- 4-7 Min Read
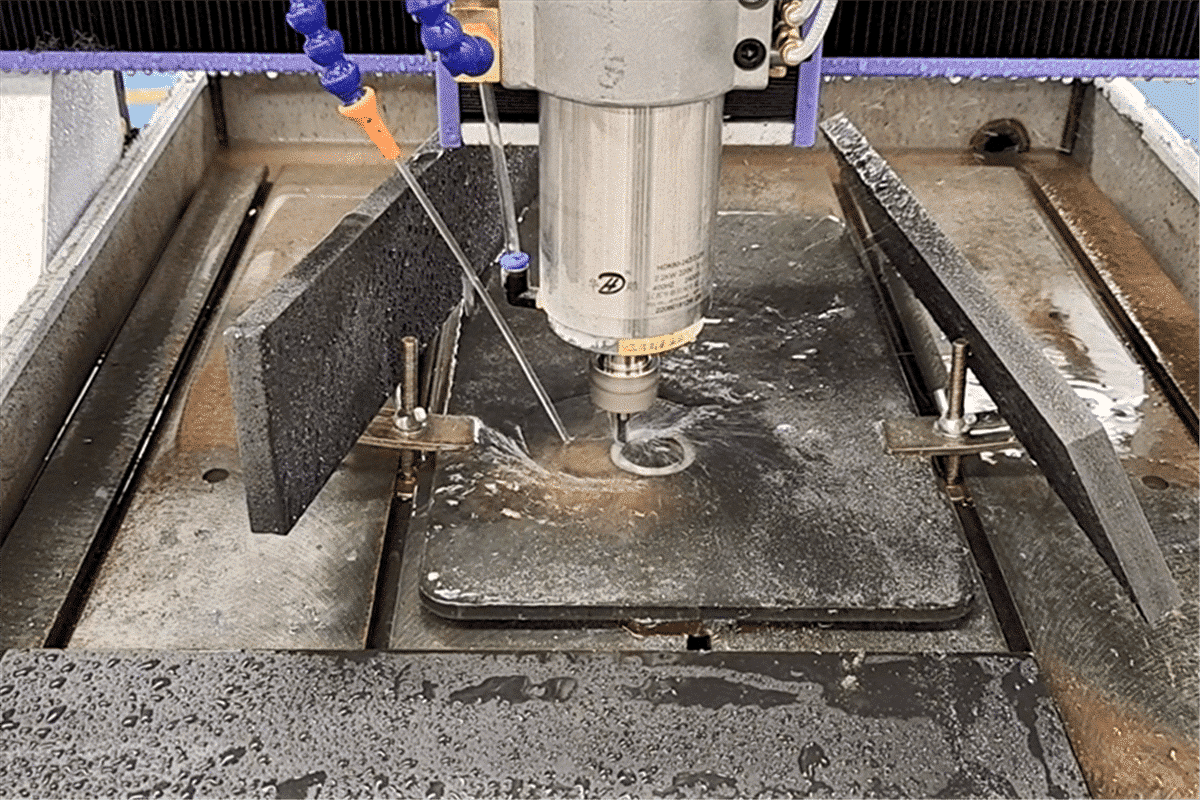
In the realm of Computer Numerical Control (CNC) machining, the pursuit of impeccable surface finish stands as a paramount objective for manufacturers across industries. Within the realm of CNC router machining specifically, achieving optimal surface finish demands a nuanced understanding of the myriad factors at play. From the selection of cutting tools to the intricacies of toolpath optimization, each element exerts its influence on the final surface quality of machined parts.
In this article, we embark on a comprehensive exploration of the diverse factors that significantly impact surface finish in CNC router machining. From the selection of cutting tools to the optimization of cutting parameters and the nuances of material properties, each element contributes to the final surface quality in its unique way. By dissecting these factors and elucidating their roles in the machining process, this article aims to equip CNC operators, engineers, and enthusiasts with the knowledge necessary to achieve superior surface finishes consistently. Through a deeper understanding of the intricacies involved, practitioners can refine their machining techniques, mitigate challenges, and unlock new possibilities in CNC router machining.
Understanding Surface Finish
In CNC router machining, surface finish refers to the quality and texture of the surface of a machined part after the CNC router has processed it. It encompasses various characteristics such as smoothness, roughness, uniformity, and the absence of defects like scratches, burrs, or tool marks. Surface finish is an important aspect of part quality, and its impact is reflected in the following points:
- Aesthetic appeal: A smooth and uniform surface finish enhances the visual appearance of a product, making it more attractive to consumers.
- Functionality: Surface finish affects the performance and functionality of components, such as reducing friction, improving wear resistance, and facilitating proper sealing or bonding.
- Compatibility: Surface finish requirements may vary depending on the application and the materials involved. For instance, certain applications may require a specific surface roughness to ensure proper adhesion between mating components.
- Manufacturing processes: Different manufacturing processes produce varying surface finishes. Engineers and designers must consider these surface characteristics when selecting manufacturing methods to meet product specifications and requirements.
Surface finish can be influenced by factors such as the type of material being processed, the machining or finishing techniques used, the condition of the cutting tools, and environmental factors such as temperature and humidity. Achieving the desired surface finish involves careful consideration of various parameters and the selection of appropriate manufacturing processes and techniques.
Factors Affecting Surface Finish
Surface finish in CNC router machining is influenced by a multitude of factors, each playing a role in determining the quality and characteristics of the final surface. Here are the key factors affecting surface finish:
- Tool Selection: The type of cutting tool used, including its material, geometry, and sharpness, can significantly impact surface finish. A sharp tool with appropriate geometry for the material being cut will generally produce better results.
