- 8-12 Min Read
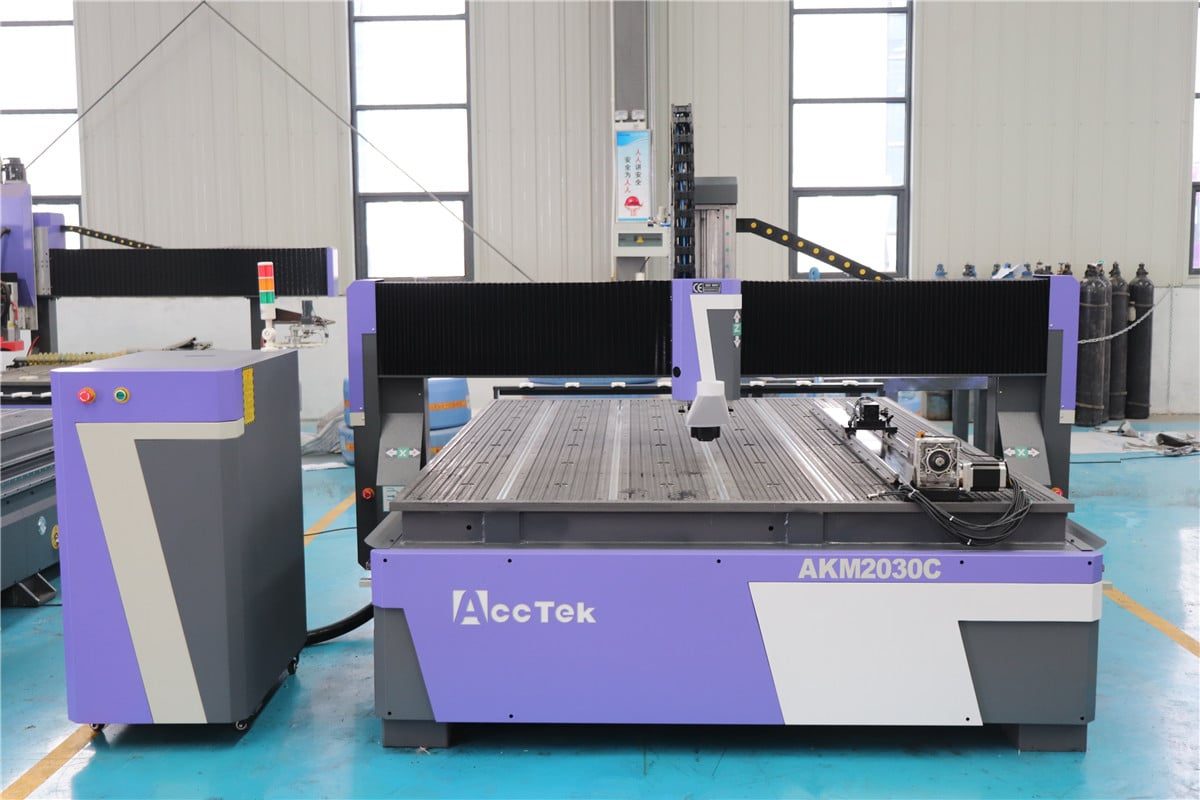
As the global pursuit of sustainable practices intensifies, industries are increasingly scrutinizing their environmental footprint. In the realm of manufacturing and woodworking, Computer Numerical Control (CNC) routers have emerged as indispensable tools, revolutionizing precision and efficiency in material shaping. However, as with any technological advancement, the environmental implications of CNC router usage warrant careful examination. From energy consumption to material waste and emissions, understanding the ecological ramifications of CNC router operations is beneficial for fostering a more sustainable approach to manufacturing. In this article, we elaborate on the environmental impact of using CNC routers from many aspects. By understanding these factors, we explore strategies for mitigating the environmental harm associated with their use, ultimately striving for a more sustainable approach to CNC machining.
