- 8-12 Min Read
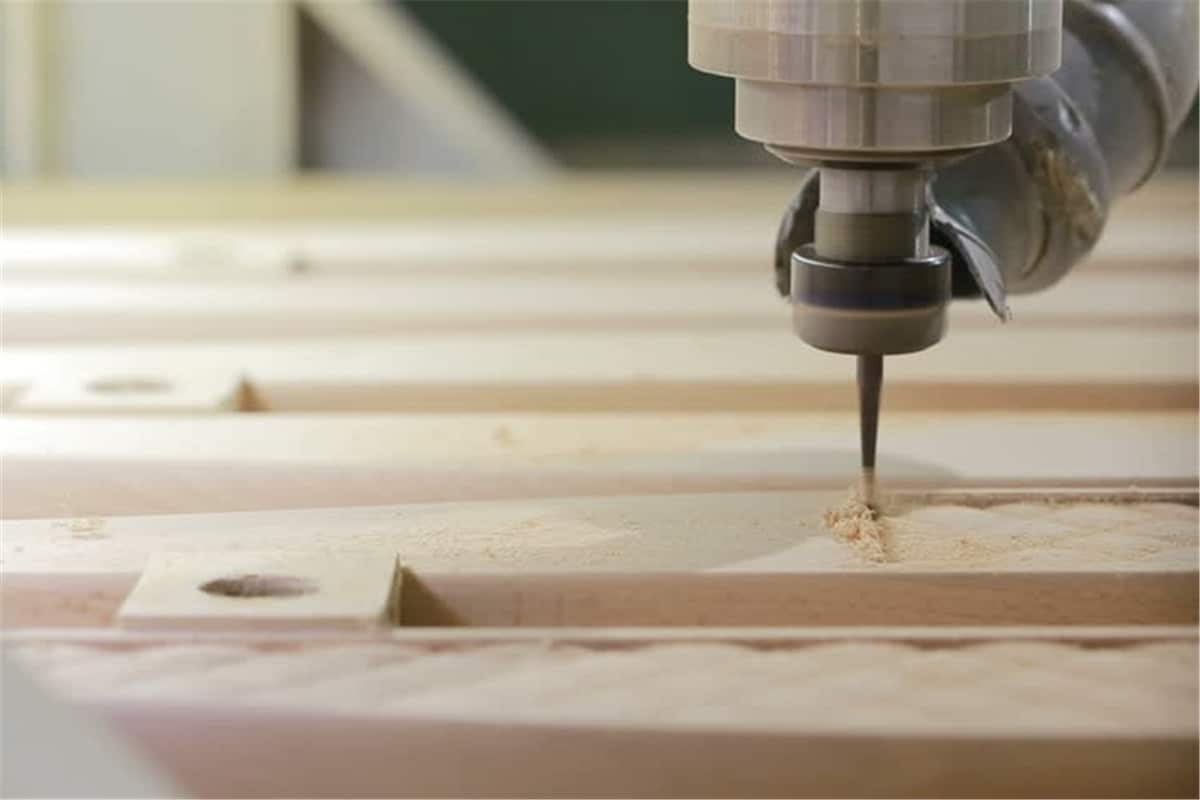
In the realm of precision manufacturing, CNC routers are indispensable tools, known for their ability to produce intricate designs and high-quality cuts on a variety of materials. However, a persistent challenge that often undermines the potential of these advanced machines is the issue of workpiece adhesion. As CNC routers seamlessly carve through diverse materials with meticulous precision, the phenomenon of adhesion stealthily undermines the cutting quality, leading to compromised outcomes and operational headaches.
This article delves into practical strategies for mitigating the impact of workpiece adhesion on CNC router cutting quality. From understanding the underlying causes of adhesion to implementing effective preventive measures, we aim to equip CNC operators and machinists with the knowledge and tools necessary to enhance their cutting processes. By exploring various techniques and best practices, this guide seeks to improve both the performance and reliability of CNC routing operations, ultimately contributing to better outcomes in manufacturing and craftsmanship.
