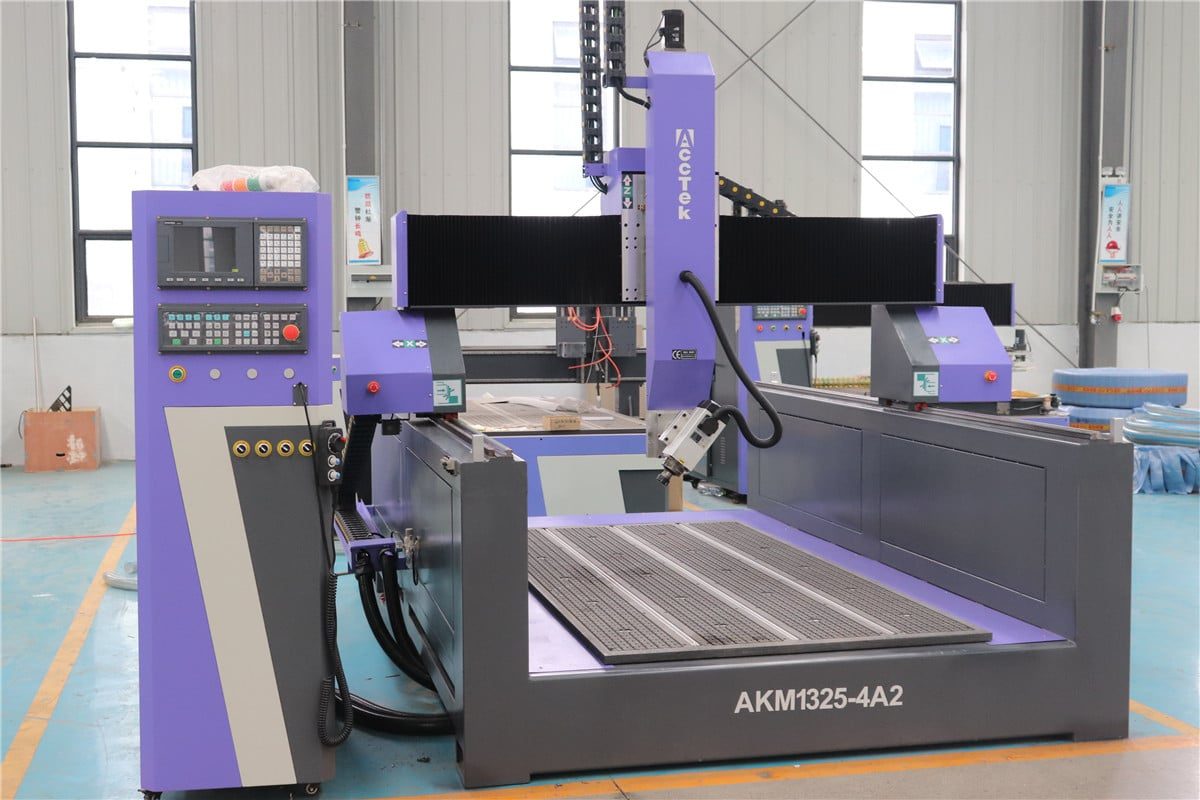
In the realm of modern manufacturing and fabrication, precision and efficiency reign supreme. Amidst the array of cutting-edge technologies, Computer Numerical Control (CNC) systems stand at the forefront, revolutionizing the way we shape, carve, and craft materials with unparalleled accuracy. Among the diverse array of CNC machines, the 4-axis CNC router emerges as a powerhouse, offering a new dimension of capabilities and possibilities. But what exactly is a 4-axis CNC router? In this introductory exploration, we uncover its fundamental workings, applications, and transformative impact across diverse industries. From its evolution beyond traditional three-axis counterparts to its intricate components and multifaceted applications, we delve deep into the essence of this revolutionary tool, uncovering the secrets behind its prowess and the myriad possibilities it unlocks for creators, artisans, and manufacturers alike.