The Importance of Assessing Environmental Impacts
The CNC routing process revolutionizes manufacturing by combining computer technology with precision cutting capabilities. This process begins with a digital design created using Computer-Aided Design (CAD) software, which guides the CNC router in executing precise movements along multiple axes. As the cutting tools move across the workpiece, they remove material according to the specifications outlined in the design file, resulting in intricately carved patterns, precise cuts, and smooth finishes. The importance of assessing the environmental impact of CNC routing is reflected in various aspects of the manufacturing process. Here are several key areas where this importance becomes evident:
- Resource Consumption: Assessing environmental impact involves evaluating the consumption of resources such as raw materials, energy, and water. By understanding the quantities of these resources required for CNC routing operations, manufacturers can identify opportunities to optimize usage, reduce waste, and minimize the depletion of natural resources.
- Energy Efficiency: CNC routers are significant consumers of electricity, particularly during the machining process. Assessing environmental impact involves scrutinizing energy usage patterns and identifying opportunities for improving energy efficiency. This may include optimizing machine settings, implementing energy-saving technologies, and scheduling operations to minimize energy demand during peak hours.
- Waste Generation and Management: CNC routing generates various types of waste, including sawdust, chips, and coolant. Assessing environmental impact entails evaluating the quantity and composition of waste generated and implementing strategies to reduce, reuse, and recycle waste materials. Proper waste management practices help minimize pollution and conserve resources.
- Chemical Usage and Emissions: Some CNC routing processes involve the use of chemicals such as adhesives, sealants, and cutting fluids. Assessing environmental impact requires evaluating the types and quantities of chemicals used, as well as their potential environmental and health effects. Manufacturers can minimize chemical usage and emissions by adopting eco-friendly alternatives, implementing proper chemical management practices, and controlling emissions through ventilation and filtration systems.
- Air and Water Quality: Assessing environmental impact involves monitoring and controlling emissions of pollutants such as particulate matter, volatile organic compounds (VOCs), and greenhouse gases. Manufacturers must implement measures to minimize air and water pollution, protect ecosystems, and ensure compliance with environmental regulations.
- Lifecycle Analysis: Assessing environmental impact in CNC routing involves considering the entire lifecycle of products, from raw material extraction and manufacturing to use, disposal, and recycling. By conducting lifecycle analyses, manufacturers can identify opportunities to reduce environmental impact at every stage of the product lifecycle, leading to more sustainable manufacturing practices.
Assessing the environmental impact of CNC routing is beneficial for minimizing resource consumption, waste generation, and pollution, and for promoting more sustainable manufacturing practices that protect the environment and safeguard human health.
The Impact of Using CNC Routers on The Environment
While CNC routers have propelled advancements in production capabilities and product quality, it is imperative to critically examine their environmental implications. By comprehensively examining these aspects, stakeholders can gain insights into the environmental challenges posed by CNC routers and identify opportunities for mitigating their adverse effects. The specific impact is reflected in the following aspects.
Raw Material Consumption
- Material Selection: The choice of materials used in CNC routing can significantly impact the environment. Some materials, such as certain types of plastics or composites, may be non-biodegradable or have high carbon footprints due to their manufacturing processes. Additionally, the sourcing of materials can contribute to deforestation or other environmental degradation if not managed sustainably.
- Material Waste: Despite the precision of CNC routers, there is still a degree of material waste involved in the process. Offcuts, scrap material, and imperfect pieces are often generated during cutting operations. This excess material not only represents wasted resources but also contributes to the overall environmental footprint of the manufacturing process.
Energy Consumption
- Power Requirements: CNC routers typically require significant amounts of electricity to operate, particularly during cutting and milling processes. The motors, spindles, and other components of the machine draw substantial power, especially in industrial-scale operations.
- Energy Types: Many CNC routing facilities rely on electricity generated from fossil fuels such as coal, natural gas, and oil. Burning these fuels releases carbon dioxide and other pollutants into the atmosphere, contributing to air pollution, climate change, and environmental degradation. While renewable energy sources such as wind, solar, and hydroelectric power offer cleaner alternatives to fossil fuels, their adoption in the manufacturing sector, including CNC routing, remains limited.
