- 8-12 Min Read
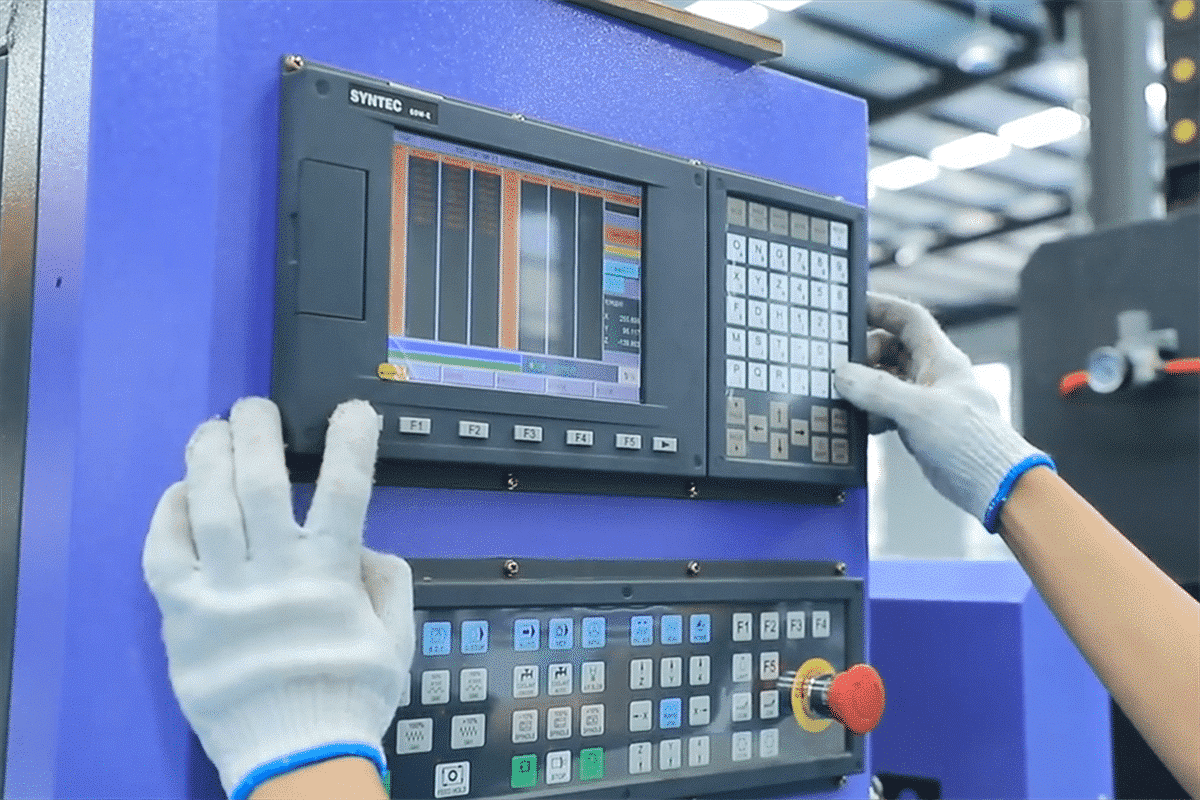
In the world of CNC (Computer Numerical Control) machining, where precision meets creativity, the choice of file format holds immense significance. From transforming digital designs into tangible creations to orchestrating intricate toolpaths, the file format serves as the cornerstone of every CNC routing project. From intricate 3D sculptures to precision-cut signage, each file format brings its own set of capabilities and considerations to the table. Whether you are a seasoned professional or a novice enthusiast, understanding the various file formats available and their suitability for CNC routers will help you get the optimal results. In this comprehensive guide, we will delve into the intricacies of different file formats, discussing their advantages, limitations, and best practices for CNC routing. With the right file format and preparation techniques, you can unleash your creativity and bring your digital designs to life with precision and confidence on your CNC router.