The Basics of 4 Axis CNC Routers
Understanding the Four Axes
The configuration of a 4-axis CNC router is characterized by its ability to move and manipulate the cutting tool and workpiece in four distinct axes of motion. Unlike traditional 3-axis CNC routers, which operate along the X, Y, and Z axes, a 4-axis CNC router adds an additional rotational axis, typically referred to as the A-axis. This additional axis of rotation enables the machine to perform complex cuts and contours that were previously unattainable with three-axis systems. Let’s delve deeper into the configuration of a 4-axis CNC router:
- X-Axis: The X-axis controls the movement of a cutting tool or spindle along a horizontal plane, usually from left to right or right to left. The extent of the X-axis movement is determined by the size and design of the CNC router.
- Y-Axis: The Y-axis controls the movement of the cutting tool or spindle along the vertical plane, the movement generally goes from front to back or back to front. Similar to the X-axis, the Y-axis range is determined by the specifications of the CNC router.
- Z-Axis: The Z-axis is the depth axis, it controls the up and down movement of the cutting tool or spindle, allowing for cutting or engraving at different depths. The Z-axis range influences the maximum thickness of the material that the CNC router can effectively work on.
- A-Axis: The A-axis introduces rotational movement around the X-axis. This rotational axis enables the machine to tilt or swivel the cutting tool and workpiece with a maximum swing range of 180°, thereby expanding the range of machining capabilities.
By incorporating the A-axis into the CNC router’s configuration, manufacturers can achieve a higher degree of versatility and complexity in their machining operations. Furthermore, the configuration of a 4-axis CNC router may include other essential components such as the frame, worktable, spindle, and control system. These components work in conjunction to ensure the smooth and precise operation of the machine, translating digital designs into physical prototypes or finished products with exceptional accuracy.
How 4-Axis CNC Routers Work
A 4-axis CNC router operates by precisely controlling the movements of a cutting tool and workpiece along four axes of motion X, Y, Z, and A axis. Understanding how 4-axis CNC routers work entails exploring the intricate coordination of motion and control that enables these machines to execute precise and complex machining operations. Let’s delve into the workings of these sophisticated systems:
- Movement System: The X, Y, and Z axes of the 4-axis CNC router correspond to the machine’s primary linear movements. The A-axis introduces rotational movement around the X-axis, allowing the cutting tool and workpiece to tilt or swivel. This rotational capability enables the machine to execute complex cuts, contours, and surface finishes that would be challenging with traditional three-axis systems.
- Control System: The control system of the 4-axis CNC router comprises a computer, CNC controller, and software. CAD software is used to create digital designs or models of the desired parts or components. CAM software generates toolpaths based on the CAD design, specifying the precise movements and cutting operations required to fabricate the part. Through coordinated motion control and software-driven commands, the CNC router follows programmed toolpaths to carve, mill, or engrave materials with exceptional accuracy and efficiency.
What are the advantages of 4-axis CNC router?
The advantages of a 4-axis CNC router make it a valuable asset for manufacturers looking to enhance their machining capabilities, improve efficiency, and produce high-quality parts with greater precision and versatility. The 4-axis CNC router has many advantages compared with the traditional 3-axis CNC router, which is specifically reflected in the following aspects:
- Increased Versatility: A 4-axis CNC router can move the cutting tool along four axes (X, Y, Z, and an additional rotational axis), allowing for more complex cuts and machining operations. This versatility enables the machine to produce various parts and components with varying geometries.
- Enhanced Precision: The additional axis of movement provides greater control over the machining process, leading to improved precision and accuracy in the finished parts. This is particularly beneficial for intricate designs and tight tolerance requirements.
- Reduced Setup Time: With the ability to tilt or rotate the workpiece, a 4-axis CNC router can machine multiple sides or angles without the need for repositioning or manual intervention. This reduces setup time and increases overall efficiency in production.
- Expanded Machining Capabilities: The fourth axis allows more complex machining operations such as 3D carving, contouring, engraving, and rotary cutting. This enables the machine to tackle a wider range of applications and meet diverse manufacturing needs.