Emissions and Air Quality
- Dust and Particulate Matter Emissions: CNC routers generate dust and particulate matter as a byproduct of material cutting and milling processes. These airborne particles can include wood dust, metal shavings, plastic fragments, and other fine particulates, depending on the material being processed. Dust and particulate matter emissions from CNC routing can contribute to environmental contamination. Fine particles can settle on surfaces, soil, and water bodies, affecting ecosystems and potentially harming wildlife.
- Volatile Organic Compound (VOC) Emissions: VOCs are organic chemicals that can easily evaporate into the air at room temperature. CNC routing processes involving certain materials, such as wood composites, plastics, and adhesives, may release VOCs into the air during cutting, milling, and finishing operations. VOCs can react with other air pollutants to form smog and ground-level ozone, which can exacerbate respiratory conditions and cause environmental damage.
Water Consumption
- Coolant Systems: CNC routers often employ coolant systems to reduce friction, dissipate heat, and lubricate cutting tools during machining processes. Over time, the buildup of contaminants can degrade coolant performance and compromise machining quality. Improper disposal of coolant fluids can pose environmental hazards, especially if they contain toxic chemicals or heavy metals. Contaminated coolant fluids can pollute soil and water sources if they are discharged into the environment without adequate treatment.
- Wastewater Management: CNC routing operations generate wastewater as a result of coolant system maintenance, tool cleaning, and equipment rinsing. This wastewater may contain suspended solids, oils, greases, and other contaminants picked up during machining processes. Discharging untreated or inadequately treated wastewater into municipal sewers or natural water bodies can pollute surface water and groundwater. Contaminants such as heavy metals, oils, and chemicals can harm aquatic ecosystems, disrupt wildlife habitats, and pose risks to human health.
Waste Generation and Disposal
- Material Scraps: Waste Generation: CNC routing processes often result in the generation of material scraps and offcuts, especially during initial setup, tool changes, and finishing operations. Improper disposal of material scraps can exacerbate environmental pollution and waste management challenges. Landfilling, incineration, or other disposal methods may result in the release of greenhouse gases, leachate contamination, and habitat destruction if not managed responsibly.
- Tools and Consumables: Some CNC routing tools and consumables may contain hazardous materials such as heavy metals, volatile organic compounds (VOCs), or toxic chemicals. Improper handling, storage, or disposal of these materials can pose risks to human health and the environment.
How to reduce the impact of CNC router on the environment
After understanding the impact of CNC routers on the environment, in this section, we endeavor to explore and elucidate actionable strategies for reducing the environmental impact of CNC routers, encompassing various dimensions of operation, from material selection and process optimization to waste management and energy conservation. By embracing a holistic approach to sustainability, organizations can mitigate the adverse effects of CNC router operations on the environment while fostering efficiency, innovation, and responsible stewardship of natural resources.
Sustainable material choices
- Material Selection: Opt for eco-friendly materials such as sustainably sourced wood, recycled plastics, or biodegradable composites. Consider the entire lifecycle of the material, including its production, use, and disposal.
- Waste Reduction: Implement strategies to minimize material waste, such as optimizing cutting paths, using nesting techniques to maximize material utilization, and reusing or recycling scrap material wherever possible.
Energy Efficiency Improvements
- Invest in high-tech CNC router: Invest in energy-efficient CNC router technologies, including advanced motor controls, regenerative braking systems, and optimized cutting algorithms. Regular maintenance and calibration can also help maximize energy efficiency.
- Renewable Energy Adoption: Transitioning to renewable energy sources such as solar, wind, or hydroelectric power can significantly reduce the environmental footprint of CNC routing operations. Consider onsite renewable energy generation or sourcing electricity from renewable energy providers.
- Demand Response and Load Management: Implement demand response programs to shift non-essential CNC routing tasks to off-peak hours when electricity demand and costs are lower. Load management strategies such as smart scheduling and power factor correction can help optimize energy usage and reduce peak demand.
Dust and Emissions Control
- Dust Collection Systems: Install and maintain effective dust collection and filtration systems to capture airborne particles generated during CNC routing processes. Proper ventilation and exhaust systems can help minimize indoor air pollution and protect worker health.