The impact of file format on CNC routing
At the heart of every CNC routing project lies a digital file containing the design or instructions for the machine to follow. The importance of selecting the correct file format for CNC routing cannot be overstated, as it directly influences the efficiency, accuracy, and overall success of the machining process. The impact of file format on CNC routing encompasses several critical aspects:
- Compatibility with CNC Software and Machinery: CNC routers rely on specific file formats to interpret design instructions and generate toolpaths. Different CNC routers and their associated control software may have specific file format requirements. Choosing a compatible file format ensures seamless integration with the CNC software, minimizing the risk of errors or data loss during file transfer. Compatibility issues can lead to time-consuming conversions or rework, hindering productivity and delaying project timelines.
- Preservation of Precision and Accuracy: Different file formats offer varying levels of precision in representing design geometry. Vector-based formats, such as DXF (Drawing Exchange Format) or DWG (Drawing), preserve precise geometric information, allowing for accurate reproduction of shapes, curves, and dimensions on the workpiece. This facilitates achieving tight tolerances and high-quality surface finishes in CNC machining.
- Complexity and Versatility of Machining Operations: Different file formats offer varying levels of support for complex geometries and machining operations. Three-dimensional formats like STL (Stereolithography) enable the fabrication of intricate 3D models and organic shapes, while 2D formats like DXF are suitable for flat profiles and engraving tasks. Selecting the appropriate format based on the complexity of the design ensures efficient utilization of the CNC router’s capabilities and minimizes unnecessary processing time.
- Ease of Editing and Modification: The selected file format should allow for easy editing and modification of design geometry as needed. CAD (Computer-Aided Design) formats like STEP (Standard for the Exchange of Product Data) or IGES (Initial Graphics Exchange Specification) enable parametric modeling and precise manipulation of individual elements within the design. This facilitates iterative design processes and enables quick adjustments to accommodate changes or optimizations, reducing downtime and improving workflow efficiency.
- Workflow Integration and Streamlining: The chosen file format should seamlessly integrate into the overall CNC machining workflow, from design creation to toolpath generation and machining. Compatibility with CAD/CAM (Computer-Aided Manufacturing) software ensures smooth data exchange and streamlines the entire manufacturing process, from design creation to toolpath generation and machining. This promotes efficient collaboration between designers, engineers, and machinists, enabling faster decision-making and smoother project execution.
- Material and Machining Requirements: Different file formats may be better suited for specific materials or machining processes. G-Code, the language of CNC machines, allows for precise control over machining parameters and toolpaths, making it suitable for customizing machining strategies based on material properties and cutting conditions. Choosing the correct file format tailored to the material and machining requirements ensures optimal performance and quality in CNC routing, minimizing material waste and maximizing machining efficiency.
The impact of file format on CNC routing is multifaceted, encompassing factors such as compatibility, accuracy, and efficiency. While there is a myriad of file formats available, not all are suitable for CNC machining. By selecting the appropriate file format tailored to the specific needs of the project, manufacturers can maximize success in CNC machining operations, ultimately driving productivity and competitiveness in the manufacturing industry.
Common CNC File Formats
In the realm of CNC machining, there are several common file formats used to communicate design data to CNC routers. Each offers its own advantages and suitability for different types of designs and machining operations. In this section, we explore three file formats, providing insights into their definitions, purposes, advantages, and limitations in the context of CNC machining.
DXF (Drawing Exchange Format)
Definition
DXF is a vector-based file format developed by Autodesk for storing 2D CAD (Computer-Aided Design) drawings. It represents geometric shapes, lines, arcs, and text in a format that is easily readable by CNC routers and other CAD/CAM software.
Purpose
The primary purpose of DXF is to facilitate the exchange of design data between different CAD/CAM systems and CNC machines. It serves as a universal format for sharing 2D design information, making it ideal for cutting, engraving, and profiling tasks on CNC routers.
Advantages
- Widely supported: DXF is supported by a vast array of CAD/CAM software and CNC router controllers, ensuring compatibility across various platforms.
- Vector-based: DXF files preserve precise geometric information, allowing for accurate reproduction of shapes, curves, and dimensions on the workpiece.
- Editing flexibility: DXF files can be easily edited and modified using CAD software, enabling quick adjustments to accommodate design changes or optimizations.
Limitations
- Limited to 2D geometry: DXF is primarily suited for 2D CAD drawings and may not adequately represent complex three-dimensional shapes and surfaces.
- Lack of support for assemblies: DXF does not support assembly structures or hierarchical relationships between components, limiting its usefulness for complex mechanical designs.
