- 6-9 Min Read
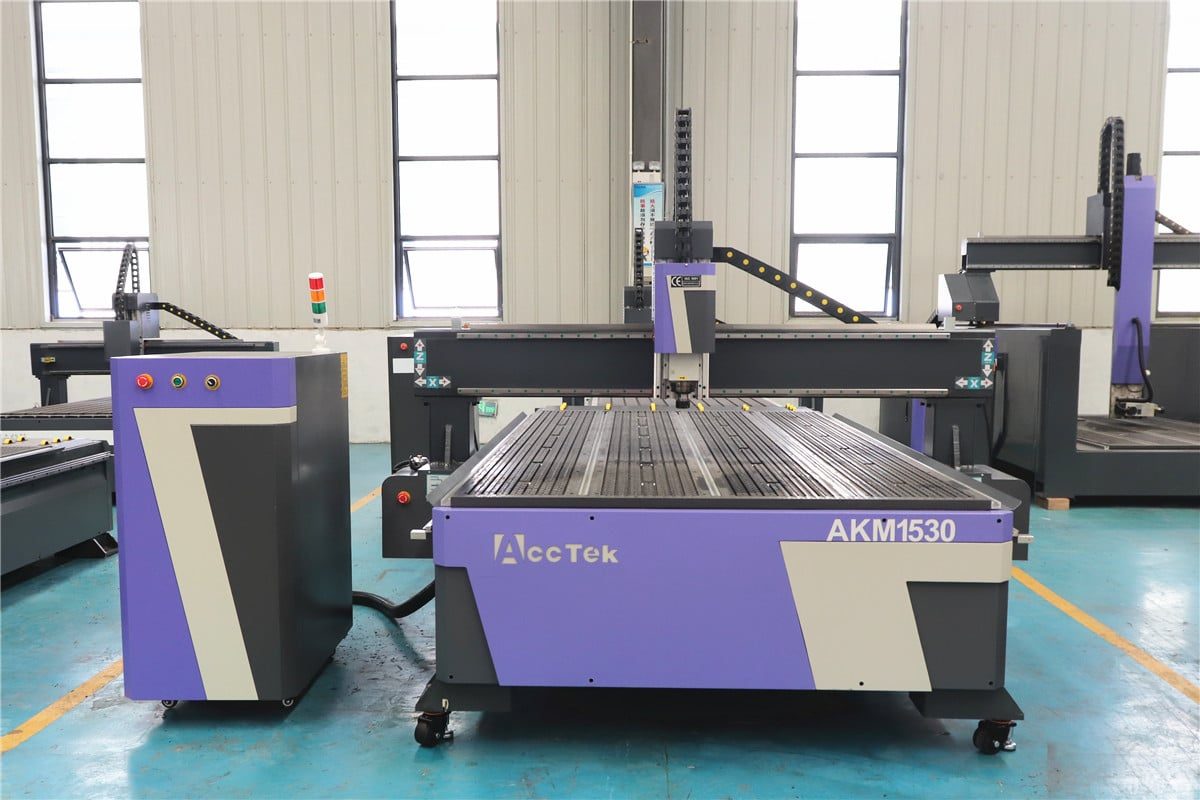
In the world of precision machining, CNC routers stand out for their ability to deliver intricate designs and exact specifications. However, one common challenge operators face is the issue of drift—a phenomenon where the machine deviates from its intended path or positioning over time. This drift can lead to inaccuracies, compromised product quality, and costly rework. As manufacturers and operators strive for perfection in their CNC routing processes, it is imperative to understand the causes and solutions for drift.
Addressing drift is not only about maintaining product quality but also about optimizing operational efficiency and minimizing costs associated with errors and rework. In this article, we delve into the causes of drift in CNC routers, explore the impact of this problem, and provide practical solutions for diagnosing and rectifying it. Whether you’re an experienced machinist or new to CNC technology, understanding and addressing drift is beneficial for maintaining the high standards of precision and efficiency expected in modern manufacturing.
Understanding Drift in CNC Routers
Drift in CNC routers refers to the phenomenon where the cutting tool or workpiece gradually deviates from the intended path or position as programmed in the machine’s control system. This deviation is unintentional and results in the machine not accurately following the specified coordinates or dimensions outlined in the design. Drift can manifest as a shift in the tool’s position relative to the workpiece, leading to inconsistencies between the planned and actual machined outcomes.