Understanding Workpiece Adhesion in CNC Routing
Workpiece adhesion in CNC routing refers to the undesirable attachment of material residues to the cutting tool or the workpiece during the machining process. This phenomenon typically occurs when the heat generated by the cutting process causes the material being machined to become tacky or when certain materials naturally tend to stick to surfaces under pressure or friction. The impact of workpiece adhesion on cutting quality can be significant and detrimental in several ways:
- Surface Finish Degradation: Adhesion can cause irregularities on the surface of the machined part, leading to a poor surface finish. This can be especially problematic for materials that tend to melt or deform when exposed to heat, resulting in rough or uneven surfaces.
- Dimensional Inaccuracies: Adhesion can result in dimensional inaccuracies in the machined part due to material buildup on the cutting tool. As the tool wears unevenly, it may deviate from its intended cutting path, leading to dimensional errors in the final product.
- Increased Tool Wear: Adhesion accelerates tool wear by creating additional friction and stress on the cutting edges, reducing the tool’s lifespan and effectiveness.
- Machine Downtime: Frequent cleaning or replacement of tools due to adhesion-related issues can lead to increased machine downtime and reduced productivity.
- Chip Formation: Adhesion can affect chip formation during machining, leading to the formation of long, stringy chips or chip welding. Long chips can interfere with the machining process and increase the risk of tool breakage, while chip welding can result in poor chip evacuation and further exacerbate tool wear.
- AdditionalMachining Forces: Adhesion can increase cutting forces during machining, placing additional stress on the cutting tool and the CNC machine. This can lead to reduced machining efficiency, increased energy consumption, and potentially compromised part quality.
Common causes of workpiece adhesion problems
Workpiece adhesion problems in CNC routing can stem from various causes. Understanding these causes is beneficial for implementing effective solutions and maintaining high machining quality. Here are some common causes of workpiece adhesion problems:
Material Properties
- Soft and Ductile Materials: Materials like aluminum, copper, and certain plastics tend to adhere to cutting tools more readily due to their ductility and tendency to deform plastically.
- High Melting Point Materials: Materials with high melting points can generate excessive heat during cutting, causing them to soften and adhere to the tool.
Cutting Tool Properties
- Inappropriate Tool Material: Using tools made of materials that are not suitable for the specific workpiece material can lead to adhesion. For example, using high-speed steel (HSS) tools for cutting aluminum may result in higher adhesion compared to using carbide tools.
- Tool Coatings: Lack of or inappropriate tool coatings can exacerbate adhesion. Coatings like titanium nitride (TiN) or diamond-like carbon (DLC) can reduce adhesion by providing a smoother surface and reducing friction.
- Tool Geometry: Improper tool geometry, such as inadequate rake angle or clearance angle, can increase the tendency for workpiece material to adhere to the tool.
Cutting Parameters
- Cutting Speed: Low cutting speeds can increase the contact time between the tool and the workpiece, promoting adhesion. Conversely, excessively high speeds can generate excessive heat, also leading to adhesion.
- Feed Rate: Inappropriate feed rates can affect chip formation and heat generation. Too low a feed rate can cause rubbing rather than cutting, while too high a feed rate can increase heat and adhesion.
- Depth of Cut: Too deep or too shallow a cut can affect chip formation and heat dissipation, leading to adhesion problems.
Coolant and Lubrication
- Insufficient Coolant: Lack of adequate coolant can result in excessive heat buildup during the cutting process, which increases the risk of material adhesion.
- Inappropriate Coolant: Using the wrong type of coolant for the material being machined can fail to provide the necessary cooling and lubrication, leading to increased adhesion.
- Poor Lubrication: Inadequate or incorrect lubrication can lead to higher friction between the tool and the workpiece, promoting adhesion.
Workpiece Contamination
- Surface Contaminants: The presence of oils, oxides, or other contaminants on the workpiece surface can affect the cutting process and increase adhesion.
- Moisture: Excess moisture on the workpiece can cause steam formation during cutting, affecting heat dissipation and promoting adhesion.
Detecting workpiece adhesion problems
Detecting workpiece adhesion problems in CNC routing involves monitoring several key aspects of the machining process. Here are some common methods and indicators for detecting adhesion problems. This proactive approach helps maintain machining quality and prolongs tool life, ensuring efficient and consistent production.