DWG (Drawing)
Definition
DWG is another proprietary file format created by Autodesk, primarily used in their AutoCAD software. It is similar to DXF but offers more comprehensive support for both 2D and 3D geometries, including advanced modeling features and assembly structures.
Purpose
DWG serves as a versatile format for storing and exchanging design data in a wide range of industries, including architecture, engineering, and manufacturing. It is commonly used for creating detailed technical drawings, architectural plans, and mechanical assemblies.
Advantages
- Comprehensive support for 2D and 3D geometry: DWG files can represent complex three-dimensional shapes, surfaces, and assemblies, making them suitable for a wide range of design applications.
- Industry standard: DWG is widely adopted as the de facto standard for CAD data exchange, ensuring interoperability and compatibility with a vast ecosystem of software tools and CNC machining systems.
- Parametric modeling: DWG supports parametric modeling and constraints, enabling precise control over design dimensions and relationships between components.
Limitations
- Proprietary format: DWG is a proprietary file format owned by Autodesk, which may limit compatibility with non-AutoCAD software and CNC router controllers.
- File size and complexity: DWG files can become large and complex, especially for intricate assemblies and detailed designs, which may impact file transfer and processing times.
STL (Stereolithography)
Definition
STL is a file format commonly used in 3D printing and rapid prototyping, but it is also compatible with CNC routers. STL files represent 3D models as a series of interconnected triangles, known as a mesh.
Purpose
STL serves as a versatile format for storing and transferring 3D geometric data, making it suitable for machining complex three-dimensional shapes and surfaces on CNC routers.
Advantages
- Suitable for complex geometry: STL files can represent intricate 3D models and organic shapes with a high degree of fidelity, making them ideal for sculptural, artistic, and prototyping applications.
- Universally supported: STL is supported by a wide range of CAD/CAM software and CNC router controllers, ensuring compatibility across different platforms and systems.
- Mesh-based representation: STL files are lightweight and easy to process, making them suitable for rapid prototyping and manufacturing applications where speed and efficiency are paramount.
Limitations
- Lack of precision: STL files represent 3D models as a series of discrete triangles, which may result in a loss of geometric accuracy and resolution, particularly for curved surfaces and fine details.
- Limited editing capabilities: STL files are not easily editable or modifiable, as they lack the parametric and feature-based information found in CAD formats like DXF and DWG. This can make it challenging to make design changes or optimizations after the initial creation of the file.
Choosing the Right File Format
Choosing the best file format for your CNC router application requires careful consideration of several factors to ensure compatibility, accuracy, and efficiency in machining operations. Here are some key considerations to keep in mind:
- Understand CNC Router Requirements: Before selecting a file format, thoroughly understand the requirements and capabilities of your CNC router. Consider factors such as supported file formats, maximum part size, machining capabilities, and controller compatibility to ensure the chosen format aligns with theCNC router’s specifications.
- Evaluate Design Complexity: Assess the complexity of your design and the machining operations required. Choose a file format that best represents the geometric complexity of your part while considering the CNC router’s capabilities. For simple 2D profiles and engraving tasks, vector-based formats like DXF (Drawing Exchange Format) may suffice. For complex three-dimensional shapes and surfaces, consider formats like STL (Stereolithography).
- Consider Editing and Modification Needs: Anticipate potential design modifications or adjustments throughout the CNC machining process. Select a file format that allows for easy editing and modification using CAD software, especially if iterative design changes are expected. Parametric CAD formats like DWG offer greater flexibility for editing compared to mesh-based formats like STL.
- Account for Material and Machining Requirements: Consider the material properties and machining requirements of your project when choosing a file format. Certain formats may be better suited for specific materials or machining processes, such as high-speed cutting or multi-axis machining.
- Ensure Compatibility with Software: Verify that the chosen file format is compatible with your CAD/CAM software suite. Ensure seamless data exchange between design software and CNC router control software to prevent compatibility issues or data loss during file transfer. Additionally, consider the compatibility of the file format with any post-processing or simulation tools used in your workflow.
- Plan for Future Scalability: Anticipate future scalability and potential changes in your CNC machining requirements. Choose a file format that offers scalability and interoperability with other CAD/CAM systems, allowing for seamless integration of new technologies or equipment upgrades as your business grows.