Because CNC routers are usually used to produce complex and delicate workpieces, high precision is required. In an ideal scenario, the machine’s tool should move exactly according to the set parameters, ensuring that each cut or engraving is performed with exact precision. However, when drift occurs, the machine’s movements become misaligned with the programmed instructions, resulting in discrepancies in the finished product. Understanding and monitoring drift is beneficial for maintaining the integrity and precision of CNC machining processes.
Causes of Drift
The causes of drift in CNC routers can be attributed to several key factors, each contributing to the gradual deviation of the machine’s tool path from its intended course. These factors can be broadly categorized into mechanical, thermal, software-related, and external influences. Understanding these causes is beneficial for diagnosing and preventing drift, thereby ensuring the accuracy and precision of CNC machining.
- Mechanical Wear: Over time, the mechanical components of a CNC router, such as ball screws, bearings, and linear guides, can experience wear and tear. This natural degradation can lead to issues like backlash, where there is unintended movement or play in the machine’s mechanisms. As these components wear down, they may not hold the tool path as precisely as intended, resulting in gradual deviations known as drift.
- Thermal Expansion and Contraction: Temperature changes can cause the materials in a CNC router to expand or contract. This thermal effect can alter the machine’s geometry and the alignment of its components. For instance, metal parts may expand with heat or contract in cold conditions, subtly shifting the tool’s position. This can lead to inaccuracies in the cutting or engraving process, especially if the machine’s temperature is not consistently controlled.
- Vibration and Resonance: CNC routers operate with high-speed movements, which can sometimes generate vibrations. Additionally, external vibrations from nearby equipment or structural elements can affect the machine. Resonance, which occurs when vibrations match the natural frequency of the machine or its components, can amplify these effects. These vibrations can cause the tool or workpiece to shift slightly, leading to cumulative errors and drift over time.
- Programming Errors: Errors in the programming of the CNC router, such as incorrect tool path commands, improper calibration settings, or software bugs, can lead to deviations from the intended design. Even minor mistakes in the code or setup can result in the tool moving incorrectly. Additionally, incorrect parameters for feed rate, speed, or tool offset can cause the machine to deviate from its intended path.
- Environmental Factors: The environment in which a CNC router operates can also contribute to drift. Factors such as humidity, dust, and temperature variations can affect both the machine and the workpiece. For example, high humidity can cause rust or corrosion on mechanical parts, impacting their precision. Dust accumulation can interfere with sensors and moving parts, while significant temperature changes can exacerbate thermal expansion issues.
Addressing these causes involves regular maintenance, careful monitoring of environmental conditions, precise programming, and proper setup and calibration. By understanding and mitigating these factors, CNC router operators can reduce the occurrence of drift and maintain high levels of accuracy in their machining processes.
Effects of Drift
Drift in CNC routers can have a range of detrimental effects on both the machining process and the final products. These effects can compromise the precision and quality of the work, leading to increased costs and reduced efficiency. Here is its concrete manifestation:
- Reduced Accuracy and Surface Finish: Drift leads to deviations from the intended tool path, resulting in parts that do not conform to the specified dimensions or tolerances. This loss of accuracy can cause misalignment of features, incorrect hole placements, or incorrect part sizes. Additionally, the inconsistency in tool movement due to drift can affect the surface finish of the workpiece. Instead of smooth and uniform surfaces, the product may exhibit roughness, tool marks, or irregular patterns. These imperfections can be particularly problematic in applications requiring high precision and fine finishes.
- Increased Scrap and Rework: When a CNC router drifts, the likelihood of producing defective parts increases. These parts may not meet the required quality standards or specifications, leading to them being scrapped. Scrapping defective parts results in wasted materials and resources, increasing production costs. Furthermore, parts that are not entirely defective but still require adjustments will need rework. Reworking parts not only consumes additional time and labor but also disrupts the production schedule and reduces overall efficiency.
- Compromised Product Quality: Drift can affect not only the dimensional accuracy of the parts but also their overall quality. For instance, uneven cuts, inconsistent surface finishes, or misaligned features can result from the tool not following the programmed path accurately. These defects can compromise the functionality, aesthetics, and durability of the final product, potentially leading to customer dissatisfaction.
- Increased Machine Wear and Maintenance Costs: Continuous drift can lead to uneven wear on the machine’s components, as parts may be subjected to irregular forces or movements. This can accelerate the wear and tear of mechanical components, such as bearings, guides, and screws, leading to more frequent maintenance and replacement needs. The increased wear can also shorten the overall lifespan of the machine, resulting in higher long-term costs.