- Improved Surface Finish: The advanced capabilities of a 4-axis CNC router enable it to execute more sophisticated tool paths, resulting in smoother surface finishes on the machined parts. This is especially important for applications requiring high-quality surface finishes, such as mold-making and prototyping.
- Cost Efficiency: While the initial investment in a 4-axis CNC router may be higher than a 3-axis machine, its increased versatility and efficiency can lead to cost savings in the long run. By reducing setup time, improving accuracy, and expanding machining capabilities, a 4-axis CNC router can help businesses optimize their manufacturing processes and increase productivity.
What are the applications of 4-axis CNC router?
The applications of a 4-axis CNC router are diverse and varied across different industries due to its enhanced capabilities for complex machining operations. This demonstrates their versatility and importance in modern manufacturing and fabrication processes. Here are some common applications:
- 3D Carving and Sculpting: 4-axis CNC routers are widely used in woodworking, sculpting, and prototyping industries to create intricate three-dimensional shapes and designs with high precision. This includes producing decorative elements, art pieces, and architectural components.
- 3D model: The 4-axis CNC router can rotate the spindle ±90°, making it suitable for processing simple 3D models.
- Mold Making: Manufacturing molds for injection molding, vacuum forming, or other molding processes can benefit from the capabilities of a 4-axis CNC router. These machines can produce complex mold designs with precise details and contours, suitable for producing a wide range of plastic, metal, or composite parts.
- Custom Furniture and Cabinetry: Woodworking shops often use 4-axis CNC routers to produce custom furniture pieces and cabinetry with intricate designs, curved edges, and unique shapes. This includes carving ornamental details, creating curved profiles, and machining complex joints.
- Prototyping and Model Making: In industries ranging from product design to architectural modeling, 4-axis CNC routers are used to create prototypes and models of various shapes and sizes with high accuracy. These machines can accurately replicate intricate designs, allowing for rapid prototyping and iterative design processes.
- Sign Making and Engraving: The versatility of 4-axis CNC routers makes them suitable for sign making, engraving, and artistic applications. They can produce detailed signage, plaques, and decorative elements on a variety of materials including wood, plastic, metal, and composites.
- Educational and Research Purposes: 4-axis CNC routers are also used in educational institutions and research facilities for teaching purposes and conducting experiments. They provide students and researchers with hands-on experience in computer-aided design (CAD) and computer-aided manufacturing (CAM) processes, as well as exploring advanced machining techniques.
Programming and operation of 4-axis CNC router
Programming and operating a 4-axis CNC router requires a combination of technical knowledge, programming skills, and practical experience. In this section, we’ll explore the key aspects of programming and operation for a 4-axis CNC router. By following these steps and best practices, you can effectively program and operate a 4-axis CNC router to produce high-quality machined parts and components with precision and efficiency.
Toolpath Strategies for 4-axis Operations
- Indexed Machining: This involves dividing the machining process into multiple setups, each with a different rotational position of the workpiece. Toolpaths are generated for each indexed position to machine the desired features. This method is suitable for parts that can be machined in segments or require machining from different angles.
- Continuous Machining: In continuous machining, the toolpath is designed to move smoothly along the surface of the workpiece while simultaneously rotating it. This allows for the machining of complex shapes and contours without the need for multiple setups. Continuous toolpaths are often used for sculpting, engraving, and 3D surface machining.
- Swarf Machining: Swarf machining involves using the side of the cutting tool to remove material in a slicing motion. This strategy is commonly used for roughing operations where material needs to be removed quickly and efficiently. Swarf machining can be performed with the workpiece tilted or rotated to access different areas.
Workholding Solutions for 4-axis Machining
- Rotary Tables: Rotary tables are commonly used to hold cylindrical or symmetric workpieces for 4-axis machining. They allow the workpiece to be rotated around its axis, providing access to multiple sides for machining.
- Indexers: Indexers are similar to rotary tables but are specifically designed for indexing the workpiece to precise angular positions. They can be integrated into the machine tool or used as standalone fixtures.