- Material Selection: Choose materials with lower dust and VOC emissions potential, such as low-emission wood products and environmentally friendly adhesives. Avoid materials containing hazardous substances or known carcinogens.
- Emission Control Technologies: Invest in emission control technologies such as catalytic converters, scrubbers, and thermal oxidizers to reduce VOC emissions from CNC routing operations. Regular equipment maintenance and monitoring can ensure optimal performance and compliance with regulatory standards.
Water Resources Management
- Coolant Fluid Management: Implement proper coolant fluid management practices, including regular monitoring, filtration, and replenishment of coolant fluids. Recycling and reusing coolant fluids can help minimize waste generation and reduce environmental impact.
- Pollution Prevention: Employ pollution prevention measures such as spill containment, leak detection, and equipment maintenance to prevent coolant fluid spills and releases. Implement spill response procedures to promptly address any accidental releases and minimize environmental damage.
- Wastewater Treatment: Install onsite wastewater treatment systems or utilize professional wastewater treatment services to treat contaminated wastewater before discharge. Treatment methods such as sedimentation, filtration, and chemical treatment can remove contaminants and ensure compliance with regulatory standards.
- Resource Conservation: Explore alternatives to traditional coolant fluids, such as bio-based or eco-friendly formulations, to minimize environmental impact and improve sustainability. Implement water conservation measures to reduce overall water usage and wastewater generation in CNC routing operations.
Waste Reduction And Recycling
- Material Optimization: Optimize cutting strategies, nesting techniques, and material utilization to minimize the generation of material scraps and offcuts. Design products with CNC routing efficiency in mind to reduce waste and maximize resource efficiency.
- Recycling and Reuse: Implement recycling programs for material scraps, tools, and consumables wherever possible. Properly segregate and dispose of hazardous materials. Additionally, explore opportunities to reuse or repurpose scrap materials and worn tools in other manufacturing processes or secondary applications.
- Waste Reduction: Implement lean manufacturing principles and continuous improvement initiatives to identify and eliminate sources of waste in CNC routing operations. Invest in advanced machining technologies and tooling solutions that extend tool life and reduce consumable usage.
Comply With Environmental Regulations
- Environmental Compliance: Comply with environmental regulations and standards regarding material sourcing, waste management, and emissions control. Invest in technologies and practices that minimize environmental impacts, such as dust collection systems to mitigate air pollution.
- Consumer Awareness: Educate consumers about the environmental implications of CNC routing and encourage responsible purchasing decisions. Promote the use of eco-friendly materials and support companies that prioritize sustainability in their manufacturing processes.
Organize Staff Training
- Environmental Awareness Training: Provide comprehensive training sessions to raise awareness among employees about the environmental impacts of CNC router operations. Highlight the significance of environmental regulations and compliance standards relevant to CNC routing operations. Ensure that employees understand their roles and responsibilities in adhering to these regulations to protect the environment.
- Energy Saving Practical Training: Train employees on proper waste management practices and environmental stewardship. Emphasize the importance of proper material storage, handling, and disposal practices to prevent contamination and minimize environmental impact.
Summarize
While the utilization of CNC routers undoubtedly offers immense benefits in terms of precision, efficiency, and productivity, it is imperative to recognize and address the environmental impacts associated with their operation. The use of CNC routers can exert significant pressure on the environment if not managed responsibly. The quest for environmental sustainability in CNC router operations is not merely a moral imperative but also an economic necessity and a strategic advantage. By aligning business objectives with environmental stewardship, companies can enhance their competitiveness, build resilience, and create long-term value for stakeholders and society as a whole.
AccTek CNC is a well-known CNC router manufacturer and supplier in China. Whether you’re engraving intricate designs, carving complex shapes, or cutting precise components, our CNC routers deliver unparalleled accuracy, speed, and reliability to streamline your machining processes and maximize productivity. Explore our range of CNC routers today and discover how our machines can elevate your machining capabilities and take your business to new heights.