- Operational Inefficiencies: Drift can disrupt the normal workflow in a manufacturing setting. The need to stop and recalibrate the machine, inspect parts for errors, and perform rework can all lead to downtime and delays. These interruptions can reduce the efficiency of the production process, leading to missed deadlines and lower productivity.
The impact of drift in CNC routers extends beyond immediate inaccuracies, it can have far-reaching consequences on production efficiency, product quality, and the reliability of the final products. By addressing the underlying causes of drift, operators can minimize these negative impacts and maintain consistent quality and efficiency in their operations.
Solutions to Mitigate and Prevent Drift
Mitigating and preventing drift in CNC routers requires a comprehensive approach that addresses various potential sources of inaccuracy. These solutions help ensure that the machine maintains its accuracy and precision, thereby producing high-quality parts. Here are some key strategies:
Regular Maintenance and Calibration
By conducting routine maintenance and calibration, operators can prevent mechanical issues that might contribute to drift, thereby preserving the accuracy and longevity of the machine.
- Component Replacement: Regularly inspect and replace worn components such as ball screws, bearings, and linear guides. These parts are prone to wear and tear, which can lead to mechanical inaccuracies and drift.
- Lubrication: Ensure that all moving parts are adequately lubricated to reduce friction and wear, which can contribute to drift.
- Machine Calibration: Regularly calibrate the machine’s axes and tools to ensure they are correctly aligned and positioned. Calibration checks should include ensuring the squareness of the axes and verifying the accuracy of the tool position.
Vibration and Resonance Management
Vibrations, whether originating from the machine itself or external sources, can cause minor shifts that accumulate over time, leading to drift. To counteract this, the following measures can be taken:
- Machine Mounting and Isolation: Properly mount and isolate the CNC router from external vibrations. Use anti-vibration pads or isolation mounts to reduce the impact of nearby machinery or structural vibrations.
- Structural Stability: Ensure that the machine is placed on a stable and level surface. An uneven or unstable surface can cause vibrations and shifts during operation, leading to drift.
Optimized Programming and Software Use
Programming errors are a common source of drift in CNC routers, so error-proof programming practices should be implemented.
- Accurate Programming: Double-check all CNC programs for errors or inaccuracies. Properly set up tool paths, feed rates, and speeds to match the material and cutting conditions.
- Software Updates: Keep the machine’s control software up to date to avoid bugs or glitches that could contribute to drift. New software versions may also offer improved accuracy and features.
Environmental Control and Cleaning
The environment in which a CNC router operates can greatly influence its performance. Controlling environmental factors such as humidity and dust levels is beneficial to prevent corrosion and interference with sensors and mechanical components.
- Temperature Regulation: Maintain a stable temperature in the machining environment to minimize thermal expansion and contraction of machine components. Temperature fluctuations can affect the machine’s accuracy and lead to drift.
- Humidity Control: Control humidity levels to prevent rust and corrosion, which can affect the machine’s mechanical components and contribute to drift.
- Cleanliness: Keep the machine and work area clean. Dust, debris, and chips can accumulate and interfere with sensors, mechanical components, and the tool path.
By implementing these solutions, CNC router operators can effectively mitigate and prevent drift, ensuring that the machine operates with high precision and produces consistently accurate parts. Regular attention to maintenance, calibration, environmental conditions, and operational practices is key to achieving optimal performance and minimizing the risk of drift.
Summarize
Addressing and mitigating drift in your CNC router is fundamental to achieving precise and reliable machining results. By understanding the causes and implementing effective solutions, manufacturers can ensure their CNC systems operate at peak performance, delivering consistent quality and efficiency in every project. A proactive approach to managing drift not only enhances the quality of the final products but also optimizes production efficiency and reduces costs, making it a critical aspect of modern CNC machining practices.
AccTek CNC is a trustworthy CNC router manufacturer known for delivering high-quality machines and comprehensive support. Our commitment to excellence extends beyond just providing top-notch machines, we also offer effective operating guides and maintenance tips to ensure that our users can operate their machines efficiently and maintain them for optimal performance. Whether you’re looking for precision, reliability, or expert support, AccTek CNC is dedicated to meeting your needs and helping you achieve the best results in your machining projects.