Surface Finish Analysis
Indicators of Adhesion Problems
- Rough or Irregular Surface: Inspect the machined surface for rough patches, smearing, or uneven textures. These can indicate that the material is sticking to the tool and being dragged across the workpiece.
- Discoloration: Look for discoloration or burn marks on the surface. Excessive heat generated by adhesion can cause the material to discolor.
- Burr Formation: Excessive or irregular burrs at the edges of the machined parts can suggest adhesion problems, as material sticking to the tool can lead to poor cutting performance and finish.
Detection Methods
- Visual Inspection: Regularly inspect the surface finish of machined parts under good lighting conditions.
- Surface Roughness Measurement: Use surface roughness testers or profilometers to quantitatively measure the roughness of the machined surface.
- Comparative Analysis: Compare the surface finish of current parts with reference parts known to be free from adhesion problems.
Tool Inspection and Wear Analysis
Indicators of Adhesion Problems
- Built-Up Edge (BUE): Check for material buildup on the cutting edge of the tool, which is a direct sign of adhesion.
- Irregular Wear Patterns: Look for chipping, flaking, or unusual wear on the tool’s cutting edges. These can indicate that adhesion is causing uneven wear.
- Tool Discoloration: Discoloration of the tool, often due to excessive heat, can suggest adhesion issues.
Detection Methods
- Visual Inspection: Regularly inspect the cutting tools under magnification to detect built-up edges and unusual wear patterns.
- Tool Life Monitoring: Track the tool life and compare it with expected performance. A sudden decrease in tool life can indicate adhesion problems.
Cutting Force Monitoring
Indicators of Adhesion Problems
- Increased Cutting Forces: A noticeable increase in the cutting forces can suggest that the material is adhering to the tool, causing higher resistance.
- Fluctuations in Cutting Forces: Irregular or fluctuating cutting forces can indicate intermittent adhesion, where the material sticks and then breaks away from the tool.
Detection Methods
- Dynamometers: Use dynamometers to measure the cutting forces in real-time. Anomalies in the force readings can indicate adhesion.
- Acoustic Emission Sensors: These sensors detect high-frequency sounds generated by friction and adhesion during cutting. Unusual acoustic emissions can signal adhesion problems.
- Real-Time Monitoring Software: Utilize CNC systems equipped with real-time monitoring capabilities to track cutting forces and detect deviations from normal values.
Alleviates adhesion-related issues
Alleviating adhesion-related issues in CNC routing requires a combination of strategies, here are several methods to mitigate adhesion problems. By employing a combination of these methods, machinists and operators can effectively detect and address workpiece adhesion problems, ensuring optimal performance and quality in CNC routing operations.
Optimize Cutting Parameters
- Increase Cutting Speed: Higher cutting speeds can reduce contact time between the tool and the workpiece, decreasing the likelihood of adhesion. However, ensure that speeds are not so high that they cause excessive heat.
- Adjust Feed Rate: Optimizing the feed rate can help in achieving effective chip removal and reducing adhesion. Too low a feed rate can cause rubbing, while too high can generate excessive heat.
- Optimize Depth of Cut: Ensuring the correct depth of cut can help in effective chip formation and removal, reducing the chance of material adhering to the tool.
Use Appropriate Tool Selection
- Tool Material: Tools made from carbide or ceramics are more resistant to wear and heat, reducing adhesion compared to high-speed steel (HSS) tools.
- Tool Coatings: Use tools with coatings like titanium nitride (TiN), titanium carbonitride (TiCN), or diamond-like carbon (DLC). These coatings provide a smoother surface and reduce friction, minimizing adhesion.
- Tool Geometry: Select tools with appropriate rake and clearance angles to facilitate smooth cutting and chip removal. Proper tool geometry helps in reducing heat and material sticking to the tool.
Proper Tool Path Planning
- Minimize Heat Generation: Plan tool paths that avoid excessive heat buildup by distributing cutting forces evenly and allowing for adequate cooling periods.
- Avoid Re-cutting Chips: Design tool paths to ensure that chips are efficiently evacuated and not re-cut, which can increase adhesion.
- Adaptive Tool Paths: Use adaptive tool path strategies that adjust in real-time to changing cutting conditions to maintain optimal cutting performance.