- Tool Speed and Feed Rate: The spindle speed (RPM) and feed rate (how fast the tool moves through the material) affect the cutting forces and heat generation, which in turn influence surface finish. These parameters need to be adjusted appropriately according to the material being processed to obtain the best results.
- Material Properties: The type and characteristics of the material being machined will affect the surface finish. Harder materials may require different cutting strategies compared to softer materials.
- Fixturing and Workholding: Proper fixturing and workholding methods ensure that the material being cut remains stable and secure during machining. Poor fixturing can lead to vibration and chatter, negatively impacting surface finish.
- MachineRigidity and Stability: The rigidity and stability of the CNC router itself play a significant role. A stable and rigid machine is better able to maintain consistent cutting forces, resulting in a better surface finish.
- Cutting Strategy: The cutting strategy employed, such as the depth of cut, stepover, and cutting direction, can affect the surface finish. Optimizing these parameters for the specific part geometry and material can improve surface quality.
- Toolpath Optimization: The toolpath generated by CAM software can impact surface finish. Smooth, continuous toolpaths with minimal sudden changes in direction can result in better surface finish compared to erratic toolpaths.
- Coolant/Lubrication: Proper coolant or lubrication application can help dissipate heat and reduce friction during machining, leading to improved surface finish, especially in materials prone to heat buildup.
- Tool Wear: As cutting tools wear over time, they may produce inferior surface finishes. Regular maintenance and tool replacement are beneficial for consistent quality.
- Operator Skill and Experience: The skill and experience of the CNC operator also play a role in achieving optimal surface finish. Experienced operators can adjust cutting parameters and troubleshoot issues more effectively.
How to Solve Surface Finish Issues
To solve surface finish issues in CNC routing effectively, you’ll need to follow a systematic approach. Here’s a step-by-step guide. By following these steps and adopting a systematic approach to problem-solving, you can desired quality standards for your machined components.
Identify the Surface Finish Issue
- Carefully examine the machined surface to identify the specific problem(s) present. Common issues include the following situations:
- Tool marks: Visible lines or ridges left on the surface due to improper toolpath or dull cutting tools.
- Burn marks: Darkened or discolored areas on the surface caused by excessive heat during machining.
- Chatter marks: Irregular patterns or waves on the surface caused by vibrations during cutting.
- Tear-out: Fibers or chunks are torn out from the surface, typically seen in wood or composite materials.
- Rough surface: Uneven or jagged surface texture caused by improper feed rates, cutting speeds, or tool selection.
Analyze the Root Cause
- Determine the factors contributing to the surface finish problem. This involves examining the following items:
- Machine rigidity: Check for any issues with machine stiffness or stability that may cause vibrations or chatter during cutting.
- Material properties: Consider the hardness, density, and composition of the material being routed, as these factors can influence cutting performance.
- Toolpath programming: Review the CAM programming for any errors or inefficiencies that may lead to poor surface finish.
- Workholding: Ensure proper clamping or fixturing of the workpiece to prevent movement or vibration during cutting.
- Operator skill: Evaluate the operator’s proficiency in CNC routing techniques and troubleshoot surface finish issues.
Make Necessary Adjustments
- Based on the root cause analysis, make adjustments to address the identified issues. Here are some common adjustments you can make:
- Tool selection: Choose the appropriate tool type, geometry, and sharpness for the material and machining operation.
- Cutting parameters: Adjust spindle speed, feed rate, and depth of cut to optimize material removal while maintaining surface quality.
- Toolpath optimization: Modify toolpaths to minimize tool retractions, optimize cutting direction, and reduce vibrations.
- Coolant/lubrication: Use coolant or lubricant to reduce heat buildup and prevent burning or tool wear.
- Climb milling: Consider using climb milling to achieve smoother cutting action and minimize tool marks.
- Tool maintenance: Regularly inspect and replace dull or worn cutting tools to maintain optimal cutting performance.
Continuous Improvement and Optimization
- Perform Test Runs: After making adjustments, run test cuts to evaluate the impact on the surface finish. Make further adjustments as necessary until the desired surface quality is achieved.
- Monitor and Maintain: Regularly monitor surface finish during machining operations and implement preventive maintenance practices to ensure consistent performance. Periodically inspect and maintain machine components, cutting tools, and workholding fixtures to prevent issues that could affect surface finish.
- Operator Training: Provide training to machine operators on best practices for achieving and maintaining high-quality surface finishes. This includes proper machine setup, tool handling, and troubleshooting techniques.
- Document and Improve: Keep records of surface finish issues, root causes, and solutions implemented. Use this information to refine machining processes, optimize tooling and cutting parameters, and continuously improve surface finish quality over time.
Summarize
In today’s competitive manufacturing landscape, surface finish excellence is not just a measure of craftsmanship but also a hallmark of efficiency and innovation. By prioritizing surface finish quality, manufacturers can differentiate themselves in the marketplace. Understanding the factors that affect surface finish and following a systematic approach to problem-solving, manufacturers can enhance surface finish quality, reduce production costs, and meet the evolving demands of customers and industries.
AccTek CNC provides you with various types of CNC routers to meet your needs for cutting different material finishes. Whether you’re working with wood, metal, plastic, or composite materials, our extensive lineup of CNC routers ensures that you have the right equipment for the job. From entry-level models ideal for small-scale workshops to high-performance machines tailored for industrial production environments, AccTek CNC has the best solution to suit your specific application and budget.