- Custom Fixtures: Custom fixtures can be designed to hold complex-shaped workpieces for 4-axis machining. These fixtures may incorporate clamps, vises, or other mechanisms to secure the workpiece in the desired orientation.
- Vacuum Chucks: Vacuum chucks can be used to hold flat or thin workpieces securely during machining. They provide uniform clamping force across the entire surface of the workpiece, eliminating the need for traditional mechanical clamps.
Programming and G-Code Considerations
- Axis Definitions: Ensure that the machine’s controller is properly configured to recognize the additional axis (typically the A or B axis) and define its orientation and range of motion.
- Post-Processor Selection: Use a post-processor that is specifically designed for 4-axis machining to generate G-code compatible with your machine tool. The post-processor will convert the toolpaths generated by the CAM software into machine-specific code.
- Coordinate System Setup: Establish a consistent coordinate system that aligns with the machine’s axes and the orientation of the workpiece. This will ensure accurate toolpath generation and machining.
- Toolpath Optimization: Optimize toolpaths to minimize unnecessary movements and reduce cycle times. Consider factors such as tool access, cutter engagement, and chip evacuation when generating toolpaths for 4-axis machining.
- Simulations and Verification: Before running the program on the machine, simulate the toolpaths using CAM software or machine simulation software to verify the machining process and detect any potential collisions or errors.
- Post-Processing Optimization: Fine-tune the post-processor settings to optimize the G-code output for your specific machine tool and controller. This may involve adjusting parameters such as feed rates, spindle speeds, and tool change sequences.
Optimized CNC router settings for 4-axis machining
Optimizing CNC router settings for 4-axis machining involves adjusting various parameters to achieve the best possible performance, accuracy, and efficiency. Here’s a comprehensive guide on how to optimize CNC router settings for 4-axis machining.
- Spindle Speed and Feed Rate: Adjust spindle speed and feed rate settings based on the material being machined, the type of cutting tool used, and the complexity of the geometry. Higher spindle speeds are generally used for softer materials, while lower speeds are preferred for harder materials to prevent tool wear and overheating. Adjust feed rates to achieve optimal chip load and material removal rates without putting excessive stress on the tool or workpiece.
- Tool Selection and Toolpath Optimization: Choose the appropriate cutting tools for the specific machining operation and material. Consider factors such as tool geometry, coating, and cutting parameters. Optimize toolpaths to minimize tool changes, reduce air cutting, and maximize machining efficiency. Use CAM software to generate toolpaths that take advantage of the 4-axis movement for complex geometries.
- Acceleration and Deceleration: Adjust acceleration and deceleration settings to ensure smooth and consistent motion of the machine. Avoid sudden changes in speed or direction that could cause vibration, chatter, or tool deflection. Optimize acceleration and deceleration parameters to minimize cycle times while maintaining accuracy and surface finish.
- Toolpath Smoothing and Contouring: Use toolpath smoothing algorithms to optimize toolpath motion and minimize jerky movements. Smoother toolpaths result in improved surface finish and reduced tool wear. Employ contouring strategies to maintain consistent cutter engagement and minimize tool deflection. This is particularly important for 4-axis machining, where tool orientation can vary during cutting.
- Coolant and Lubrication: Use coolant or lubrication as needed to reduce heat buildup, improve chip evacuation, and prolong tool life. Adjust coolant flow rates and nozzle positions to ensure effective cooling and chip removal. Consider the type of coolant or lubricant suitable for the material being machined and the cutting tool used.
- Workholding and Fixture Design: Ensure that workholding fixtures provide adequate clamping force and stability to prevent movement or vibration during machining. Use precision alignment tools to accurately position the workpiece relative to the machine’s axes. Design custom fixtures or use standard workholding solutions that accommodate the rotational movement of the workpiece in 4-axis machining.
- Tool Length Offsets and Compensation: Calibrate tool length offsets accurately to ensure that the tooltip is positioned correctly relative to the workpiece surface. Use a tool presetter or touch probe to measure tool lengths and input them into the machine controller. Apply tool length compensation in the CAM software to account for variations in tool length and ensure accurate machining results.