Implement Effective Cooling and Lubrication
- Use Appropriate Coolant: Select a coolant that is suitable for the specific material being machined. Ensure that the coolant has good cooling and lubricating properties to reduce heat and friction.
- Maintain Coolant Flow: Ensure an adequate and continuous flow of coolant to effectively dissipate heat and flush away chips.
- Apply Lubricants: Use lubricants that can reduce friction and prevent adhesion. Mist or spray lubrication can be particularly effective.
- Check for Compatibility: Ensure that the lubricants and coolants used are compatible with both the tool and the workpiece material.
Tool Damping Technology
- Damped Tool Holders: Use tool holders with built-in damping mechanisms to reduce vibrations, which can cause intermittent adhesion and poor surface finish.
- Damping Materials: Incorporate damping materials into tool holder designs to absorb and dissipate vibrations.
- Real-Time Vibration Control: Implement systems that actively monitor and counteract vibrations during machining to maintain smooth cutting conditions and reduce adhesion.
Tool and machine maintenance
Proper tool and machine maintenance is beneficial for alleviating adhesion-related issues in CNC routing. Regular maintenance ensures optimal performance, prolongs the lifespan of tools and machinery, and maintains the quality of machined parts. Here are the key aspects of tool and machine maintenance:
Regular Tool Maintenance Practices
Regular tool maintenance involves a series of systematic checks and procedures to keep cutting tools in optimal condition. These practices help prevent tool wear, reduce adhesion problems, and maintain machining quality.
- Visual Inspection: Regularly inspect cutting tools for signs of wear, damage, and built-up edges (BUE). Use magnification to detect smaller defects.
- Debris Removal: Clean tools after each use to remove adhered material, chips, and coolant residues. This helps maintain the tool’s cutting efficiency.
- Tool Sharpening: Periodically sharpen cutting tools to maintain their edge and cutting performance.
- Tool Replacement: Replace tools that show significant wear, chipping, or have reached the end of their effective lifespan to prevent machining issues like adhesion and poor surface finish.
- Coating Inspection: Check the integrity of tool coatings. Tools with worn or damaged coatings should be recoated or replaced, as coatings play a significant role in reducing friction and preventing adhesion.
- Appropriate Coatings: Ensure the use of tool coatings that are suitable for the specific material being machined (e.g., TiN, TiCN, DLC) to reduce the likelihood of material adhesion.
Machine Calibration
Regular calibration helps maintain machining tolerances and prevents errors that can lead to poor quality and increased adhesion.
- Alignment Checks: Regularly check and adjust the alignment of the spindle to ensure it is perpendicular to the worktable. Ensure that tool holders are properly aligned and securely fastened. Misalignment here can lead to increased tool wear and adhesion problems.
- Calibration Procedures: Calibrate the X, Y, and Z axes to ensure accurate movement and positioning. Use calibration tools and software to check and adjust the machine’s axis movements. Regularly update and calibrate the CNC control software to ensure that all movements and operations are executed accurately according to the programmed instructions.
- Test Cuts and Adjustments: Perform test cuts on a sample workpiece to check for accuracy and surface finish. Analyze the results and make necessary adjustments to the machine settings. Regularly check for and adjust any backlash in the machine’s movements to ensure precision in cutting.
Summarize
Addressing workpiece adhesion is not just about solving an immediate problem—it’s about investing in long-term machining excellence. Through our exploration of workpiece adhesion and its multifaceted impact on CNC router cutting, we have uncovered a plethora of strategies and best practices for mitigating its effects. By integrating these strategies, CNC router operators can achieve superior cutting quality, extend tool life, and maintain consistent machining performance. Addressing adhesion-related problems proactively not only enhances productivity but also ensures the production of high-quality machined parts, ultimately contributing to operational efficiency and cost savings.
For those seeking reliable and versatile CNC routing solutions, AccTek CNC stands out as a premier choice. As a well-known CNC router manufacturer in China, AccTek CNC offers a diverse range of machines tailored to meet the varied needs of different users. Whether you are a hobbyist looking for a compact and user-friendly CNC router or an industry professional in need of a robust, high-performance machine, AccTek CNC has the right model for you. With a commitment to quality and innovation, AccTek CNC ensures that each of their routers delivers precision, durability, and exceptional cutting performance, making them an excellent partner for your machining needs.