- Consider File Size and Transfer Speed: Some formats may result in larger file sizes, which could impact transfer times and storage requirements. Opt for file formats that strike a balance between file size and quality to optimize efficiency in your CNC machining workflow.
- Perform Compatibility Testing: Before finalizing your choice of file format, perform compatibility testing with your CNC router and software environment. Verify that the file format produces accurate toolpaths, maintains design integrity, and achieves the desired machining results. Address any compatibility issues or discrepancies encountered during testing before proceeding with production.
The importance of hierarchical organization
Hierarchical organization is important when choosing the right file format for CNC routers because it helps ensure that the design data is structured in a way that can be easily interpreted and translated into tool paths and machining instructions. Here’s why hierarchical organization matters in this context:
- Efficient Tool Path Separation: CNC routers often require specific instructions for different machining operations, such as cutting, drilling, or engraving. Hierarchical organization enables the file format to store information about each machining operation separately, allowing the CNC software to generate optimized tool paths for each operation. This can lead to more efficient machining processes, reducing machining time and improving overall productivity. By choosing a file format that supports hierarchical organization, manufacturers can ensure that the CNC router can interpret the design data accurately and generate efficient tool paths for complex machining tasks.
- Material Considerations: Different materials require specific machining parameters and tooling considerations. Hierarchical organization in the file format allows CNC programmers to incorporate material considerations at each level of the design. This includes adjusting cutting speeds, feeds, and tool selection based on the material properties. By choosing a file format that supports hierarchical organization, manufacturers can easily adjust machining parameters to accommodate various materials, ensuring optimal cutting performance and surface finish.
- Ease of CNC Programming: Hierarchical organization simplifies CNC programming by breaking down the design into manageable components or features. This makes it easier for programmers to create tool paths and generate CNC code, as they can focus on individual sections of the design hierarchy. Additionally, hierarchical organization facilitates code reuse, as similar machining strategies can be applied to different parts of the design. By selecting a file format that supports hierarchical organization, manufacturers can streamline the CNC programming process, reduce errors, and enhance overall CNC system efficiency.
Best Practices for File Preparation
Regardless of the chosen file format, proper preparation helps ensure optimal results on your CNC router. Here are some best practices for file preparation:
- Clean Geometry: Ensure that the design geometry is free from errors, such as overlapping lines, gaps, or self-intersections. Use CAD software tools to repair and simplify the geometry before exporting to a CNC-compatible format.
- Scale and Units: Verify that the design is correctly scaled and aligned with the desired machining dimensions. Pay attention to units of measurement (e.g., inches or millimeters) to avoid scaling discrepancies during CNC machining.
- Toolpath Optimization: Optimize toolpaths and machining parameters based on the material properties and cutting conditions. Consider factors such as cutting speed, feed rate, and tool geometry to achieve the desired surface finish and dimensional accuracy.
- Simulation and Verification: Use simulation tools within your CAD/CAM software to visualize the machining process and detect any potential issues before sending the file to the CNC router. Verify toolpaths, collision avoidance, and material removal to ensure a smooth and error-free operation.
Summarize
Selecting the optimal file format for CNC router operations helps ensure precision, efficiency, and compatibility throughout the manufacturing process. By understanding the strengths and limitations of popular file formats such as DXF, DWG, and STL, manufacturers can make informed decisions tailored to their specific requirements. Factors such as geometry complexity, compatibility with design software, and CNC router capabilities should be carefully considered when choosing the most suitable format. Additionally, staying updated with advancements in software and technology can further enhance workflow and productivity. Ultimately, by prioritizing the selection of the right file format, manufacturers can streamline their CNC routing processes, minimize errors, and achieve superior results in their fabrication endeavors.
Renowned as a professional CNC router manufacturer, AccTek CNC specializes in providing users with high-quality machinery tailored to diverse processing requirements. With a comprehensive range including 3-axis, 4-axis, and 5-axis CNC routers, AccTek CNC ensures versatility and precision in every project. Whether you’re in woodworking, metalworking, or signage production, AccTek CNC’s lineup guarantees exceptional performance and efficiency. Trust in AccTek CNC for solutions that elevate your manufacturing capabilities to new heights.