- Simulation and Verification: Before running the machining program on the CNC router, simulate the toolpaths using CAM software or machine simulation software. Verify that the toolpaths are free of errors, collisions, and excessive tool deflection. Perform dry runs or test cuts to validate the machining program and make any necessary adjustments before machining the actual workpiece.
By optimizing CNC router settings for 4-axis machining according to these guidelines, you can achieve enhanced performance, accuracy, and efficiency in your machining operations. Regular monitoring, testing, and refinement of settings will help you fine-tune your processes and maximize the capabilities of your CNC router.
Challenges in 4-axis CNC routing
4-axis CNC routing offers significant advantages in terms of versatility and complexity of machining operations, but it also presents unique challenges and considerations that operators must address to achieve optimal results. Here are some of the key challenges and considerations in 4-axis CNC routing:
- Programming Complexity: One of the primary challenges in 4-axis CNC routing is the increased programming complexity compared to traditional 3-axis routing. Generating toolpaths that effectively utilize the additional axis of rotation requires advanced CAD/CAM skills and knowledge of multi-axis machining strategies. This can be challenging, particularly for intricate geometries and multi-sided machining operations.
- Machine Calibration and Accuracy: Maintaining precise alignment and calibration of your CNC router’s axes is key to ensuring accurate machining results in 4-axis CNC routing. Any inaccuracies or misalignments can lead to dimensional errors, surface finish issues, and scrapped parts.
- Collision Avoidance: With the addition of a rotational axis, the risk of tool collisions with the workpiece or machine components increases in 4-axis CNC routing. Operators must carefully plan toolpaths and verify clearance to prevent collisions and minimize the risk of damage to the machine or workpiece.
- Surface Finish and Quality: Achieving a high-quality surface finish can be challenging in 4-axis CNC routing, particularly in areas where the tool orientation changes rapidly. Optimizing toolpaths, feed rates, and spindle speeds can minimize tool marks, chatter, and other surface imperfections.
- Chip Evacuation: Proper chip evacuation becomes more challenging in 4-axis CNC routing, especially when machining deep pockets or cavities. Chips can become trapped or interfere with the cutting tool, leading to poor surface finish, tool wear, or tool breakage. Adequate coolant flow and chip evacuation strategies must be implemented to ensure efficient chip removal and prevent recutting.
- Operator Training and Skill: Operating a 4-axis CNC router requires specialized training and expertise due to the increased complexity of setup, programming, and operation. Operators must be proficient in multi-axis programming, machine operation, troubleshooting, and maintenance to overcome the unique challenges associated with 4-axis routing.
Despite these challenges, advancements in CNC technology, software capabilities, and machining techniques continue to address many of the complexities associated with 4-axis CNC routing. With proper training, equipment, and problem-solving skills, manufacturers can effectively overcome these challenges and harness the full potential of 4-axis CNC routing for a wide range of applications.
Summarize
In the ever-evolving landscape of manufacturing, 4-axis CNC routers stand as a testament to innovation and precision engineering. With their ability to navigate complex geometries and produce intricate designs with utmost accuracy, these advanced machining tools have become indispensable in a wide range of industries. As technology continues to advance and new applications emerge, the role of 4-axis CNC routers in shaping the future of manufacturing is poised to expand further, unlocking new possibilities and pushing the boundaries of what is achievable in the realm of precision machining.
At AccTek CNC, we specialize in delivering solutions tailored to meet the diverse production requirements of our clientele. With our commitment to excellence and innovation, we take pride in offering a comprehensive range of CNC routers designed to elevate your manufacturing capabilities. Our extensive product lineup includes versatile 3-axis, 4-axis, and 5-axis CNC routers, meticulously engineered to deliver unparalleled precision and efficiency across various industries. Whether you’re a seasoned professional or a budding entrepreneur, our state-of-the-art machines empower you to unleash your creativity and maximize production output like never before. Contact us online to get your own customized CNC router solution.